风电机组偏航静态偏差对发电性能的影响及优化方法探讨
- 来源:消费电子 smarty:if $article.tag?>
- 关键字:发电性能,影响,方法 smarty:/if?>
- 发布时间:2024-07-17 11:55
朱佳国 邸永杰
【摘 要】偏航静态偏差会引起机组输出功率的波动,导致机组发电性能下降,影响风电机组的整体运行效率和稳定性。本文分析了风电机组偏航静态偏差对发电性能的影响,并提出了风电机组偏航静态偏差的优化方法,希望为风电行业的可持续发展提供技术支持和实践参考。
【关键词】风电机组;偏航静态偏差;发电性能;影响;方法
引言
随着可再生能源领域的迅猛发展,风力发电作为其中的佼佼者,其在促进能源结构转型和应对气候变化方面发挥着举足轻重的作用。然而,在风力发电机组的运行过程中,偏航静态偏差现象普遍存在,这不仅影响了风电机组的发电效率,也给机组的稳定运行和维护管理带来了挑战。在此背景下,深入分析风电机组偏航静态偏差对发电性能的具体影响,并探索有效的优化方法,成为了提升风电机组性能、确保能源供应可靠性的关键议题。
一、风电机组偏航静态偏差对发电性能的影响
(一)降低风轮效率
风电机组偏航静态偏差是指风电机组在自动或者手动偏航过程中由于系统误差、环境因素或机械限制导致的与风向不完全对齐的状态,这种状态直接影响了风轮对风能的捕捉效率,进而对风电机组的发电性能产生显著影响。偏航静态偏差导致风轮与风向不完全对齐,风流通过风轮时产生的力矩减小,影响了风轮的旋转速度和稳定性。旋转速度的降低意味着单位时间内风能转换为机械能的效率降低,从而导致发电量下降。风轮效率的降低还会影响风电机组的风能利用率。在偏航静态偏差状态下,风轮叶片不能始终保持在接收最大风能的最佳角度,风能的损失在整个风轮的运转周期中是累积的,这种效率的降低使得风电机组的整体风能利用率下降,长期以往会对风电场的经济效益产生不利影响。偏航静态偏差还会影响风轮叶片的气动性能。当风轮与风向不完全对齐时,叶片所受的风力分布不均,这不仅会引起叶片振动,降低其工作的稳定性,还会因为局部过载而加速叶片材料的疲劳损伤[1]。
(二)增加结构疲劳
偏航静态偏差意味着风电机组在自动或手动偏航过程中,由于系统误差、环境因素或机械限制,未能使风轮与风向线完全对齐,从而在风轮和其他结构组件上产生非对称的风力载荷。这种非对称载荷首先导致风轮叶片和主轴受到周期性变化的应力,随着时间的推移,这些关键结构组件的材料将经历不断循环的拉伸和压缩,从而加速材料疲劳过程。结构疲劳是指材料在经历多次循环载荷后的性能退化,表现为裂纹的产生和扩展,最终可能导致结构失效。偏航静态偏差还会引起塔筒和基础的振动问题。由于风轮受到的风力不均,会在塔筒中产生循环的倾斜力矩,这种力矩会对塔筒的结构完整性构成威胁,特别是在风速较高的情况下,振动的影响会更为显著。长期来看,这种振动不仅可能导致结构连接件的松动,还会使塔筒底部的基础受到不均匀的载荷,进而影响整个风电机组的稳定性。在偏航静态偏差的影响下,风电机组的维护和检修工作也变得更加频繁和复杂。结构疲劳的积累可能导致关键部件提前进入维修或更换周期,给运营商带来额外的经济负担。
(三)影响功率曲线
偏航静态偏差使风轮与风向不完全对齐,导致风轮叶片接受的有效风速降低,风能捕捉效率下降,从而使得实际功率输出点偏离理想功率曲线。这种偏离不仅降低了风电机组在特定风速下的发电量,还增加了功率输出的波动性,使得风电机组的功率输出在不同风速下的可预测性下降。偏航静态偏差还会影响风电机组对风速变化的响应速度和精度。在风速变化时,风电机组需要通过调整叶片角度或偏航角度来适应风速变化,以维持最优的发电效率。然而,偏航静态偏差会降低调节系统的响应精度和效率,导致风电机组在风速变化时无法及时或准确地调整至最佳工作状态,从而影响功率曲线的平滑性和风电机组的整体发电性能。这种对风速变化响应的不足,不仅降低了风电机组的能量捕捉效率,还可能导致电网频率和电压的不稳定,影响电网的稳定运行[2]。功率曲线的不稳定性还会影响风电机组的经济效益。由于发电量的不确定性增加,风电项目的经济回报预测变得更加困难,增加了投资风险。(四)提高维护成本
