数智精耕,以实赋实,走进新华三未来工厂
- 来源:智能制造 smarty:if $article.tag?>
- 关键字:工厂,运输,数智精耕 smarty:/if?>
- 发布时间:2023-07-15 16:26
文/本刊编辑部 李国庆
在“数字大脑”的指挥下,机械臂在集成电路板上挥舞,60s内贴合7 000多个比蚂蚁还小的零部件,旁边是半人高的AGV无人运输车,有序穿梭在生产车间里……
在杭州萧山区,一座集合了5G、人工智能和工业互联网等新技术的新华三未来工厂,成为智能工厂建设的一面旗帜。
近日,在由机械工业信息研究院旗下《智能制造》杂志与新华三集团联合主办的2023智能制造高端沙龙期间,近百位来自制造业信息化领域的企业领导和技术专家一道参观了新华三未来工厂。
作为业界先进的智能制造样板工厂,同时也是浙江杭州智能制造实践的“网红打卡地”,新华三未来工厂应用的系列数字化解决方案,业已收获实效,同时具备可复制性,能够面向行业大规模应用,真正实现行业赋能。
为智能制造立标杆,为落地赋能树旗帜
回溯新华三未来工厂的建设时间节点,2019年8月,工厂正式举行开工仪式;2021年8月,工厂完成交付并全面启动设备进场和人员入驻。其中,一期投产的智能产线有2条,主要用于新华三高端服务器的生产制造,年产服务器50万台。
这座工厂建设初期便设立了几个重要目标。首先在高端智能制造方面,新华三要持续推进自主创新及研发能力,去打造世界级的高科技生态产业链;其次是优化供应链,其目的是为了今后企业能够拥有自研、自制和自销的全链化流程,能够对产品质量有更好的把控,对市场需求也能更快地做出响应;此外,在高端服务器制造方面,依托于新华三现有的信息技术,致力于打造业界领先的智能工厂样板点,并形成可复制的数字化工厂解决方案,向业界输出,推动整个产业链向数字化、智能化的转型持续迈进,整体带动产业发展,提升行业竞争力。
工厂落成之后,从智能研发、智能生产、智能物流到智能销售、智能服务和智慧园区等各个环节实现了数字化的打通,具有精益、智能、柔性、物联和绿色的先进性特征。
比如在精益方面,这座工厂实现了设计精益化、仓储物流精益化和生产精益化。通过设计立库打破各楼层限制,实现同等场地的储位最大化,利用U型线体和穿层物流,大大提高了周转效率,利用立库、多穿库、环形库协同AGV实现物料按需精准配送,使得物流自动化运作效率成倍提升。同时,工厂还打造了行业首创的全自动服务器主板组装线,实现单板加工(SMT)、单板组测、整机组测和包装的自动化生产,目前这座工厂人员同比减少60%,同时人均产出提升了5倍。
此外,在智能生产管理方面,基于工业4.0理念,通过数字孪生手段,工厂引入AI+5G技术,实现单板和整机检测方式的创新;使用智能测试系统,实现全面定制化测试创新。针对产品特点智能化配置,实现产线的柔性化与定制化业务需求。灵活、精准地开展智能产线规划。
值得一体的是,通过产品和工艺设计创新,高精度机器人和AGV自动上下料,首次实现单板加工无人化,整机加工少人化,整体加工自动化率达到88%,业界第一。同时,通过数字化运营管理中心,可实现生产现场可视化,生产各类实时数据的量化分析,现场管理效率提升50%。
而在智能设备管理方面,工厂通过工业物联网平台对全厂所有生产、物流设备进行联网和数据采集,实现设备的可视化和统一化管理。通过对设备数据监测和分析,可实现设备的异常主动预警、预防性维护等智能化应用,使设备稼动率提升15%。
深入核心场景,重塑“工厂上云”新价值
针对新华三未来工厂的整体业务战略,工厂还设计了一个既满足于当下,也能随需迭代的技术体系架构。总的来说,它脱胎于新华三的“数字大脑”计划,包括4个基础模块和N 个业务应用。其中的基础模块包括基于一体化设计的云边协同架构及主动安全和统一运维模块。
据了解,工厂设备通过各种边缘节点接入到本地云上,被采集的数据在云端汇总分析,在智能算法的加持下,管理员可以实时精准地掌握工厂的运营状态。在整个平台上能够同时支持传统的和云智原生的应用,可实现应用的敏态智能开发。目前已经上线了几十个应用,涵盖设备物联、MES、WMS、品控管理、物流和园区管理等。
通过此架构为新华三未来工厂提供一套稳定的、高性能的、可靠的和智能的支撑系统,在数字化、全连接、自动化和智能化等几个方面的能力取得了领先行业的地位。
