下一代汽车需要更明确的互连策略
- 来源:国际汽车设计及制造 smarty:if $article.tag?>
- 关键字:汽车,策略,功能 smarty:/if?>
- 发布时间:2023-11-17 19:36
当前汽车设计日益复杂,为提高舒适性、提升性能和确保更高的安全性,很多汽车的设计中融入了更复杂的功能。安装在汽车上的传感器和成像设备的数量也在急剧增加。这种情况不仅出现在豪华车市场,中档乃至经济车型也在增加额外的功能。
与此同时,其他动态因素也在改变汽车设计的实施方式。为减轻重量以延长电动汽车(EV)的续航里程,过去采用的机械系统正在逐步被淘汰,取而代之的是电子线控系统。
这两种不同的趋势将带来同一个必然的结果:现在普通车辆所产生和传输的数据量会比过去传统汽车要大几个数量级。此外,应该注意的是,随着汽车自动驾驶水平的提高(且我们开始迈向车辆完全无人驾驶的阶段),数据量只会越来越大。
数据爆炸及其影响
据分析公司麦肯锡预计,如今普通车辆每小时产生的数据量已达25GB左右,但这仅仅是个开始。安装于车身内外的摄像头数量还在持续增加,且例如激光雷达、飞行时间(ToF)和超声波等3D成像技术也将在短短几年内成为一种常见功能。
如果汽车系统要做好充分的准备以应对前所未有的数据需求,那么支持性的互连解决方案也需要得到相应发展。此外,构建并向市场提供此类解决方案的方式也将发生根本性变化。
互连器件要想在充满挑战的汽车环境中发挥效用,并符合严格的国际标准(如欧盟的LV214和美国汽车工程师学会的USCAR2),就必须具备多种属性。首先,它们需要能够承受冲击和振动,其次,还要考虑到暴露于高温环境中的问题。不过,随着汽车行业从燃油车转向电动汽车,这一问题会逐渐减少。
电磁干扰(EMI)源的存在如不予解决,则可能会对传输数据的信号完整性产生不利影响。为解决这一问题,需要在模块中加入屏蔽装置。随着时间的推移,锡须的出现会对互连的可靠性造成严重影响,并有可能出现短路,从而导致系统故障。
此外,车辆设计的空间限制意味着汽车级互连器件必须非常紧凑。这通常需要高密度解决方案。在某些情况下,这些解决方案可能需要将电源和数据传输结合起来。
解决组装方面的问题
除了考虑互连器件本身的性能和可靠性,电子控制单元和传感器模块的一级供应商还必须考虑互连器件集成对量产组装制程的影响。若安装互连器件会增加必要的步骤数量,从而减慢工作流程,这将意味着产出会受到影响。例如,如果需要旋转PCB以改变朝向,则会浪费时间。此外,如果互联器件的组装需要人工干预(而不是完全自动化),那么整个流程的耗时也会更久(出错的风险也会大幅增加)。
鉴于上述问题,压接互连技术日益受关注。压接连接能够提供可靠且简单的连接方式。通过使用这种技术,就能大幅提升组装工作效率,还能避免复杂、劳动密集型和混乱的作业流程(如焊接)。
免焊连接还带来了另一项显著优势:锡膏是完全刚性的,因此在受到冲击或振动时容易开裂,而压接连接具有更大的容差。因此,采用压接连接的模块比采用焊接引脚的模块具有更长的使用寿命。
Interplex开发的压接连接目前已广泛应用于车用系统,并获得了众多一级供应商的认可。其厚度从0.4毫米到0.8毫米不等,可提供持续可靠的运行,且易于装配。除了机械方面的稳定性外,它们还具有强大的保持力和行业领先的热特性。
通过可应用于压接互连的IndiCoat电镀专利技术,Interplex能够克服锡须这个对于其他连接器供应商来说颇为挑战的困难。基于此,最终产品的质量可得到长期的保证。
很多汽车企业都希望将电子控制单元或传感器模块的设计工作外包,而比起通过公司内部或其一级供应商来进行,许多企业现在都依靠Interplex来承接这些工作,进而将工程资源集中在自身能够获得最大差异化之处。
通过与Interplex合作,汽车品牌能够利用高精度机械工程和涂层技术等领域中业界领先的专业知识。图2所示的雷达单元和图3所示安全气囊电子控制单元都是Interplex为汽车部署而设计和制造的众多模块之一。
定制电池互连系统助推轻量化趋势
在刚刚落幕的第九届上海国际新能源汽车技术与供应链展会(NEAS China 2023)上,Interplex展出了其出行服务相关的产品线,包括新的基于无焊接卡入式布置的、灵活的新型专有电池互连CCS组件Cell-PLX™等在内的与能源、动力和先进出行相关的产品。
