隆力奇:智能工厂建设路径解读
- 来源:智能制造纵横 smarty:if $article.tag?>
- 关键字:智能,建设,路径 smarty:/if?>
- 发布时间:2022-09-03 18:48
江苏隆力奇生物科技股份有限公司(以下简称“隆力奇”)成立于1986年,以优质的产品和周到的销售服务体系,将产品带到千家万户。随着互联网的发展,线上化妆品销售稳步增长。上升的市场规模、较高的品质要求、上升的成本、网络消费模式、消费者个性化需求的满足等诸多需求和变化,决定了化妆品生产企业必须随之改变现有经营和制造模式。
隆力奇通过梳理企业内部需求,构建了智能工厂的总体框架规划。确立以克劳丽工厂为试点,逐步推广到其它生产工厂,并进行人员组织配置,确保已规划的工厂有效落地和复制推广的总体策略。截至目前,隆力奇已在全球拥有五大智能工厂和九大研发基地,围绕日化美妆产品核心业务,打造了大规模柔性化生产的全流程、全链路、智能化生产新模式。
智能工厂建设实施规划
隆力奇智能工厂建设的总体目标是借助自动化技术、信息技术、智能化技术实现“集成化、精益化、数字化、互联化、智能化”,满足企业未来的规模化定制服务能力,同时搭建平台为日化行业数字化转型提供实践样本。
1、构建产品配方库,实现产品的全流程管理
为了实现产品的全流程管理,隆力奇进行了全要素仿真分析、三维流体学仿真测试、包装承压仿真测试,并集成了知识库,覆盖产品研发流程、化妆品配方及产品注册等方面。可以自动生成含量降序排列的全成分表,满足法规要求的1%以上的成分的降序排列,≤1%的成分可以按任意顺序排列。在符合法规的情况下,按原料特性对其赋能,令系统自动生成“活性成分在前,负面原料在后”的中英文全成分表。
通过PDM系统、营销系统、制造过程系统的有效集成,构建产品配方库,为客户个性化定制提供试样能力,同时能有效将数据传递到生产过程,实现过程自动化,为规模化定制提供有利保障。
2、实现柔性化制造能力,实现现场智能化
在现有应用机器人、影像检测仪等设备的基础上,加大关键工序的自动化、智能化改造,构建能够适应客户个性化需求的柔性生产线。各工序生产线单元中应用了大量的过程称重计量检测系统、控制组件与剔除装置,主要应用内容为半成品过程称重计量控制和成品检验。在满足国家CNAS认证的实验室内新增多种国际先进的测量仪器,从原料到成品,历经多重检测分析。
在生产现场,实现对原有人机协同的配料系统的改造,通过对原有配料配置加装传感器、流量计等智能硬件,实现对料仓的材料智能化的配料控制,以及对搅拌速度的控制,实现智能化配料;在生产造粒、研磨、出条、切块、丝印等各个环节实施相应传感器的加装,实现对设备与装置的参数和状态的实时获取,并实现集中控制;在装箱封箱、码拖环节实施自动化改造工作,结合自动化物流线、机器人等手段实现自动装封箱和码拖,降低每条产线工位人员6人,同时结合客户的产品包装要求、封箱要求及码拖要求,实现智能化的装封和码拖工作,相比原有模式,有效提升全流程的生产效率4%以上。
在产品外观检验方面,原有模式主要依赖作业人员和质检人员通过目视的方式进行检验,现场作业效率不高,且会因为节拍因素导致人员漏检情况。现结合质量检验环境的要求,进行了视觉检测及处置系统的建设工作。视觉识别及检测部分由计算机、相机、镜头、光源等组成,采用CCD照相机将被检测的目标转换成图像信号,传送给专用的图像处理计算机,实现自动识别功能,根据识别结果发出指令到控制执行部分。通过机器视觉与自动化装置的配合,将良品流转至下一工序,按照要求对不良品进行分拣处理。一方面,有效减少对质检人员的需求,避免人为因素的漏检问题;另一方面,实现过程环节产品的全部检验,在提升检验效率的同时又能保障产品的质量可靠。