电子信息制造行业正在由传统模式转向市场需求导向的模式。新的模式要求在运营管理过程中,需要对各个业务环节进行良好的运营管理。工厂面临的挑战就是在运营管理过程业务数据体量大、分布广泛、结构复杂且维度多,导致不能精准掌握企业现状,无法及时决策并有效预测企业未来状况,进而带来企业效率、质量和成本等方面的问题。
对此,新华三设计了一套基于智能架构的工厂治理云图系统。它能支持业务自定义的扩展模式,支持私有云、公有云及混合部署方式,能将工厂所有数据集中管理。支持业务场景化、可视化实时展现,现场感强,提升企业整体形象。通过数据采集、大数据模型和预测模型,对工厂数据进行立体实时分析,对未来业务场景进行模拟,为决策管理提供参考依据,降低运营风险。
设备智连和数据采集是新华三未来工厂实现数据化管理的基础条件。目前工厂已经可以实现对全厂设备资产的数字化统一管理,包括生产设备物联状态实时监控、设备参数程序随业务需求的自动调整和设备运维的全流程管控,通过构建新华三未来工厂设备物联互联互通的数采标准、接入标准和业务集成标准等基础能力,有效支撑生产管理的运转与执行。设备物联管理平台提供多源的边缘设备接入能力与强大的边缘计算能力,支持多种工业协议解析,提供可视化流式管理,提供设备精准运维管理,助力企业数字化生产,打造工业互联网标杆工厂。
同时,为交付质量更优的电子产品,新华三未来工厂设置了数字化产品研发生产基地,其中包括了人工智能技术的引入,主要是使用AI结合传统机器视觉对产品外观进行缺陷判断,并利用云计算技术,进行模型的迭代升级。基于AI模型的一体化品控服务,采用云、边、端一体化的架构, 云端实现在线标注、数据增广、模型训练、模型测试和模型下发等功能,采集端支持图像采集,边缘端进行图像处理和上传。
整个方案包括自动化设备、视觉系统、边缘工控机及软件。通过对接客户流水线产线,完成采图、OCR识别和缺陷分析判断等功能,具备可视化界面、复判功能服务及网络存储等功能,支持系统数据通信对接,实现产品缺陷特征的自动识别、归类及精准判断。
此外,品控云服务结合当下5G技术与AI深度学习技术的运用,克服了传统人工检验的过程质量不稳定问题,以及传统视觉模型无法优化升级等问题。
基于AI深度学习技术,实现随机瑕疵的有效判断,是生产制造企业成品外观检验新风向,基于云端模型可实现行业方案的快速复制快速应用到新产线,将大量减少产线人员,推进制造工厂检测升级,提高品质管控的量化水平,提升行业的数字化运作能力,提高企业的生产力和生产效益,推动产业的智能化进程。
“5G+工业互联网”实践标杆
在服务器中,单板作为硬件智能控制的中枢平台,是整个生产制造流程的核心之一。在新华三未来工厂的单板生产线上,5G的创新技术全方位地融入到了生产、控制和检测的各个环节。现在,SPI锡膏检测设备、AOI自动光学检测机等专业设备都能通过5G专网接入边缘算力平台,在5G网络的加持之下,智能化的生产线能让几千个零部件在极短时间内快速组合,全方位的AI视觉检测更保证了产品品质,为数字世界筑造起了坚实有力的算力中枢。
在服务器的生产过程中,把内存条、电源和硬盘等等组件快速精准地组合在一起,是整个制程中最复杂、难度最高的工序之一。在智能工厂全国第一条全自动服务器整机组装线上,无数的机械臂通过5G网络接受着来自云端的统一指令,仅用几分钟就能快速变线,生产完之后还要经过工业相机360°的全面检测,不放过任何一处细小的缺陷。
新华三未来工厂已成为“5G+智能工厂”实践的标杆。在生产制造环节,通过应用5G相关技术,达到了降本增效的目的,为“5G+工业互联网”应用树立了行业典范。
面对未来工厂全设备感知及产业链协同的特点,为了满足未来工厂在业务协同和数据交互方面的新需求,对应的5G技术也需要不断更新迭代。在智能工厂中,通过5G定制专网及定制云网技术,实现了网络的精细化切分,以满足内部外部不同场景的需求。
基于5G技术的超强能力,提供3C制造业对网络的高带宽、低时延和海量接入的新的想象空间,使能制造业降本增效。新华三未来工厂也在若干场景采用了5G方案。
首先是场内物流5G + AGV,AGV在不同物料搬运中体现的柔性化、准时化优势,从而形成一个完整的无标识智能搬运AGV系统,提升货物管理、安全和准确性。
