平板陶瓷支撑体的制备与表征
- 来源:工业技术创新 smarty:if $article.tag?>
- 关键字:陶瓷支撑体,氧化铝粉,颗粒级配 smarty:/if?>
- 发布时间:2020-12-02 10:17
摘 要: 采用平均粒径10 μm和5 μm的氧化铝粉为主要原料,通过颗粒级配,制备出孔径分布较窄的陶瓷支撑体,并研究颗粒级配对陶瓷支撑体相关性能的影响。研究表明:随着5 μm氧化铝粉比重增大,陶瓷支撑体孔隙率减小,抗压强度增大,平均孔径减小,气体通量减小;当10 μm氧化铝粉与5 μm氧化铝粉质量比为1:1时,所得陶瓷支撑体孔径分布最窄,孔隙率为43.5%,抗压强度为25.8 MPa,平均孔径为0.6 μm,气体通量为21.9 m3/(m2·h)(△P=0.1 bar)。
关键词: 陶瓷支撑体;氧化铝粉;颗粒级配;孔隙率;孔径分布;气体通量
中图分类号: T Q174 文献标识码: A 文章编号: 2095 - 8412 ( 2020 ) 0 5 - 001 - 0 5
工业技术创新 URL: http://gyjs.cbpt.cnki.net DOI: 10.14103/j.issn.2095-8412.2020.05.001
引言
20世纪80年代,陶瓷过滤膜开始实现工业化应用。陶瓷过滤膜因其化学稳定性好、耐腐蚀性能优异、力学性能优良、易洗涤再生等优点而逐渐被工业界所接受,在化工、食品、环保等众多领域得到广泛应用[1-3]。陶瓷过滤膜是一种多孔梯度材料,在结构上包括分离层、过渡层及支撑体三部分。支撑体作为陶瓷过滤膜的基底材料,是保障陶瓷过滤膜机械性能的关键。因此,制备具有优异机械性能和渗透性能的陶瓷支撑体,是制备具有优异性能的陶瓷过滤膜的前提条件。
目前,陶瓷支撑体多以类球形氧化铝(Al 2O3)为主料。在生产过程中,采用蜂窝陶瓷挤出成型方式制备生坯,经高温煅烧后,即可获得具有孔道结构的陶瓷支撑体[4]。在高温作用下,颗粒间形成颈部连接,使支撑体具有一定的机械强度。根据粉末烧结理论,物质的扩散除受温度影响外,还与粉体颗粒的形貌和大小相关[5],因此颗粒的形状、粒径及粒度分布直接影响陶瓷支撑体的孔道结构及气孔率。
关于粉体的平均粒径及粒径分布[6-9],成型方法[10],成型过程中所用粘结剂和造孔剂的种类、用量,烧结工艺[11]等对支撑体性能的影响,目前均有报道。但是,通过对商品化平板陶瓷过滤膜及现有文献的综合分析,发现由于所用原料不同,现有支撑体孔径没有受到有效控制,孔径分布较宽,为提高过滤精度和分离层强度,往往在支撑体和分离层间引入过渡层。但过渡层的存在增加了膜层的厚度,增大了过滤过程中的阻力,水处理成本增高;同时,引入过渡层使得平板陶瓷过滤膜的制备工序复杂化,致使缺陷率增加,生产周期延长,生产能耗增大,产品成本提高。
本文采用不同粒径分布的两种氧化铝粉体进行颗粒级配,辅以适量的粘结剂和造孔剂,通过蜂窝陶瓷挤出成型工艺制备孔径分布均一的平板陶瓷支撑体。该平板陶瓷支撑体可直接用于分离层的涂覆,省去了过渡层,降低了陶瓷过滤膜的生产成本。此外,研究颗粒级配对陶瓷支撑体孔隙率、孔径大小、孔径分布、气体通量及抗压强度的影响。
