融合5G 丰富场景打造标杆工厂
- 来源:智能制造纵横 smarty:if $article.tag?>
- 关键字:5G,标杆,工厂 smarty:/if?>
- 发布时间:2024-09-08 16:00
某工程机械集团成立已有33年的历史,长期处于中国工程机械行业排头兵地位,目前位居世界工程机械行业前三位。其产品销售网络覆盖180多个国家及地区,年出口额连续30年保持国内行业首位。
集团向市场提供工程起重机械、路面机械、压实机械、铲土运输机械、混凝土机械、高空消防设备、建筑机械、特种专用车辆、液压件、工程机械专用底盘、驱动桥、回转支承、驾驶室、柴油机、齿轮箱、齿轮泵、工程轮胎等系列工程机械主机和基础零部件产品。
启程信息化建设
该集团的信息化发展历程,历经从世纪交替时期的信息化基础建设阶段,至2010年前后两化深度融合阶段,至十三五期间数字化提升阶段,一直到当前大数据时代下的智能化升级阶段。整个过程从上世纪80年代的“甩图板”起步,目前已经开始了以智能制造为主攻方向,全力推动智能化产品与智能施工能力;推进智造升级,融合5G丰富的场景打造标杆工厂;开展智能化服务,提供数字化产品,以支撑集团从战略控股型向战略经营型的转变,真正立足于工程机械行业之巅。
为了实现企业信息化向数字化和智能化的转变,集团统筹规划了新的IT架构:一方面在成熟的业务应用系统之上,依托新建的数据主线能力,实现全集团的业务流程贯通;另一方面从业务流程角度,围绕市场需求和产品战略、需求定义和设计立项、新品开发和设计复用、功能定义和结构配置、生产工艺和质量工程、原型模拟和测试、供应链管理、智能制造、产品营销和售后服务等核心业务领域,建立全球化、智慧化的战略经营支撑能力。
在进行智能化建设的过程中,该集团引入了PTC的产品。双方的合作起步于三维CAD设计PRO/E产品的导入,后来逐步采用了Windchill等PLM/SLM解决方案。
首先是产品研发智能化,当前该集团正与PTC合作建立“全球产品协同研发信息平台”。集团基于PTCWindchill PLM平台,整合研发和BOM数据,统一服务于各个产品事业部与研发相关的部门。实施横跨产品三维设计、研发项目管理、设计任务协同、市场营销共享,和面向工艺、测试、制造和质量合规等诸多业务场景的智能化建设方案。如面向平台化产品的需求实现TOPDOWN的产品设计;面向营销和生产效率的提升落地选装选配;面向集团所有的研发项目管理建立一体化、并行化、结构化、可视化和数字化的智慧项目管理体系框架等。
其次是面向产品服务的智能化,通过在产品设计阶段,将面向售后服务的需求、服务策略、FRU规则、指导手册架构和验证确认等服务环节要素,引入产品服务功能设计(DFS)规划。实现在智能产品服务流程管理中,基于数据分析提供零备件的预测和优化;以数据驱动的服务过程管理系统,支持人员效率的持续优化和知识库迭代。配合服务3D模型和现场物联网数据,将增强现实技术引入服务技工培训和服务现场交互性支持等。
打造智能工厂
当前,工程机械行业制造环节正面临着众多复杂且极具挑战性的场景,例如:
• 产品定制化程度高,非标和变异产品型号繁多,造成产品设计变化导致的工艺、材料甚至装备都经常需要调整和更新;
• 生产装备来源复杂,设备状态和工况难以监控、管理和进行绩效统计,维修保养和生产计划脱节等,导致运维成本和材料浪费难以控制;
• 实际生产过程中的工艺参数难以采集和汇总利用,质量缺陷缺乏预测性和可控性,违规作业时有发生,产品质量控制目标难以达成;
• 生产过程数据实时可见性无法满足,各类消耗统计延迟,生产成本和产出难以关联,生产管理和决策效率低下,精益化生产无以为据等。
为了解决这些问题,实现制造环节数字化和智能化的提升,2020年,该集团在智能工厂项目中引入PTC ThingworxIIoT平台,全力构建集团一体化设备互联互通平台,以实现“设备高效采集、数据深度挖掘、精益持续改善、效益明显提升”的目标,为公司数字化转型,智能工厂提质增效提供重要支撑。