其次是质量品质管理。5G+AOI/AXI/SPI,通过5G网络为无线通信底座,结合AOI/AXI/SPI进行自动化检测,准确无误的发现产品瑕疵,精确定位问题产品,提升产品高质量和良好口碑,减少停机时间,优化生产质量并减少操作员的工作负荷,使用集中式的控制和数据分析进行互操作。
第三方面是5G+AR/VR的应用,实现装配工艺的模拟和优化,提高概念设计的效率,精简设计单位和更加有效地进行工厂规划、客户沟通,虚拟现实与智能制造的“虚实融合”。
据了解,整个5G端到端解决方案分为5个部分,分别是生产设备地终端层、完成终端设备接入5G网络地接入设备层、5G网络部分、提供云服务的园区数据中心及在其之上运行的各种行业应用服务层。新华三具备端到端全场景解决方案的能力,涵盖了基础工程、网络、平台、应用服务和运营管理,提供多种网络接入方式:有线、无线wifi、5G和UWB;在平台侧通过新华三园区数字平台和紫光工业互联网平台进行纳管,并实现工厂的智能安防、AGV调度、能耗管理和高精度定位等智慧工厂业务;实现制造行业数字智能化转型。
在这座智能工厂里,新华三集团以5G、AI等云智原生的技术创新,定义了未来工厂进化的方向。
在工厂里掀起绿色化浪潮
作为一场广泛而深刻的经济社会系统性变革,实现碳达峰和碳中和是我国一项重大战略决策。在“双碳”战略和“数字浙江”目标指引下,新华三集团一直致力于积极探索双碳演化路径。
新华三未来工厂是双碳时代下节能减排领域的标杆案例,也是新华三在零碳智慧园区建设中的典型代表。新华三未来工厂数字化和绿色化转型进程中,新华三集团充分发挥自身优势,同时集结行业生态资源,以新华三数字大脑为核心底座,整合物联、视频、5G、云计算、大数据、AI和工业互联网等最新技术能力,形成数字化双碳智慧平台,并从产业层、企业层和园区层3层实践电子行业全面双碳数字化管理,打造国内领先的工业4.0样板点,最终实现“智能工厂”解决方案的产品化。
在新能源方面,通过利用新能源技术和储能技术,可明显改善厂区碳排放现状并减少能源支出。以新华三未来工厂实施光伏工程为例,可根据工厂可用屋顶面积进行屋顶光伏铺设,光伏铺设面积1万m2,装机容量1 000kW,实现电力自发自用,并利用余电上网,使屋顶利用率最大化。
新华三智慧园区解决方案以绿洲平台为核心底座,整合物联、视频、大数据和AI等新ICT能力,赋能各行业园区实现数字化转型。当前已服务超过50个智慧园区。
近年来,新华三集团加快推进“数实融合”,将数字化变革与促进“碳中和”结合起来,并针对零碳智慧园区建设,在业界率先提出“1+4+N”顶层设计理念,从源、探、管和服4个维度,全面赋能传统工业园区加快绿色低碳转型。如今,新华三除率先通过在新华三未来工厂开展数据驱动的双碳实践,树立行业标杆之外,还以模块化自由组合的方式对外输出方案能力。截至目前,该方案已在百行百业的众多园区落地实施。
写在最后
当前,新一代信息技术与先进制造技术融合发展,已成为新一轮产业变革的鲜明特色,正在驱动全球产业链、价值链发生深刻变化。党的十八大以来,我国智能制造应用规模和发展水平大幅跃升,制造业智能化发展成效明显。目前,我国已建成2 100多个高水平的数字化车间和智能工厂。其中,209家示范标杆工厂开展智能化改造后,产品研发周期缩短20.7%,生产效率提升34.8%,不良品率降低27.4%,碳排放减少21.2%。
据悉,未来,工信部将落实《“十四五”智能制造发展规划》,持续开展智能制造试点示范行动,特别是围绕设计、生产、管理和服务等制造全流程,挖掘一批低成本、模块化、可落地、易推广且带动意义强的智能制造典型场景,建设细分行业智能制造示范工厂,探索智能制造最佳实践推广路径。
新华三未来工厂在战略规划、管理运营、模式创新和信息网络平台建设等方面全面布局。通过利用新一代信息技术与制造业的融合,建立全链条、高效协同的全生命周期的服务型制造模式,实现企业生产的数字化、集成化、平台化,正在成为智能工厂的新标杆。同时,新华三也正在积极发挥旗舰型企业、链主型企业作用,将这座未来工厂打造为智能工厂样板点,向外界输出“工业互联网与数字化智能工厂解决方案”最佳实践,助力制造业转型升级。
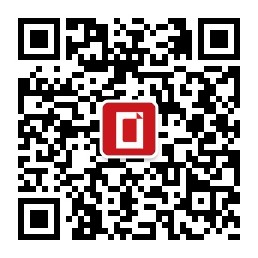