人工智能推动光子系统制造
- 来源:国际工业激光商情 smarty:if $article.tag?>
- 关键字:人工智能,光子系统,制造 smarty:/if?>
- 发布时间:2023-11-17 20:25
如今,光子系统制造的许多趋势已经非常明显,这些变化包括组件微型化和集成化、批量规模扩大,以及越来越多地扩展自动化和可持续制造。与此同时,质量控制仍然是首要任务,但也面临着越来越多的挑战,例如零缺陷生产或完全可追溯性。要实现这些目标,就必须采用“检测/ 预测/ 预防/ 修复”的方法,这种方法的基础是全面的传感器网络(可监控生产链中的每一个步骤)以及利用这些网络产生数据的复杂软件。因此,人工智能就成为了成功的关键。
对此,一些欧洲公司和研究机构联合开发了“适用于新的和现有光电子制造生产线的整体框架,以实现灵活性、零缺陷生产和可持续发展”研究项目(iQonic)。在“欧洲地平线2020”计划的资助下,iQonic 项目旨在探索传感和工艺链,以提高光电子制造的质量、可重构性和可回收性。
该项目将零缺陷制造定义为,是一种防止有缺陷光子部件到达客户的方法。因此,所有工作的重点都是在制造流程和供应链中尽早识别缺陷部件。在过程中,许多步骤中的每一步都成本高昂,因此通过尽早识别和消除潜在的缺陷部件,可以帮助用户节省时间和成本。
根据项目研究人员发表的一份科学出版物,他们选择了零缺陷制造,而不是其他质量改进方法,如六西格玛或精益六西格玛。他们之所以做出这样的决定,是因为光子制造流程具有独特的特点,即中小批量生产、高价值产品的个性化以及具有不同制造流程和技术序列的长价值链。这些特点不仅产生了大量与生产相关的数据,而且还需要结合使用基于统计和知识的技术来解释这些数据。
工业应用案例
该项目于2022 年秋季启动,总体思路是收集不同应用案例中光子制造链各个环节的数据,并考虑团队成员如何利用这些数据来提高制造性能,以实现零缺陷制造。在这一框架内,合作伙伴在四家参与公司的应用案例中开展工作,包括Alpes Lasers 公司的量子级联激光器(QCL)生产;Brighterwave 公司的光电多组件模块的大批量生产;Filar Optomaterials 公司的原材料合成晶体生产;以及Prima Electron 公司的光纤耦合高功率激光二极管模块生产。
实现项目目标的方法与工业物联网或工业4.0 采用的方法类似,采用智能传感器和软件监控和改进生产流程。更具体地说,来自质量控制框架的数据可用于指导制定进一步的质量措施(以验收合格与不合格部件为衡量标准)或启动维修流程。数据还可用于制定措施,在流程早期预防缺陷,从而帮助提高质量,最终实现零缺陷生产和零浪费的目标。该项目的所有四个用例都成功实施了这种制造方法。
预测激光故障
Alpes Lasers 公司为生产量子级联激光器而实施的用例,体现了光电系统制造过程中的许多典型挑战。生产量子级联激光器首先要采用复杂的半导体加工技术,将激光结构加工到晶片上。这一步之后还有大量复杂的制造和测量步骤来完成激光模块。
虽然许多单一的测量都会沿着这条制造链提供数据,但最终的接受/ 拒绝决定取决于激光器是否能在特定温度下的特定波长上达到预期的输出功率。重要的是,在加工过程的不同阶段,可能会出现一些问题,导致激光器成品出现故障,从而导致组件失效。显然,决定接受/ 拒绝的标准无法在早期生产步骤中进行测试。不过,某些传感器数据有助于在生产早期预测成品模块的故障。
例如,如果显微图像显示光栅结构缺失,则该部件将无法产生正确的辐射。该项目的目标是利用传感器数据和机器学习建立图像数据与最终激光输出之间的关系。有了这种方法,就有可能在流程早期预测哪些部件的输出功率会低于所需的阈值。此外,生产操作员可通过用户界面做出此类决定。
发现光栅缺陷
