大幅提升加工效率
- 来源:国际金属加工商情 smarty:if $article.tag?>
- 关键字:加工,效率,数字化 smarty:/if?>
- 发布时间:2024-10-27 11:33
本文译自德国Werkstatt und Betrieb杂志
Voith集团旗下的涡轮器部门为全球客户提供智能化驱动技术、系统以及定制服务,其开发的未来型增压技术和数字化解决方案服务于石油、天然气、能源、采矿、工程机械、海运以及铁路等诸多领域。
位于德国慕尼黑附近的加兴工厂是Voith集团的重要生产基地之一,该工厂在15米长的生产线上加工GD-ALS 110铝合金材料的DIWA系列公交车变速器。安装在自动生产线控制计算器上方的XXL监控器可实时显示复杂公交车变速器壳体变型的全部加工过程。Voith公司数控加工程序员Steffen Seifert介绍:“对我们来讲,这里的全部加工过程意味着粗加工和包括达到最后加工尺寸要求的精加工在内的铣削、钻屑、倒角和攻丝加工——所有这些都在生产线上的3个夹具中完成。”这些任务由3台恒轮MC 20卧式加工中心完成,并配有清洗机构和机器人负责上下料及运输。
Seifert指出:“当然,最短的切削加工时间和始终如一的高加工质量最为重要;但切削加工过程的绝对可靠性也至关重要。随着科技的不断革新,行业内正积极寻找创新的切削解决方案,以进一步优化和完善现有的加工流程。在此过程中,数控编程人员特别指出:“刀具的选择至关重要。”作为CAM部门的一员,Seifert与其团队共同负责刀具管理,深知这一点。以最新研发的攻丝刀具为例,它便是一个显著提升生产效率的有力证明。
优势显著
Voith集团,作为刀具采购的多元化企业,长期以来与弗兰肯地区的刀具巨头Emuge-Franken保持着紧密的合作关系,尤其是在公交车变速箱壳体螺纹加工方面,Emuge的丝攻产品一直备受信赖。然而,一个名为Taptor的革新性螺纹加工技术,凭借其独特优势,深深吸引了Voith公司的目光。
Seifert回忆道,他敏锐地关注到Emuge-Franken公司与奥迪携手研发的Taptor技术,这项技术采用的特种刀具能在铝合金变速箱壳体上一次性完成M6螺纹底孔的钻孔与攻丝,彻底颠覆了传统分步加工的模式。这种创新不仅大幅缩短了换刀时间,更在螺纹质量上实现了质的飞跃。尤为重要的是,他注意到奥迪的测试案例与Voith集团的变速箱壳体螺纹加工高度相似,这立即激发了他探索Taptor技术应用于大规模生产的浓厚兴趣。
Seifert找到了Emuge Franken公司负责Garching工厂的销售代表Armin Kusch商谈Taptor技术的现场测试。Kusch也承诺将Taptor技术转移到公交车变速箱M6和M8螺纹的现场,进行实地验证。
将钻和丝攻的功能集成到一起
Emuge-Franken公司技术专家Thomas Funk介绍说道:“二合一专用刀具的进给速度就像丝攻一样,刀具每转一转的进给量相当于一个螺距。一旦达到所需的钻孔深度刀刃就会空切。到达孔底时也不会有不完整的螺纹了。这样,根据不同的螺纹直径螺孔底部只有一个螺距大小的尺寸没有螺纹。当专用刀具反向旋转时会退出螺纹孔。”这一螺纹加工技术即可用于盲孔也可用于通孔的螺纹加工。
根据Funk的说法,可靠地从螺纹底孔中排出铁屑也是非常重要的。因此,专用攻丝刀具横刃上的断屑槽可以确保加工的铁屑很短,并有着始终如一的相同形状。这里被称为断屑槽、分屑器的钻尖横刃有着很大的后角,这种大后角也有助于保持很小的轴向力。Funk强调说:“这就是为什么与整体硬质合金钻头相比在进给速度相同时产生的切削力要低得多。”
作为Taptor技术的早期参与者,Funk深知奥迪对新刀具的严苛要求,包括螺纹强度等。铸铝材料制造的发动机零件中常见的螺纹都在攻丝过程中形成了受“挤压”的表面——这对铝合金材料的零件强度来讲是一个有益无害的事情。Funk说:“这就是为什么我们也要通过测试专门测试一下Taptor螺纹加工技术加工的螺纹是否有着与常规螺纹攻丝工艺相同的强度等级。因此,我们在测试时设计了一个特殊的内螺纹 —— 一部分切削成形,另一部分挤压成形。”
最终,拉伸试验的优异成绩证明了Taptor螺纹加工技术及刀具完全胜任Voith集团公交车变速箱的螺纹加工需求。Funk自豪地补充:“值得一提的是,Taptor加工的螺纹还成功通过了DIN ISO 1502标准螺纹塞规的严格检测。”
螺纹加工NC数控程序
