连续纤维3D 打印在航空领域的应用
- 来源:国际复材技术商情 smarty:if $article.tag?>
- 关键字:纤维,3D打印,航空领域 smarty:/if?>
- 发布时间:2023-09-03 11:30
自美国于2014 年推出首台连续纤维3D 打印机以来,该技术正在快速发展并在航空领域取得应用。随着技术的逐渐成熟和大规模推广应用,该技术或将颠覆现有复合材料无人机、低成本复合材料航空结构的生产模式。
连续纤维3D打印的技术优势
连续纤维3D 打印技术综合利用工业机器人、3D 打印末端执行器、原位检测、智能监测与机器学习等技术,快速输送、沉积连续纤维增强体,以及基体树脂并原位浸渍、固化,与传统的自动铺丝成形以及熔融沉积成形等工艺相比,自动化程度和柔性更高,对于典型的碳纤维/聚醚醚酮零件,研发周期可缩短至原来的1/30,生产速度可提高100 倍。
增材制造(AM)为现代制造商提供了一种最简单的生产方式,利用复合材料制造终端零件,缩短交货周期,加快原型工具生产时间。使用高性能热塑性塑料打印的零件,可满足飞机内饰许多部件的火焰、烟雾和毒性(FST)要求,配合3D 打印机制造商Markforged 专有的连续纤维增强打印技术,可生产高强度,耐热,以及更高物理性能的零件。
连续纤维3D 打印机可以由多机器人组成柔性单元,机器人上还可添加多个3D 打印末端执行器,同时打印头可支持碳纤维、凯夫拉、玻璃纤维甚至光纤和金属丝等材料,使该技术既可以用于大批量生产复合材料零件,也可以一次性打印高度复杂的几何形状或者需要极其精密制造的关键零件。
连续纤维复合材料的优势
在一个受到严格监管的行业中竞争,OEM、MRO 服务提供商、商业航空公司和其他行业玩家必须优先考虑安全和性能,并且严格遵守监管指导方针,不断发现提高业务效率的方法。
随着材料学的发展,金属已经不再是我们的唯一选择,有大量的非金属材料因为特殊的性能而被应用到航空发动机中,如陶瓷材料和碳纤维。陶瓷因为其极佳的耐高温性能从而在航空发动机高温部件中得到使用;碳纤维则以优秀的比强度、比模量等综合指标被航空航天工业青睐,它可以被用来制造火箭的燃料储藏罐,也可以用来制造飞机的外壳。
随着时间的推移,传统上由铝合金制成的飞机部件越来越多地被复合材料取代,尤其是现在先进民用客机制造中,复合材料的使用比例已经超过了50%。
在高强度和低重量的基础上,航空航天应用的材料必须具有耐腐蚀性,并能够可持续地承受大范围的工作温度。金属材料或者铝合金在几百度的高温以后,它的力学性质就发生了很大程度的降低,而复合材料在经受了同样的高温以后,其机械性能下降相对要低很多。此外,碳纤维这种材料抗拉强度极高,想要拉断高强度碳纤维材料需要用拉断同样横截面积钢铁的力的两到四倍。其他航空航天材料如Onyx FR-A、碳纤维FR-A 和ULTEM ™ 9085(可在FX20 上打印)可以承受大多数航空航天应用中的工作温度。
航空航天工业受到严格监管,所有飞机部件和材料必须得到批准来自相关监管机构的认证,比如联邦政府航空管理局(FAA)或欧洲航空局、安全局(EASA)。航空航天制造商必须证明他们的部件和材料符合联邦航空局的一系列综合要求测试标准,如强度、耐久性、紫外线、流体灵敏度、振动、可追溯性和火焰、烟雾以及毒性(FST)。通过选择符合测试要求的材料,航空航天制造商才可以进行下一步操作。否则,制造商将不得不重复漫长的资格认证,重新回到起点。
为什么航空航天使用3D打印?
