劲胜精密 打造高标准的智能化车间
- 来源:中国信息化周报 smarty:if $article.tag?>
- 关键字: smarty:/if?>
- 发布时间:2018-04-08 10:34
东莞劲胜精密组件股份有限公司(以下简称“劲胜精密”或“公司”)成立于2003年,是东莞第一家创业板上市公司。公司于2015年成为智能制造首批试点企业,同时,公司“移动终端金属加工智能制造新模式”项目是工业和信息化部全国首批智能制造专项项目。公司基于智能制造专项项目的建设经验,将继续完善集高端数控机床、国产机器人、自动化设备、国产系统软件等于一体的智能制造产品和服务体系,打造智能工厂系统集成总承包服务和智能工厂整体改造方案的能力。
顺应数字化趋势
手机行业的产品升级和消费个性化需求的快速增长对高精密结构件产品的研发与制造行业提出了更高的要求。由苹果手机引领的金属外壳化趋势引发了3C产业以CNC为核心的智能制造系统与装备需求的爆发式增长。然而,三星、中兴、华为、OPPO等丰富多元的客户资源,与其他厂相比而言生产的品类更多,这加剧了对其制造能力和制造效率的挑战。同时,由于产品升级越来越快,对交期管控越来越严格,零部件制造环节对机器人灵活性和精确度的要求、对智能制造系统中计划、物流及质量精准管控的要求都越来越高。
劲胜精密自成立以来,一直非常注重智能制造系统在设计、制造环节的应用。截至2015年4月,已通过自主开发和外部合作方式,先后建立了ERP、PDM、MES等系统,打造出适合自身需求的数字化制造解决方案,为近年来主营业务飞速发展提供了强有力的保障。ERP系统管理规模和范围涉及全面,实现了公司七个事业部31个车间的运营级别业务流程在统一平台进行管理。其精益生产系统除保证车间生产过程管理外,还将生产设备如数控机床等做到了多种客户端可视化展示。同时,劲胜精密也非常注重制造装备的升级改造工作,仅在高速钻攻加工环节就投入2500台智能化数控设备,并计划3年内完成总共6000台高速钻攻中心设备的配置,主要用于移动终端中的智能金属手机外壳及相关金属部件的精密加工制造。
为了面向未来多品种、高品质、快速交付的市场要求,劲胜精密进一步提升产品质量稳定性、提升产品加工效率、降低产品成本。因此通过项目提升企业的智能制造水平,并通过项目的成果,带动我国高精金属加工行业的智能制造水平的总体提升。
实现高速高精国产钻攻数控设备、数控系统与机器人的协同工作,在业内率先实现装夹环节采用机器人代替人工操作,节省70%以上的人力;建立基于物联网技术的制造现场“智能感知”系统,改造升级现有智能化系统,建立全制造过程可视化集成控制中心,实现对加工中心、机器人、物流装备等的全面支持,最终实现少人化协同化生产。
实施创新举措
劲胜精密拥有全行业首家大量采用国产数控系统配套核心关键装备的智能化车间:基于完全自主知识产权的国产数控系统,配套移动终端产品核心部件智能制造车间关键装备高速钻攻中心装备和工业机器人,打破国外技术与市场垄断,同时,其自主知识产权的总线通信技术保障了智能化车间装备的数据安全和使用信息安全。
建立基于物联网技术的制造现场“智能感知”系统:将制造生产过程中的关键部件、制造资源结合物联网技术进行“智能感知”,使其在每个生产环节上能实时主动告知其位置、生产状态、工艺参数等信息,并将数据传至上层决策系统,实现“物物相联”的制造现场“智能决策”。
构建基于数据驱动的三维仿真模型:采用轻量化及分块分层算法以保证工厂及设备大规模数据的快速显示,采用基于时间轴的动画插值技术实现离散位移数据的平滑运动显示,规划物流模型运动路径,实时检测三维模型之间的碰撞,建立三维模型运动与数据变量的实时关联,最终实现三维模型的数据驱动。
实现基于三维的工艺协同:实现工艺软件、知识库与三维CAD的集成,实现基于MBD的制造特征定义与信息提取,打通几何特征模型和制造特征模型之间的联系;将工艺知识融入到后端的自动化设备应用中,实现三维工艺从产品设计-工艺-智能制造的贯穿式应用,全面提升行业加工智能性和效率。
建立全制造过程可视化集成控制中心:将计划、执行、物流、质量等业务板块的实时决策数据与图表集中展示,打通各功能域的关联,建设可视化集成控制中心,打造实施过程数据驱动的制造车间决策支持平台,支持计划、物流、质量、采供等多功能组织的全局协同生产与调度。
构建基于企业私有云的分布式协同制造服务体系:建立面向3C制造的企业级私有云制造服务平台,将分布在不同地域的7个事业部35个车间通过企业私有云连接,打造支持企业内多工厂协同制造的云服务模式,提升企业异地协同制造能力。
在业内产生的影响
采用国产智能装备、国产数控系统、国产工业软件实施智能制造,对提升国产智能制造产品的核心竞争力具有示范意义,为实施“中国制造2025”探索途径。
对于劳动力密集型的企业通过智能制造实现转型升级具有示范意义。促进3C产业智能制造升级意义重大,也可推广到其它行业。不仅帮助企业提质增效,同时满足未来市场的个性化、定制化的产品需求,促进企业向制造服务业“智能工厂系统解决方案服务商”的升级。
开发的3C行业CNC钻铣中心集成了具有自适应能力的多种加工模式切换功能,实现不同结构和材料特性的产品零件对象的高速精密加工。同时,针对3C产品加工的智能伺服动态制动技术,高速钻攻中心行程范围小且加工速度高,在机床遇故障需要快速停机时,通过伺服动态制动技术的实现,实现移动轴的快速制动。
完成和设计开发工业RFID、机器视觉和智能感知系列化核心技术,设计并实现了配合机器人、自动化设备、机床、信息系统的核心装置,实现了传感器的多方位结合,获得国家技术发明二等奖1项,发明专利3项,实用新型专利2余项,参与起草了超高频电子标签国家标准,长期致力于电子制造装备研制开发工作,在IC装备制造领域处于国内前列。
实现“三国”的智能制造集成应用示范:由劲胜精密牵头组织、工研院和华中数控参与建设的全国智能制造示范点,实现了“国产装备、国产数控系统和国产软件”的自主知识产权产品应用。
创新带来的效益
通过实施创新举措,节省金属加工环节人力70%以上(以每日两班生产基准,按照每人管理2.5台机器,每机器人1拖2计算)。
实现高速高精钻攻中心、国产数控系统、机器人与收取料系统的协同运动控制,实现多种车间智能装备之间的协同工作。
采用基于工艺知识库的三维智能工艺规划,提高研制效率;通过高级计划排程和实时生产响应技术,减少设备空转时间。
建立生产过程数据库,充分采集制造进度、现场操作、设备状态等生产现场信息;提高车间加工过程质量检测自动化程度,建立产品质量追溯系统,实现全制造过程品检数字化。
建立面向大批量快速响应生产的制造执行系统(MES),实现基于实时制造数据的可钻取仿真车间。
可为企业每年新增8500万元的营业收入,每年可为地方政府新增税收300万元。
佚名
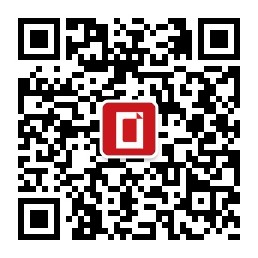