研究人员发现,在制造量子级联激光器时,用于检测缺陷的目视检查和显微镜检查足以为预期决策过程收集数据。目视检查的主要目的是发现激光器光栅结构中的缺陷。从数据采集到决策的过程可分为四个步骤。
前两个步骤包括图像采集、透视和透镜畸变校正,然后是设备映射过程,在设备映射中识别晶片上的光栅结构。图1 所示的低分辨率图像提供了有关光栅质量的信息。需要注意的是,光栅一旦被嵌入到晶片顶层,在后续处理步骤后就不再可见。
第二步需要重建晶片图并创建光栅图像。结构的配准利用的是晶片上的对应点。通过训练有素的分割模型可以识别出几类缺陷,并创建带有缺陷彩色标记的新晶片图像,提供给操作员(图2)。
第三步是对设备缺陷进行评估,首先要准备一个训练数据集,根据故障与否对过去的设备进行区分,然后训练机器学习软件推断任一设备类别的特征,以识别不同类别的缺陷。训练完成后,这些模型就能为识别图像中的潜在缺陷提供合理的建议。
第四步也是最后一步,决策支持系统会将前几个步骤的输出结果结合起来,并将结果直观地呈现给操作员(图3)。
使用显微镜检测故障
通常使用放大5 倍的显微镜检查晶片是否有缺陷。这足以识别每一个激光芯片,并破译受缺陷影响的芯片。对于一个2 英寸的晶片,需要将400 张显微镜图像拼接在一起。合并后的图像包含20000 × 20000 像素的彩色信息。显然,缺陷检测评估过程的自动化可以节省大量时间。
同样,自动化的评估过程必须先对图像进行映射,才能有效识别缺陷。在这种情况下,需要应用一套复杂系统控制,包括旋转、平移和缩放过程,以提供最终的映射图反馈。映射过程完成后,缺陷检测算法将应用于调整后的图像。缺陷检测采用模板匹配、阈值处理、形态学运算和边缘检测等图像处理技术。
检测结果用于判定每个部件“合格”或“不合格”。Alpes Lasers 公司用例的软件实施由技术提供商开发的子服务组成。这些子服务通过高级通信中间件(HLCM)实现的公共总线进行通信。HLCM 遵循微服务架构,充当协调者的角色,促进低分辨率和高分辨率晶片图像的信息流。
数据分发通过MQTT 代理(一种机器对机器的网络协议)实现,其中图像由制造商发布、聚合,并通过不同的微服务进行转发,这些微服务负责映射晶圆设备、检测缺陷,并向决策支持系统(DSS)提供输出,以便制造商工程师轻松识别有问题的设备。DSS 是向操作员展示两个评估步骤结果的用户界面(图3)。
结果
在Alpes Lasers 公司用例中实施的系统,对来自多个晶片的数百台激光器进行了测试。结合使用两种缺陷检测方案,结果表明,与被归类为“不合格”且光栅缺陷全无的激光器相比,被归类为“合格”且光栅缺陷全无的激光器在特定频率上发光的几率要高出6 倍。
正如一位实践“iQonic 项目”零缺陷制造方法的终端用户所指出的那样,这对Alpes Lasers 的QCL 制造工艺而言已经是一个巨大优势,因为有缺陷的组件将免于后续漫长而昂贵的增值制造过程,并且不会影响产量。
这一新的光电设备生命周期监测工具同时使用了图像处理和深度学习算法。通过使用低分辨率光栅图片和高分辨率表面扫描图像的两个基于图像的缺陷检测管道,实现了自动化缺陷识别。所有获取的数据都标有额外的缺陷类型分类,从而为光电工程师提供了设备维护指导。
iQonic 项目的其他三个用例也开发了类似的系统。这些系统还使用了嵌入ficonTEC 机器的设备或化学传感器的数据输入。所有使用案例都表明,对制造过程早期收集的数据进行汇编和分析,可以准确预测最终产品的性能。这样就可以在制造链的早期阶段重新安排部件的生产路线,让有缺陷的部件在浪费额外的加工步骤之前,就得到回收、维修或移除。
iQonic 项目于2022 年9 月启动,弗劳恩霍夫应用光学和精密工程研究所等参与方将继续改进该技术。
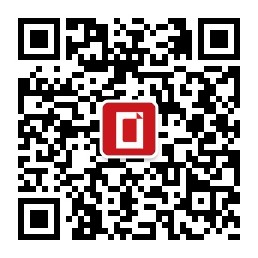