新的增材打印技术即将占领市场?
- 来源:国际汽车设计及制造 smarty:if $article.tag?>
- 关键字:打印,技术,市场 smarty:/if?>
- 发布时间:2024-03-23 12:51
本刊编辑整理
作为一种新型数字化制造技术,近年来增材制造(AM)技术在各个领域展现出巨大的潜力。据报告,全球整个工业增材制造市场2022年价值95.3亿欧元,预计到2027年市场规模将达到215.8亿欧元,年复合年增长率(CAGR)为17.7%。其中,我国汽车市场,尤其是新能源汽车的高速增长成为增材制造产业蓬勃发展的强劲动力。
增材制造技术在汽车零部件开发和赛车零部件制造领域的应用已有二十余年,主要围绕着以下几点展开:
1、快速实现设计件;
2、结构复杂零件的直接制作;
3、轻量化结部零件;
4、专用工件和检测器具的定制;
5、整车制作;
6、维修及数字备件仓库。
不可否认,增材制造技术在少量复杂零件生产的快速实现和一体化设计上具有无可替代的优势,但在大批量自动化加工上,增材制造的瓶颈同样非常突出。
目前增材制造可用材料种类仅200余种,分为金属、工程塑料、陶瓷、树脂和其它材料。细分到某个应用领域时,能用的材料就更少了。由于加工方式特殊,3D打印的原材料成本较高,每公斤金属粉末的价格可达上百甚至千余元。此外目前最快的3D打印设备每小时只能生产100cm3的零部件。加工材料、加工速度和成本上的缺陷使得3D打印技术似乎更适合留在设计院。因此,研发企业大多从“新技术”“新材料”“新应用”“新工具”入手,弥补目前增材制造大批量生产的短板。
新技术:粘结剂喷射技术应用快速增长
技术方面,激光粉末床熔融技术是目前应用最多的增材制造技术之一,受限于成本、材料和速度的要求,主要应用于小批量、高价值应用。例如通用汽车使用激光粉末床熔融技术将汽车传统座椅支架的八个组件整合为一个组件;布加迪制造了新款凯龙制动钳;保时捷设计了铝合金发动机外壳原型;宝马为i8 Roadster跑车批量打印软顶支架等。
相比之下,粘结剂喷射金属3D打印更适合于大批量零件制造。它的设备成本比传统3D打印机低,打印速度是激光粉末床熔融设备的几十倍至上百倍不等;采用传统MIM材料打印,原料成本、成品成本更低。
以美国Desktop Metal的大规模金属3D打印系统为例,设备包含超16000个喷嘴,每秒出墨15亿滴,具有1200x1200DPI的原始分辨率,堆积效率可达12,000cm3/小时,每天多达10,000个零件。因此粘结剂喷射金属3D打印更适合代替已有零件生产方式,实现大批量制造。
基于以上优势,主流车企正在加快粘结剂喷射金属3D打印技术落地。比如大众汽车与惠普紧密合作,2021年其德国工厂使用粘合剂喷射 3D 打印制造组件,成为首家在生产过程中使用该技术的汽车制造商;2022年,宝马成为Desktop Metal(DM)的主要投资者之一,DM在短短一年内获得了1690万美元的订单,主要为数字铸造动力集成部件。
在我国,粘结剂喷射金属3D打印技术起步较晚,目前国内相关企业有北京隆源、墨科瑞、易制科技等约20-30家,但缺少大规模应用市场。
其中,北京隆源于2018-2020年间完成粘结剂喷射金属3D打印开发,推出了AFS-J120、AFS-J380、AFS-J380L系列设备。该系列设备搭建集成了小粒径(5~15μm)低流动性粉末精准供料系统、新型铺粉辊压系统和高精度喷墨打印系统(1200dpi),可实现±0.1mm的打印精度、>3600cc/h的打印速度及>55%的素坯致密度;墨科瑞研发了粘结剂喷射金属3D打印低温烧结技术,该技术将全新的金属“生坯”低温钎焊烧结(Brazing)技术融入到常规粘结剂喷射金属3D打印的后处理烧结过程中,可获得致密的几乎没有收缩和非对称变形的金属部件。此外,其还研发了多款环保型水性粘结剂喷射金属3D打印用墨水,填补了国内空白;易制科技是目前国内少数掌握了从软件到材料和烧结工艺全套技术的主要团队之一,并已在多个应用场景开始尝试批量化应用。
数据显示,金属3D打印系统每年的销售量接近2250台。其中激光粉末床熔融技术在全球增材制造中占最大比重,累积拥有近17,000台的安装体量。金属粘结剂喷射设备仅有100-200台,但已呈快速增长趋势。尤其是DM的金属粘结剂喷射打印机,已成为当下市场的领导者,惠普、GE等企业也在加速相关设备的入市。预计未来五年内,金属粘结剂喷射设备的销量将有3-6倍的增长,以取代复杂的机械加工、金属注射成型、压制烧结等传统加工技术。
新材料:占据更广阔的市场
新技术的诞生对材料的发展同样起到了推进作用,有的技术会提升成品性能而提高材料的要求,有些技术则会降低材料性能要求的门槛。粘结剂喷射金属3D打印技术就属于后者。