在构建过程中,首先利用IoT平台,并结合5G、AR等新技术,在重点设备端实现数据高效采集,智能辅助维修以及对现场、资产和人员的集成管控。
其次,采用数字孪生框架,为运营端提供业务模式所需的资产可视性和互操作性、订单执行管控和追溯、生产实时绩效管理、质量预测和精益提升等支持。
在已经实施的第一期智能制造项目中,基于当前规划的业务场景,为了满足整个集团的承载力需求,实施了集群部署的架构,将Thingworx平台部署到集团的IT基础设施中。基于设备管理、生产绩效管理和数据分析工具,建立了工业物联网基础平台,并提供了系统集成接口和部分数字孪生和大数据分析创新应用。
当前实现的核心功能包括:
设备连接:采用Kapwar e采集复杂的自动化协议;Thingworx Edge SDK对接非标的自动化设备协议;第三方RTU采集环境和能源数据;通过RESTFUL方式对接MES等信息化系统。
设备管理:设备信息档案全记录;设备参数⸺采集点位及重要数据追溯;设备状态、指标实时监控⸺设备运维人员可以快速了解设备情况;带时间戳的状态参数⸺基于设备历史记录,为工艺人员提供大数据分析支撑;报警、点检、巡检、维保日志和知识库管理等。
生产管理:生产工艺、程序管理和执行过程参数监控;生产绩效管理⸺OEE等各类KPI看板和报告;工单与设备状态匹配度;产前检查、产中监控和产后追溯管理等。
维保管理:维修计划、设备状态监控、告警、故障报修、工单管理、维修日志、零备件管理和故障处理知识库⸺原因分析、知识增补、知识图谱和现场AR指导。
基于大数据分析的质量控制和工艺优化:设备数据分析⸺通过机器学习算法模型建立故障模型,提供故障预警;焊机数据分析管理⸺通过焊接故障控制实验,对数据进行分析,建立焊接机器学习算法模型;刀具数据分析⸺通过刀具故障控制实验,对数据进行分析,建立机器学习算法模型。
数字孪生:通过车间和单体设备的多个视角,展示设备实时加工姿态和实时数据,为不同角色提供设备相关的基本信息、效率信息、成本信息,以及报警信息。
工厂实施初具成效
经过一年的实施,该集团在工业互联网平台实现了设备数据全量采集和与MES/SCADA系统的全面打通。目前在设备综合管理层面已能了解设备健康度管理所涉及的设备实时数据,故障数据,运行数据,运维数据,实现生产设备的总体状态分析、预测告警和趋势分析,以及故障追溯和判断工具,指导排产、维护和优化。
同时在设备管理与生产管理相结合方面,实现了面向不同管理层级的设备绩效指标可视化和统计分析的综合看板、移动应用和数字孪生展示看板等业务应用。围绕业务需求制定大量的设备KPI指标,例如设备综合效率(OEE)、计划/24小时开机利用率、开机率、设备故障率、设备速度效率、保养执行率、点检执行率等,多角度、全方面考察设备管理全过程。同时这些KPI指标还可以在多个维度进行详细对比,结合工厂日历以及上下件报工,来形成精准的KPI情报,支撑精益化管理。
工艺及质量控制层面在机加工、焊接等关键工序,实现了工艺全流程管理、机加工质量超差缺陷控制告警和焊接质量缺陷告警等人工智能业务应用。
在工艺质量和设备维保智能化角度,基于工业物联网平台建立了设备故障知识库和故障根因统计分析、追溯和优化分析系统。如焊接设备的主要故障为寻位短路、送丝系统故障和撞枪,通过排除寻位系统故障、保养送丝回路、优化工装定位和焊接程序,可降低近80%的故障停机。目前该知识库积累了1万余条预置报警代码,系统支持处理方式不断的积累和迭代,形成智能化的知识分享机制。
结语
目前,该集团的工业互联网项目已经成功地进入了第二阶段。后续将进一步开发设备物联网与5G和AR技术相结合的创新应用,在充分挖掘物联网大数据支撑的智能化运营创新应用的同时,最大限度地推进企业数字化转型。以尽快获得工业互联网时代的核心竞争力,巩固和提高集团在全球工程机械行业排头兵地位。
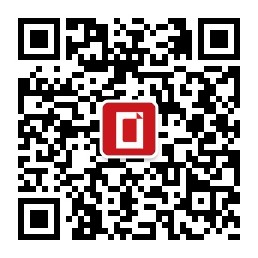