更强的竞争力
- 来源:国际金属加工商情 smarty:if $article.tag?>
- 关键字:竞争力,发展,因素 smarty:/if?>
- 发布时间:2024-04-14 14:19
本文由德国LiCON 公司供稿
作者:Nils Baumgartner
德国汉格斯特国际集团是滤清解决方案领域的专家,该集团十分信赖并依靠德国施瓦本地区的机床制造商LiCON 的解决方案来生产卡车和汽车过滤器壳体。这些方案包含两套自动化生产单元,由5 台双主轴加工中心组成,采用LiCON 自己生产的工装夹具和工件夹爪,以交钥匙方式交付使用。除了诸多经济性优点外,支持环境可持续发展也是汉格斯特国际集团选择LiCON 的决定性因素。
对于汉格斯特滤清系统国际集团来说,“可持续发展”很多年来一直起着决定性的作用。该公司不仅生产环保和健康的产品,而且其业务活动还全面转向经济及生态可持续发展。为了实现这些目标,汉格斯特集团一直在寻找新的解决方案。
若干年前,汉格斯特集团决定为他们的卡车和汽车过滤器壳体线扩充产能,所以投资了巴登- 符腾堡州劳普海姆镇的机床制造商LiCON 的两套自动化生产单元。这2 套LiCON 自动化生产单元的核心是5 台LiFLEX II766 双主轴加工中心,这些机床安装在汉格斯特集团的Nordwalde 工厂并以交钥匙方式投入生产。
其中较大的生产单元拥有3 台LiFLEX 双主轴加工中心,用于加工卡车过滤器壳体。而较小的生产单元拥有2台LiFLEX 双主轴加工中心,用于加工德国某高端品牌汽车过滤器壳体。通过投资LiCON 的双主轴机床,汉格斯特集团在成本效益和可持续发展方面获得了决定性的优势。
相比之前相同产能的单主轴机床,双主轴加工中心可节省占地面积约40%。因此,工厂每平方米的产能和产值得以显著提高,而这只是汉格斯特集团决定投资LiCON 双主轴机床的原因之一。
在接触LiCON 公司之前,汉格斯特集团采用的是单主轴四轴加工中心,因此加工过滤器壳体的5 个侧面至少需要2 次装夹。而LiCON 公司的五轴加工中心,只需一次装夹即可完全加工零件,因此可以避免多次装夹引起的误差,进一步提高成品的加工精度和一致性。
“为了便于扩充产能,每台机床独立加工完成成品是及其重要的。通过这种方式,每增加一台机床,便可以直接扩展产能。得益于 LiCON 公司的加工中心,我们成功地在汽车过滤器壳体线和卡车过滤器壳体线上做到了这一点。”汉格斯特集团工业工程部的 Hans-JoachimDaum 兴奋地说道。而他本人正是“卡车过滤器壳体”项目的总负责人。
“我们的加工中心的工作区域专为加工五面体的框架式夹具而设计。这使汉格斯特滤清系统能够以最佳方式进行产能爬坡,试生产阶段客户只需为每种零件订购一台机床即可。”LiCON 大客户经理Nils Baumgartner解释道。
微量润滑
在接触LiCON 公司之前,汉格斯特集团采用的是传统的乳化液作为工艺润滑,而现在使用的是先进的微量润滑工艺。该工艺将油雾混合物通过刀具中的冷却通道以特定的剂量输送到切削刃。 在工艺调试期间,LiCON针对各刀具和加工工艺优化相关的剂量参数,并把这些数据存储在 NC 程序中。该润滑工艺确保了加工后的工件“几乎干燥”,并可以从机床直接取出来,完全避免传统乳化液对机床及其环境的污染,而且方便直接回收并循环利用切削屑。此外,该工艺无需冷却液循环所需的泵和马达,这意味着可显著节省能源。
使采用微量润滑工艺的LiFLEX 双主轴加工中心平均耗电量为15 千瓦。与采用传统乳化液工艺的加工中心相比,每台加工中心每小时至少可节省 10 度的电能。按照年运行时间 5000 小时计算,每台加工中心每年可节省 5万度电,所有五台加工中心每年可节省 25 万度电。
模块化上料系统
汉格斯特滤清系统集团要求尽可能使用相同的机床来加工2 种尺寸相差很大的过滤器壳体。因此,LiCON最终选择相同的机床类型来加工大型和小型过滤壳体零件,但机床的上料配置有所不同,这归功于LiCON 的模块化设计理念。LiFLEX II 766 提供三种常见的上料配置:直接上料、双摇篮快换站和托盘快换站。加工该大型壳体零件需要较长的循环时间,所以LiCON 的LiFLEX II 766 iDL B2 加工中心采用直接上料配置,即上下料时候机床处于待机状态。该零件的上下料时间相对于整个循环时间占比小,所以配备一套快换站反而不经济。此外,直接上料和快换站相比可以减少50%的夹具数量和质量控制成本。而加工较小的汽车过滤器壳体,情况则截然不同。汉格斯特滤清系统工业工程部门的Marco Gerhard 这样解释他的项目:“由于汽车过滤器壳体的体积较小,循环时间明显比卡车过滤器壳体短,因此在加工的同时完成上下料是更经济的方案,为此LiCON采用了托盘快换站。在机床上,每套夹具可以装夹2 个汽车过滤器壳体,对应的每个主轴可以加工2 个零件,即每个循环在双主轴中加工4 个过滤器壳体。这使得加工效率又提高了 15%。
按需配置自动化
卡车过滤器壳体的生产单元一共有3 台加工中心,配备龙门架和顶置式行驶机器人,可以从机床上方上下料。为此LiCON 开发了灵活的四零件夹爪单元,可补偿铸件毛胚余量波动,同时抓取2 个毛坯和2 个成品零件,确保过滤器壳体准确无误地定位在工装夹具中。汽车过滤器壳体的生产单元包含2 台相对放置的加工中心,配备固定式机器人上下料。在2 个生产单元中,工人负责放置毛坯件在传送带上,各单元的缓冲区容量均允许无人运行。“自动线的灵活性对我们很重要,我们还希望可以进入加工区域并手动上下料,这样我们就能够在3 台高性能双主轴机床的任一台上小批量生产旧型的卡车过滤器壳体,所以顶置式机器人是我们最理想的选择。”工厂经理Michael Cedrola 支持这一决定并解释道。
高度自动化的生产系统需要透明的数据管理。该项目需要确保每个零件生产历史的可追溯性,所以每台加工中心都可以把所有重要数据提供给上级主机。此外,设备的传感器系统还可以监控刀具破损和加工质量问题,并提供必要的预防性维护分析。
一站式提供集成解决方案
汉格斯特滤清系统工业工程团队负责人Alf Bönisch认为,这样大型的项目必须尽可能采用一站式交付解决方案。“LiCON的整体交钥匙解决方案包括机床,工装夹具,自动化以及零件夹爪单元。该单元及其复杂,可同时夹持4 个零件,包括2 个毛坯和2 个成品。 由于工装夹具和零件夹爪单元的接口配合极具挑战性,所以由同一供应商设计和制造这2 套系统就很有必要。为了最大限度地缩短调试时间,LiCON 不仅模拟了整个工艺过程,而且提前进行虚拟调试,这为我们的项目节省了宝贵的时间。”Bönisch解释决定选择LiCON 的原因。
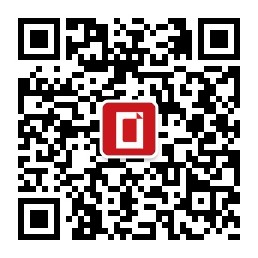