1 实验
1.1 实验材料及仪器
1.1.1 实验材料
(1)主料:平均粒径10 μm氧化铝粉体和平均粒径5 μm氧化铝粉体;
(2)粘结剂:羟丙基甲基纤维素;
(3)造孔剂:玉米淀粉;
(4)烧结助剂:水洗高岭土;
(5)增塑剂:甘油。
1.1.2 实验仪器
(1)Master Sizer 3000激光粒度测试仪;
(2)JHT10台式双运动混合机;
(3)NHJ-50捏合机;
(4)TL-150真空练泥机;
(5)WHJ-15T液压挤出机;
(6)101-1A型电热鼓风干燥机;
(7)KSS-1750型高温炉;
(8)XM-50KN电子万能材料试验机;
( 9 ) TM3030 场发扫描电子显微镜(SEM);
(10)3H-2000PB泡压法滤膜孔径分析仪。
1.2 陶瓷支撑体的制备
称取总质量为20 kg的氧化铝粉(10 μm氧化铝粉与5 μm氧化铝粉的质量比分别取1:0、1:1、1:2、0:1),外加一定量的粘结剂、造孔剂、烧结助剂后充分混合均匀,再将混合好的粉料转入捏合机中,加入适量增塑剂和水捏合成泥料。再将泥料粗炼、陈腐、精炼、挤出成型、微波定型、暖风干燥、切割整形、吹灰、煅烧(1 350℃,保温2 h),制得厚度为6 mm、宽度为100 mm的中空平板状陶瓷支撑体。
1.3 陶瓷支撑体性能的表征
采用激光粒度测试仪测定原料的平均粒径及分布,结果如图1所示。采用SEM观察样品的形貌和微观结构;按照GB/T 1966-1996[12]标准,采用阿基米德原理测定陶瓷支撑体的孔隙率和吸水率;通过电子万能材料试验机表征陶瓷支撑体的抗压强度;采用泡压法滤膜孔径分析仪测试陶瓷支撑体的平均孔径及孔径分布、气体渗透率和气体通量。依据泡压法的原理,陶瓷支撑体的孔径与压力的关系如Washburn公式:
(1)其中:D,孔隙直径;γ,液体的表面张力;θ,接触角;P,压差。
2 结果与讨论
2.1 颗粒级配对陶瓷支撑体孔隙率的影响图2显示了颗粒级配对陶瓷支撑体孔隙率的影响。例如,当10 μm氧化铝粉与5 μm氧化铝粉质量比为1:1时,所得陶瓷支撑体的孔隙率为43.5%。可以看出:随着平均粒径5 μm氧化铝粉的质量百分比增大,陶瓷支撑体的孔隙率减小,但降低幅度不大,因此颗粒级配对陶瓷支撑体的气体通量影响较小。这一结果验证了Lee等[13]的研究结论。Lee等认为:在相同的煅烧条件下,小颗粒会部分填充到大颗粒堆积形成的孔道中,导致陶瓷支撑体中总的孔体积减小,孔隙率降低。
2.2 颗粒级配对陶瓷支撑体抗压强度的影响
图3为颗粒级配对陶瓷支撑体抗压强度的影响。例如,当10 μm氧化铝粉与5 μm氧化铝粉质量比为1:1时,所得陶瓷支撑体的抗压强度为25.8 MPa。可以看出,在相同煅烧温度下,随着5 μm氧化铝粉的质量百分比增大,陶瓷支撑体的抗压强度逐渐增大,这是由于细粉活性远高于粗粉活性,促进了烧结,加强了颗粒之间的颈部连接[14],提高了陶瓷支撑体的力学性能。