风电机组偏航静态偏差导致风电机组的运行状态偏离最佳工作点,风轮叶片、偏航系统、传动系统等关键部件承受非理想的工作负荷,从而加速设备磨损和老化。特别是偏航系统,作为调整风轮迎风面的关键组成部分,偏航静态偏差会增加其操作频率和负载,导致其驱动电机、传动机械和控制系统等部件的过早磨损,维修和更换的成本随之增加。偏航静态偏差还可能导致风电机组内部的力学平衡被打破,风轮叶片、主轴和轴承等部件会因为非均匀的风力负载而出现应力集中,这不仅缩短了这些关键部件的使用寿命,还可能导致突发性的设备故障,增加了紧急维修和部件更换的风险和成本。偏航静态偏差对风电机组的控制系统提出了更高的要求。为了补偿偏航偏差带来的影响,控制系统需要进行更加频繁和精细的调整,这不仅增加了控制系统的工作负荷,还可能导致控制策略的复杂度提高。控制系统的频繁运行和复杂调整策略的实施,加速了控制设备的磨损和老化,提高了系统的维护成本。
二、风电机组偏航静态偏差的优化方法
(一)优化风轮设计
优化风电机组偏航静态偏差中的风轮设计主要涉及对风轮叶片的气动形状、结构设计和材料选择进行综合优化,以提高风轮在偏航条件下的性能。从气动形状的角度出发,对于叶片的气动形状设计,利用先进的计算流体动力学(CFD)软件进行精细的模拟,不仅模拟叶片在正常工作状态下的气流分布,更重要的是要模拟在偏航状态下的气流行为。特别是在不同偏航角度下,叶片的升力和阻力变化情况,通过调整叶片的扭曲和弯曲形状,实现在一定偏航角度范围内,叶片依然能够维持较高的气动效率。结构设计优化方面,利用有限元分析(FEA),工程师能够预测在不同的偏航角度和风速条件下,叶片会经历怎样的应力和变形。结合有限元分析(FEA)技术对叶片的结构应力分布进行分析,找出在偏航状态下受力集中的薄弱环节,通过结构优化设计提高叶片的抗疲劳能力。例如,可以在应力集中区增加局部的材料厚度,或者改变内部支撑结构的布局,以提升整个叶片的承载能力和使用寿命。在材料选择上,针对偏航条件下的特殊要求,选择更具韧性和抗疲劳裂纹扩展能力的先进复合材料,如碳纤维增强塑料(CFRP),并精确控制纤维的排列方向和层数,以适应叶片在偏航状态下复杂的受力条件[3]。通过精确控制纤维的排列方向和层数,可以进一步优化叶片的强度和弹性模量,确保叶片即使在复杂的偏航工况下也能保持良好的性能。利用智能材料和结构如形状记忆合金或压电材料,实现叶片在特定条件下的自适应变形。
(二)强化结构强度
为了提高风电机组在偏航状态下的整体稳定性和抗风能力,需要从多个角度进行综合考虑和精确实施。针对风电机组主要承载结构的优化,利用高级的结构分析软件如ANSYS或ABAQUS进行有限元分析(FEA),模拟在实际风场条件下,包括偏航静态偏差在内的多种复杂负载条件对结构的影响。这些分析不仅需要考虑静态负载,如重力和稳定风压,还要考虑动态负载,如阵风和风力机械负载。这种分析不仅能够揭示主轴、叶片和塔筒等部件在风力作用下的动态互作用,还能帮助工程师评估偏航载荷对风电机组整体结构稳定性的影响。在识别了这些潜在的薄弱环节后,采取针对性的强化措施来提高结构的整体强度和耐久性。例如,针对塔筒结构,可以在应力集中区增加壁厚或者采用更高强度的材料。对于塔筒底部,考虑到偏航静态偏差可能导致的不均匀负载,可以通过增加基础的尺寸和深度,以及使用高性能混凝土和加固钢筋,来提高其抗弯抗扭性能。对于叶片结构,除了在设计阶段选择合适的材料和结构布局外,还可以在运行阶段通过定期检查和维护来预防潜在的结构问题。例如,定期使用无损检测技术(如超声波检测或红外热像技术)检查叶片的内部结构,及时发现和修复裂纹和层间分离等问题。在风电机组的连接部件设计上,例如,在叶片与转子的连接处,可以设计具有更高承载能力的连接结构,采用经过特殊热处理工艺的高强度螺栓,并配备精密的拉伸加载设备,以确保连接部位在长期运行中能够承受周期性的偏航载荷而不产生松动。
(三)精确控制偏航角度
