大国纺机:铸就纺织强国根基
- 来源:中国纺织 smarty:if $article.tag?>
- 关键字:纺织业,检测,支持 smarty:/if?>
- 发布时间:2019-12-08 09:09
我国纺织机械工业发展是在自力更生、自主创新的基础上逐步发展起来的。建国初期,我国没有纺织机械制造业,更没有成套工业技术装备的制造业。目前,我国纺织机械工业已经建成了比较完整的工业格局。现在全国有1000多个纺织机械生产企业,可以生产3000多种主机和几千种辅机、检测仪器以及专用基础件,能为40多个纺织行业提供成套的工业技术装备。我国纺织机械工业不论在行业、产品品种和规格以及产量上都稳居世界之首,已经成为世界上最大的纺织机械制造大国、使用大国。
有了自主装备 才能发展产业
纺织机械工业属于制造业中的专用设备制造业,纺织机械工业是纺织工业的装备部、是纺织工业的技术后方,这就确定了其服务纺织行业的特有属性,也无形中确定了它在中国工业发展史上特有的历史方位、社会定位和特殊地位。
据原纺织工业部技术装备司副司长、中国纺织机械协会高级顾问吴永升回忆,中央领导曾多次明确指出振兴纺织工业首先要振兴纺织机械工业。正是牢牢抓住这个方针不放,纺织机械工业才得到了快速、持续、稳步的发展。
建国后,国家从政策、资金和外汇等多方面对纺织机械工业给与支持。从生产维尼纶成套设备到“四大化纤”项目,再到把剑杆织机和气流纺纱机的国产化作为引进技术消化吸收实现国产化的专项之一,把纺织机械的“自动络筒机和无梭织机引进技术和国产化”列为一个专项,后来还有“印染工艺设备一条龙发展”专项、复合纤维编织专项等。吴永升回忆,为了纺织机械发展事业,时任中央书记处候补书记的郝建秀同志曾在仪化公司、天津石化公司蹲点,了解、总结发展化纤机械经验,并亲自把他们叫到中南海,用了半天时间,向她汇报纺织机械情况,分析原因,明确发展思路,并对纺织机械工业发展做出重要指示。
正是有了国家支持,加上地方资金和企业资金的投入,纺织机械工业得到了有效发展,真正成为了纺织工业的技术后方。在这期间,纺织机械企业自己也不断武装自己,增加教育、科研力量,提高制造手段。吴永升讲道,比如,改革开放初期,纺织机械企业第一个与德国汉诺威大学合作生产出我国第一条FMS柔性加工生產线;机床加工设备从数显发展到数控机床,直到柔性生产线;铸造自动生产线从配沙、输沙、造型、连续浇注直到铸件清沙、整理的工艺生产线。有了这样的基础,很快,一个新的工业制造体系形成了。实践证明,有了自主的装备制造业,才能自己装备自己,发展产业。
纺机设备飞速进步
过去几十年来,棉纺工艺技术装备已先后出现了三次大的更新换代,对行业发展产生了深刻变化。吴永升说,以传统棉纺装备为例,40年前,产品是“十年如一日”,改动的很少,棉纺设备用的是“A”字头,织造设备也是“1”字头。改革开放之后,才开始变革,从“A”字头到“FA”系列,生产性能、技术水平和生产效率都有大幅度提高,特别是机械化、自动化、单机之间相互连接。这些变革使纺纱机机械技术水平显著提高,传统的清花、梳棉已经推广到混、开、清、梳的联合,台时产量从改革初期的28公斤提高到100~120公斤;条并卷与精梳机实现了联接,精梳机保持在400钳次以上,落棉率达标。粗纱与粗细纱实现了联接,细纱机长车达到1820锭,附有集体落纱装置,并实现了与自动络筒设备的联接。自动络筒工序后的筒子检测、包装形成自动线,减轻了体力劳动,节约了劳动力,效率大大提高。改革开放之前,计划经济时期核定的万锭企业定员是691人,3万锭规模的定员是1768人,现在的万锭直接定额生产工人都在30人以下,有的更少。
