三座“灯塔工厂”解密博世行业先锋之谜
- 来源:智能制造纵横 smarty:if $article.tag?>
- 关键字:“灯塔工厂”,博世行业,先锋之谜 smarty:/if?>
- 发布时间:2022-10-07 15:39
在世界经济论坛公布的2022年新晋全球“灯塔工厂”名单中,博世长沙工厂(以下简称“博世长沙”)成功入选。这已经是博世中国于2021年、2018年无锡动力总成工厂以及苏州汽车电子工厂(以下简称“博世苏州”)相继获得“灯塔工厂”称号后,第三家工厂获此殊荣。
本期,我们将以其中两家为例,走进博世中国苏州汽车电子工厂和博世长沙工厂,共同探寻这家备受“灯塔工厂” 青睐的汽车企业在进行智能工厂的建设过程中有哪些奥秘。
苏州汽车电子工厂
2013年,为提高生产效率并降低生产成本,从而提升行业竞争力,博世苏州起步实施智能制造。2016年,在从无到有的传感器测试车间对数字化展开初步探索,并成功应用到电控单元制造车间;2017年,再次成功将成果复制到常州武进分公司。博世苏州凭借系统且全面的数字化转型战略;高可用、高可复制应用及全面体系的数字化人才发展策略,从业务模块集成互联化、流程智能化对企业进行转型升级。
博世苏州以业务梳理为基础,建设具有数据指导、自主行为发生和自适应流程的数据驱动工厂:
• 在供应链端,打造从供应商端到公司内部生产,及交付到客户端的整体信息及流程透明化,与前端供应商及后端客户积极打造实时交互的信息。移动互联网,云计算的日渐成熟,让各行各业都具备了收集、传输及处理大数据的能力。原材料或产品实体与互联网中的数据一一对应,数据信息的流动伴随着物料的流动,全部生产借助数据指导规划,驱动运转,供应链信息趋于透明。
• 在排产和销售方面,实现以产线柔性制造为基础,需求为驱动,依托大数据分析预测市场及客户订单量,实现小批次多品种高度个性化的订单快速生产,并拉动前端智能排产计划。
• 在运输端,实现自动物料供给及智能运输。
• 在制程工艺方面,实现实时工艺过程监控及预警处理,机器学习和决策,实现设备预测性保养和维护,并基于大数据分析及人工智能优化工艺流程,提升生产质量并节约成本。
以上流程目标中,博世苏州借助实时虚拟与现实的镜像,即数字孪生手段,对产品制造的所有环节进行虚拟仿真,从而提高了企业全产品生命周期制造的生产效率。
博世长沙工厂
作为全球“灯塔工厂”网络的全新成员,博世长沙凭借在人工智能驱动生产能源管理、机器人实时管理系统、数据智能决策、全透明的生产现场管理和端对端智慧物流中台等五个方面的前瞻性创新举措,为全球生产技术革新提供更大的规模化效益。
AI赋能节能减排,助力可持续生产
围绕中国的双碳目标,立足于可持续生产需求,博世长沙采用自研的人工智能驱动生产能源管理系统加速推进生产转型。该系统搭载自研AI算法,能结合客户需求及预测、生产计划、天气情况、温湿度等多项业务及环境因素,滚动给出未来7天内产线级的能源使用预测及生产排产。在预测结果精确到小时的情况下,平均绝对百分比误差仍低于3.2%。
此外,在AI算法的加持下,该系统还能提供优化的停机管理和精确的能耗异常监测,让节能减排深入到各个环节。当前,该系统已帮助博世长沙实现年耗电量减少18%,二氧化碳排放量降低14%,并进一步引导生产转型数字化进程。
全面打造敏捷、高效供应链网络
在博世长沙,端到端的物流集成平台将第四次工业革命的创新步伐从实体工厂拓展到其供应链的上下游。从原材料供应、运输、内部流转到生产及货物出厂,整个流程都由物流中台通过实时数据连接,在流程大数据的加持下实现全局赋能。
通过对自动导引运输车(AGV)、RFID/视觉识别、自动化应用以及智能报表的灵活调度,并结合云技术、AI技术与物流业务的深度融合,该平台帮助博世长沙节省了30%的物流成本和15%的库存周转天数,使生产周期缩短至3年前的 64%。在大大提高生产效率的同时,其创新的方案和系统创造了博世全球多个第一。
数字智能决策,提高生产运营效率
制造行业的高质量发展离不开持续的技术创新。通过使用各类智能传感器,博世长沙对生产过程中的各类数据进行持续采集。基于海量数据资源,数据科学家团队运用大数据技术、机器学习算法对其进行深入分析并建立高精度耗品使用寿命预测模型,从多个维度对生产表现和易耗品损耗情况进行分析,给出易耗品最佳更换时间。
经由模型的把关,在提高产品质量稳定性的同时还避免了单一的经验和人工误判造成的浪费。该模型上线后帮助提升焊接电极、车削刀具等生产易耗品30%以上的使用寿命,并节省了50%的更换时间。
智能设备维护管理,强化成本竞争力
深度数字化和智能化不仅能够提升维修流程的敏捷性、高效性,同时也实现了设备智能化管理,为稳定生产排除后顾之忧。博世长沙的设备预测性维护系统使用深度学习算法,通过对历史数据的分析和实时数据的监控,实现了设备从预防性维护到预测性维护的转变。
AI预测模型对设备24小时内的健康情况进行预测,并给出预先警告,帮助维修和生产人员提前准备和快速响应,减少紧急维修工单的产生,提前规划保障了生产的稳定性。该系统的使用节约了19%的维修时间,节省了25%的维护成本和 17%的缺陷成本。
全面数字化管理,创造更广泛价值
有效的数据互联互通在推动规模化发展中功不可没,而以人为本能最大化技术和创新基础设施带来的效果。通过渗透率达到100%的可视化数字化车间管理,博世长沙内部实现了涵盖流程、原料、设备、人事、文件系统等多个业务环节的精益日常管理。基于电子文档的流程全面数字化,为其他基础设施的建立奠定了标准。
车间数字化管理系统由可视化5M1E(人员Man、机器 Machine、材料Material、方法Method、测量Measurement和环境Environment)平台赋能,实现了基于人员资质、能力认证、变更点控制管理的智能人员分配。博世长沙也因此实现了20%的生产力提升,并有效缩减12%的人力成本,更创下了顾客零投诉的记录。
据了解,未来博世中国将继续致力于技术革新,深度聚焦物联网、人工智能、生产流程自动化、智能化、数字化的全面实现,构建智能制造价值链及智能生态系统,向“未来工厂”的建设目标持续迈进,率先踏入工业4.0的新阶段,助推中国先进制造业领跑世界。
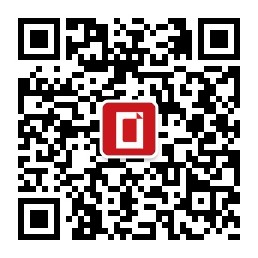