柔性制造:工业柔性的硬实力
- 来源:科技创新与品牌 smarty:if $article.tag?>
- 关键字:工业,柔性,硬实力 smarty:/if?>
- 发布时间:2024-12-07 12:45
文/本刊记者 王怡
智能制造作为高阶制造业态和新型生产方式,正成为全球制造业加速迈向工业4.0时代的核心驱动力。其中,柔性制造因其灵活性、敏捷性、模块化与智能化,成为制造业转型升级的重要方向。
传统的“刚性”自动化生产线,主要实现单一品种的规模化生产;而随着现代制造业的市场需求和发展趋势,传统生产模式已经难以满足消费者“多样化、小规模、周期可控”的生产需求,兼具灵活、高效的柔性制造生产方式由此应运而生。
工业4.0时代的模式创新
作为一种应对大规模定制需求而产生的新型生产模式,柔性生产的概念最早由英国公司Molins提出,在20世纪70年代末开始推广应用;随后,更多的欧美国家在发展中孕育出多家全球领先的柔性制造系统供应商。
我国对柔性制造的运用起步较晚。工业化时代的经济环境以及消费结构,使刚性制造成为制造业核心的生产模式;直到20世纪90年代,国家开始推广集成制造系统(CIMS)应用,部分企业才开始导入柔性制造系统。近年来,信息技术促进的产业变革不断呼唤柔性制造的普及,随着工业智能化进程的深入与国家政策加码,我国柔性制造正逐渐缩小与国际先进水平的差距。
工信部在《工业互联网创新发展行动计划(2021—2023年)》中提出:“鼓励消费品、汽车、钢铁等行业企业基于用户数据分析挖掘个性需求,打造模块化组合、大规模混线生产等柔性生产体系,促进消费互联网与工业互联网打通,推广需求驱动、柔性制造、供应链协同的新模式。”2024年1月,工信部等七部门发布《关于推动未来产业创新发展的实施意见》,提出“发展智能制造、生物制造、纳米制造、激光制造、循环制造,突破智能控制、智能传感、模拟仿真等关键核心技术,推广柔性制造、共享制造等模式”,对未来制造方向进行了战略部署。
柔性引擎加速释放工业新动能
当前,以先进制造业为支撑的现代产业体系在发展中仍存在部分深层次结构性问题,柔性制造的“柔性”特征,使之具有加快释放工业新动能的优势。
首先,柔性制造具有鲜明的灵活性与定制性,可以通过自动化的生产制造系统,满足制造任务或生产环境变化下的多产品定制化需求,解决生产品类“多”的难点;其次,敏捷性与高效性特征,可以使其通过优化生产管理系统,增强供应链的资源配置柔性,实现供应链对定制需求的敏捷响应和快速交付,解决需求变化“快”的难题;此外,模块化与通用性特征,可以使生产系统实现不同模块的选择和组合,以构成不同功能或功能相同但性能、规格不同的产品,适应不同客户的需求和订单量。并且,在定制化需求下,订单产品参数各不相同,设备和生产线的自动化与智能化则是实现快速、高效柔性生产要求的重要保障。
对于制造业来说,柔性制造从来不是一个单点能力,而是系统的组织能力,企业需要柔性物流、柔性控制、柔性调度、柔性生产计划,并在此基础上完成柔性生产,考验的是生产线和供应链的反应以及协同速度。一方面,数据是形成新质生产力的优质生产要素,柔性生产离不开数字化驱动;另一方面,供应链及物流的柔性化程度形成生产资源的协同关系。物流路径的柔性可以实现资源的动态协同,供应链的柔性化则通过改良生产工艺、优化生产流程、降低库存成本的同时,快速触达消费者的个性化需求。此外,除了高度的自动化和智能化技术支持,还需要具备敏锐的市场洞察力和快速响应能力。
柔性制造因其强大的技术创新引领力、对生产模式的深刻转变以及对产业升级的强劲推动,成为中国新型工业化的代表助推新质生产力发展。
柔性生产线助力企业精益升级
作为我国航天系统首家数控技术研究和生产试点单位,中国航天科工三院159厂在发展过程中,逐渐感受到传统生产模式越来越难以满足航天产品多品种、多状态、小批量定制化生产需求。2015年,159厂决定构建适合航天产品快速生产的柔性生产线,从而实现产品加工快速响应。
在后续发展中,中国航天科工三院探索出一条适用于航天装备的智能制造新模式,生产线设备利用率提升达到90%以上,创造了多种核心零件最快生产纪录,实现无干预加工模式的应用和产能跃升,真正做到“产品不落地,生产零等待”。此后,越来越多的企业顺应柔性生产趋势实现提质增效。
一汽红旗工厂的智能焊装车间是红旗首个高柔性化、高数字化、高绿色化的焊装车间,车型柔性化生产焊接自动率达到100%;三一重工位于长沙的“18号工厂”被誉为亚洲最大的智能化制造车间之一,人工、设备、物料、工艺等各要素在这里柔性融合,依托工业互联网络将大数据联结起来并通过制造运营管理系统处理,制定最合适的生产方案,最优地分配各种制造资源。
随着技术走向成熟,柔性制造正成为中国工业扩容海外市场的重要方式,但与此同时也面临诸多挑战。例如,随着生产流程的复杂化,管理和维护的难度随之增加,可能导致生产效率下降和成本上升,保持产品质量的一致性也是不小的挑战。面向未来,柔性制造生产模式还需要加强技术创新、人才培养等各方面协同努力,从而推动中国智造实现稳健长远发展。
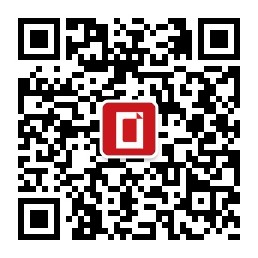