接下来,让我们聚焦于加兴生产基地的实际情况,特别是关于螺纹加工数控程序的编制。Funk,作为数控程序开发的负责人,详细介绍了Taptor技术在数控系统中的实现方式:“我们采用G331数控加工指令来控制Taptor技术,这一指令在西门子Sinumerik数控系统中尤为高效,它允许我们在不使用浮动夹头的情况下,顺利完成攻丝循环。发那科数控系统也提供了类似的解决方案,而对于其他数控系统,我们正积极与制造商协商,以确保兼容性的实现。”Funk先生强调,机床的动态性能和主轴的脉冲传感器对于确保螺纹加工同步性至关重要。为支持客户,Emuge公司还提供了Taptor加工循环所需的G代码应用示例,以简化集成过程。
然而,对于Voith集团而言,这一步骤并非必需。因为Voith集团的程序员Seifert本人就是一个数控技术专业人员,在得到Emuge-Franken公司提供的基础信息后他就在很短时间里完成了Taptor螺纹加工循环的控制程序。而且Voith集团使用的MC 20卧式加工中心本身配备的就是Sinumerik 840D数控系统。在数控加工循环的控制下,Taptor攻丝刀具可以直接完成螺纹全深的攻丝加工。Seifert说:“数控加工循环,这里最重要的是螺纹的螺距。当达到螺纹的规定攻深时恰好完成螺纹底孔的孔口倒角和螺尾空刀。”然后主轴反向旋转、并在同一加工循环的控制下控制着Taptor刀具退出螺纹孔。Seifert说:“重要的是,Taptor刀具加工时的起始位置必须与退出位置必须完全重合,否则螺纹就会乱扣。”
随着一切准备就绪,螺纹加工试验正式拉开序幕。攻丝时的切削速度为每分钟3000转。恒轮MC 20卧式加工中心的螺纹加工循环很容易实现这种转速的同步。“由于我们在当前测试阶段的Taptor技术时没有使用Speedsynchro速度同步器,因此直接将Taptor刀具系统装夹在整体式热缩刀柄中进行测试。”Seifert所说的Speedsxnchro速度同步器是一个具有长度补偿并集成有Emuge-Franken公司开发的“快速”补偿机构的刀具夹头。用了这一刀柄之后可以将电机主轴转速每分钟2000转时的同步速度提高大约4倍。Voith集团当时使用的快速补偿装置只适合用来加工变速箱壳体上M8的螺纹,并没有适用M6的快速补偿装置。
令人信服的冷却和排屑
Seifert说:润滑和冷却液是机械加工最重要的工艺参数之一。“通常,我们在加工中心里使用的都是过滤精度很高的冷却润滑液。”这也是Voith公司为3台MC 20卧式加工中心配备IDV Engineering过滤系统的原因。这种旁通式过滤器可以过滤掉大于10μm的碎屑和其他颗粒物。为微米级的冷却液过滤对内冷式的Taptor刀具系统是非常重要的。因为极为微小的颗粒物也会干扰螺旋状内冷通道中的冷却液流动。有了良好的冷却润滑之后就可以克服攻丝过程中切屑带来的许多问题,包括螺纹牙形的高温烧蚀。Seifert说:“高温烧蚀是Taptor技术中一个非常敏感的问题。因为我们这里的每转进给量就等于一个螺距。”
在Emuge-Franken公司的帮助下,尤其是在Kusch的帮助下测试的结果非常成功。Seifert说:“我们在第二次试验中就实现了最初制定的目标。之后的每次测试、试验都有新的收获。”这样,在Taptor技术的帮助下实现了在大批量生产条件下完成除盲孔螺纹之外变速箱壳体全部攻丝任务。
节省了两把刀
测试试验的结果令人振奋,Seifert详细报告了Taptor技术带来的显著效益。与传统的钻孔和攻丝技术相比,Taptor技术实现了时间节约上的两位数百分比提升,尽管尚未达到50%的目标,但这并非其主要追求。Taptor技术的真正价值在于其多方面的优化,其中减少刀具数量是一个重要方面。
在MC 20卧式加工中心的有限刀具库容下,每一把刀具的占用都显得尤为珍贵。Seifert指出,通过采用Taptor攻丝系统,他们不仅省去了钻孔步骤所需的刀具,还因无需再使用进给同步器而额外节省了另一把刀具的空间,总计赢得了两个宝贵的刀位。这两个刀位原本被进给同步器所占据,现在得以释放,用于容纳其他更为关键的刀具。
对于测试试验后的初步评估,Seifert表示,就当前生产线上的各种变速箱壳体加工而言,Taptor技术已经实现了大约5%的时间节约。他相信,随着设备操作人员的技能提升和工艺的不断优化,这一节约比例还将进一步增加。同时,少用两把刀具完全符合他们的预期,为生产线带来了更高的灵活性和效率。
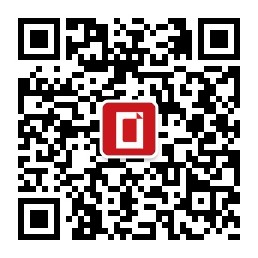