V205白车身车门装配尺寸控制原理及应用
- 来源:汽车工艺师 smarty:if $article.tag?>
- 关键字:白车身装配尺寸,车门Y向装配尺寸,车门Z向装配尺寸 smarty:/if?>
- 发布时间:2020-10-08 08:33
摘要:通过Y向小三角控制原理,避免了车门单件尺寸波动带来的装配不稳定性,并且在Y向装配姿态稳定的基础上,规范了Z、X向控制点的位置。通过多轮的试验及验证,制定了适合铁质车门的装配工艺卡,既保证了整车装配尺寸,又达到了令顾客满意的关门力,并成功消除了窗框区域的噪声问题。
关键词:白车身装配尺寸;车门Y向装配尺寸;车门Z向装配尺寸
白车身装配尺寸是整车外观精致度的重要考核指标,且车门Y向装配尺寸对车门关门力的大小有直接影响,车门Z向装配尺寸对窗框噪声影响较大。故车门装配尺寸的提升对整车装配尺寸及关门力噪声等考核项的优化至关重要。
V205白车身在试制阶段存在间隙平顺度问题及关门力大、窗框噪声问题,现有德国Daimler公司制定的车门装配工艺适用于德国不莱梅工厂的铝件,而北京奔驰V205车门采用铁件,由于材料的改变需要优化装配工艺。
车门装配尺寸控制原理的执行
覆盖件装配可以执行物体在空间定位的3-2-1定位原则,尤其对于车门区域,针对间隙平顺度控制点的设置可以采用此原则。
1. 车门Y向装配尺寸小三角控制原理
物体在空间定位采用3-2-1原则或N-2-1原则,对于前门及后门而言,Y方向装配尺寸执行小三角控制原理,即Y方向控制车门外板区域而不包括窗框区域。相对车门外板区域,V205窗框区域冲压件的尺寸偏差会积累,且尺寸不稳定,这样可以避免窗框区域的尺寸波动对装配尺寸的影响。如图1所示,红色三角由三个Y向控制点组成,分别为上下铰链深度及门锁区域Y0控制点。对于后门而言,执行小三角控制原理之前,V205一致执行大三角控制原理,其中一个Y向控制点由车门窗框而非铰链上深度点,大三角控制无法抵消窗框自身的波动,从而使装配波动性变大。前门Y向控制点的选择采用小三角控制原理,即选择前门上下铰链深度及前门归零点Y 0,上下铰链深度分别为(29.5+0.5 -0.8 )m m以及(31.5 +0.5 -0.5 )mm。后门由三个Y向控制点组成,分别为上铰链深度及归零点Y 0,深度值为(79.5+0.8 -0.5 )mm,下铰链深度控制点数值(48.5+0.8 -0.5 )mm,以上数据由Cubing车身及车身数模测量得出。最后一个Y向控制点是Y向归零点,即车门Y0。
以上数据并非完全复制德国Daimler下发的装配规范,根据Daimler下发工艺卡分别控制上窗框深度及车门底角平顺度,如图2所示。此控制方法会由于车门零件的波动影响最后的装配尺寸。德国的车门单件的生产及装配自动化率较高,尺寸相对稳定,而北京奔驰现有生产线相对自动化率较底。但发现现有装配尺寸Y向控制点可以通过车门铰链工装控制,在执行小三角控制原理后,经过试验及实际生产中发现,上下铰链深度波动仅有0.2~0.5mm。并且可以避免车门单件底角的波动带来车门装配姿态的变化,有效控制车门窗框平顺度及后门与侧围平顺度,可以将其波动控制在0.5~1.0mm。
2. 车门Z向装配尺寸测量点的选择及控制
由车门Y向小三角控制原理得知,车门装配Y向工艺的设定可以有效控制窗框与侧围的间隙及平顺度,但仍然存在波动。故车门Z向的测量点不可选择窗框区域,在投产阶段采用测量窗框与侧围Z向的相对距离作为Z向的测量点,且发现无论前门或是后门,Z向测量数据会受到车门自身窗框尺寸的波动以及装配尺寸的影响。现选取车门外板与侧围的相对距离作为Z向控制点,并且此控制点与CMM测量点相一致,实现了生产制造与检测的统一,如图3、图4中红线方框所示。并且发现了CMM数据的优化:优化前数据存在超差现象,而执行新的Z向工艺后,前门及后门的Z向可以控制在±0.7mm内。
