汽车发动机复杂铸件的无模快速制造研究
- 来源:3D打印世界 smarty:if $article.tag?>
- 关键字:汽车发动机,铸件 smarty:/if?>
- 发布时间:2015-12-18 15:30
摘要:本文分析了汽车发动机复杂铸件试制的技术难点,并提出了先进的解决方案——利用无模快速制造技术可以完全突破传统工艺及技术的局限(周期长、成本高、风险大、多次试模等),具有快速、精确、高效、经济的特点,非常适合单件、小批量、个性化、形状复杂金属零件的快速制造和新产品开发(以铸铁缸体为例说明)。
一、前言
21世纪以来我国汽车行业迅猛发展,汽车发动机的质量及可靠性取得了较大的进步,但是发动机的关键技术远低于国外先进水平,尤其在节能减排方面,平均油耗高于国外发动机10%以上。在我国经济保持快速增长的背景下,未来汽车行业仍将保持快速增长,人们更加追求个性,更加挑剔,思想更加多元化,这也导致多种风格同时涌现,呈现“百花齐放、百家争鸣”的局面,汽车市场也随之蕴含着巨大商机。随着我国汽车燃油经济性标准和排放法规日益严格,再加上国内汽车企业参与国际竞争、走向国际市场的需要,汽车发动机的研发迫在眉睫。
发动机作为汽车的“心脏”,它的研发是一个系统工程,但主要瓶颈在于复杂铸件(例如缸体缸盖、进排气管、壳体支架等)的制造。传统方法就是开模具(木模或者金属模)然后翻砂造型浇注,存在周期长、成本高、风险大、多次试模修模等特点,对产品的试制造成很大的影响。比如国内某自主品牌汽车企业2009年研发的1.3L和2.0L发动机,由于复杂铸件无法按时完成导致项目推迟几乎一年,大大超出了预期,错失发展良机,损失惨重。
现代工业生产正在从大规模批量化生产转变为中小批量和个性化生产,产品的生命周期和投放市场的时间越来越短。比如汽车行业,十年前开发一款新车型需要两年以上的时间,而现在同一个汽车制造厂商每年就有几款新车型问世,开发一款新车型不到一年时间。市场的严酷竞争要求应尽可能缩短产品的设计和制造周期,同时应尽量降低成本和风险。
二、快速制造技术
20世纪80年代中发展起来的快速成形技术(Rapid Prototyping,简称RP技术)是制造科学上制造理念的突破,是制造技术发展的重要里程碑。RP技术是由CAD模型直接驱动的快速制造任意复杂形状三维物理实体的技术总称。RP的基本过程是:首先设计出所需零件的计算机三维模型(数字模型、CAD模型),然后根据工艺要求,按照一定的规律将该模型离散为一系列有序的单元,通常在Z向将其按一定厚度进行离散(习惯称为分层),把原来的三维CAD模型变成一系列的层片;再根据每个层片的轮廓信息,输入加工参数,自动生成数控代码;最后由成形系统成形一系列层片并自动将它们联接起来,得到一个三维物理实体(参见图1)。
经过二十几年的发展,RP技术已经到了快速制造(Rapid Manufacturing,简称RM)和快速模具(Rapid Tooling,简称RT)阶段,涌现出了SLA(光固化/立体光刻)、SLS(激光选区烧结)、FDM(熔融沉积成形)、LOM(叠层实体制造)、3DP(三维打印)、LENS(激光近净成形制造)、EBM(电子束选区熔化)、SLM(激光选区熔化)等多种工艺,其中在复杂铸件的快速制造方面优势最明显、应用最广泛的是无模铸型快速制造技术(Patternless Casting Manufacturing,简称PCM技术),与之类似的还有美国Exone公司的快速铸造技术.RapidCasting Technology简称RCT技术.。
三、无模快速制造技术及装备