Cell-PLX™是Interplex为满足客户应用需求而设计的定制电池互连系统,适用于圆柱形、软包和方形电池模组设计方式的锂电池组,包装形式坚固耐用,可用于高振动性环境。灵活性和可定制性是电池互连应用的关键,Cell-PLX™支持各种设计配置形式的探索和开发,其高精度元件无缝集成到一个精心组织的系统中,提供了一个可满足客户电池设计要求的可靠电池互联系统。
电池的成本在整个新能源车占比是最高的,虽然目前中国新能源汽车市场的渗透率刚超过30%,但为了适应电动汽车的快速发展,同时也为了降低成本,作为Cell-PLX™的关键组件,CCS的创新和变革是亟需的。
当前,电池包的主流设计方向有CTP和CTC,其最大的挑战是体积,同时,对精密度的要求也很高,盖板一定要准确放在电芯上,否则就没有办法焊接,因此,冲压一定要精密。在设计方面,传统式的电池盖板设计会多一层很厚的铝排,把电流引回去,但Interplex的设计是U型的一片式设计,盖板厚度可以做到2毫米,并且可以保持一致,因此电流分布很均匀。
“我们在设计U-Turn时,会把长铝巴片去掉,这样做一方面可以节省成本,另一方面极薄的铝巴片盖在电芯模组上重量分布很均匀。”Interplex能源系统产品总监陈志伟分享到,“传统客户需要购买铝排、电芯支架等部件,Cell-PLX™把塑料托盘、铝巴、FPC结合在一起变成系统,客户只需要购买这一个部件就可以直接把它放在电芯上面,用激光焊接连接即可,可以显著优化成本增加效益。”
“我们有超过半个世纪的精密冲压和大件冲压的经验,因此在做这条年轻且非常有前景的产品线时展示出的铝巴片是大件冲压的外形尺寸,同时里面的精密连接和精密冲压又有很大的关系。”Interplex中国区移动业务负责人张寅分享道,“我们以前有接触到很多国内自研的客户,他们要的做的产品都是1毫米、1.2毫米甚至有到1.8毫米的,而Interplex可以轻松做到0.3毫米厚并且能够保证品质,在我们进入市场以后可以帮助客户直接巴片减少厚度,节约成本并且减少电池包的重量。”
圆柱形电池的电芯规格相对规范,产品更加标准化,电芯的一致性更高。张寅还告诉我们,对于在国内刚刚起步适用于圆柱型的CCS汇流排,Interplex有很前瞻的视角以及落地经验。“Interplex作为圆柱电池领域比较领先的方案解决供应商,三年前我们与圆柱电池相关的CCS汇流排已经开始在杭州工厂量产了。Interplex一直走在前沿,从18650的电芯到21700的圆柱电芯以及现在的4680电芯都有涉及。”
电动汽车制造商及其电池供应商和技术合作伙伴需要应对两大重要问题,即成本上升和可持续性。Interplex的 Cell-PLX™ 互连制造方案可实现电池互连过程的自动化,其作为一种大批量解决方案,可大幅节省时间和成本。其在回收和电池更换方面也具有显著的优势,能够为环境带来积极影响。
值得一提的是,Interplex可以根据客户车型的不同以及对图纸要求和电气性能的差异化,从选材开始就提供一站式的定制服务。“不同于现在市场上大多直接一体冲压形成的硬母排,我们还提供了柔性母排,通过非常薄的材料叠层和焊接达到柔性母排的效果,每层最薄可做到0.2毫米,我们也是国内为数不多能将这项技术进行量产的工厂。”张寅如是分享道。
结语
显然,现代汽车制造商及其一级合作伙伴需要卓越的互连器件。这些产品不仅必须提供该领域一直以来所期望的更高性能和长期可靠性,还必须超越当下,提供简单的组装和充足的适应范围,从而降低总成本并实现产量最大化。
Interplex技术团队服务汽车领域的客户已有数十载,无论是对于当前处于开发进程中的新车型,还是尚未发布、仍处于概念阶段的车型,Interplex技术团队都能深入洞察其需求。在电子控制单元和传感器模块中加入压接端子,可使装配更轻松,从而加速生产流程以助力提高盈利能力。此外,在构建这些模块时,通过采用顶部加载、基于平台的方法,能够实现足够的灵活性,从而尽可能地提高生产流程的成本效益。
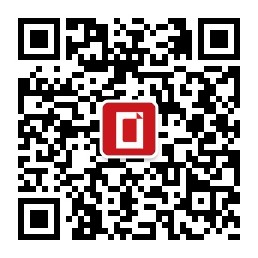