医疗器械品类微型零件制造的未来吗?
- 来源:医疗设备商情 smarty:if $article.tag?>
- 关键字:医疗,器械,未来 smarty:/if?>
- 发布时间:2024-10-05 19:42
从生命科学到电子等各个行业,创新通常都需要超高分辨率和精密部件——尤其是当创新被微型化驱动时。随着产品和技术的小型化,作为整体的零件的复杂性也在不断增加。许多工程师和产品设计师正在转向3D打印来制造这些高精度的小型零件。与传统成型工艺相比,增材制造最近被证明是一种有效的选择。
微型3D打印用于制造医疗设备、光学、光子学、微流体和消费包装商品的高精度微型部件。其中许多部件已成为个性化医疗设备的支柱。它们还广泛应用于航空航天和汽车领域。
BOSTON MICRO FABRICATION(BMF)全球运营首席执行官 John Kawola表示,多年来,制作原型模具是微型部件的唯一解决方案,但这种方法既耗时又昂贵。如今,许多行业和应用都使用增材制造作为按需原型设计和生产的经济实惠的选择,而且也使工程师能够突破创新的界限。
“在BMF,我们的客户通常需要的精度水平是机械加工或成型等传统制造方法根本无法实现的。BMF的投影微立体光刻(PμSL)技术可以让客户始终如一地实现高精度、高分辨率和高准确度的超小型特征。我们还开始开发终端应用,我们的技术特别适合解决行业难题。例如,如果没有微型3D打印,就不可能制作出UltraThineer贴面(世界上最薄的美容牙科贴面)。”
高精度不仅仅对微型部件很重要。随着产品设计继续成为创新的驱动力,无论部件尺寸如何,对高精度和准确部件的需求仍然存在。“虽然BMF 通常与微型打印有关,这是我们业务的核心,但我们也可以打印更大的部件。我们构建了 microArch S350平台,专门满足市场需求,即需要高精度和精确度,但不需要我们其他系统的超高分辨率。这是一个25μm平台,可以使用工程级材料以更快的速度进行打印,使那些可能不需要超高分辨率但对准确性和精确度很看重的制造商能够使用。”
在BMF 之前,除了微注塑等传统制造方法外,没有其他方法可以制作具有复杂几何形状和小特征的微型部件原型。许多公司发现,部件越小,使用传统方法制造就越困难,成本也越高。BMF的PμSL技术利用轻便、可定制的光学元件、高质量的运动平台和受控的加工技术,为产品开发、研究和工业小批量生产提供业内最准确、最精确的高分辨率3D 打印件。
各个行业,从原型设计到生产的不同产品开发阶段,对具有尺寸精度和精密度的微精密零件有着很大的需求。
3D打印能否获得高分辨率、准确度和精度取决于多种因素。这些因素包括光学分辨率、机器中机械系统的精度、曝光控制和由此产生的固化、部件与所需支撑结构之间的相互作用,以及最后,部件的整体尺寸和控制整个构建过程中公差的能力。
“我们的每台打印机都具有有助于分步重复过程的功能,该过程允许使用高分辨率和受控加工技术制造高精度物体。整个microArch系列还包括可定制的高分辨率光学系统和移动平台、实时图像监控、自动对焦和曝光补偿,以及具有简化界面和客户参数设置的操作软件。microArch 3D打印系统能够实现超高分辨率、大面积打印,用于工业原型设计和短期生产。”
BMF 的3D 打印机采用PμSL 技术,这是一种立体光刻(SLA) 技术,结合了DLP® 光引擎、精密光学元件、运动控制和先进软件。SLA使用光化学工艺分层生产零件。感光液体树脂暴露在光线下,从而发生聚合物交联和固化。借助PμSL技术,一束紫外线(UV)光可使整层树脂快速光聚合。
PμSL工艺是自上而下的。自上而下的方案不仅最大限度地减少了所需的支撑结构数量,而且还提供了一种减少对小特征的损坏和使用刮刀在透明膜上刮除气泡的方法。无需支撑即可将底面固定到打印表面,并且由于通常重量较轻的部件和树脂浮力的相互作用,因此悬垂部分所需的支撑有限。BMF的PμSL系统可以实现低至2μm的XY分辨率、10μm的最小特征尺寸和+/-10μm的尺寸公差,该技术支持连续曝光以实现更快的处理速度。
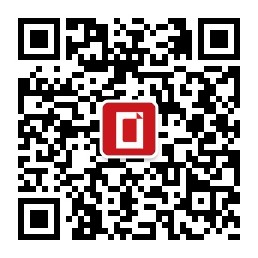