数字孪生:以“未来之眼”,透视智能制造变革之路
- 来源:智能制造纵横 smarty:if $article.tag?>
- 关键字:智能,制造,变革 smarty:/if?>
- 发布时间:2025-03-17 11:09
近日,NVIDIA宣布推出多个生成式AI模型和蓝图,进一步扩展其Omniverse一体化平台至物理AI应用,如机器人、自动驾驶汽车和视觉AI等。NVIDIA Omniverse是一个提供API、SDK和服务的平台,用于开发适用于工业数字化和物理AI仿真的OpenUSD应用。借助此平台,开发者可以将通用场景描述(OpenUSD)和RTX渲染技术集成到现有软件工具和仿真工作流中,以构建AI系统。
当前,NVIDIA Omniverse的数字孪生技术已经涵盖汽车、制造、建筑、能源、科学运算仿真等多个行业,与西门子、微软、罗克韦尔自动化等企业建立了合作关系,这些合作涵盖了工业制造、建筑设计、能源管理等多个领域和场景。在制造业,企业通过Omniverse平台可以创建数字孪生来设计、模拟、构建、运营和优化整个资产及工作流程,提升运营效率并节省成本。
技术发展现状及进步
据市场研究机构艾瑞咨询预计,2025年,中国数字孪生市场规模将跃升至375亿元人民币。这一增长背后,一方面是物联网、云计算、人工智能、大数据等多种前沿技术的集成应用,使得数字孪生技术能够进行全方位的仿真和管理,应用领域不断拓展。
纵观2024年,在数字孪生领域,有一些新的变化已经发生。
仿真建模技术提升:仿真建模技术的提升加快了数字孪生计算速度及模型构建效率,使得数字孪生模型更加精准和高效。
XR技术完善:XR(扩展现实)技术的完善带来了新型人机交互模式,提升了数字孪生的应用空间和交互性。通过XR技术,用户可以在虚拟环境中与数字孪生模型进行更直观的交互和操作。
大数据与人工智能融合:大数据和人工智能技术的融合应用,使得数字孪生能够更高效地处理和分析海量数据。通过机器学习算法,数字孪生可以实现对物理实体的实时监测、预测和优化,提高系统的智能化水平。
物联网技术集成:物联网技术的集成应用使得数字孪生能够实时获取物理实体的状态信息。
通过传感器网络,数字孪生可以实时监测设备的运行状态、环境参数等,为优化决策提供数据支持。
新型计算架构支持:随着云计算、边缘计算等新型计算架构的发展,数字孪生的计算能力和存储能力得到了显著提升。这些新型计算架构使得数字孪生能够更高效地处理和分析数据,同时降低了对本地硬件资源的依赖。
此外,国家对数字经济和相关技术的重视,为数字孪生领域的发展提供了政策扶持和推动。截至2024年1月,中国已有数字孪生相关国家标准2项,团体标准59项,标准化工作推进进程明显加快。
数字孪生正深度融入制造业
在制造企业中,数字孪生技术的应用日益广泛,如航空航天、汽车制造、机械设备等。通过构建物理对象的数字映射,实现虚拟与现实同步,数字孪生技术为制造业带来了显著成效。
在产品研发阶段,数字孪生技术可以支持三维建模,实现无纸化的零部件设计和装配设计,还能取代传统通过物理实验取得实验数据的研发方式,用计算、仿真等方式进行虚拟实验,从而简化、减少甚至取消物理实验,缩短产品的设计周期,提高产品研发的可行性、成功率,并降低试制和测试成本。
在生产制造阶段,数字孪生技术可以应用于生产制造过程从设备层、产线层到车间层、工厂层等不同的层级,对生产过程进行仿真、评估和优化,系统地规划工艺、设备和资源。同时,它还能实时监控生产工况,及时发现和应对生产过程中的各种异常和不稳定性,实现降本、增效、保质的目标和满足环保的要求。