随着3D 打印部件作为飞机部件飞行,必须最大限度地减少部件的重量,这可以提高燃油效率,同时最大限度地减少二氧化碳排放。复合材料高强度、低密度、轻量化,它在高强度的同时又保持了非常低的重量。以碳纤维为例,碳纤维的密度一般在1400~2000kg 每立方米,经过环氧树脂强化的碳纤维密度也不过1600kg 每立方米而已,远远好于金属材料。
然而,低重量不能以牺牲部件强度或材料性能为代价,每个制造部件必须满足严格的安全和可靠性要求。3D打印碳纤维增强部件,可以生产出与6061-T6 铝强度相同的部件,同时与具有同等强度的金属部件相比,可以显著减轻重量。
在高强度和低重量的基础上,用于航空航天应用的材料必须耐腐蚀,并能够持续承受大范围的工作温度。适用于航空航天的材料,如OnyxFR-A、碳纤维FR-A 和ULTEM ™ 9085 等。
复合材料还具有良好的耐冲击性和抗疲劳性,作为成型件有很高的安全性。一个件在反复受力很千/ 万次以后,还能够保持强度。
此外,复合材料的可设计性强。因为复合材料具有各项异性,那么它的各项一直沿着纤维的方向,其强度尤其高,我们可以根据其纤维方向,结合使用场景的受力方向,把它作为一个更针对性的设计。
同时,相比于传统制造技术,AM带来了更高的成本效率、交货时间短、更快优化设计,让用户可以在需要时在需要的位置快速打印正确的零件,提供分布式制造操作。
增材制造非常适合满足航空航天领域对小批量、定制化零件的生产需求,让这些零件在需要的时候,以优越的价格,利用3D 打印技术将他们按需生产出来。更大的打印尺寸使航空航天制造商能够将多个小部件组装成单个部件,减少装配次数、零件计数,更大的减少误差。
借助支持云的分布式制造模式,可以在需要时在需要的位置快速打印正确的零件,而不是将零件生产好之后,再通过物流运输。借助3D 打印软件,存储在基于云的数字库存中,这样零件就可以发送到网络内的任何3D 打印机上打印,只需一个CAD 文件,制造商就可以在内部完成零件的制作,使他们的供应链比以前更紧密、更高效。这种能力也可以避免制造商囤积大量库存,实现准时制 (JIT) 的精益制造模式进行有效运营生产。
当供应链中断导致制造所需的工具和零部件短缺时,生产可能会停滞数周时间。一个零件的丢失可能会导致制造过程完全停止,无论购买新零件需要多长时间。使用AM 技术可以帮助其控制其供应链,降低制造风险和复杂性。通过引入3D 打印平台,可以让制造企业绕过许多风险,同时还可以使其供应链比以前更紧密、更高效,加快交付时间和研发速度。
增材制造在航空航天领域的应用现状
● 空客的复合材料机舱支架
基于种种优势,空客多年来一直在飞机设计和制造过程中采用3D 打印技术。多年过去,3D 打印工艺和材料科学获得了进一步发展,“轻量化”和“仿生学”也指向了一个新的趋势。空客正在研究3D 打印复合材料支架制造代替钛合金的可能性。
先进制造商Arris Composites 与空客公司合作了一项研究,该项目专注于机舱支架的生产,并希望通过利用创新的制造方法和材料(包括复合材料)来实现航空碳排放量的显著减少。据Arris 称,将220 克的金属支架进行拓扑优化后采用连续纤维复合材料3D 打印可以使零件重量减轻75% 到50 克。由于每架飞机会配备500 个这种支架,如果一年会制造100架飞机,50000 个轻量化的支架在整个生命周期中会节省1.13亿吨的燃油,并减少3.57亿吨的CO2 排放。
Arris Composites 公司开发了一种称为Additive Molding 的技术,通过在热塑性树脂中精确排列连续纤维,获得了具有无与伦比机械性能的下一代复合材料及成熟的大批量成型方法,这些产品具有高度集成性,所制造的产品比金属更坚固、更轻。
Arris Composites 表示,金属替代的新时代已经到来,机加工、3D 打印、金属铸造、金属注射成型和金属包覆成型的产品可以被卓越的复合设计替代。连续纤维+ 热塑性塑料复合制造实现了高强度和轻量化零件的批量生产,通过这种新工艺,可以以与塑料成型产品相同的速度生产高级碳纤维材料,而碳纤维零部件替换钛材料,可使重量减轻78%。
● 低成本复合材料结构的大批量生产
