带有功能性IML 标签的单一材料医疗产品
- 来源:国际塑料商情 smarty:if $article.tag?>
- 关键字:功能性,标签,医疗 smarty:/if?>
- 发布时间:2024-09-21 13:43
本文翻译自Plastics Insights杂志
作者:Dr. Clemens Doriat
当Arburg 与Kebo AG 公司的首席战略官约翰内斯·斯特拉斯纳(Johannes Strassner)以及项目组的其他四名成员见面并讨论一种可用于医疗技术的新用途时,他直奔主题道:“迄今为止,这种产品的制造方式产生了巨大的机会成本。我们所讨论的是高达10% 的废品率。”机会成本是指公司在面临多种选择时因未选择最佳方案而损失的理论利润。
由五家合作伙伴——注塑机制造商Arburg、模具制造商Kebo、自动化专家Beck Automation、标签制造商MCC Verstraete 和塑料包装行业领先的光学检测系统供应商 Intravis 开发的替代方案涉及离心管的生产。数十亿个该塑料部件被用于医疗和制药行业。因此,受波及的资金量很大。它们的主要区别在于,在此之前,刻度体积标尺(标题图)是在注塑成型完成后通过单独的步骤印在管子上的;新工艺则通过模内贴标(IML)整合了这一步骤。
众多优势——包括可持续性
该生产线最初在Fakuma 2023展会上作为“概念验证”展出并获得了巨大反响,后于NPE 2024 展会上首次亮相北美市场。IML集成了众多优势,尤其是从可持续性的角度来看。斯特拉斯纳对此进行了罗列:“标签间接增加了离心管的稳定性,从而可以减小壁厚。这反过来又使制造商能够减少大规模生产所使用的塑料量。而且,由于管子和标签都是由 PP 制成,这种单一材料产品还具有回收潜力。”
接着,斯特拉斯纳补充了最重要的一点,即印刷和相关物流等容易出错的额外工作步骤被省去。“印刷是一个涉及湿介质的机械加工过程。高达10%的废品率是这里的常态,而非个例。标签的使用消除了液体涂料污染的问题。IML非常干净,适用于洁净室。”他说。得益于这条新生产线,整个生产过程快速、节省空间、经济高效,并且没有任何额外的卫生风险。由于IML可以轻松地从一种设计切换到另一种,因此可以带来更高的产量、更高的良品率和更大的灵活性。
精准渗透到每一步——从标签开始
该工艺的顺利运行要求所有生产线组件和生产步骤都具有很高的精度。这一要求从标签制作的初始步骤开始。MCC Verstraete 公司的欧洲销售和业务开发经理金·布朗迪尔(Kim Blondeel)解释说:“标签厚度仅为55μm,模切公差仅为0.2mm。包装产品IML 装饰的公差通常为1-1.5mm,外观和手感往往是次要的。但是,对于医疗产品而言,标签必须完全满足技术和功能要求。”除了坚固性和洁净加工外,标签尺寸小、经济性和大量供应等也很重要。还应注意的是,这些标签可以在实验室中使用,因为它们被印于背面,因此具有耐酒精和防刮擦性。
这种标签也可用于其他圆形部件,如胰岛素笔和医用量杯。“考虑到这项技术的潜力,这将是下一个逻辑步骤。”斯特拉斯纳证实。但是,这些标签还可以配备其他功能。布朗迪尔解释道:“一个附加的热敏元件可以让用户看到所需的冷却温度是否已达到。在我们最新的应用中,热致变色条带在低于7° C 的温度条件下会可逆地改变颜色,但也有可能实现不同的温度设置和不可逆的颜色变化。”
此外,每个标签上单独的二维码还可携带其他关于产品回收和仓库管理的诸多信息。布朗迪尔还认为,RFID 代码将来还能够跟踪流程、质量和患者数据,每个单独的部件都具有100% 可追溯性。为了实现患者与医生之间或居家护理应用之间顺畅的数字通信,这些数据必须安全智能地连接起来。
