复合材料打造高性能的车顶连接支架
- 来源:国际复材技术商情 smarty:if $article.tag?>
- 关键字:复合材料,高性能,支架 smarty:/if?>
- 发布时间:2023-09-03 11:20
几十年的经验和传统智慧告诉我们,纤维增强越长,所得到的复合材料的机械性能越高。虽然纳米复合材料添加剂的引入在某种程度上挑战了这一断言,但设计用于注塑成型的超短(但不是纳米级)碳纤维(USCF)增强热塑性塑料(CFRTP)系列已被证明始终优于短纤维和长纤维(玻璃或碳)热塑性塑料。在复杂的几何形状中尤其如此,因为在精细的零件细节中很难实现良好的纤维穿透。事实上,这些化合物被称为KyronMax,可从三菱化学先进材料公司(MitsubishiChemical Advanced Materials,MCAM)获得。不仅优于传统的热塑性复合材料,而且还优于金属。这方面的一个很好的例子是一系列的车顶结构控制/ 支架,用于固定2021 吉普牧马人运动型多用途车(SUV)和Gladiator皮卡的可拆卸软顶或硬顶。
KyronMAX 产品线基于结构性化合物制成,而此种化合物是利用注射成型工艺制成的、全球最强大的化合物之一。KyronMAX 化合物可用于取代结构性部件中的钢。由于不断创新和研发其广泛的产品系列,MCAM 打破了行业壁垒,其提供的材料的抗拉强度达60,000 psi(414 MPa)。
金属置换应用,特别是汽车零部件领域的金属置换应用已经成为OEM 轻量化与可持续性项目的一部分。该公司表示:“我们对利用KyronMAX 化合物取代金属所能实现的节约进行了研究,发现当开始减轻材料的重量时,可以大幅降低二氧化碳排放,因为不再需要太多的燃料来驱动汽车。”此外,KyronMAX 技术能够利用注射成型工艺制成非常复杂的零部件,并且保留金属部件的强度和机械性能以及其他好处。
对航空航天来说足够强,对汽车来说足够快
KyronMax 化合物最初是为航空航天开发的,后来扩展到高性能体育用品应用,其中高温热塑性基质是一个优势,在复杂的几何形状中实现高纤维渗透的能力对于满足低重量苛刻的机械要求至关重要。毫不奇怪,这些材料在汽车行业引起了人们的兴趣,因为注塑成型工艺非常适合满足该行业的高产量、高可重复性和可再现性(R&R)要求以及极具竞争力的成本目标。
设计结果
● 提供与压铸钢相当的机械性能,重量降低79%,成本降低38%。
● 满足之后的兼容性(服务/ 售后更换)的钢材美观要求,同时采用耐候、彩色模压配方改善划痕和损坏,无需打磨和粉末涂层。
● 从离岸进口的金属部件转向近距离运输的复合部件,与基准钢材相比,缩短了供应链,减少了制造和使用寿命的碳足迹。
复合支架的开发始于一次会议,会议讨论了MCAM 在其产品组合中可能对当时的菲亚特克莱斯勒汽车公司(FCA,现为Stellantis)创新小组有用的新材料。经过对KyronMax 产品线的讨论,以及对几种具有不同基体和纤维重量分数(fwf)的产品的数据表的审查,FCA 的多个应用工程团队在不同的车辆上进行了展示和讨论,FCA 的创新小组决定进一步探索这些材料,并开始寻找可以评估化合物性能的应用。
吉普车顶支架最初是采用熔模压铸钢生产的,被认为是一个不错的选择,因为这些部件是结构性的,尺寸适中,但具有复杂的几何形状,这对实现良好的纤维穿透非常重要。此外,考虑到它们位于车顶顶部,如果能够显著减轻重量,那么将有助于降低车辆的重心(COG),这将改善用于崎岖地形越野的车辆的操控性和稳定性。然而,另一个考虑因素是钢制支架是由一家离岸供应商生产的。
设计的机会
正如最初为2018-2021 年吉普牧马人和Gladiator 设计的那样,有三种类型的钢制连接支架,尺寸大致相同,但几何形状不同,每种都有左侧和右侧版本:有两个外板和两个内板,都安装在前车顶交叉构件上,对于JeepFreedom Panel 硬顶,用板材成型复合材料(SMC)成型,两个额外的后连接支架安装在后车顶交叉构件上。
