Cr32Ni7Mo3N特级双相不锈钢的空蚀行为
- 来源:不锈钢商圈 smarty:if $article.tag?>
- 关键字:双相不锈钢,空蚀,腐蚀,蒸馏水 smarty:/if?>
- 发布时间:2014-12-16 08:29
摘要:利用磁致伸缩空蚀试验机对Cr32Ni7Mo3N特级双相不锈钢在蒸馏水和人工海水中进行了空蚀实验,并采用扫描电镜跟踪观察了经不同时间段空蚀后试样的形貌。通过测量失重绘制了材料的累积失重量和失重率曲线。经电化学工作站测量了材料在静态与空蚀条件下的极化曲线和腐蚀电位变化。对比分析了Cr32Ni7Mo3N与SAF2205双相不锈钢在人工海水的抗空蚀能力。结果表明:Cr32Ni7Mo3N特级双相不锈钢空蚀破坏首先在铁素体薄弱区以及铁素体和奥氏体相界发生,并向铁素体内扩展,铁素体发生解离断裂脱落;奥氏体随着空蚀的进行,滑移线增多,显微硬度值增加,且人工海水中奥氏体显微硬度值比在蒸馏水中的高;铁素体大面积破坏后,奥氏体才失稳产生延性断裂脱落,奥氏体的存在延缓了破坏在整个材料表面上的扩展。空蚀与腐蚀交互影响导致材料在人工海水中加速破坏。Cr32Ni7Mo3N特级双相不锈钢在人工海水中的抗空蚀能力优于SAF2205双相不锈钢。
关键词:双相不锈钢;空蚀;腐蚀;蒸馏水;海水
空蚀是一种由于液体中空泡溃灭产生的瞬间力和热作用于材料表面所造成的材料表面损伤现象,它极易造成器件效率降低,甚至断裂失效。常见空蚀破坏形貌为针孔和麻点,严重时为海绵状、蜂窝状等。双相不锈钢(duplex stainless steel,简称DSS)具备极佳的力学性能和耐蚀性能,广泛应用于石油化工、船舶、桥梁建筑等行业,并用来制造成遭受空蚀作用的零部件,如过高液体流量用的管道、泵以及螺旋桨。按照耐点蚀能力划分,双相不锈钢可分为普通双相不锈钢(点蚀抗力当量值(pitting resistance equivalent number,PREN)<40,如SAF2205)、超级双相不锈钢(PREN>40,如SAF2507)以及特级双相不锈钢(hyper duplex stainless steel,HDSS,PREN>45)。目前,部分学者和科技人员已对双相不锈钢的空蚀行为进行了一定的研究,获得了有益的成果,值得借鉴。但是,对于特级双相不锈钢这类新型材料,国内的研究报道还不多见,而针对其抗空蚀性方面的研究几乎未见报道。基于此,本文开展了新型特级双相不锈钢抗空蚀行为的研究,并与SAF2205双相不锈钢进行了对比分析。
1 实验方法
利用316L不锈钢、金属铬、钼铁、电解镍、氮化合金等原材料,在35kW、8kg中频感应炉中熔炼,分别将熔炼好的合金注入不同的红热熔模模壳中,凝固冷却后获得Cr32Ni7Mo3N和SAF2205材料。通过直读光谱分析仪。Cr32Ni7Mo3N材料点蚀抗力当量值为52.1,属于特级双相不锈钢。Cr32Ni7Mo3N材料固溶处理工艺为:1200℃保温2h,水冷。SAF2205材料固溶处理工艺为:1050℃保温2h,水冷。
空蚀实验前后对试样进行超声波清洗和干燥后称重,并记录重量和空蚀时间。称重采用感量为0.1mg的分析天平。空蚀实验设备采用型号为KJ-1000的磁致伸缩式超声处理仪。将固溶处理后的Cr32Ni7Mo3N和SAF2205材料加工成表面积(即遭受空蚀的表面)为2cm2的圆柱形作为空蚀试样。第1次空蚀时,工作面用砂纸打磨并抛光至镜面。空蚀振动频率设为20kHz,峰-峰振幅为60μm,试样固定在距离变幅杆端面1mm处,变幅杆端面浸入介质的深度为15mm,介质温度控制在(25±2)℃。空蚀实验介质为蒸馏水和人工海水。空蚀后,试样表面显微硬度测量采用71型显微硬度计,形貌观察采用XL30-ESEM环境扫描电子显微镜。
空蚀电化学测量采用CHI650C电化学工作站。电化学测量采用三电极体系,参比电极为饱和甘汞电极,对电极为铂电极,工作电极用圆柱形的Cr32Ni7Mo3N制备,其表面积(空蚀面)为2cm2。工作电极工作面打磨抛光至镜面,非工作表面用环氧树脂涂覆。空蚀条件下进行电化学测量时,空蚀频率、振幅的设定以及工作电极的固定方法同空蚀失重测量实验方法一致。磁致伸缩式超声处理仪以及电化学测试系统如图1所示。
