智能制造焊装工厂数字化转型之路
- 来源:国际金属加工商情 smarty:if $article.tag?>
- 关键字:智能,焊装,数字化 smarty:/if?>
- 发布时间:2024-09-21 14:08
随着汽车制造业迈入数字化时代,焊装工厂作为汽车生产过程中的重要环节,正经历着深刻的转型与变革。在第27届北京·埃森焊接与切割展览会期间举行的汽车焊装智能工厂技术研讨会上,来自北京奔驰和上汽大众这两家中国汽车行业的领先企业的专家们就通过各自独特的数字化战略和技术应用,展现了焊装工厂智能制造的创新实践与成效。
北京奔驰:PAMS系统的建设与应用
北京奔驰汽车有限公司成立于2005年,是梅赛德斯奔驰在全球范围内面积最大的综合性乘用车制造基地,拥有德国本土以外第一个发动机制造工厂及电池工厂。公司自成立以来,持续推动数字化、柔性化和绿色制造,致力于将这些理念贯穿于生产过程中的每一个环节,荣获了多个国内外荣誉。
北京奔驰的数字化转型分为五个阶段:数据采集、数据可视化、数据分析、数据驱动和智能化转型。在这一过程中,PAMS(生产管理系统)平台的开发和应用成为核心。该平台通过整合数据采集、传输和存储,形成了全流程闭环管理,使得生产运营的透明度大幅提升,设备利用率和质量保证能力得到了显著提高。
在具体应用场景中,北京奔驰的PAMS系统在焊装工厂中发挥了至关重要的作用。例如,通过对工业机器人的状态监测,系统可以实时采集传感器信号,分析设备状态,从而提前预测故障,进行预防性维护。这一技术的应用显著提高了生产设备的稳定性和生产效率,减少了停机时间和维护成本。
通过PAMS系统的实施,北京奔驰在生产效率和管理效率方面均取得了显著的成效。生产效率提升了22%,设备综合效率(OEE)提升了11%,同时生产的年总值提升了40亿人民币以上。质量缺陷率和返修成本大幅降低,预测性维护的应用也使得设备运维更加高效和节约。
上汽大众:焊装工厂的微循环发展
上汽大众作为中国首家中外合资企业,已经有40年的发展历史。在这一过程中,上汽大众通过多次技术路线的调整,逐步确立了以智能制造为核心的发展路径。焊装工厂在上汽大众的数字化转型中起到了至关重要的作用。焊装工艺的复杂性和多样性决定了其对智能制造技术的强烈依赖。
上汽大众的焊装车间围绕平台化的思路进行布局和管理。平台化指的是在同一技术基础上,通过不同的车型变型和造型变化,生产不同的汽车产品。在上汽大众,不同平台间的切换和柔性制造成为提升生产效率和应对市场变化的重要手段。
焊装车间中的智能制造技术应用非常广泛。通过模块化的
平台设计,上汽大众可以实现多车型的柔性生产,大大提升了生产线的利用率和产能。此外,焊接工艺的智能化升级也帮助企业应对了钢铝混合车身结构带来的工艺挑战。流转系统、激光焊接、射钉铆接等多种技术在焊装车间的广泛应用,帮助上汽大众实现了更高的生产精度和效率。
未来,上汽大众将继续依托其模块化平台和数字化制造技术,推动焊装车间向更加智能和高效的方向发展。随着电动车市场的扩大,上汽大众在纯电动汽车制造领域的投入也将逐步增加。这不仅仅是传统制造工艺的升级,更是向智能化生产迈进的重要一步。
数字化转型的共性挑战与机遇
无论是北京奔驰还是上汽大众,在数字化转型中都遇到了数据采集和应用的挑战。如何实现生产设备与信息系统的高效联通,如何在海量数据中找到有价值的信息,是每一个企业在数字化转型中必须解决的问题。通过智能化平台的搭建,企业逐步实现了从数据采集到数据驱动的全过程闭环。
数字化转型不仅仅是技术上的升级,更是组织架构和人员技能的转型。北京奔驰通过设立数字化融合委员会,推动员工参与到数字化创新中来,这种做法在激发员工创新热情的同时,也确保了数字化转型的顺利实施。上汽大众则是通过焊装车间的微循环发展,不断优化生产流程和管理模式,为员工提供了更多技能提升和发展的机会。
随着市场对汽车个性化需求的不断增加,焊装工厂的柔性制造能力成为衡量其竞争力的重要标准。北京奔驰和上汽大众通过平台化管理和智能制造技术的应用,实现了多车型生产的高效切换。这不仅提高了生产效率,也提升了企业应对市场变化的灵活性。
结语
北京奔驰和上汽大众在焊装工厂的智能制造和数字化转型中,展现了两种不同的发展路径与成功实践。北京奔驰通过PAMS系统的建设,实现了全流程闭环管理和设备状态的智能监测,极大提升了生产效率和质量保证能力。而上汽大众则通过平台化管理和模块化生产,灵活应对多车型的生产需求,推动了焊装工厂的数字化进程。
未来,随着智能制造技术的不断发展和深入应用,焊装工厂的数字化转型将继续加速。对于整个汽车制造行业而言,北京奔驰和上汽大众的成功经验不仅为行业树立了标杆,也为其他企业提供了宝贵的借鉴和启示。在智能制造的大潮中,焊装工厂的数字化转型之路才刚刚开始。
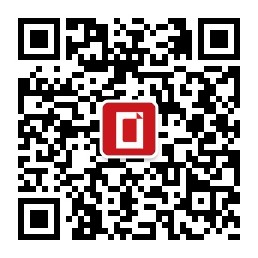