以智能技术和互联网为切入点推进智能制造
- 来源:中国信息化周报 smarty:if $article.tag?>
- 关键字: smarty:/if?>
- 发布时间:2017-09-21 10:14
推进智能制造先从哪里入手呢?我认为可以从车间现场做起,尤其是对于刚起步的企业,质量、高效是基本目标,服务、绿色、个性等是新的目标。而且在车间现场围绕基本的目标,数据、设备、人里面都可以找到机会,总而言之,数字、智能技术非常重要,离我们并不遥远。
智能技术应用
排查车间质量问题
举个例子,华中数控把智能技术、自动化技术用在机床上,像人的心电图一样,可以测量机床指标,目的是对数控机床进行定期体检,保证机床健康的同时提高加工质量。
另外,通常数控系统是不能够做智能补偿的,也就是说在加工的过程中没有办法实时地补偿,但现在华中数控做了一些智能补偿,通过测量空间的误差、数据建模在加工过程当中根据变化的工况问题进行补偿。
我们现在可以通过大数据分析去控制车间的质量问题。实际上,以前我们没有大数据分析,仅仅是通过感知数据进行质量控制。当时,其实会有很多有效数据资源被我们筛掉了,而这些信息可能是影响质量问题的深层原因。现在,通过数据分析我们可以更及时地发现车间质量问题。
从车间现场来看,通过智能技术和互联网,我们可以做很多事情。例如,我们甚至可以让客户去漫游车间、漫游设备,来看一看帮他加工的零件质量是不是有问题,所以这也要利用互联网技术,也需要智能技术。
智能技术应用
降低能源消耗
另外一个话题,绿色越来越成为关键点。我们讲绿色,不光是说产品没有污染,其实我们减少浪费、减少资源消耗是非常重要的。比如说车间的机油问题,以前是定期换,实际上我们可以通过智能技术的应用来智能检测油品程度的污染,这样可以减少浪费。华中科技大学做的智能型数控注塑机是很普通的东西,但是上面有一个很关键的东西,就是能量可以按需供给,而普通注塑机的能量在不使用它的时候也在消耗。我们做过测算,智能注塑机的耗电能减少60%,这个数字非常可观。
我们和武钢做了电网网损管理,武钢是耗能大户,我们把网损率控制在1.10%以下,基本上减少了三分之一的网损,电费在一个厂就减少1.2亿元,这个数字也很可观。
再举一个国外的例子,BigBelly集太阳能、物联网、高效压缩机为一体,垃圾快倒满时,压缩机会在40秒内将垃圾的体积压缩至原来的五分之一,垃圾箱快满时自动发送信息至垃圾处理中心。处理中心的系统根据各个垃圾桶发回的数据分析,规划最佳回收路线和时间。
海尔现在十分重视服务。未来中国的很多企业也会越来越重视服务。我举个例子,无锡天奇为一个汽车厂做自动装配线,装了很多传感器,还有一个智能引擎的云中心,在云中心通过智能分析来判断设备是否正常。如果有问题的话,需要维护、维修。他们有一个云平台的数据管理专家系统,这也是智能技术。在车间里很多不起眼的设备上,如皮带轮、轴承柱上装了很多传感器,而这些地方恰恰是容易发生故障的地方。
再举一个例子,日本小松通过对挖掘机安装传感器与GPS定位系统,从而实时监控车辆运行情况,并通过大数据分析,对用户的使用习惯进行分析与建议从而降低油耗。
另外就是个性化,红领的个性化设计做得非常好。红领集团建立的个性化服装数据系统能满足超过百万万亿种设计组合,个性化设计需求覆盖率达到了99.9%,顾客只需按红领量体法采集身体18个部位的22个数据,形成专属于该顾客的版型,顾客自主决定工艺、价格、服务方式。具体到红领的车间现场,他们能做到成衣数据自动分解到各工序,跟随电子标签流转到车间每个工位,可在七个工作日交付成品。通过用工业化的流程生产个性化产品,红领的生产成本只比批量制造高10%,但回报至少两倍以上。目前,红领年均销售收入、利润增长均超150%,平均一分钟能够定制服装几十单,仅纽约市场每天定制产品已达400套件。
《华尔街日报》曾报道过德国Kaiserslautern城市的一个案例,化工巨头巴斯夫要生产高度“定制化”的洗发水和液体肥皂。生产过程是每个塑料瓶依次在传送带上灌装、封盖、包装。最终,巴斯夫通过在每个产品标签上嵌入芯片,记录不同数据,如灌装什么颜色和成分的肥皂液,具体是怎样的调配比例、包装方式等,实现了个性化定制生产。
智能技术实现柔性生产
东莞劲胜是智能制造示范企业,他们是做手机壳的。产品的研发、多品种带来的品质管控点增加等一系列问题都需要靠数字化、智能化技术,而且是要靠车间生产的柔性化。因为现在加工的手机壳有七十多种,一定要企业的柔性,柔性在这里怎么保证车间物料有序配送,工时动态匹配、排程协同优化?这都要靠数字化技术、智能化技术。
江淮汽车做了混流生产,本来汽车是大批量生产,现在是混流生产,就是柔性,就是把优化方法用上去了。我的一个学生做优化,后来在优化领域受到国际上的关注。
车间首先是要强调高效。富士康做的事情,就是机器人、自动物流等。我们还是以劲胜为例,通过把虚拟的开发设计软件用上去,自动化的卓越去取代一些人工,把它的开发周期从120天缩短到80天,把产能提升了15%,效果非常明显。
其次是精简人力。劲胜的车间原来是204人,现在只有33人,人力节省超过了80%,这也是靠自动化的卓越和信息化的管理。劲胜以前的车间存在一些问题,如机床加工效率有待进一步提高,加工路径、参数缺少优化,品种多,切换频繁等,我们相应地采取了一些措施,用数字化技术、智能化技术去解决这些问题。结果是车间单件加工效率提升10%。加工效率是3C制造企业的生命线,对一个3000台机床规模的3C加工车间而言,若单件加工效率提升10%,可节省300台机床,这个数字是非常可观的。我们通过基于大数据的工艺参数自动优化,去提高效率,效果非常明显。
此外,通过国产的CAPP系统实现加工工艺路径优化,也使得加工效率提高,这里面包括三维设计、仿真优化等。国产的MES,我们进行了动态调动、智能排程、混流配送等。
最后是缩短工艺开发周期。我们从微观、中观、宏观层面都采取一系列相应措施,来缩短工艺开发周期,提升加工效率,确保产品质量。
值得一提的是,在车间里我们要关注一个问题。我们现在关注分享经济,如滴滴打车,我们多数人关注的还是在消费领域,但实际上生产资料也是可以分享的,我们有很多很好的企业,有很好的设备,但是设备利用率非常低,同时另外有一些企业可能面临一些产品自己加工不出来的问题。因此,我觉得我们是要从个人消费到服务,到为企业服务,从分享消费资料走向分享生产资料,这是我们要关注的,对很多企业而言,我觉得非常有意义。
下面一个例子,就是优制网,优制网是什么意思?就是怎么使制造企业的制造资源、制造能力和技术服务能力可以分享。有一些企业可以把他们富裕或是闲置的资源与别人一起分享,同样,另外一些企业也可以寻求分享。
(本文根据李培根院士的公开演讲内容整理而成,未经本人确认。)
中国工程院院士 李培根
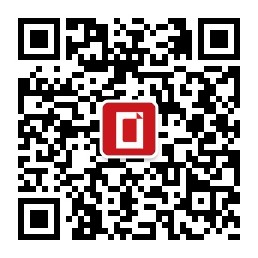