在传感器的选择和布置上,采用高精度的风向风速传感器,如光纤风向仪和激光多普勒风速仪(LiDAR),它们能够提供高分辨率和高频率的风场数据。这些传感器不仅安装在风电机组的主塔上,还布置在周边区域,形成一个传感网络,通过数据融合技术整合多点信息,提高对风场动态变化的感知精度。在控制算法方面,传统的偏航控制策略往往只依赖于当前风向传感器的数据,而先进的控制策略,采用实时数据处理和高级控制算法。通过实时数据处理平台,如基于边缘计算的处理节点,快速处理来自传感器网络的数据,并通过高级控制算法,如模型预测控制(MPC)或自适应控制策略,对偏航动作进行实时优化。这些算法不仅基于当前的风场状况,还能预测未来短期内的风场变化,从而提前调整偏航角度,以最大限度减少偏航误差。在偏航驱动系统方面,需要提高其响应速度和精确度。这通常需要对偏航驱动机构进行优化设计,在偏航执行机构的选择和优化上,采用高精度、快速响应的伺服电机和减速机构。这些执行机构的精确度和响应速度直接影响偏航控制的实际效果。通过对执行机构进行精确的动力学建模和参数调校,确保其能够精确执行控制命令。执行机构本身也配备高精度的位置传感器和力矩传感器,实现闭环控制,确保偏航角度的精确调整和实时监测。为了提升偏航控制策略的鲁棒性和可靠性,需要进行充分的测试和验证。包括进行大量的数值模拟和风洞实验,以验证控制策略在多种风速和风向条件下的性能。同时,也需要在实际风电机组上进行现场测试,收集实际运行数据,通过数据分析和机器学习技术不断优化控制策略,提高其在实际应用中的适应性和效果[4]。
(四)实施预测性维护
预测性维护是通过综合运用先进的监测技术、数据分析方法和维护策略来提前识别和解决潜在问题,从而降低偏航静态偏差对风电机组性能的影响。在监测技术方面,应用多种传感器对风电机组的关键部件,如叶片、主轴、齿轮箱和发电机等进行全面监测。这些传感器包括振动传感器、应力传感器、温度传感器和声发射传感器等,它们能够实时收集关于设备运行状态的详细数据。例如,振动传感器可以监测叶片或齿轮箱的振动水平,从而识别出结构疲劳或轴承损伤的迹象;温度传感器可以监测关键部件的温度变化,及时发现过热问题。在设备监测阶段,除了传统的振动、温度和声发射传感器外,还应引入更高级的监测设备,如基于光纤的应变传感器,以精确捕捉偏航静态偏差对风电机组结构带来的细微影响在数据处理阶段,利用高性能计算平台对收集到的大量数据进行处理和分析。通过时间序列分析、频谱分析和高级统计方法,可以从这些数据中提取出设备健康状况的关键指标。例如,通过分析叶片应变传感器的数据,可以精确识别由于偏航静态偏差导致的非对称负载,从而提早发现叶片或轴承的异常磨损。在故障诊断阶段,结合机器学习和人工智能技术,对提取的健康指标进行深入分析,从而实现对风电机组潜在故障的早期诊断。通过构建健康状态评估模型,如基于支持向量机(SVM)或神经网络的故障诊断模型,可以高效地对设备的运行状态进行评估,准确地预测设备的维护需求[5]。在维护决策阶段,基于故障诊断的结果,结合维护资源和运营成本,制定维护计划,不仅包括定期维护和紧急修理,还包括长期的设备性能优化和升级计划。
结语
基于对风电机组偏航静态偏差及其对发电性能影响的深入分析,实施有效的优化方法显得尤为关键。在未来的工程实践中,应持续优化和完善风轮设计、结构强度、偏航角度控制及预测性维护等策略,以确保风电机组在复杂多变的自然环境中稳定高效运行。通过科学的方法和先进的技术,不仅可以显著提升风电机组的运行效率,还能有效降低运维成本,为风电技术的持续发展和广泛应用奠定坚实基础。
参考文献:
[1] 刘传亮, 闫立鹏, 张成义, 等. 数据驱动风电机组偏航误差在线智能识别研究[J]. 可再生能源,2023,41(4):487-492.
[2] 刘栋, 王景丹, 卢晓光. 基于数据驱动的偏航偏差辨识及控制优化[J]. 自动化与仪表,2022,37(10):30-34.
[3] 庄勇, 吴士华, 林涛, 等. 大型风电机组偏航系统误差优化研究[J]. 中国设备工程,2021(22):14-16.
[4] 刘诗意, 张超宇, 王桐. 基于风向预测的风电机组偏航优化控制方法[J]. 风机技术,2023,65(4):55-59.
[5] 张团结. 风电机组偏航性能异常及检修方法分析[J]. 中国科技期刊数据库 工业A,2023,(12):035-038.
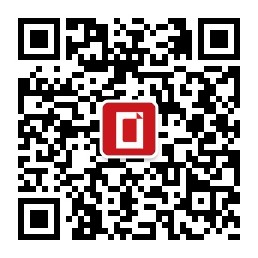