传感器+边缘AI,实现数据实时处理的转机?
- 来源:智能制造纵横 smarty:if $article.tag?>
- 关键字:传感器,边缘AI,数据 smarty:/if?>
- 发布时间:2024-12-02 11:09
随着智能制造的深入发展,传感器获取的数据以几何级增长。为了更高效地处理信息,传感器解决方案供应商通过5G高带宽、云处理、本地处理等方式不断提升数据处理速度和性能。当下,传感器+边缘AI的解决方案已成为新的发展方向,越来越多的企业以此实现了更高效的传感器信息处理与通信。
在上一期内容中,我们也聊到了AI传感器正在成为新一代智能传感器的核心。但在具体实践中,由于边缘AI需要将算法和模型部署在本地边缘设备上,传感器小巧的尺寸很大程度上限制住了运算性能,所以边缘AI是否适用于所有生产环境一直是各大企业争论的话题,也是传感器解决方案供应商当下集中攻克的难题。那么现阶段的生产企业该如何取舍?本期内容中我们就通过一些案例和分析,给大家提供一些参考。
通过边缘计算对传感器加成
边缘传感器(Edge Sensors)是指在网络边缘执行数据采集、预处理和分析的感知控制设备。它最大的优势在于利用边缘计算(Edge Computing)架构,使企业应用程序更接近数据源。通过在数据源附近进行计算任务,达到降低数据传输延迟和带宽需求,提升系统的实时响应性和效率。通过边缘计算,传感器几乎能把数据进行实时处理。
消除了传统云处理时数据上传下载的不稳定因素。另一方面,边缘计算传感器更加独立可靠,从“网游”变成“单机”后,全面停盘的可能性几乎被降到零,即便单个传感器出现问题,检修和恢复速度也远高于传统处理方式。更重要的一点是,数据安全有保障了,没有了数据上传这一动作后,制药、医疗等数据敏感企业将不用担心泄露和网络安全风险。此外,边缘传感器支持实时决策和行动,对于需要快速响应的应用场景至关重要,如:智能制造、自动驾驶、物联网(IoT)等领域。
在不同领域落地实例
以智能制造为例,预测性维护是边缘AI传感方案大有可为的领域。意法半导体基于STM32硬件平台,提供NanoEdge Studio模型创建工具。该工具为传感器、变频器、伺服设备提供了机器学习功能。通过对生产设备的电流、电压等数据处理和监控,用户不需要增加新的传感设备,就可以在资源受限的边缘计算设备上快速构建准确高效的AI算法。结合不同生产环境中的传感器(振动传感器、超声、温湿度、气压和加速度计),能够高精准度实时检测生产设备的任何偏移或者异常,在发生重大故障之前触发警报作出调整。
机器视觉更是智能制造的核心之一。由于机器视觉对时效性、计算效率有更高的要求,更贴近数据源头的边缘计算具有天生的优势。对此,越来越多的机器视觉方案供应商不断推出带硬件加速的MCU和MPU产品。
还是以意法半导体为例,STM32MP25系列不仅内置了高达1.35 TOPS算力(每秒1.35万亿次运算)的NPU加速器,还采用了900MHz的3D GPU来实现全高清视频编解码。同时配备了MIPI CSI-2摄像头接口,支持RGB、LVDS和DSI输出的全高清视频。开发者可灵活选择在CPU、GPU、NPU上运行AI应用,对企业来说,适用性和兼容性也更高了。
此外,自动驾驶也是边缘AI传感解决方案大放异彩的领域。
随着汽车上搭载越来越多的传感器,其对数据传输和处理的要求也越来越高。在边缘AI中,高分辨率传感器与AI处理器之间的数据传输链路在整个系统的性能中起着至关重要的作用。为了保证多数据高同步采集、采集数据录制、实时数据回放、数据高效多维度处理和数据校验,需要有性能强大、稳定性高、精准性好的车载AI边缘计算硬件产品来提供强大的支撑。
这也意味着,车载边缘AI传感解决方案中需要配置更高性能的处理器,支持显卡和AI加速卡,低延时处理传感器数据。同时需要具有丰富的接口,能满足不同车型不同传感设备方案,做到连接互通。此外,为应对车辆行驶中的颠簸,数据存储、数据保护、抗冲击能力都是供应商们要解决的课题。
除了这些大家熟知的应用领域,边缘AI传感解决方案在矿产、气田、高温高压等极端生产环境中无疑是更可靠的选择。
以气田行业为例,矿底压力变化直接影响产线的正常运作。传统作业中,传感器会将数据变化上传至地面,由操作人员处理判断。但受特殊环境影响,数据传输往往会有延时。即便数据传输能实时将正确数据上传至信息中心,操作人员的经验和响应速度往往更为关键,尤其是在中小型矿场。
对针这类需求。斯伦贝谢推出过一种智能针阀边缘计算解决方案(SNV),就是将传感器结合边缘计算技术,实现全自动、全周期的闭环算法控制,用于动态管理气井的间开生产调度。
SNV由传感设备和AI两部分组成。其中,传感设备包括多种传感器、远程控制针阀(RCNV)和边缘计算智能网关(Agora)。
该系统的运行方式如下:
1)、Agora通过Modbus TCP协议与远程终端单元(RTU)建立连接,RTU负责现场的数据采集和控制指令下发;
2)、通过压力、温度等各类传感器,Agora实时获取关键气井变量数据;
3)、Agora将这些数据交由SNV处理,优化气井生产调度结果;
4)、Agora将结果返回RTU进行生产控制;5)、最后,将所有数据传输至本地服务器或者云端,实现整个生产过程的数据管理。
在这一流程中,SNV利用机器学习方法对实时数据分析和生产制度优化,以增加产量。最终,这将提升气井的开井时间比率,并减少操作人员的现场作业。SNV主要利用现场传感器收集到的高频生产数据,包括油管压力(THP)、套管压力(CHP)、温度和产气速率等。当气井正在生产时,SNV会实时计算井筒内的液位高度。当液位高度超过阈值时,SNV将自动关闭该气井。当气井处于关闭状态时,SNV将使用一个结合深度学习和机器学习的集成模型推荐最佳的关井时长和下一次的开井时刻。当系统运行到该时刻气井将被自动打开。
据现场测试,SNV解决方案能有效增加单井产量6%-8%;开关操作率提高了20%-30%;减少了50%的现场操作,从而减少了运营成本、安全风险和碳排放。
市场逐渐地兴起
说了那么多优势,再来说说边缘AI传感器的短板:性能限制、资源限制、能效和可扩展性等都是目前阻碍边缘AI传感器扩大应用范围的阻力。当然,供应商们也正通过各种技术来弥补缺陷。这也引发了另一个问题:边缘智能技术发展迅速亟需建立统一的技术标准和生态系统,促进不同设备和方案之间的兼容性。
但就如同所有新生事物都有那么一些“不完美”,技术缺陷是会随着工艺提升不断完善的。
据IDC预测,预计2024年全球边缘计算支出将达到2280亿美元,较2023年增长14%。到2028年,边缘计算支出或将接近3780亿美元,并以两位数的复合年增长率稳步增长。这一数字不仅反应了市场的热度,更有可能加速技术发展。
因此,我们很坚定地认为边缘AI传感解决方案也不是大型企业的专享,中小型企业也应该密切关注它的进化,说不定很快,随装随用的方案即将来到你我的身边。
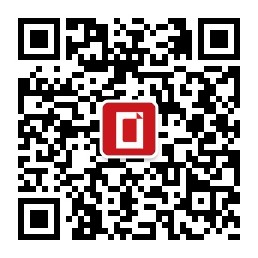