图4显示了四种氧化铝颗粒级配制得陶瓷支撑体的表面微观结构。可以看到,大颗粒间主要依靠小颗粒粉体扩散形成颈部连接,随着小颗粒粉体的增多,颗粒之间的接触点或接触面增多,连接颈部的面积增大,有助于颗粒度烧结。在高温烧结的过程中,颗粒之间结合得更紧密。这为陶瓷支撑体力学性能随着小颗粒粉体含量的增大而增大提供了证据。
2.3 颗粒级配对陶瓷支撑体平均孔径及孔径分布的影响
图5是颗粒级配对陶瓷支撑体平均孔径的影响。例如,当10 μm氧化铝粉与5 μm氧化铝粉质量比为 1:1 时,所得陶瓷支撑体的平均孔径为0.6 μm。可以看出,10 μm氧化铝粉制得陶瓷支撑体的平均孔径明显大于5 μm氧化铝粉的情形。根据等径球体堆积理论:单一尺寸的原料,孔径只与颗粒的大小有关,原料颗粒尺寸越大,陶瓷支撑体孔径就越大[15]。随着小颗粒粉体比重增大,陶瓷支撑体的平均孔径逐渐减小,这是因为小颗粒填充了大颗粒之间的孔隙,促进了颗粒的有效堆积,小孔数量随之增加[16]。 因此,通过调控大小颗粒级配,可有效调配陶瓷支撑体的平均孔径。
图6显示了颗粒级配对陶瓷支撑体孔径分布的影响。从图6a、6d可以看出,单组分粉体制得陶瓷支撑体孔径分布较宽,且大颗粒粉体制得陶瓷支撑体的孔径分布宽于小颗粒粉体的情形。当两种粉体进行级配时,所得陶瓷支撑体的平均孔径变小,且分布变窄。这是因为小颗粒填充了大颗粒之间的孔隙,从而缩小了陶瓷支撑体孔径分布宽度。分析可知,选用更小级别的粉体进行颗粒级配,则可得到更小孔径、更窄孔径分布的陶瓷支撑体。
2.4 颗粒级配对陶瓷支撑体气体通量的影响图7显示了颗粒级配对陶瓷支撑体气体通量的影响。例如,当10 μm氧化铝粉与5 μm氧化铝粉质量比为1:1时,所得陶瓷支撑体的气体通量为21.9 m3/(m2·h)(△P=0.1 bar)。可以看出,陶瓷支撑体的气体通量随着小颗粒粉体比重的增加而减小,这与陶瓷支撑体孔隙率和平均孔径的变化趋势一致。陶瓷支撑体孔隙率的降低和平均孔径的变小都增大了陶瓷支撑体的过滤阻力,因而陶瓷支撑体的气体通量呈逐渐减小的趋势。
3 结论
本文采用平均粒径为10 μm和5 μm的氧化铝粉进行颗粒级配,成功制备出孔径分布窄的陶瓷支撑体。通过研究不同颗粒的级配对陶瓷支撑体相关性能的影响,得出以下结论:
(1)随着5 μm氧化铝粉体比重的增大,制得陶瓷支撑体的孔隙率逐渐减小,平均孔径和气体通量逐渐减小,而抗压强度则逐渐增大。
(2)单一组分制得陶瓷支撑体的孔径分布较宽,而进行颗粒级配所得陶瓷支撑体的孔径分布变窄。
(3)在10 μm氧化铝粉与5 μm氧化铝粉质量比为1:0、1:1、1:2、0:1的情形中,质量比为1:1的孔径分布最窄。通过多级颗粒级配,可获得平均孔径更小、孔径分布更窄的多孔陶瓷支撑体。
基金项目
洛阳市科技重大专项(项目编号:1901008A)
参考文献
[1] 范益群, 漆虹, 徐南平. 多孔陶瓷膜制备技术研究进展[J]. 化工学报, 2013, 64(1): 108-116.
[2] 徐南平. 面向应用过程的陶瓷膜材料设计、制备与应用[M]. 北京: 科学出版社, 2005.
[3] 吴泽霖, 王斌, 陈家才, 等. 高性能氧化铝陶瓷膜支撑体的制备及表征[J]. 佛山陶瓷, 2019, 29(1): 10-14.