带有软顶的车辆仅使用前外置连接支架,而SMC 自由面板硬顶使用所有六个连接支架。钢件采用粉末涂层,具有耐腐蚀、防紫外线和美观性。在使用中,支架永久安装在车辆上;面板可以通过启动释放手柄来拆卸,并且可以在重新接合手柄后重新安装。
吉普工程团队确定了每种型号连接支架在使用中的一系列关键载荷:舷外的X、Y和Z载荷,舷内和后部的Z载荷,以及舷内和舷外的非对称载荷。为了通过CPN(克莱斯勒零件号)的完整电池验证测试,CFRTP 连接支架需要通过与钢制连接支架相同的测试,包括湿/ 热和干/ 冷操作条件下的加速老化、评估噪音/ 振动的振动测试。振动/ 声振粗糙度(NVH)、颜色匹配和连接支架必须表现出出色的尺寸稳定性/ 零弯曲蠕变,以确保良好的车顶板密封。此外,不允许更改包装或装配线;复合材料连接支架必须在相同的封装空间中提供类似钢的性能,并以相同的方式组装到车辆上。
另一个要求是复合连接支架需要在视觉上与基准钢组件相匹配,以确保之后的兼容服务/ 售后更换。因此,候选材料需要满足苛刻的机械要求,重量轻,提供A 级耐候性表面,并满足OEM 的成本目标。
由吉普、MCAM 和工具制造商Maple Mold Technologies 组成的合作团队开始研究复合连接支架的潜在设计。在针对各种连接支架的五套初始设计中,有两套进行了原型设计和测试,其中包括Maple Mold 生产的四套原型工具。舷外原型工具可以注入多种设计进行测试。比较保守的两种舷外设计在复合材料中有金属插入,而另一种没有。连接支架的设计进行了轻微的修改,以提供防错漏功能,因此在装配线上不会出现左侧和右侧的装配错误。
在材料选择中,对实验设计(DOE)进行了重要的考虑。初步评估了26 种金属和复合材料选择,其中超过15种是高温聚酰胺(PA)选择,要么是聚酞胺(PPA),要么是PA9T。这两个系列的特点是具有高耐热性、耐化学性、耐湿性和耐磨性,同时具有出色的尺寸稳定性和成型性。对于每个基体,评估了许多FWF和纤维类型和长度选项,包括USCF、短玻璃、长玻璃和长碳纤维。在两套设计中,几种不同的聚合物/ 纤维选择从虚拟原型发展到物理原型。最后两种复合材料/ 设计组合在启动前四个月进入车辆验证测试阶段。
所有性能都以更小的质量实现
综合物理测试性能最好的复合配方是KyronMax S-4330,这是专门为该应用开发的新等级。该化合物是30%的USCF/PPA。有趣的是,全复合材料车顶连接支架的机械性能实际上优于带有金属嵌套的版本。此外,30% 的USCF/PPA 在关键指标上也优于50%的短玻璃和40% 的长碳纤维PPA。与短纤维或长纤维热塑性塑料相比,KyronMax 化合物据说可以像纯树脂一样成型,并具有各向同性(像金属一样)。
尽管严格的注射成型工艺,纤维长度据说是保留,而不是进一步减少。在生产工具上带有直接阀口的热流道可以最大限度地减少阀口残留。此外,USCF 化合物以较低的残余应力/ 内应力退出模具,从而提供更好的针线/ 焊缝强度,减少翘曲以获得更高的尺寸精度和更好的美观性。
注射成型复合材料提供了相当的零件强度,质量降低了79%(对于六个连接支架/硬顶版本),成本降低了38%,同时满足或超过了Stellantis 对负载偏转、扭矩和白车身扭矩保持的所有性能要求,确保了关闭密封的完整性。
此外,通过耐候性的彩色模具(MIC)配方,可以改善划痕和损伤,该配方与基准钢材美学相匹配,并在客户可见的表面上选择纹理。抛光和粉末涂层等精加工步骤被取消。
从进口的金属部件转向复合部件,缩短了供应链,减少了长距离运输相对较重的部件的能源需求。因此,与基准钢部件相比,复合材料连接支架的制造和使用碳足迹更低(每年减少1137 吨二氧化碳),有助于支持可持续发展目标。该应用被认为是第一个大批量结构CFRTP MIC 和耐候性车身应用。
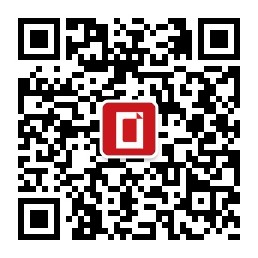