织造机械变化更大,络筒机、整经机和浆纱机分单元自动化进行更新,制造出了新的机型,从有梭织机的生产数量减少到全部由无梭织机替代。无梭织机的发展从普及型剑杆织机开始,到高端剑杆织机、多项剑杆织机、双层割绒剑杆织机,再到高端喷气织机、喷水织机和片梭织机,适应了使用纺纱织造原料结构的变化。多种无梭织机的高速发展,缩小了与世界水平的差距。在发展无梭织机的同时为织机配套的经轴架、各种上下经轴装置,也配套生产。
在发展和提高传统纺纱工艺技术的同时,转杯纺纱机、涡流纺纱机和喷气纺纱等新型纺纱工艺技术也得到了快速发展。
在发展传统织机的同时,针织机械也得到了高速发展。比如,改革开放之前,针织机械只能织造民用汗衫、手套和袜子,经编机也只有一种可以织造蚊帐或者低档的、不要布票的普通化纤织物。当时的电脑横机引进技术之后放在一个军工企业生产,多年也出不了产品。改革开放之后,乡镇企业、民营企业兴起,群策群力,攻克了难关,得到了高速发展。现在中高档的电脑横机年产10万台以上,畅销国内外市场。多功能经编机也同样国有、民营、外企同时生产,技术上相互促进。目前经编机已经实现了智能化生产,在一台智能化经编机上,通过工艺控制系统的设定,一台机器同时可以生产多种无缝内衣和手套、袜子。
纤维加工机械中还有粗毛纺、精毛纺、毛线和几种混纺原料的驼毛、牦牛毛和兔毛原料的粗加工、精加工以及半精纺加工工艺技术装备。有了这些装备,适应了毛纺织工业的发展。
丝绸加工机械特别是仿真丝织物的发展,工艺技术装备都服务于这些行业的发展。
值得提出的是在发展纺机产品的同时,也发展了专用基础件。诸如摇架、锭子、罗拉、钢领等基础件的技术水平与主机发展同步。配套的辅机和在线检测终端产品的质量检测控制仪器都得到了同步发展。
化纤设备取得巨大突破
纺织机械工业服务于纺织工业,必须要围绕化学纤维产业的生产来发展。生产这些产品必须得有整套的物理与化学相结合的工艺技术装备。纺织机械工业要承担的就是这些纤维生产机械,包括聚合、纺丝和后处理的成套工艺技术装备。
我国的人造纤维——统称粘胶纤维,包括长丝和短丝,其工艺技术已于上世纪60年代从东欧国家引进,单线产能有限。改革开放之后,我们积极发展从浆粕连续投料、箱式老成、大型黄化、以及实施大型计量泵、组合式纺丝组件,提高单线产能,使原来的年生产线提高到一万吨、三万吨,再到六万吨,现在的单线年产能可以达到十万吨。同样的流程,这些年各方在工艺技术上的改进、创新和提高,见到了实效。
粘胶长丝连续纺丝工艺成套设备融纺丝、成型、牵伸、上油、烘干和卷绕于一体,使长丝纺丝工艺时间由原来的七十几个小时缩短到现在的几分钟内完成,生产现场杜绝了天上滴水、地上流水的现象。
合成纤维行业在引进“四大化纤”的基础上,不断进行创新,逐步扩大产能,实现国产化。醋酸纤维成套工艺技术也实现了国产化。
合成纤维生产的主体在聚酯纤维生产。改革开放之前,基本上处于学习、研发、打基础到实践的阶段。改革开放以后,通过引进技术、消化吸收、进行自主创新的过程,有了飞速发展。
聚酯装置可以说从无到有,通过工艺技术设备的研究,在引进年产6万吨设备的基础上逐步改进提高,实现国产化。目前发展到单线产能20万吨、30万吨直到40万吨以上。有纤维级聚酯,还有瓶级聚酯,大大缩小了与国外先进技术的差距。
聚酯长丝纺丝和短丝纺丝过去都是使用切片再溶解间接纺丝工艺,产量小而成本高。现在实现了长丝短丝直接纺的纺丝工艺,从熔体管道直接进入纺丝箱进行纺丝、牵伸、定型到成品包装的连续化、自动化。长丝还可以实现对丝饼进行检测、包装,进入立体仓库的自动化;短丝生产线年产6万吨以上。