精确的标签定位
由于管子上的刻度用于表示准确的填充程度,因此薄膜嵌片的精确控制和背模成型至关重要。这一点通过Beck 公司提供的自动化技术来实现。该技术可确保标签在模腔中的位置尽可能精确,其标签调整头对生产公差进行了补偿,使其降至百分之几毫米(图1)。“这对于功能来说至关重要,并且还能显著减少质量波动和废品数量。”Beck Automation AG 公司的销售经理拉尔夫·齐默(Ralf Ziemer)说道。
工艺周期开始之初,配备四节夹爪的机器人从料盒中取出标签。然后,对齐和施加标签的技术将精度提升到了卓越的水平。“四个调整头每个都测量一个单独的标签。因此,每个标签在两个轴上朝一个角度移动。最后获得定位绝对准确的模腔测绘结果,它由Intravis 公司生产的摄像系统监监测。”齐默说。随后对标签进行静电充电以防止其滑落。接着,第二个同样配备了四节夹爪的机器人将它们拾取起来并精确地放置在嵌入型芯上(图2)。为了装载全部八个模腔,机器人在每个周期中需执行两次该操作。“因为周期时间约为10s,这些操作可以轻松完成。”齐默补充道。
生产单元适配预定义的生产网格
Kebo 公司生产的8 腔模具配有阀式热流道,可用于生产15 毫升的即用型PP 管。定位精度也得到了保证。“组件上的流边有助于将熔体以有利的流动角度引导到模腔中。”斯特拉斯纳解释道。此外,注塑机的伺服电力驱动可确保精确且可重复的模具定位。模具制造商的另一个准则是,考虑到低壁厚,模芯必须具有高刚性才能实现中心填充并最大限度地减少模芯错位。
生产单元紧凑的占地面积也有利于可持续性。ArburgGmbH + Co KG公司的医疗技术专家斯文·基茨林格(SvenKitzlinger)说道:“生产单元的占地面积可轻松融入预定义的生产网格。”其核心部件是一台Allrounder 520 AUltimate 电动注塑机,锁模力为1500kN,专为快速、严苛的工艺而设计,例如薄壁应用。这款高性能机器采用洁净室设计,符合ISO 7 级要求。基茨林格表示,直接驱动装置的温度由液体控制,并且使用了特殊的NSF-H1 类食品级润滑剂。
成型部件的实时光学检查
完成注塑成型并从模具中取出后,还需对部件进行实时检查(图3)。这一步通过集成在自动化系统中的四个Intravis 摄像头(型号:IMLWatcher)完成。“它们会检查刻度的位置是否正确以及浇口上是否有任意注塑成型误差,例如拉丝。任何细小的误差——尤其是标签定位方面的误差都可能造成重大影响。”Intravis GmbH 公司的国际销售经理马尔特·韦斯特曼(Malte Westermann)强调道。这些检查还包括管颈和螺纹以及印刷到切割偏移量的识别。如果检测到故障部件,检查单元直接向自动化系统发送信号,以便将有问题的部件弹出。IMLWatcher 控制面板还会显示发生的错误类型,方便生产人员做出决定是否进行干预。与传统的生产和下游印刷组合相比,该生产线处于有利地位:“这是一项非常成熟的技术,从一开始,废品率就低于1%。”韦斯特曼说。目前的重点是工艺验证。在实际应用中,生产单元还可用于将管子拧接起来并将它们装入流袋中。
那么接下来是什么?约翰内斯·斯特拉斯纳回答道:“我们收到了很多咨询,但在医疗/ 制药领域,你需要时间和耐心。无论如何,我们都有充分的理由和积极的经验。”关于项目联合体,他回答道:“继续合作有很多好处,因为我们一起完成的项目越多,我们就会变得越好。”
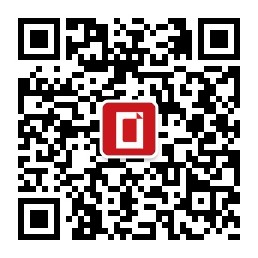