[4] Tsuru T. Inorganic porous membranes for liquid phase separation[J]. Sep Purif Methods, 2001, 30(2): 191-220.[5] 周永欣, 林钰青, 陈献富, 等. 粉体颗粒参数对多孔陶瓷支撑体性能的影响[J]. 膜科学与技术, 2016, 36(2): 81-85.
[6] 刘丰利, 杨玉龙, 常启兵, 等. 造孔剂对粉煤灰基多孔陶瓷
膜支撑体的性能影响[J]. 中国陶瓷工业, 2019, 26(2): 21-25.
[7] 胡嗣胜, 漆虹, 徐南平,等. 成孔剂的量对多孔氧化铝支撑体孔结构的影响[J]. 南京工业大学学报, 2005, 27(1):8-11.
[8] 丁祥金, 张继周, 宝志琴, 等. 氧化铝多孔支撑体的研究[J]. 膜科学与技术, 2000, 20(1): 17-21.
[9] 丁贯保, 漆虹, 邢卫红, 等. 粒径分布对氧化铝多孔支撑体孔结构的影响[J]. 膜科学与技术, 2008, 28(5): 23-27.
[10] 王焕庭, 刘杏芹, 周勇, 等. 多孔陶瓷支撑体膜材料的制备和表征[J]. 膜科学与技术, 1997, 17(1): 47-52.
[11] 漆虹, 邢卫东, 范益群, 等. 低温烧成高纯Al2O3多孔支撑体支撑体的制备[J]. 硅酸盐学报, 2010, 38(2): 283-288.
[12] 多孔陶瓷显气孔率、容重试验方法: GB/T 1966-1996[S].
[13] Lee D Y, Kim D J, Kim B Y, et a1. Effect of alumina particle size and distribution on in filtration rate and fracture toughness of alumina-glass composites prepared by melt infiltration[J]. Mater Sci Eng A, 2003, 341(1-2): 98-105.
[14] Wa n g Y H , Z h a n g Y, L i u X Q , e t a 1 . S o l - c o a t e d preparation and characterization of macroporous -Al2O3 membrane support[J]. J Sol-Gel Sci Technol, 2006, 41(3): 267-275.
[15] 周健儿, 杨玉龙, 常启兵, 等. 颗粒级配对氧化铝多孔陶瓷膜支撑体孔径及抗折强度的影响[J]. 人工晶体学报, 2014, 43(8): 2125-2131.[16] Shiau F S, Fang T T, Leu T H. Effects of milling and particle size distribution on the sintering behavior and the evolution of the microstructure in sintering powder compacts[J]. Mater Chem Phys, 1998, 57(1): 33-40.
Preparation and Characterization of Flat Ceramic Supports
LI Dai, LI Shun, PEI Guang-bin, MA Teng-qi
(Luoyang Zhongchao New Materials Co., Ltd., Luoyang 471000, China)Abstract: Alumina powder with average particle sizes of 10 μm and 5 μm is used as the main raw material.
Through particle gradation, a ceramic support with a narrow pore size distribution is successfully prepared, and the effect of particle gradation on the support-related properties is studied. The research shows that as the proportion of 5 μm alumina powder increases, the porosity of the ceramic support decreases, the compressive strength increases, the average pore diameter decreases, and the gas flux decreases accordingly; when the mass ratio of 10 μm alumina to 5 μm alumina is 1:1, the distribution of the pore diameter is the narrowest, the porosity of the support is 43.5%, the compressive strength is 25.8 MPa, the average pore diameter is 0.6 μm, and the gas flux is 21.9 m3/(m2·h) (△P=0.1 bar).Key words: Ceramic Support; Alumina; Particle Gradation; Porosity; Distribution of Pore Diameter; Gas Flux
李岱,李顺,裴广斌,马腾琪
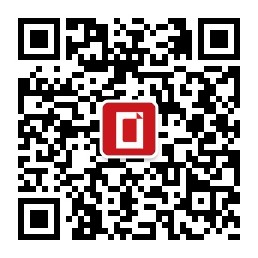