新质生产力:强化智能制造的根基
- 来源:智能制造纵横 smarty:if $article.tag?>
- 关键字:新质生产力,智能,制造 smarty:/if?>
- 发布时间:2024-05-12 15:03
今年全国“两会”中,新质生产力被写入政府报告,发展新质生产力成为我国制造业下一阶段的重要目标。如何发展新质生产力?在政府会议中也对其进行了解读,即“新质生产力是创新起主导作用,摆脱传统经济增长方式、生产力发展路径,具有高科技、高效能、高质量特征,符合新发展理念的先进生产力质态。它由技术革命性突破、生产要素创新性配置、产业深度转型升级而催生。”
在我国制造业以智能制造为主攻方向转型升级的大背景下,以科技创新为引领的新质生产力的提出,进一步支撑了行业向高端化、智能化、绿色化前进的步伐。对于制造企业而言,发展智能制造推动转型升级是智能化技术的价值创建与企业制造系统业务重构的过程,是通过新的技术、新的方法、新的速度、新的服务、新的价值、新的集成,一步一步推动企业逐年提升、创建并实现智能制造。
智能制造新模式
对于企业智能制造的实施,在工业和信息化部联合发展改革委、科技部和财政部编制的《智能制造工程实施指南》中,对不同行业、制造模式的转型进行了解读,并明确指出离散型智能制造、流程型智能制造、网络协同制造、大规模个性化定制、远程运维服务共五种智能制造新模式。对于其中的关键要素,本期内容中我们一起来分享。
1、离散型智能制造
离散型智能制造新模式包括:车间总体设计、工艺流程及布局数字化建模;基于三维模型的产品设计与仿真,建立产品数据管理系统(PDM),关键制造工艺的数值模拟以及加工、装配的可视化仿真;先进传感、控制、检测、装配、物流及智能化工艺装备与生产管理软件高度集成;现场数据采集与分析系统、车间制造执行系统(MES)与产品全生命周期管理(PLM)、企业资源计划(ERP)系统高效协同与集成。
2、流程型智能制造
流程型智能制造新模式包括:进行工厂总体设计、工艺流程及布局数字化建模;生产流程可视化、生产工艺可预测优化;智能传感及仪器仪表、网络化控制与分析、在线检测、远程监控与故障诊断系统在生产管控中实现高度集成;实时数据采集与工艺数据库平台、车间制造执行系统(MES)与企业资源计划(ERP)系统实现协同与集成。
3、网络协同制造
网络协同制造新模式包括:建立网络化制造资源协同平台,企业间研发系统、信息系统、运营管理系统可横向集成,信息数据资源在企业内外可交互共享。企业间、企业部门间创新资源、生产能力、市场需求实现集聚与对接,设计、供应、制造和服务环节实现并行组织和协同优化。
4、大规模个性化定制
大规模个性化定制包括:产品可模块化设计和个性化组合;建有用户个性化需求信息平台和各层级的个性化定制服务平台,能提供用户需求特征的数据挖掘和分析服务;研发设计、计划排产、柔性制造、物流配送和售后服务实现集成和协同优化。
5、远程运维服务
远程运维服务新模式包括:建有标准化信息采集与控制系统、自动诊断系统、基于专家系统的故障预测模型和故障索引知识库;可实现装备(产品)远程无人操控、工作环境预警、运行状态监测、故障诊断与自修复;建立产品生命周期分析平台、核心配件生命周期分析平台、用户使用习惯信息模型;可对智能装备(产品)提供健康状况监测、虚拟设备维护方案制定与执行、最优使用方案推送、创新应用开放等服务。
今年,我国制造业增加值占全球比重约30%,连续14年位居全球首位。截至2023年年底,我国已培育421家国家级示范工厂、万余家省级数字化车间和智能工厂,累计在国家层面创建绿色工厂5095家。作为智能制造发展的典型应用场景,智能工厂在我国经历了从理论到示范到落地的过程,越来越多的企业结合自身情况改造、新建独具特色的新工厂,在优化流程、降低成本、提质增效等方面取得了不同的收获。
