“灯塔工厂”之电子/ 半导体篇
- 来源:智能制造纵横 smarty:if $article.tag?>
- 关键字:灯塔工厂,电子,半导体 smarty:/if?>
- 发布时间:2021-03-20 15:04
美光新加坡工厂
美光科技是世界领先的创新存储解决方案供应商,先后推出了DRAM、NAND、NOR和3D XPoint™等存储方案,改变了世界使用信息来丰富生活的方式。新加坡工厂是美光的全球运营总部,助力美光高效地服务亚洲客户。
该灯塔工厂整合了大数据基础设施和工业物联网,以实施人工智能和数据科学解决方案。这些举措帮助它提高了产品质量标准,并使其新产品的生产速度翻了一番。
美光在新加坡不仅成立了非易失性存储器的NAND卓越中心,还设立了公司最大规模的制造基地,其中包括三个200 毫米和300毫米的存储器晶圆厂,以及一个测试和组装厂。卓越中心也包含一个NAND创新研发技术中心,以及一个为新加坡和亚太地区业务提供集中化支持的共享服务中心。
美光科技台中工厂
2020年9月,全球内存和储存解决方案领导企业美光科技位于中国台湾省台中市的工厂被评选为“灯塔工厂”,此前美光新加坡工厂已获选为“灯塔工厂”。
美光台中工厂在其尖端DRAM产品的开发和制造方面扮演着举足轻重的角色,该工厂生产制造的产品广泛应用于服务器、计算机、GPU、手机和高效能运算装置等。不同于传统的制造模式,美光台中拥有众多领域专家、数据科学家、数据工程师和软件工程师团队。此外,该工厂开发了集成物联网和分析平台,确保可以实时识别制造异常,同时提供自动化根本原因分析。在供应链和厂区还部署了人工智能和机器学习技术,提升效率,其显著的成果包含:美光台中厂区员工生产效率提升18%,机器非计划性停机时间减少30%,产品质量偏差率降低40%。除此以外,缩短新产品良率提升的周期20%,并减少用电量达15%。
英飞凌新加坡工厂
半导体大厂英飞凌科技在新加坡开展业务已经有约50年历史,通过数字化骨干和人员培养,在其制造工厂和供应链网络中应用数据、高级分析和自动化技术,从而降低了30% 的直接劳动力成本,提高了15%的资本效率。
2020年12月,英飞凌宣布未来三年将在新加坡打造它首个全球人工智能创新中枢的计划,包括投资2700万元及提升本地超过1000名员工的技能,作为整个企业集团进行数字转型的一部分。新加坡工厂已成为英飞凌开发智能生产方案以及测试车用微控制器的中枢,并且是其在全球重要的分销中心和亚洲重要的微电子学研发中心。新加坡工厂如今率先开展这个人工智能旅程,已拨出2700万元预算。
诺基亚芬兰奥卢5G工厂
当众人对诺基亚的印象还停留在手机品牌的时候,其位于芬兰奥卢的“未来工厂”已经在智能制造的实践中,成为先驱。奥卢的“未来工厂”旨在展示制造诺基亚4G和5G基站的工业4.0概念,利用诺基亚的专用(4.9G / LTE)无线网络为工厂内外的所有资产提供安全可靠的连接,在Edge云上运行的 IoT分析以及实时数字孪生运营数据。该工厂每天生产1,000个 4G和5G基站,每年产生重大改进⸺包括生产率提高30%以上,产品交付市场时间节省50%以及每年节省数百万欧元。
作为全球灯塔网络的一部分,诺基亚将与其他世界领先企业合作,分享知识和最佳实践,以帮助企业和制造商采用未来的技术,并克服企业在数字化转型过程中面临的关键挑战。大多数制造商寻求在工厂自动化和重新配置时提高灵活性。诺基亚针对高需求环境进行调整的专业知识可确保该公司具备将企业带入工业4.0时代的良好装备。屡获殊荣的未来工厂展示了客户设施如何从其在奥卢实现的业务中获得提高的生产率,敏捷性,产品质量和产品交货时间的好处。
诺基亚高管指出,即便5G在即,但4G网络目前尚未得到充分利用,并且仍在许多领域推出。运营商希望有更多的时间来收回他们对4G的投资,进而继续制定5G计划。仅使用 4G,高管估计他们已将奥卢工厂的一些产品线自动化提升至约99%,一些原型制作流程则需要手动完成。像诺基亚这样的公司面临着在不削弱4G的情况下鼓励更大连接的5G投资之间的微妙平衡。