在发展民用丝的同时,还可以按照工艺要求配置设备。包括帘子线的聚合、纺丝、初捻、复捻(现在都已采用直捻机),直到浸胶成套工艺技术装备的国产化。
值得一提的是这些长丝成型之后,接下来的牵伸、定型、加捻都可以按需配备。还可以通过分丝机,把复丝分成六根或八根更细的单丝,供下游生产选用。
腈纶纤维有短丝和长丝之分,有湿法和干法类别。多用于纺毛织物。改革开放之后,湿法工艺线有比较成熟的传统工艺,主要进行技术改造,提高产能。而干法纺丝工艺则需另起新步。通过“年产30万吨乙烯”项目国产化,带动了干法腈纶设备的国产化。在短期内先后建成了5个项目,从丙烯腈的聚合、纺丝、牵伸到长短丝的成型、包装,年产能16.5万吨。有了这个基础,不仅可以用于民品,而且为碳纤维生产打下了基础。
氨纶纤维的整套工艺技术以及纤维过去全靠进口,价格昂贵,氨纶纤维要十几万元一吨。现在通过消化吸收工艺技术装备实现国产化以及再创新之后,单项、单线年产能都在一万吨或二万吨左右。工艺技术装备国产化以后,氨纶价格大幅下降,人民从改革发展中得到好处。
随着我国进入了新时代,新工艺、新技术层出不穷,接踵而来的是新型纤维的出现,包括芳纶1313、芳轮1414以及碳纤维的出现,我们不但要学、要赶、还要超。这些新材料、新纤维的工艺技术装备目前基本上也立足于国内生产。碳纤维和玻璃纤维实现规模化生产以后带来高新技术复合材料的发展。碳纤维的整经、织造、热塑、热固与浸料生产线到制成品的工艺技术装备,不少项目已处于国际先进水平。
纤维生产机械不仅有主机,还有辅机以及相应的专用基础件,诸如纺丝泵、油剂泵、喷丝板的工艺技术已处于国际上与德、日并驾齐驱。喷丝头过去由黄铂金制成的喷丝头改用钽合金替代,大大降低了生产成本。
工艺生产线、工程成套配用的在线检测和质量控制系统都已配备齐全。可以这样说,我国生产纤维生产机械的类别、品种、规格已基本齐全,不仅可以供应国内,而且可以成套出口。
目前,纤维加工机械正在加快机械化、连续化、自动化的基础上向智能化生产、智能化管理迈进。
印染装备聚焦节能减排
改革开放前,我国织物长期处于白、黑、蓝和灰单一品种生产。改革开放后,为了适应市场需求,急需增加染色布的生产能力,我国采用从境外进口加上在国内配置一部分设备的模式,初步形成了较为完整的印染前处理、染色、印花和后整理成套设备。后来随着国外逐步放开工艺技术装备才有了快速发展,包括灯芯绒生产线、涤纶长丝、牛仔布的印染工艺生产线,涤纶织物的传统印染生产线、针织品的印染成套工艺技术装备。染色发展也形成了品种齐全的系列产品。比如,坦克式、管道式、绳状、平幅以及多种溢流染色、气流染色、高温、高压、常温、常压染色等等,品种齐全,而且还实现小浴比染色。
印花是一项关键技术,在自主研发的基础上,通过引进技术、消化吸收,实现了再创新。随着传统的滚筒印花已经淘汰,随之而来的是平网印花机,有宽幅用于床单、装饰织物的;幅宽适应特种织物的;有刮刀式,有磁棒式,磁棒式也有电磁铁式和固定磁铁的等多种机型可供用户选用。之后的圆网印花机,同样有多种幅宽,大直径圆网、小直径圆网,刮刀式、磁棒式等等。
冷转移印花、热转移印花、衣片印花、冷轧印花等等。现在时髦的喷墨印花已推广多年。印花不但用在衣着装饰方面,而且还用于陶瓷印花。
印染之后的后整理工艺设备同步得到快速发展,诸如针织物的磨毛、起毛、化纤长丝织物的单面起绒、双面起绒、涤纶长丝织物的柔软处理等等。还有织物的涂层处理。
在发展主机的同时,轧、洗、蒸、烘四种单元机的技术水平同步提高。印染设备的专用基础件诸如对花装置、吸边装置、扩幅器、烘筒、导布辊和布铗链条同步发展。单机和联合机控制系统,在线检测和终端产品的检测都同步得到发展。