1、PCM技术
无模铸型快速制造技术是将CAD计算机绘图、快速成形技术与传统砂型铸造工艺有机结合而设计开发出的一种数字化制造的综合技术。它无需模具,能够快速、柔性、准确地制造内腔、表面较为复杂的铸型(芯),特别适合单件、小批量、个性化、形状复杂的大中型铸件的试制和新产品开发。
PCM技术基本原理是:利用RP技术的离散/堆积成形原理,采用轮廓扫描、喷射固化工艺,实现铸型的快速直接成形而无需模样,如图2所示。
首先从零件CAD模型得到铸型CAD模型;由铸型CAD模型的STL文件分层,得到截面轮廓信息,再以层面信息产生控制信息;造型时,第一个喷头在每层铺好的型砂上由计算机控制精确地喷射粘结剂,第二个喷头再沿同样的路径喷射催化剂;两者发生交联反应,一层层固化型砂堆积成形。这样在粘结剂和催化剂共同作用的地方,型砂被粘结在一起,其它地方型砂仍为颗粒态。固化完一层后再粘接下一层,所有层粘接完后就得到一个空间实体。在粘结剂和催化剂没有喷射的地方仍是散砂,比较容易清除。清理出散砂,就得到铸型(芯),在铸型(芯)的表面涂敷或浸渍涂料之后就可用于浇注得到铸件。
PCM技术的主要特点:
a.无需模具,直接堆积制作铸型(芯);
b.易于制造含任意自由曲面(曲线)的铸型(芯),越复杂越能体现其优势;
c.无需拔模斜度,减轻铸件重量;
d.减少设计约束和加工余量,完美体现设计者意图;
e.型、芯可一体化成形,提高定位精度;
f.可实现全自动,劳动强度低,运行成本低;
g.可制造黑色金属(HT/QT/RuT)、有色金属(铜合金、铝合金、镁合金)、铸钢(不锈钢)等多种材料金属零件,也可制作模具毛坯,减少加工余量,提高模具寿命;h.在RP、RM、RT上都得到广泛应用,比如制作复杂陶瓷卫生洁具原型和原胎模、翻制树脂模等。
2、PCM装备
随着PCM技术的不断发展,我们成功研发出PCM系列装备并推向市场,主要有两种规格——PCM‐1200和PCM‐800,具体见图3、图4和表1:
四、利用PCM技术无模快速制造发动机复杂铸件(以缸体为例说明)
经过十几年的积累和沉淀,PCM无模快速制造技术逐步为广大客户(尤其是发动机研发工程师)接受、信任并依赖,因为它具有快速、精确、高效、经济的特点,非常适合单件、小批量、个性化、形状复杂金属零件的快速制造和新产品开发。截止目前,我们已经为国内近30个省市自治区超过100家企业提供了优质的技术服务和设备销售,并获得客户认可和好评;尤其在汽车行业,发动机缸体缸盖、进排气歧管、壳体支架等复杂铸件的研发由于时间紧、难度大、任务重等因素,必须选择最先进、最可靠的无模快速制造技术才能按时保质保量完成。
我们公司技术服务的主要流程如下:接受产品三维数据——数据检查及产品分析——建立浇注系统——模流分析并改进——分模——PCM工艺或多种工艺分工并行制造——组型合箱后浇注——毛坯处理及检测——精密加工——综合检测——包装入库——按照订单出货——用户信息反馈。下面以一个四缸灰铸铁缸体为例介绍整个过程。
a.现有一汽车发动机的四缸灰铸铁缸体样品制造(如图5所示),数量:3件;周期:35天。
以前,国内很多汽车企业都是发到国外(主要是欧洲的德国、意大利、西班牙、奥地利等)进行试制,一个铸铁四缸缸体约需3万欧元,再加上沟通困难、周期过长、出差费用等因素,都大大限制了开发的效率;用传统方法就要开模具,费用在100万左右,周期大概2‐3个月,开出的模具需要修补3‐4次才能达到要求,并且要考虑拔模等因素;而现在利用PCM无模快速制造技术仅用1个多月就制作了3个合格的缸体铸件交给客户用于测试,在质量、周期、成本上均具有非常大的优势,也大大降低了新产品开发的决策风险。