2 实验结果与分析
2.1 失重及形貌分析
对在两种介质中经不同时段空蚀后的Cr32Ni7Mo3N试样进行了称重,其累积失重量和失重率曲线如图所示。可知,前4h材料累积失重量增加并不明显,其失重率极低。在人工海水介质中,随着空蚀时间延长,材料空蚀失重量和失重率都呈增长的趋势,14h后材料失重率达到最大值0.23mg·h-1。在蒸馏水介质中,也有着同样的规律,但试样空蚀20h时失重率才达到最大值0.145mg·h-1,具有明显的滞后期,而且其值约为前者的2/3;此后,材料空蚀失重率下降,累积失重量增加速度变缓。人工海水中试样空蚀39h后,试样失重率到达稳定期,材料累积失重量曲线出现平台区。空蚀84h后材料在蒸馏水和人工海水介质中空蚀累积失重量分别为4.5和6.9mg。显然,在人工海水介质中材料空蚀破坏程度要大于蒸馏水中的试样。
累积失重量和失重率曲线反映了材料在空蚀破坏过程中导致表面材料脱落造成的质量损失情况,但无法明确其破坏机理。为了探究材料在海水环境工况下的空蚀破坏行为和机理,采用扫描电镜跟踪观察了不同时间段空蚀后材料的变形损伤以及断裂形貌。
试样在人工海水介质中空蚀4h后扫描电镜照片。空泡溃灭作用力超过了材料抗冲击强度极值,发生破裂,形成空蚀微孔。放大视场观察,空蚀微孔主要分布在铁素体相(α)内和相界(α/γ)处,而在奥氏体相(γ)上有诸多滑移线。因此,空蚀初期材料失重主要来源于铁素体相。
试样在人工海水介质中空蚀14h后的扫描电镜照片。可知,部分奥氏体周边的铁素体发生剥离,呈现岛状,而奥氏体相表面滑移线变得更多更明显。进一步进行观察与分析,铁素体上有大量的小片状脆性剥落痕迹,而且材料脱落后断面形貌有解离台阶、相互平行的解离面以及穿过多晶粒的河流花样。因此,铁素体在空泡溃灭作用力下发生解离断裂脱落,属典型的脆性失效。空蚀14h,铁素体大面积破坏而奥氏体相表面却形成大量滑移线,说明奥氏体比铁素体耐空蚀。奥氏体相是面心立方结构,铁素体相是体心立方结构,结构的差异将决定这两相对空泡溃灭冲击载荷反应机制差异。与面心立方结构奥氏体相相比,体心立方结构的铁素体相有特定的解离面,解理面处表面能最小,较易分裂,因而铁素体相对空泡溃灭冲击载荷的耗散能力就弱。又因奥氏体面心立方结构的主滑移面滑移和面心立方结构对应变率敏感,容纳应变的空间大,耗散空泡溃灭所产生的冲击载荷能力大,导致其抗破坏能力比铁素体强。对在蒸馏水和人工海水中经不同时段空蚀后试样表面的奥氏体相进行了显微硬度测试。可以发现随着空蚀时间的延长,奥氏体相显微硬度值越来越大,而且在人工海水中,试样硬度提高的值比蒸馏水中要略大。这说明奥氏体内滑移的产生,导致其发生加工硬化现象,从而提高了奥氏体的耐空蚀性能。在人工海水中,由于有盐类的存在,具有更大的密度,当空泡破裂时,造成的冲击力增大,使得奥氏体产生更多的滑移线,导致硬度略有提高。总之,奥氏体的存在会延缓空蚀破坏在整个材料表面的扩展,最终提高材料整体耐空蚀能力。
由前面的分析可知,初期空蚀破坏只形成微孔,后期既有铁素体小片剥落,又有大面积铁素体破坏,然而与铁素体接触的奥氏体周边只有少量破坏痕迹,因此可以认为这个时段内的受损过程为:当材料受到空泡破裂产生强大冲击力作用时,在铁素体薄弱区域以及铁素体和奥氏体接触处于高能量的相界首先发生破裂,然后向铁素体内扩展。扩展到一定程度时,出现小的剥离片,但同时又会产生新的小微孔。如此反复,最终导致铁素体大面积破坏。
试样在人工海水介质中空蚀39h后扫描电镜照片。岛状奥氏体周边铁素体脱落区增大增深,形成了大片空穴。进行分析:此阶段由于材料表面有大量空穴的形成,缓冲了空泡溃灭载荷,起到“水垫”作用,因而此阶段空蚀失重量和失重率降低。但此时,空蚀已造成奥氏体发生破裂剥落。可以观察到,奥氏体部分区域有深坑,底部还有大的裂纹,显然是整块奥氏体从基体上发生了脱落。奥氏体虽然未脱落,但空泡溃灭冲击力已经使其表面产生了裂纹,而破坏的B区域则出现了韧窝和撕裂岭,这是典型的韧性断裂。因此,可以认为奥氏体的失效,一方面由于奥氏体缺少了附近基体的“支撑”,强度减弱,另一方面产生的应力集中,促使裂纹在奥氏体根部的扩展和连接,导致奥氏体失稳产生断裂脱落。
