汽车行业的智能制造距离我们有多远
- 来源:汽车工艺师 smarty:if $article.tag?>
- 关键字:汽车,行业,智能制造 smarty:/if?>
- 发布时间:2021-09-19 21:22
在“ 2 0 1 9 汽车零部件先进加工技术研讨会( 湖北站)”,东风商用车有限公司首席师李喜咏指出:当前汽车行业的制造发展方向,主要是“五化”:
(1)数字化——数字化设计、模拟分析、制造、生产和管理。
(2)智能化——从自动化生产转向智能化,满足个性生产需求。
(3)精致化——提高外观魅力品质,满足造型需求。
(4)绿色化——优化生产流程和工艺,提高装备通用性,实现柔性生产,提升生产效率。
(5)轻量化——对高强度材料、铝合金材料的使用比率越来越高。
汽车发动机对制造技术的要求
目前,中国已经掌握了发动机现代制造技术体系、质量检测和评价标准等,引进机型制造水平与国外同类产品相当。其中,缸体、缸盖、曲轴、连杆、凸轮轴、活塞及涡轮进排气系统等主要零部件都可实现自主化生产。然而,高端机型制造的成套工艺与装备仍依赖国外引进,缸孔珩磨、油泵喷油器等关键零部件加工工艺开发能力不足,设备能力发挥不够,大批量加工质量和性能一致性较差;新一代喷油器、高压共轨等核心部件只能小批量实现自主生产;高端数控机床依赖进口设备,使用和维护成本高居不下,自主机床可靠性不足。总体来说,我国现有工业体系与智能制造、工业4.0等新技术发展的结合仍有待提高。
(1)发动机产品快速更新换代的制造需求 近10年来,中国产的发动机发生了翻天覆地的变化。具体表现在如下几个方面:高压缩比、高爆发力;小型化、精密化;轻量化;可控变结构。
(2)消费者需求发展和工业4.0带来的生产方式变革 “个性化、智能化、网络化”是工业4.0未来工厂的特点,智能制造发展的前提非常重要,如果没有做好“可靠性成本” 和“品质享受”,以及“节能环保”,一切都是“纸上谈兵”。其最终目的就是“快速响应市场的大规模定制”。
(3)国内市场激烈竞争带来的制造成本巨大压力 我国汽车发动机加工中高档数控加工机床、机器人等高端装备国外进口比例超过90%,刀具等基础部件和测试专机等严重依赖国外,重复引进,投资和维护成本高昂。
制造精度与产品性能
“智能制造”是一个“三位一体”的课题,首先要 “产品智能”,其次是“工艺智能”,最后才是“服务智能(售后服务、用户体验,等等)”。仅仅从制造层面、工艺层面空谈“智能制造” 是片面的,也是不可能实现的。
发动机缸体、缸盖、曲轴等核心部件,几何特征多、精度要求高、加工节拍快,宏观微观多尺度加工误差严重影响发动机服役性能。 我们目前研究讨论的重点、难点就是“静态精度”向“过程精度”控制的转变。发动机加工过程中多工序、宏观微观误差传递规律复杂,控制困难,这也是目前大学等科研院校和团体研究的内容,需要依托大量的模拟软件、大量且严格的检测设备、实验环境(如恒温、恒湿等等)。
发动机最终加工误差并非是单工序加工误差的简单累加,仅靠提升单工序加工精度,难以保证产品最终质量且成本高昂。我们亟待形成“产品—工艺—装备”的完整融合,借鉴智能制造和工业4.0,创新发动机工艺研发与生产模式。
总结来说,就是“市场引领产品,产品决定工艺,工艺带动装备” ——预测制造精度对使用性能的影响,以指导产品设计;合理分配各零件各尺寸公差,以指导生产制造。
制造技术路线图目标及核心制造技术课题
从质量控制试验工程(Q u a l i t y C o n t r o l Te s t Engineering)的四个方面出发,实现质量一流、成本最优、效率一流、制造绿色的动力总成精密制造的标准规范及制造体系。以“箱体”“轴齿”“毛坯”为分解目标, 分别在2020年、2025年和2030年三个节点,李喜咏介绍了制造技术的目标及其支撑技术。
1)到2020年,总成制造质量达到英法韩水平 , 动力总成总装环节后工序不良品率≤60ppm。从价值百分比角度衡量,装备国产化率≥50%。单位小时人均产出提升率≥10%,生产线自动化率≥50%,总成装配线开动率≥90%。工厂能耗下降比例5%。
2)到2025年,总成制造质量达到德日美水平,动力总成总装环节后工序不良品率≤30ppm。从价值百分比角度衡量,装备国产化率≥60%。单位小时人均产出提升率≥15%、生产线自动化率≥60%、总成装配线开动率≥94%。工厂能耗下降比例10%。
3)到2030年,总成制造质量达到国际领先水平,动力总成总装环节后工序不良品率≤15ppm。从价值百分比角度衡量,装备国产化率≥70%。单位小时人均产出提升率≥20%、生产线自动化率≥70%、总成装配线开动率≥96%。工厂能耗下降比例15%。
核心制造技术课题
(1)5C件制造技术 包括: 缸体制造技术——耐高温镁合金缸体制造技术、缸体内孔等离子喷涂技术;缸盖制造技术——缸盖气门座圈组合刀具加工技术、缸盖燃烧室容积数字化检测技术;曲轴制造技术—— 锻钢曲轴的制造技术、 曲轴圆角滚压强化技术、曲轴切点跟踪精密磨削技术;凸轮轴制造技术——金属塑料复合凸轮轴制造技术、 装配式凸轮轴滚花连接及装配技术;连杆制造技术——连杆裂解加工技术、 纤维强化铝合金连杆加工技术、 纤维强化铝合金连杆加工技术。
(2)其他关键零部件 包括: 变速器制造技术—— 齿轮干式切削技术、轴齿复合加工技术、变速器生产线装配机器人技术;活塞制造技术——活塞环耐磨涂层技术、直线电动机微进给活塞异形孔加工技术。
(3)共性技术 包括:整机尺寸公差设计技术、加工工艺数字化设计、毛坯精密制造技术、刀具技术、生产线数字化技术、生产线数字化技术和制造节能减排。
结语
智能制造的发展任重道远,业界把近70年的发展分为三个阶段。首先,是1956-2016年,传统智能阶段,初始的数字化制造工厂的建立。其次,是2016-2026 年,智能发展阶段,数字化孪生(数字化双胞胎)的计算模型构建。然后,是2026-2030年(新一代智能),基于计算机的数字模型,真正的现代制造、未来制造的腾飞并正式运营应用的阶段。让我们拭目以待。
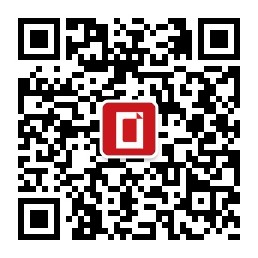