增材制造中的金属粉末:探索可持续生产、使用和回收利用(上)
- 来源:国际工业激光商情 smarty:if $article.tag?>
- 关键字:金属,粉末,回收 smarty:/if?>
- 发布时间:2024-07-09 17:12
本刊编译整理
当前,可持续性已上升到全球制造业议程的首位。虽然金属增材制造被认为是一种绿色技术,但其生产过程并非对环境没有影响。本文探讨了全球如何通过使用更具可持续性的金属粉末,同时更注重粉末的再利用和再循环,以此改善对环境产生的影响。当然,与此密不可分的还有经济收益,以及在供应链方面的国家安全利益。
在过去五年,对于增材制造零件生产商来说,金属增材制造的“可持续性”始终是一个重要问题,即使他们没有表明。现在,绿色政策和倡议已经上升到决策者议程的首位。本文将尝试深入探讨材料的回收利用,包括其实际含义以及实现可持续发展背后的现实。
废料凸显可持续性
现在,许多粉末供应商和材料生产商会经常谈论和宣传在可持续发展方面所做的努力。在去年举行的欧洲PM2023 全体会议上。Tikomet Oy 公司的研发主管TeemuKarhumaa 说:“废料是新的黄金”。他还指出,随着全球都在努力降低金属材料的生产成本以及生产过程中对环境的影响,在不久的将来,二次原材料将面临巨大的竞争。这确实凸显了回收材料用于生产金属粉末的潜在价值。
材料供应链的可持续性可能一直是废金属行业的驱动力。任何从事钢材或铝合金生产的人,都不认为废金属回收是一个新概念,而是会告诉你,废金属是一种关键原材料。不过,人们可能没有意识到,回收材料已被大量用于生产普通金属粉末。
例如,很难想象任何年产量达数千吨钢的粉末生产商,不依赖废料来降低成本。只是在此之前,他们可能不太愿意公开这一事实。不过,考虑到世界上有大量的不锈钢废料(镍基合金、铝和铜也很可能如此,但活性金属可能不是这样),这样做是完全合理的。
在可持续发展成为各行各业和各国政府关注的主流领域前,粉末冶金领域(包括金属注射成型、冲压和烧结以及热等静压)各种零件的产出,都含有回收材料粉末。在这方面,循环经济也并非新鲜事物。
然而在金属增材制造的早期,那些粉末生产企业很可能是利用预合金坯料或将元素直接引入坩埚来生产粉末。现在,随着人们认识到保护环境是工业界的责任,可以看到创建更清洁、更可持续的金属粉末供应链,用于增材制造。如果不出意外,随着更广泛的最终用户和消费者提出相应要求,很可能成为许多购买决策中的差异化因素。
在去年的Formnext 展览会上,包括Tekna 和Höganäs在内的几家主流供应商都将展览的部分重点放在了回收利用和可持续发展上。增材制造设备供应商EOS 表示,今年将对其粉末规格进行修改,首先从AlSi10Mg 开始。该公司现在要求供应商在任何原料中至少包含30% 的可回收材料,并声称这将使二氧化碳排放量减少25%。
金属增材制造技术为在全球范围内引领可持续制造提供了绝佳机会。与那些被视为“传统”工艺相比,有可能使用更少的材料和能源,对环境造成更小的影响。
增材制造的现状
十多年前,增材制造刚开始流行时,它是作为一种更环保的零件生产方式而出现的。当时增材制造只使用成品中的少量材料,同时,关于增材制造几乎零浪费的说法不绝于耳。然而,随着时间的推移,人们逐渐明白,事实并非如此;根据所选工艺,会产生固有的损耗水平。例如,使用激光粉末床熔融设备,保守估计每次生产的粉末损耗量为分配粉末的5-15% 之间。
金属粉末在增材制造中的应用无疑将继续增长。这不仅适用于已经普遍使用的合金,还将包括越来越多的其他合金,这主要是由于使用金属粉末的打印设备发生了两大变化。首先,随着设备越来越大,生产零件的能力越来越强,它们需要更多的粉末填充。其次是设备的多样化。过去,粉末床熔融占据主导地位,而现在,电子束粉末床熔融、定向能沉积、粘结剂喷射 、材料挤压和冷喷的市场也在不断扩大。