试样在蒸馏水和人工海水中空蚀84h后扫描电镜照片。蒸馏水中试样表层材料均已脱落,分辨不出两相组织,且断口处有明显的疲劳断裂辉纹。人工海水中试样表层材料不仅完全脱落,形成了许多细小的蜂窝状空蚀坑,表面呈现诸多裂纹,且蜂窝状空蚀坑和裂纹向材料基体内纵向延伸。因而,人工海水试样破坏程度比蒸馏水中严重。进行分析知:空蚀累积曲线进入平台区域后,此阶段材料失重以裂纹扩展连接导致材料脱落和疲劳断裂脱落为主,材料空蚀破坏形貌呈蜂窝状。
2.2 空蚀与腐蚀的交互
静态和空蚀条件下试样的极化曲线。由塔菲尔直线外推法得到静态和空蚀条件下腐蚀电流密度分别为0.89和39.16μA·cm-2,空蚀使材料的电化学腐蚀速率增大了44倍。
显然在腐蚀介质中,空蚀与腐蚀互为影响,导致材料失效率增大。这是由于一方面振幅杆的振动以及空泡形成和溃灭产生搅拌作用,加快了材料表面、表面--介质附近离子和分子的传输,同时也增强了离子、分子与材料表面的电子交换,加速了对材料的腐蚀;另一方面,奥氏体在空蚀冲击载荷作用下表面塑性变形产生位错、滑移等,在腐蚀溶解作用下,位错、滑移等移动阻力下降,材料表面出现应力松弛,弱化了表面材料结合力,使奥氏体抵抗空泡溃灭载荷能力减弱,同时腐蚀溶解使得铁素体表面硬度降低,抗冲击能力减弱,最终降低了材料抗空蚀的能力。
因此,空蚀的搅拌作用加速了材料表面及其附近腐蚀介质的电子传质过程,从而导致自腐蚀电位负移、腐蚀电流密度增大;腐蚀降低材料表面力学性能,使材料空蚀破坏加速,两者交互影响导致材料加速失效破坏。
2.3 两种材料抗空蚀性对比分析
前面对Cr32Ni7Mo3N钢的空蚀累积失重量和失重率曲线、空蚀发展过程以及空蚀与腐蚀的相互关系进行了研究和分析,但还无法直接判断这种材料的抗空蚀能力的优劣。基于此,选取了SAF2205钢作为对比材料,也在人工海水中进行相同的空蚀实验。SAF2205钢在人工海水中空蚀5h时就达到最大失重率7.3mg·h-1,其最大失重率是Cr32Ni7Mo3N的31.7倍,而且SAF2205钢达到最大失重率耗时明显比Cr32Ni7Mo3N钢的短。SAF2205钢空蚀24h后的累积失重量是53.3mg,Cr32Ni7Mo3N钢空蚀84h后的累积失重量只有6.9mg。显然,SAF2205钢空蚀耗时不到Cr32Ni7Mo3N钢的1/3,空蚀所导致的质量损失量却是Cr32Ni7Mo3N的7倍多。采用扫描电镜跟踪观察了SAF2205钢在人工海水中空蚀不同时间后试样表面形貌。SAF2205材料空蚀破坏表面形貌变化与Cr32Ni7Mo3N钢相似,空蚀破坏都是先在铁素体相(α)和相界(α/γ)发生,然后在铁素体相上扩展,SAF2205钢在人工海水中空蚀5h铁素体发生大面积破坏,而Cr32Ni7Mo3N钢中铁素体大面积破坏需要空蚀14h;随着空蚀的进一步进行,奥氏体开始大面积破坏直至试样表面材料完全脱落形成蜂窝状空蚀破坏形貌。与SAF2205材料空蚀24h的表面形貌相比,Cr32Ni7Mo3N钢空蚀84h后表面才形成细小蜂窝状空蚀坑。因此,无论从材料的失重量,还是形貌破坏程度,都说明Cr32Ni7Mo3N钢比SAF2205钢具有更优的抗空蚀能力。
3 结论
(1)空蚀时,Cr32Ni7Mo3N钢破裂首先发生在铁素体薄弱区域以及铁素体和奥氏体接触处于高能量的相界,然后向铁素体内扩展,铁素体发生解离断裂脱落;奥氏体因滑移产生加工硬化延缓了破坏在整个材料表面上的扩展;铁素体大面积破坏后,奥氏体失稳产生断裂脱落。
(2)空蚀与腐蚀交互影响导致Cr32Ni7Mo3N钢在人工海水中加速破坏;但在人工海水中,材料经空蚀后,其奥氏体硬度值比在蒸馏水中略有提高;Cr32Ni7Mo3N钢在人工海水中的抗空蚀能力优于SAF2205。
文/何福善,向红亮,顾兴,刘东
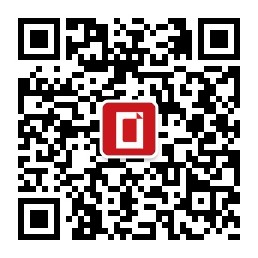