由于粘结剂喷射金属3D打印技术是冷成型且与MIM技术有重合性,所以可以使用MIM的现有材料体系,具有巨大的供应链优势。我国材料供应链的提供相对完善,且具有更广的材料选择。
同时,随着技术的突破,可用于粘结剂喷射金属3D打印加工的材料种类也越来越多。例如今年3月,Desktop Metal宣布,采用自家的Production System™粘结剂喷射金属3D打印机成功攻克Ti64钛合金与C18150铜合金制造。至此,DM完成攻克粘结剂喷射金属3D打印最为难以成形的钛、铝、铜合金的制造,全面突破材料、加工速度、应用领域的瓶颈。
其中,Ti64钛合金成形工艺的攻克是DM与TriTech Titanium Parts公司合作完成的,通过打印生坯,真空中烧结至约98%的密度,按需后处理或表面精加工,可实现大批量的钵合金精密零件制造;C18150铜合金制造工艺是DM与山特维克共同完成的,后者开发提供C18150粉末,在P-1机型上完成打印并烧结后可获得98-99%致密度,能够满足汽车制造商的使用需求。C18150是一种兼具强度、导电和耐腐蚀性的铬锆铜合金,广泛适用于工业和商业应用。它能够承受高达500°C的工作温度,使其成为汽车行业发动机应用的理想选择。
此外,对粘结剂喷射金属3D打印技术而言,粘结剂的重要性甚至高于加工材料。目前常见的粘结剂共有5种,可满足常用金属材料,某些陶瓷材料,复合材料(渗铜材料等)加工需要:
●NFuse:悬浮纳米颗粒,提高烧结后的致密度
●CFuse:不增碳,适合对碳敏感的金属材料
●AFuse:水基粘结剂适用于大多数金属材料
●FFuse:适用于各种金属材料和非金属材料
●PFuse:耐高温材料和非金属材料
新应用:能否帮助新能源车电池实现突破?
先说结论:增材制造打印新能源电池的市场还处于早期阶段。好消息是,目前已有一些公司正试图将相关技术商业化并已经取得了可喜的进展。
据预计,在2020年至2030年内,3D打印电池市场将以19.53%的复合年均增长率速度扩张。尽管推动3D打印电池的终端需求主要集中在可穿戴设备和物联网(IoT)传感器,但3D打印电池高能量密度使得新能源汽车电池同样看到了续航极限的突破口。
例如,瑞士投资公司黑石资源(Blackstone Resources)目标在2025年之前将一种新的3D打印钠离子电池推向市场;固态电池技术开发商Sakuu Corporation (前身为KeraCel Inc.)也打算在2023年推出800Wh/L的能量密度高性能3D打印电池,并于同年开发能量密度超过1200 Wh/L的第二代全打印电池,预计到2028年达到60GWh的电池产能。另一家3D 打印电池公司Blackstone在产品成熟度方面比Sakuu更进一步,已于 2021 年打印出其首款功能性电池。其独有的“厚层技术”核心是3D丝网打印技术,比传统电池制造便宜30%,并且可用于液态电解质和固态电池。
国内方面,4月25日,高能数造宣布与广发证券达成合作,正式开启IPO筹划。如果成功,这将是国内首家上市的3D打印电池设备产业化公司。目前,高能数造已上市了3款S系列电池专用型3D打印机,今年3月21日推出了全新一代全固态电池3D打印机——TOP.E M20。据官方介绍,新一代全固态电池3D打印机不仅能够轻松实现10μm层厚电解质薄膜的高效率打印制造,还实现电解质层和电极层的阶梯化设计,且保证各电池内部各层级间整体制造高度一致性与稳定性,为电池性能的提升提供了更加广阔的想象空间。
新工具:打印软件&研发平台,为AM插上翅膀
“好马配好鞍”,升级技术和材料更需要适合的打印软件系统。一般来说,大型车企出于机密保护,更多的采取核心部件自研+第三方合作的方式。比如,奥迪在几年前引进了3D打印公司Stratasys的打印系统;宝马于2020年6月开设了自己的3D打印中心;意大利汽车公司达拉拉与3D打印公司Conflux合作,为其三级方程式赛车制造热交换器。
国内更偏重于第三方合作,以追求更灵活更高效的设计节奏。比如一汽大众与华曙合作,设计、试产保险杠导轨支架等零部件;重庆金石仅需15天就能完成一辆汽车的整车模型试制。
线上平台的出现则进一步降低了应用门槛,缩短了设计周期。比如Fast Radius 云制造平台已为2000 多家客户提供服务,迄今为止已经制造了超过 1100 万个定制零件。当然资本也没放过这一风向,西门子、蔡司等巨头向线上打印初创公司MakerVerse投资超千万美元。
当然,增材制造的未来绝非粘结剂喷射金属技术一统天下,先不说市场的主流仍是激光粉末床熔融技术,未来还会有更多日趋成熟的打印技术加入市场竞争。但不可否认,增材制造技术已经成为公认的创新驱动源头,我们不仅希望能早日看到增材制造技术实现大规模高精度快速生产,同样希望能看到中国增材制造企业达到国际上游水平。
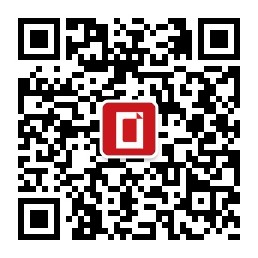