3、计划协同与生产过程调度可视化建设
原有计划协同方式,主要通过人工编制同步到各个生产车间,生产车间通过现场记录再反馈到计划部门,需要大量的人力、物力才能够满足反馈需要,且在多次传递过程中存在数据失真、沟通不畅等因素。隆力奇有效融合营销系统、 ERP系统,通过MES、自动化车间改造等项目的推进,优化现有的生产计划体系,由现有的三级生产计划模式升级为一级生产计划模式,实现计划协同与生产过程调度信息的协同,从而提升生产效率。
原有生产过程主要依赖人工记录进行现场生产实际绩效的反馈,信息相对比较滞后。在生产现场对升级后的柔性制胶生产线罐体、搅拌器、输送泵、控制阀、智能传感器、清洗系统、控制系统进行组网,实现了对生产设备运行状态的监控。若遇到故障,传感器可自动识别,将PLC分析信号传送至故障报警灯或报警器以发出信号。通过与设备PLC采集通信,实时了解设备、流水线的运作情况。在生产信息反馈方面,业务接到订单,整理后发送供应链计划部,梳理分析后排入NC系统,通过车间模型及MES生产数据,实时地展示产品从生产到入库的整个动态过程,可及时了解生产情况及原料出入库、成品入库等情况,实现计划与生产实际绩效的实时反馈。
4、融合过程/存储一体化物流,建设物流一体化能力
配置自动识别技术设施、自动物流设备,建成智能化车间物流体系。该体系主要分为输送大宗原料的智能投送料系统、输送中间半成品的转储系统和灌装线送料系统。以智能投送料系统为例,主要进行大宗原料的生产线投送,整个系统主要由原料储罐、原料输送管道、输送控制系统等组成。在系统的统一指令下,指挥仓库智能堆垛机自动取放料。通过电动叉车将原料搬运到待转平台,原料直接被放置在立体库内暂存,通过堆垛机、输送机和提升机出货到原料仓出库口。系统同时接收各生产线完成产品的指令反馈,将加工好的产品通过小车送至出货端或立体库。
5、构建场务安全控制能力,实现风险预防与节能责任
通过信息技术实现过程的安全管理、监测预警、事故应急等管控。建立典型风险、隐患管理结构化知识库,自动给出安全管理建议,以风险管控为核心,逐步改善风险识别、评审和治理的各项过程管理模式;重要安全生产作业环节和部位实现实时监控、智能分析,主动发现违规行为、异常状态,及时报警并关联相关控制系统,实现智能预警、联动处置。建立能源综合管理监测系统,实现实时监测与控制:自动数据采集,保证数据的真实性,如原料和能源消耗、生产负荷、过程检验、设备停机等;建成实时运行工艺监控。显示报警显示盘、趋势图、控制图等,以便及时发现、及时处理;实时监控生产过程,包括能源、材料、产品、工艺、设备等,把控现场,监控异常并及时处理;实时监控生产进度,合理调度,均衡生产。实现批次成本、日周成本、成本趋势可视化。细化到物料、生产线、班次、班组、批次、操作员,有效降低能源和物料成本。细化到每次质检数据,通过SPC分析及时发现质量异常。细化到事件和调度管理过程。与ERP、SCADA集成,协调管理。集中技术、集中计划、集中监控、集中绩效、集中对标。实现工厂管理、工厂监控、工厂检验、工厂调度等一系列功能。
提升企业管理生产效率
通过整个智能工厂的建设工作,隆力奇实现了在各个环节的人员优化与岗位调整。通过过程智能化改造技术手段,产品节拍效率提升10%。结合工业视觉与自动化的整合能力,过程质量检验良率提升2%。原有生产模式异常的处理流程需要人工上报,通过设备互联互通与数据共享模式,协同效率提升30%。
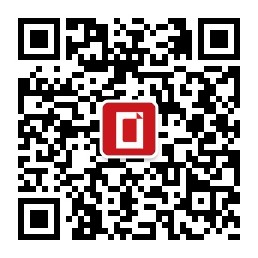