增材制造为复合材料制造商提供机会
- 来源:国际工业激光商情
- 关键字:复合材料,制造商,机会
- 发布时间:2023-06-21 20:52
与传统生产工艺相比,增材制造(AM)有能力打破工业流程并有助于实现创新、经济高效和快速的结果。与复合材料产品需求的快速增长相吻合,增材制造将彻底改变国防、航空航天和其他行业的复合材料生产。复合材料天生比传统材料更坚固、更轻、更环保。在这些领域,增材制造可以用于空气、流体和能源管理应用的管道和通风口的芯轴制造。
芯轴是制造中空复合材料零部件时必不可少的工具。在制造过程中,芯轴被插入管子或管道末端,并在周围形成物体时固定到位。这确保了成品保持形状和尺寸。传统上,最常见类型的芯轴由钢制成,但也可以使用铝和其他金属。然而,这样材料的芯轴的应用受限且可能造价高昂。本文将解释如何通过增材制造生产芯轴,作为复合材料制造的耗材来简化和优化制造过程。
复合材料是由两个或多个不同的部件组成的材料,广泛应用于制造业。这些成分可以是金属、聚合物、陶瓷、纤维和各种其他物质的组合,具体取决于应用。复合材料被用于各种工业应用,因为它们具有许多优点,例如重量轻、高燃料效率并表现出更高的强度、更高的稳定性、更大的耐磨损性,以及更高的耐候性和环境友好型。
复合材料也比金属、塑料和陶瓷更容易制造,也可以成型较为复杂的形状。通过将不同类型的材料结合在一起,工程师可以创造出满足特定要求的材料,并为许多行业提供服务。随着对复合材料需求的不断增长,很明显,这些多功能材料将在未来几年继续在工业中发挥重要作用。
传统制造VS 增材制造芯轴传统的芯轴
制造方法已经存在了几个世纪,至今仍在使用。主流的传统制造方法主要有三种:铸造、锻造和机加工。铸造是制造工业芯轴最常见的方法。在这个过程中,熔融金属被倒入模具中,该模具具有所需芯轴的形状。待金属冷却并硬化后,将芯轴从模具中取出。在锻造过程中,将一块金属加热至具有延展性,然后使用锤子和其他工具将其成型为所需的芯轴。在机械加工过程中,使用车床、铣床或其他机床将金属件切割或铣削成所需形状。
传统制造芯轴的工艺技术有许多缺点,其中的关键是耗时、劳动密集、经常产生大量废料,并且它们所能达到的几何复杂性有限。增材制造可用于创建具有复杂几何形状的芯轴,这些芯轴很难或不可能使用传统方法生产。增材制造提供了一种更灵活的方法,可以非常快速地创建具有复杂设计和内部功能的芯轴,而不需要昂贵的切割工具。如果是复杂的几何形状,传统的芯轴生产方法需要生产多个零件,而这也意味着额外的成本,非常耗时并可能出现错误和返工。
使用增材制造芯轴的好处包括更低的工具成本、更短的交付周期和更大的设计灵活性。增材制造的芯轴可以从数字文件中快速轻松地制造出来,非常适合短期或一次性生产。此外,与传统工艺相比,它们在形状和几何形状方面为设计师提供了更大的自由度。
Massivit 的解决方案
Massivit 3D 开发了一种专有的打印工艺,用于生产坚固耐用的芯轴。这为复合材料零件的生产提供了一种高度创新的解决方案,与传统方法相比具有显著优势,能够以更短的交付周期和更低的成本生产高质量的复合材料零件。如前所述,使用增材制造芯轴的一个关键优势是,可以实现更为复杂的设计。借助增材制造,芯轴零件的几何形状没有任何限制。这为芯轴设计开辟了一个全新的可能性范围,意味着它们可以根据特定应用的特定需求进行定制化生产。
随着对复合材料零件需求的增加,对更高效、更具成本效益的生产解决方案的需求也在增加。Massivit 开发了Massivit 10000 增材制造系统以满足这些要求。该设备结合Massivit 3D 的专利凝胶点胶印刷(GDP)方法,使用了运动浇铸(CIM)技术。它允许将模具直接铸造到3D打印的外壳中。为了实现这一点, Massivit 10000 采用了双头系统和超快专利技术。所有这些都使制造商能够在数小时内而不是数周内生产出复杂的芯轴。
Massivit 的防水材料非常适合芯轴的生产。这种材料最显著的特征之一是可以在水中轻松分离。这使得心轴在生产后能够容易地从最终产品中移除。该材料也很轻(在生产过程中易于处理和运输);坚固耐用(可用于各种应用);环境友好(与减法相比,最大限度地减少浪费,并最大限度地降低对大量材料储存的需求);而且速度快,芯轴只需几个小时就能打印出来。
工艺流程
为了说明Massivit 3D 芯轴生产方法的颠覆性,本案例研究着眼于为国防和航空航天部门服务的Kanfit 公司制造芯轴所涉及的工艺步骤。委托使用的芯轴需要用Massivit 的防水材料打印,打印模具的外表面需要非常光滑。
首先,创建了尺寸为381 mm(X)、191 mm(Y)和 567 mm(Z)的芯轴CAD 模型。为了使其与Massivit 的3D 打印技术最佳对齐,模型的法兰区域进行了数字扩展,以更好地进行叠层制造,模具壁设计有三个最终宽度为5.4mm 的打印轮廓,以承受制造阶段的真空压力。
根据完成的CAD 文件,在Massivit Smart 切片机软件上创建了芯轴的G 代码。打印是为了使用最少的时间和材料而设计的,总共只用了8 小时。这个芯轴样品是使用的是Massivit 水溶性DIM-WB 光聚合物材料生产。在对零件的后处理过程中,表面用砂纸打磨并涂上一层环氧树脂,使芯轴表面不透气。
对于叠层阶段,芯轴设置在旋转夹具上,从而能够在工具周围应用环氧树脂和碳纤维片(总共6 片)。一旦涂上碳纤维,模具就进入真空过程,在真空压力下保持3 小时。然后将其取出并静置24 小时,最后固化。
完成的模具被放置在清水中24 小时,所有残留的水溶性材料被从表皮上移走。然后对芯轴进行修整,并在发布前在质量控制部门进行验证。与传统生产相比,使用增材制造生产芯轴来制作此类应用中的复合材料部件,可以简化和精简复合材料的生产过程。
彻底改变制造业
使用增材制造的芯轴有可能彻底改变复合材料零件的制造方式。与传统制造的芯轴相比,使用增材制造生产的芯轴优势明显。此外,使用增材制造制造的芯轴可以用先进的材料生产,如Massivit 的水溶性材料,简化了后处理过程中的拆卸。
这使得生产的复合材料零件质量更高、更可靠。随着增材制造芯轴的出现,复合材料零件制造的前景是光明的。
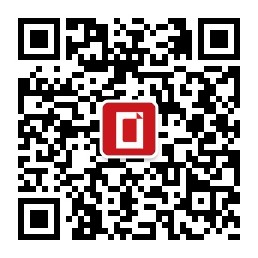