所有这些应用都在日益普及,需要粒度分布相似或重叠的金属粉末等级。所有这些应用都在与其他传统的粉末冶金应用竞争,预计这些应用对粉末的需求也会增加。随着每种增材制造工艺采用率的增加,这些粉末的废料流也会随之增加。就可持续性而言,每种金属粉末可能是过滤系统中流失的粉末、增材制造机器机械装置中夹带的粉末,或者是部件或其支撑结构封闭体积中包含的粉末。对于后两种情况,人们一直在努力回收这些粉末,以再利用。
材料挤压
在所有增材制造工艺中,材料挤压成型技术可能是最具有内在可持续性的工艺。在这种工艺中,细金属粉末与粘合剂混合,生产出丝状、棒状或颗粒状的材料,因此该工艺不使用干燥、松散的粉末。由于没有飞溅物、滞留粉末、过量配料、冷凝物或进入过滤器或其他机器死角的粉末等工艺损失,因此损耗极低。使用这种技术,最接近于只使用制造零件所需的材料,而且通常情况下,任何未烧结的材料都可以直接用于生产新的原料。
粘结剂喷射
可持续发展的下一个方向是粘结剂喷射。尽管从技术上讲,这是一种粉末床技术,但它不涉及加工过程中的熔化,而且粉末回收率非常高。被截留的粉末可能会造成少量损失,粘结剂的杂散喷射进入粉末床可能会造成污染,但与基于熔融的工艺相比,使用过的粉末的可回收性应该会更高。
粉末床熔融
粉末床层熔融工艺要比上述工艺复杂一些,因为它们的损耗比上述工艺更大。在熔化过程中,粉末有可能以喷溅颗粒或其他喷出物(如烟雾、冷凝水和细粉)的形式流失。后两类颗粒有时会被严重氧化,因此通常不考虑再利用或回收。这些废物流的去向仍然是个问题;它们很可能被填埋或焚烧。
长期以来,粉末床身熔融设备中所谓的“粉末回收”(在使用粉末制造零件的情况下,实际上应称为粉末再利用)一直是一个令人担忧的问题,而且必须比其他增材制造工艺受到更严格的控制。必须比其他增材制造工艺受到更严格的控制。
一些最终用户已经完全禁止使用曾经暴露在增材制造工艺任何部分的粉末;当然,这与增材制造是一套可持续的、更环保的工艺完全不符。然而,我们不难理解人们的担忧,因为该行业的早期采用者,本身就对重复使用暴露金属粉末的真正风险心存疑虑。
这可能是由于缺乏对工艺本身的了解、大气暴露对粉末的影响、成分退化或氧化增加,再加上评估使用过的粉末的手段不足,甚至是对不合格的新工艺的简单不信任。值得庆幸的是,这并没有让所有人望而却步。包括服务提供商在内的其他早期采用者,很快就意识到了这个问题并开发出了自己的方法来跟踪加工粉末的使用情况和质量。
因此,金属增材制造技术在一级方程式赛车、航天和医疗领域取得了显著成功。如今,行业标准(如SAEInternational 的AMS 7031)已经发布,规定了粉末重复使用的要求,特别是在 粉末床熔融设备中。该标准明确区分了两种粉末,一种是在设备中简单“翻转”并多次使用的粉末,另一种是从工艺中移除的粉末,经过修整后与新粉末无异,可以重新投入工艺。
对此,金属委员会还在编写另一份文件,以解决闭环送粉系统机器的建议问题。很明显,粉末的可持续性现在已成为任何粉末床熔融工艺的关键因素。
冷喷和直接能量沉积
冷喷(Cold Spray)和直接能量沉积(DED)这两种沉积技术的受欢迎程度,紧随粉末床熔融增材制造工艺之后。在冷喷增材制造中,没有熔融。相反,该工艺依靠极高的冲击能量来共同粘合金属颗粒。虽然这种工艺可以使用极少量的粉末,但会产生一定量的喷射粉末,目前还不能被认为是可重复使用的,必须在工艺结束后丢弃。
相反,在直接能量沉积打印设备中,引入的粉末是完全熔化的,可能会出现大面积的喷溅和其他与熔化有关的喷出颗粒,这些颗粒都不能在工艺中重复使用。在这两种工艺中,无论使用哪种气体进行喷射或保护,喷出的颗粒都很可能被严重氧化。在数量允许的情况下,最好的办法就是将它们收集起来,作为三级“废料”送回。
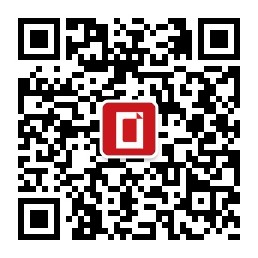