3D打印在液压行业的应用和挑战
- 来源:国际工业激光商情 smarty:if $article.tag?>
- 关键字:3D打印,液压行业,挑战 smarty:/if?>
- 发布时间:2024-06-15 18:06
上海商蔚机械科技有限公司成立于2003 年,经过20 年发展成为了一家高新技术企业。目前,公司主要经营精密液压阀和电液控制成套系统,产品包括比例控制阀、保压控制阀、方向控制阀、压力控制阀、流量控制调,以及电子控制器和电液控制成套系统等。值得一提的是,公司还是比例伺服阀性能完全达到国际标准样本参数要求的国内少有厂家之一。
两年前,在董事长陆林海的带领下,公司与国内某3D 打印设备商合作攻克3D 打印在液压行业的技术难关,目前距离产业化落地非常接近。在5 月初举办的2024 亚洲3D 打印、增材制造展览会上,陆总代表公司向现场嘉宾与业界同仁做了相关报告,介绍了当前国内外3D 打印技术在液压行业的应用。
改进设计,提升效率
相比其他行业,液压行业有其特殊之处,各种阀体的内部流道复杂,以往这些阀体只能通过铸造完成,但当遇到复杂内部流道时,传统工艺时常无法完成。3D 打印可以轻松解决阀体内部复杂流道的问题。对此,商蔚机械在两年前就开始了3D打印的创新之路,研发了阀体从铸造改用金属3D 打印的解决方案。
与其他工艺不同,应用3D 打印需要从流道设计就和液压工程师紧密合作,确保阀体结构设计符合行业标准,保证流道的产品属性和质量稳定。公司的第一款3D打印阀体试验产品,历经大约4-5 个月时间。陆总坦言,当初没有选择行业普遍采用的激光熔覆技术,也是考虑到成本问题。因为激光熔覆的打印成本偏高,1 克的生产成本就能达到2 元甚至更高,而传统铸造的造价只有1 角/ 吨,两者相差太大。即使激光熔覆可以满足阀体的相关设计要求,但对于液压行业而言也是难以承受的。因此,公司采用了粘结剂喷射金属3D 打印技术,经实际测算,该技术的生产成本可降至激光熔覆的四分之一。
3D打印不仅改变了阀体的流道设计,还颠覆了工艺流程。过去,公司在设计阀体产品时往往是由外到内,逐层深入进行。采用3D 打印方法,可以让设计师先进行管道设计,让复杂流道成为可能。3D 打印的最大魅力就在于,当有一个好设计的想法时就可以快速落地实现。
通过3D 打印,实现了对阀体内部流道的优化设计,同时也给后续验证提供了便利。过去,铸造开模的费用是几万元,周期至少需要两个月,如果需要修改模具,产品的开发周期则更长。现在,经过3D 打印的原型零件可以非常方便地做流场分析,降低企业损失,分析后还可以做二次优化,大大缩短了产品开发周期,实现了产品结构优化迭代的快速提升。
具体到单类产品,以比例伺服阀和电磁转向控制阀为例,运用3D 打印技术可以让阀体产品的结构设计和性能优化得到很大的提升。通过3D 打印,不仅可以改变比例伺服阀的外壳设计,还能改变其内部结构,减轻衔铁和阀心重量以提高频响。在电磁转向控制阀方面,3D 打印技术让阀体具有良好的耐腐蚀性和机械性能,改建内部设计获得更高效的流道组合。
稳定性和可持续,是企业的核心诉求
当前,3D 打印在国内液压行业的应用还处于起步阶段。尽管该技术具有先天优势,可以满足企业对打印产品快速测试验证的要求。但粘结剂喷射金属3D 打印技术有其局限性。打印后的阀体需要经过烧结后才能完全成型,期间,零件会出现不同方向上的应力收缩,甚至还会出现破损和开裂的情况。同时,由于行业对于阀体内孔加工精度有很高的要求,因此需要特别控制烧结温度,这对最终的阀体质量至关重要。
目前,公司正在和国内3D 打印设备供应商紧密合作,希望加快产业化落地。将阀体的铸铁材料转换成不锈钢,如果能解决加工精度和烧结变形等问题,不锈钢阀体凭借耐腐蚀性能将有广阔的应用前景。当前,国内在粘结剂喷射金属3D 打印方面,与国外的产业应用有较大差距。在国产化替代浪潮的推动下,国产打印设备是否经得起市场和规模生产的检验,这也是当下液压企业普遍关心的问题。
陆总表示,如果一项技术再好但只停留在实验室阶段,没有进行产业化,那终将不是一项好技术。中国制造2025 工业强基里面,提到的核心基础是零部件、液压件。他相信,随着3D 打印技术的逐渐成熟并被行业用户接纳,未来液压行业也将搭上3D 打印顺风车,助力国产化替代,实现在高端市场上替代进口产品。
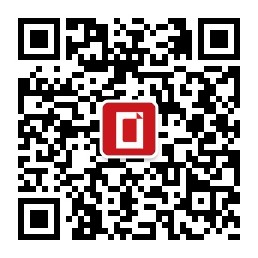