智能工厂落地案例
某鞋业集团经过近三十年的发展与优化,拥有行业内较为先进的管理模式和业务流程,例如部署ERP、CAD/CAM、MES等工业软件建立信息化基础应用管理平台,应用于企业管理、生产、研发方面。
企业计划建设皮鞋数字化车间,提升皮鞋自动化智能制造设备、在线生产及检测技术,实施MES、WMS系统并与企业现有的ERP、OA等系统无缝集成,打通企业全供应链管理,打造鞋业特色的智能制造新模式,将全面提升产品质量、提高生产效率、缩短研发周期(快速响应市场需求),从而提升企业运营效率、降低生产成本。
其实施内容包括采用智能化鞋楦机、智能裁床、工业机器人、柔性生产线、智能定型线等高端智能装备,打通裁断、针车、成型三大工艺流程,打造从下料、裁断、针车、成型、包装到出货的全流程的数字化车间。重点实施ERP企业资源管理、MES生产制造执行系统,集成ERP、MES、CAD/CAM、鞋博士、HR、ERP-U8等信息系统,实现生产车间的数字化和智能化管控。通过智能设备和系统的集成应用,提高生产效率、提高产品质量、降低人工成本。
1、数字化产品设计
该企业应用鞋博士进行产品设计开发,通过网络接收客户的产品需求信息,业务人员将相关信息录入至ERP系统,通过ERP系统进行产品的研发管理,样品的制作可通过3D打印机直接进行打印,与客户完成异地确认,实现样品的快速开发与确认。
2、智能化生产制造
根据精准生产的管理理念,进行车间生产装备的改造升级,应用自动流水线设备、鞋面打粗上胶设备、震动刀头切割机、捏炼机、三维打印设备、电脑控制中后帮机、电脑控制自动前帮机、中底裁断机、自动激光切割机、自动化成型线、鞋业智能柔性全自动包装线等高端装备。将原本的裁床、缝纫、定型生产几大工序进行融合贯通形成定型—成型—的一体化作业,提高生产过程的自动化,减少中间人工作业和搬运环节,降低制造成本。
3、数字化运营管理
该企业已建立一套业务比较先进的ERP系统,用于企业的进、销、存及生产管理,通过ERP系统里的采购/仓库管理进行生产物料的采购及供应商的管理。计划全面实施MES生产制造执行系统,提升生产制造过程的数字化和可视化,打造数字化车间。通过实施MES系统,接收ERP系统的生产计划,根据订单的鞋型、尺码等信息,结合车间现场生产进度制定车间现场生产任务。并将加工制造要求下发到机器人打粗工作站、机器人喷胶工作站、机器人楦头装卸工作站和机器人喷脱模剂工作站进行生产。
建立工业互联网平台,实施设备联网和数据采集,通过对生产设备的状态和工艺参数进行实时采集,及时反应出具设备运行状态,并通过声光装置对设备进行监控和异常报警。MES系统与产品生产设备及检测设备进行集成,实现公司产品的精确追溯。
4、数据采集与机器互联
在生产过程中应用RFID识别系统进行生产过程数据(鞋型、尺码、产量、合格率左右脚等)的采集。将RFID芯片固定在鞋楦上,在生产线上对数据进行识别,并将相关数据传送给打粗机器人、喷胶机器人、连帮注射设备等生产设备,以便调用对应程序;同时根据不同鞋型、尺码,调节流水线速度等。基于对鞋楦的识别和联网,实现配码和混码生产,提高后段配码效率,减少人工操作。
据了解,该鞋企通过本项目建成智能化车间,项目实施完成后产品研制周期由50天缩短至30天,周期缩短40%,订单交付周期由90天缩短至55天,订单交付周期缩短35天,订单交付周期缩短39%。生产效率由60%提升至90%,产品不良率降低23%,企业运营成本降低25%,能源利用率提升12%。
对于制造企业而言,推动企业健康可持续发展是永远的命题,智能制造技术不断发展,新质生产力也会持续产生,相辅相成,源源不断推动行业滚滚向前。
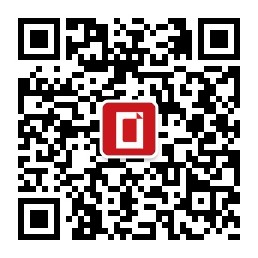