3. 车门X向装配尺寸测量点的选择及控制
前门及后门X向控制点选择相类似,分别位于车门外板后端,如图5所示,前门上间隙测量点为10点,间隙值为(4.8+0.5 -0.5 )mm。前门下间隙测量点为8点,间隙值为(3.8+0.5 -0.5 )mm。后门上间隙测量点为15点,间隙值为(5.1+0.5 -0.5 )mm。后门下间隙测量点为14点,间隙值为(3.5+0.5 -0.5 )mm。而针对于前门而言,需要设置前门的翘起值kickup,最新工艺卡为(2.3+0.5 -0.5 )mm, 图3 前门高度CMM数据图4 后门高度CMM数据由此数据对比德国初始的工艺卡中kick-up翘起值(1.6+1.0)mm提高了0.2mm,且上间隙变大了0.2mm,下间隙变小了0.3mm,即间隙变得更加V形间隙,后门的工艺设置也出现了相同的情况。V形间隙不仅需要大量的试验与生产验证,也与车门材质有关,V205国产化以后车门由铝件改为钢件,车门的质量变大,为防止车门下坠更多,即以铰链为轴顺时针旋转造成A间隙,故提前在车身工厂将间隙的预设值变大,如图6所示,绿色区域为在线检测前门及后门测量数据,随机选取1个班次,可以发现间隙数据100%符合工程要求。前后门间隙得到有效控制,此前后门的间隙有效控制保证了X向的装配尺寸。
质量目标达成状态
1. 间隙平顺状态
V205 四门间隙平顺度,包括前门及翼子板的间隙平顺度都是质量部的考核项,质量部通过CalipriGap激光测量设备对四门区域进行测量,每天测量一台车。现随机选取了100台车的测量数据,且间隙平顺考核分为一级和二级公差。前后门匹配区域一级公差为±0.5mm,二级公差为±1.0mm,车门窗框与侧围且车门与底边梁一级公差为±0.7mm,二级公差为±1.4mm。试生产完成后,批量执行相关装配原理后,间隙平顺度得到有效控制。
现选取的右侧前后门评估间隙平顺的状态,右侧前门及后门B柱区域窗框平顺度稍外闪,10%超公差二级,但此区域可以通过返修满足工艺要求,且2%的右侧底边梁间隙一致性超二级公差,此区域较难返修,但此区域非重点关注区域,若需要返修,可以平衡窗框间隙及前后门间隙综合评估,进行返修。不过现状态90%的白车身不需要人工返修即可满足间隙平顺要求。如图7所示。
2. 关门力状态
间隙平顺度得到稳定控制以后,尤其是前后门Y向铰链深度以及后门与侧围平顺度,前门、后门平顺度得到有效控制,车门关门力状态也稳定下来。针对关门力的监控,质量部每天在生产线上随机选取一台车,利用测量关门力特殊测量设备对四门进行分别测量,一级公差为(65±15)cm,二级公差为65±25cm,现选取了100量份的考核报告,100%的测试车关门力状态符合二级公差,90%以上的测试车符合一级工差,如图8所示。
3. 窗框风噪问题的解决
试装阶段发现关门力偏大,当关门力被逐渐优化到偏小30~40cm后,车门窗框风噪的问题随之出现。车门装配的Y向状态与关门力相关,故仅能从Z向装配尺寸优化风噪问题,且外放车门铰链深度后,窗框平顺度相对外闪0.5~1.0mm,故向车门Z向装配尺寸平均提高0.5mm,减小了窗框胶条与侧围的Z向内间隙,从而解决了窗框风噪问题。且使窗框平顺度平均里凹了0.5mm,同时平衡了关门力数据。
结语
通过以上优化,在随机选取的100台整车中,保证了90%以上的车门间隙平顺度满足一级公差考核要求,100%的测试车关门力状态符合二级公差,90%以上的测试车符合一级工差,并且成功消除了窗框区域的噪声问题。
张皓源
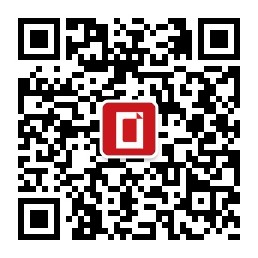