随着技术的不断发展,数字孪生的关键技术如建模技术、渲染技术、仿真技术等也在持续突破:建模技术通过多种方法创建物理实体的数字模型,包括3D扫描、参数化建模和逆向工程等;渲染技术通过多种方法实现数字模型的逼真视觉效果,例如基于物理的渲染、实时渲染和云渲染等;仿真技术则基于构建好的3D模型,结合物理规律和机理,计算、分析和预测物理对象的未来状态。
这些关键技术的突破使得数字孪生在制造业中的应用场景不断拓展,从最初的产品设计、生产流程模拟到设备维护优化,再到现在的智能制造、智能工厂等。下面,以工程机械企业中联重科利用数字孪生技术构建塔机智能工厂项目为例进行阐述:
在数字化浪潮的推动下,中联重科积极致力于推动数字化和智能化转型,其塔机智能工厂通过引入数字孪生技术,来实现对工厂生产情况的全面感知和监测。
在技术应用方面,中联重科在塔机智能工厂部署了3D可视化大屏,展示了从工厂到工位的多级可视化界面,管理者可通过鼠标点击轻松切换场景,实时获取各级3D模型和2D图形信息,包括用途、进度、运行状态、预警告警等,实现快速决策。同时,中联重科还构建了多层级的数据指标体系,涵盖生产节拍、进度、设备状态、质检结果等,全面反映工厂生产情况,便于动态监测和问题解决。
通过数字孪生技术的应用,中联重科塔机智能工厂的生产效率得到了显著提升。例如,在标准节灯塔车间,集成了5条标准节智能化焊接生产线,投入了200余台自动化机器人和30余套AGV、RGV无人化搬运小车。这些智能化设备的引入,使得产品成本不断降低,生产效率大幅提升。
同时,数字孪生技术的应用还使得中联重科塔机智能工厂的产品质量得到了有力保障。通过实时监测设备状态、质检结果等信息,管理者可以及时发现并解决生产过程中的质量问题,从而确保产品的稳定性和可靠性。
智能制造的产业镜像
数字孪生是智能制造深入发展的必然阶段和关键支撑技术。它通过构建物理实体在虚拟世界中的精准数字镜像,实现物理世界与数字世界的紧密连接。这种连接为智能制造提供了前所未有的可视化、可预测和可优化能力,包括但不限于以下几类:
1、优化产品设计
在设计阶段,通过数字孪生技术,工程师可以在虚拟环境中模拟产品的性能和表现,预测潜在问题,并在实际生产前进行优化。这不仅缩短了产品开发周期,还降低了成本。
2、提升生产效率
在生产过程中,数字孪生技术可以实时监控生产线的运行状态,预测设备故障,提前进行维护。通过模拟生产流程,还可以找出生产瓶颈,优化生产布局,从而提高生产效率。
3、增强质量控制
数字孪生技术可以对产品质量进行全程跟踪和监控,确保产品在生产过程中的质量稳定。通过模拟不同环境下的产品表现,还可以预测产品在实际使用中的性能,为产品改进提供依据。
4、促进供应链协同
通过构建供应链的数字模型,制造企业可以实时监测供应链的运行状态,并与上下游企业共享数据和信息,提高供应链的透明度和协同效率。
当前,数字孪生技术正在深刻改变着制造业的生产和管理方式。它通过构建数字模型,实现数据驱动和场景支撑,为制造企业提供了全新的发展机遇和广阔的市场空间。未来,随着物联网、云计算、人工智能等前沿技术的不断发展,数字孪生技术的应用也将更加广泛和深入,推动制造业向更高水平的智能化和数字化发展。
(本文综合整理自NVIDIA、中联重科以及艾瑞咨询)
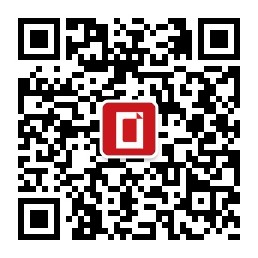