富士康深圳工厂
2019年1月,富士康收到了扎根深圳30年来最值得骄傲的一份礼物。鸿海集团旗下的富士康深圳“柔性装配作业智能工厂”被宣布成为“灯塔工厂”,标志着富士康已成为制造业进入第四次工业革命时代的领导者之一。
富士康深圳工厂专门生产智能手机等电气设备组件,采用全自动化制造流程,配备机器学习和人工智能型设备自动优化系统、智能自我维护系统和智能生产实时状态监控系统。富士康注重优先引入第四次工业革命技术,令生产效率提高30%,库存周期降低15%。
据了解,富士康深圳工厂已基本实现了熄灯状态下的无人自主作业,全部生产活动由电子计算机控制,自主研发的雾小脑将海量设备连接至边缘计算及云端,应用到表面贴装、数控加工、机器人、组装测试、环境数据采集等场景中,覆盖全行业数据采集,而机器人+传感器的模式,则开发出机器人AI的自感知、自诊断、自修复、自优化、自适应功能,能在提高产品良率的同时降低成本浪费。
此次入选制造业灯塔工厂网络的深圳关灯工厂,整个项目共导入108台自动化设备,并全数完成联网化。在制程中SMT导入设备9台,节省人力50人,节省比例为96%;总成导入设备21台,节省人力74人,节省比例79%;测试部分导入设备78台,节省人力156人,节省比例88%。整体项目完成后,人力节省280人,人力节省88%,提升效益达2.5倍。
Rold意大利Cerro Maggiore工厂
这家仅拥有250名员工的企业,主要生产洗衣机和洗碗机锁定系统。作为“灯塔网络”中唯一一家中小型企业,Rold 使用智能手表、快速成型和数字仪表板等第四次工业革命技术,成功将营业额提升7%~8%。这表明中小型企业即便在有限的资源条件下,也能实现数字化。
Rold工厂内的SmartFab系统通过日常设备(例如触摸屏,智能手机和智能手表)将通知实时发送给操作员,以便响应紧急情况。触摸屏的安装,有助于将最重要的数据快速传递出去,易于操作员进行分析和采取行动。同时,办公室与触摸屏远程连接,管理层可以全面监督生产。
此外,工厂使用了基于车间物联网(IoT)设备的数据收集,并结合了商业智能工具,有助于提高Rold成本模型的准确性。同时,通过3D增材制造快速设计原型可以缩短新产品推出的上市时间。尽管大型企业被认为是工业4.0的最大受益者,但Rold表明,无论是在意大利还是在东盟,中小型企业都可以利用这些流程实现数字化。
施耐德电气法国Le Vaudreuil工厂
施耐德电气法国Le Vaudreuil工厂被评为全球制造业领域先进的“灯塔工厂”之一,源于其在应用第四次工业革命技术、实现生产现代化方面的突出表现。
施耐德电气Le Vaudreuil智能化集成工厂,在对一系列第四次工业革命技术的规模化应用过程中,将人与可持续性发展作为其创新策略的核心。通过引入增强现实等数字化技术,工厂操作人员可在跨站点操作、维护和能源使用过程中实现可视化,这不仅使维护成本降低了30%,相应的设备使用率还整体提升了7%。
施耐德电气Le Vaudreuil工厂还应用了最新的数字化工具,如EcoStruxure™ Augmented Operator Advisor,通过引入增强现实技术提高运营和维护效率,将生产力提高2%-7%。同时,在初次应用EcoStruxure™ Resource Advisor后,工厂的能源节约高达30%,且能效提升仍在持续。
结语
如今,工业制造产业正站在转型升级的十字路口,面对信息技术的赋能与商业模式的创新,也在同样面临着相似的困局⸺前路未知,智能制造在时代的聚焦下如何发展?
随着先行的智能制造探索者逐步在各自的行业上取得不错的实践成绩,市场也逐渐意识到,或许以他们的经验为主导,在探索工业制造业升级的旅程上,行业可以点亮新领域的“灯塔”,以此来指导其他智能制造企业的发展,加速整体产业智能化进程。
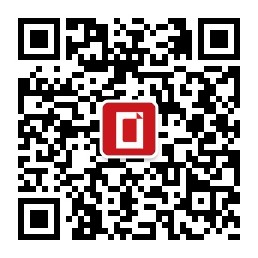