b.数据主要检查完整性(烂面、缺漏、倒角圆角等)、壁厚和加工余量是否满足要求、二维三维是否一致等;产品分析则重点关注结构、材料和热处理等分析。
c.接下来就是工艺人员根据产品特点和经验确定工艺方案,建立浇注系统,给出工艺参数。(为了提高成品率,减少不必要的损失,我们特地引进了西班牙Quantech公司的Vulcan铸造模流分析软件;同时,我们公司也是该软件的国内代理商,它的主要客户有Airbus、Toyota等)。Vulcan可以模拟大部分铸造工艺,包括砂型铸造、重力铸造、低压铸造和高压铸造等,可以进行充型过程分析、凝固过程分析、热应力分析、铸件最终缺陷分析等,针对这个缸体的分析如图6所示。
d.通过分模则知缸体的型芯可以做如图7的分拆组装;而后,根据分拆件的具体结构特点,选择PCM技术或者相关技术进行并行快速造型,充分集成各种工艺的优势,从而达到最快速度、最高质量、最低成本的目标去完成任务。
目前,除了PCM无模快速制造技术以外,国内外很多公司都在利用加工中心或雕刻机对砂块进行直接加工而得到铸型,称之为“直接铸型加工技术”(DirectMouldMilling,简称DMM技术)。该技术同样由于省去了模具的制造环节而对砂块进行直接加工,使分型面的选择具有更大的灵活性,更易实现造型方案多样化,因而可使复杂铸件的精度大为提高,且减轻了毛坯重量;但是DMM技术对复杂的芯和有倒钩等复杂特征的铸型仍无能为力,必须依赖PCM技术或其它技术。由此可见,集成和优化组合多种制造工艺是必然趋势。
e.根据以上的分析并行制造型芯,如图8所示。
f.组型合箱浇注得到铸件,如图9。
g.铸件检查。主要包括材料(化学成分、机械性能和金相等检测)、铸造缺陷(肉眼看、截面剖开或探伤检测,见图10)、尺寸精度(划线或三坐标检测)、表面粗糙度(样板对比检测)、试压(粗加工后封闭内腔进行压力测试)、清洁度检查等。
h.铸件检查合格后,如客户要求机加工,则转入加工中心进行精密加工。
i.完成加工后检查尺寸精度(量具或三坐标),如有不合格项,则返工直至全部合格;试压合格后清洗零件,综合检查合格后包装入库,等待发货。
j.客户反馈,总结归纳整理存档。
通过以上流程,我们可以看出,PCM无模快速制造技术相比传统工艺有很大的优势。
在这个流程中,我们非常注重细节的管理,尽最大可能保证每个工序都是合格的,包括工艺方案会审,三维数据的校对,型芯尺寸、强度和发气量的检测,严格保证工艺参数等。只有这样才能不断提高核心竞争力,只有这样才有利于我们向“更快、更好、更省”的目标前进!
五、其它典型案例
六、结语
无模快速制造技术是多项先进制造技术集成的综合技术,具有快速、精确、高效、经济、综合效益好、发展潜力大等优点,我们将不断开拓创新,顺应铸造“高品质、高效率、轻量化、环保化”的发展潮流,打造核心竞争力,为中国铸造企业的持续又好又快发展而努力!
撰文/广东峰华卓立科技股份有限公司
第一作者:金枫,男,1978年11月出生,高级工程师,毕业于北京科技大学,现任佛山市峰华卓立制造技术有限公司常务副总经理,主要从事快速制造技术及装备的研发和应用研究,拥有8项发明专利和1项实用新型专利,发表论文多篇,希望能为提升我国装备制造业的综合技术水平和国际竞争力贡献绵薄之力。
Email:godenmaple@126.comWeb:www.fsfenghua.com
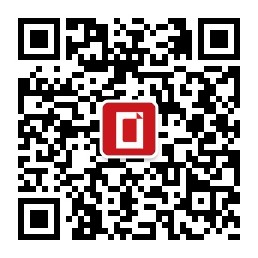