目前印染和后整理技术装备的主要任务就是围绕节能减排降耗做出新的贡献。
产业用设备成为亮点
随着产业用纺织品技术的发展,尤其是改革开放之后,随着产业用纺织品市场需求的拉动,产业用行业正在成为纺织工业对社会的一大贡献,也正在成为纺织工业发展的一个亮点。
改革开放之初,衬衣领衬、服装用衬布都靠进口,就连最简单的浆点撒粉工艺需要的原料和设备也都需要进口。后来,有企业从境外引进热熔,热风、热轧,瓶级塑料再生纤维生产,水刺工艺生产线后,人们才逐步认识到产业用纺织品工艺流程短,相对经济效益好,用途比较广泛等优势,从餐巾纸、衛生巾再到土木建筑,交通运输的需求,水刺针刺等设备相应而生,逐步实现了工艺技术装备的国产化。
目前,国产化的产业用纺织品的工艺技术装备品种规格已基本齐全。过去的粘合工艺、热风工艺、热轧工艺已基本淘汰,新发展的主要是纺粘工艺、熔喷工艺、水刺工艺和针刺工艺整套工艺技术装备。
从切片配置到螺杆挤压、熔体管道到纺丝、热轧的纺粘生产整套设备,品种规格齐全。
从切片输送到纺丝系统形成熔喷成套工艺技术装备自动生产线,品种规格齐全。还可以采用疊加式的使用,即S+M+S或者是M+M+S以及S+S生产工艺,制成不同规格的品种,适应市场需求。
从不同原料的混合、称量、梳理成网、水刺到烘干分切的水刺成套工艺技术装备生产线,工艺技术有显著提高。不但可以使用化纤混纺原料,而且新开发了纯棉纤维,制出高档水刺无纺布。
有了自己的专有技术,国产纺机设备不但供应国内市场需求,同样出口到境外,打出了中国品牌。
发展产业用纺织品,最难啃的硬骨头是针刺生产线,其中高速针刺机是关键中的关键,国际上也只有两家企业生产。针刺生产线可以生产产业用纺织品,从薄织物到地毯织物,工艺成套难度比较大,我们发挥自我优势,坚持技术创新,实现了国产化,而且有了自己专有技术。目前预针刺、上针刺、下针刺、花色针刺的生产工艺技术装备已经成熟,可以提供成套工艺生产线。
可喜的是我国碳纤维生产形成能力之后,碳纤维的织造、预浸、热固、成型的技术装备水平可以与境外企业相媲美,已经进入军工和汽车行业,有了新的起点。
大战略推进纺机进程
现今,在世界范围内,中国纺织工业不仅工业规模遥遥领先,其设备、技术也已经总体进入国际先进行列。这个重大进展,并不是自然而然形成的,其中确确实实有大战略在起着重大作用。
早在1988年7月8~14日,第一届中国国际纺机展览会在北京举行,来自世界20多个国家和地区的520家厂商、510多台先进纺织机械和仪器参加了展出。这也为中国纺机企业与世界先进技术近距离交流创造了条件。
之后,中国纺机发展步入了快车道。比如,1992年4月,“自动络筒机和无梭织机引进技术与国产化”(简称“两机”专项)开始实施。该项目批准的总投资为14.86亿元和国拨外汇1.56亿美元,总共从德国、英国、丹麦、日本、瑞士、法国、意大利等7个国家的17家公司引进19种纺机产品和相关专用基础件、配套件的设计制造技术。
随着行业的快速发展,我国纺机制造水平出现了飞速提升。2007年2月27日,国家科学技术奖励大会在北京隆重举行。纺织行业“年产45000吨粘胶短纤维工程系统集成化研究”项目获国家科技进步一等奖。以后又有“高效短流程嵌入式复合纺纱技术”、“筒子纱数字化自动染色成套技术与装备”、“千吨级干喷湿纺高强/中模碳纤维产业化关键技术”等三个项目获同一奖项。
纺织工业70年克服了诸多困难,取得了一个个令人瞩目的成就,实现了纺织大国向纺织强国的跨越。在此期间,中国纺机制造业也走过了一条从无到有、不断壮大的光辉历程。
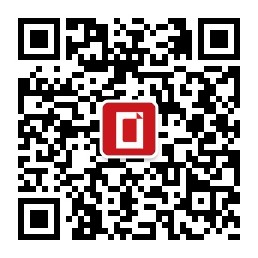