美国阿瑞沃公司开发了可将热塑性预浸丝束打印成零件的直接能量沉积(DED)工艺,空客资本公司参与了对该公司的投资。DED 工作单元由工业机器人、激光加热打印头和旋转构建平台组成,与传统3D 打印相比,能够将生产速度提高100倍。除无人机机身、机翼等航空零件外,阿瑞沃公司还生产与无人机框架结构类似的自行车车架,连续纤维3D 打印技术使其开发周期从18 个月缩短到了18 天。
该公司于2019 年2 月投入使用的新工厂拥有8 个机器人工作单元,可完成包括打印本身、后处理(例如钻孔)以及用于喷涂的预打磨,每天共可生产8 个大型零件。该公司正在测试每台机器人运行多个打印头以及每个工作单元运行多个机器人,以将生产速度再提高3 倍。为了在整个提速过程中保持质量和可重复性,该公司采用了原位检测和机器学习技术,为打印头配装多个传感器(测量高度、压力、变形等),系统软件使用这些传感器数据,根据需要实时调整工艺参数。这样,当工作单元需要更快运行时,就可以确保沉积速率、加热、固化和其他参数得到最优匹配。
● 碳/碳复合材料3D打印技术的重大进展
国外航空航天和国防生产商诺斯罗普·格鲁曼(Northrop Grumman)集团公司报告称,已经在碳/ 碳复合材料3D 打印技术层面获得了重大进展。该加工工艺使该企业可以大批量生产连续纤维增材复合材料,据悉这一点在增材行业是“前所未有的”。
碳/ 碳复合材料因为独特的特性,已广泛用于航空航天、汽车产业、医药学等行业,如冲压发动机喷嘴以及喉衬、航天飞船的端头帽和飞机翼外缘热防御系统、飞机场刹车片等。
诺斯罗普• 格鲁曼武器装备企业副总裁兼经理Dan Olson 说:“我们正开辟一种迅速、免工具的使用加工工艺,用以生产制造航空公司级连续纤维集成化复合结构,制造业这类发展将比普通的方式更有效地为战争产生水平,以确保我们自己的军队,有着前沿技术和高科技武器,来面对目前和未来武装力量威协。”
该工作组研发的技术性,被称作可扩展性复合型增材(SCRAM)。这是名副其实的六轴连续纤维工业生产3D打印机器设备,致力于生产制造集成化复合结构而设置的。随后,这种构造通过特有的加工工艺并转化成碳/ 碳结构,为满足要求繁杂、近净样子耐腐蚀材料的设计定位。因而,该企业需要这种繁杂的耐高温样子来制作高超音速和其他快速武器装备。
● 修复飞机的主旋翼叶片
Bell(贝尔直升机)和IngersollMachine Tools 利用 MasterPrint 大幅面3D 打印机,成功制造出一个长达22英尺长的复合基修复工具,以及修整飞机主旋翼组件的合作细节。
这个项目实际上是在2019 年完成的,但由于涉及商业机密和先进航空零件制造的保密条例,直到去年才得以公开。该项目使用位于美国罗克福德Ingersoll 总部的混合大幅面MasterPrint3X 龙门式3D 打印机和5轴铣床协作完成。
通过使用1150 磅ABS 材料和20% 的短切碳纤维填充物,3D 打印了转子叶片复合基修整工具。在连续75小时的运行中,打印过程作为一个单独的部分完成。打印后,通过将打印模块更换可在MasterPrint 机器上使用的5 轴铣头继续工作,最终将模具表面和工具位置加工成最终尺寸。后续加工在一周内完成,最终零件实现了可完全真空密封。最后,Ingersoll 机器利用siemens Sinmerik One CNC 系统来控制加工和3D 打印。
通过3D 打印制造和高效的5 轴加工操作,实现大幅度缩减时间成本。3D 打印和减材工艺以原生CAD 软件格式无缝协同设计。但如果使用传统工艺,以铝制模具为例,通常构建周期为4 到5 个月。而这种制造过程仅在几周内完成。“多年来,贝尔一直使用复合材料制造机身部件,利用这种快速制造技术,贝尔将大大加快组织内部开发工具的速度。”贝尔工艺稳定性高级经理James Cordell 说。
● 其他进展
著名的3D 打印机公司EOS 曾与工程设计软件专家Hyperganic 合作,以提高3D 打印航空航天部件的外观和功能。作为合作的一部分,这两家企业旨在将基于人工智能的算法工程软件Hyperganic Core 与EOS 的激光粉末床熔融3D 打印机相结合。随着该软件的出现,EOS 的客户在设计他们的空间推进部件时可以完全排除传统的部件设计程序,同时利用算法模型。这一变化预计将极大地简化设计工作流程,在几分钟内就能计算出性能更强的零件几何形状。
此外,3D 打印机生产商Stratasys公司和通用电气航空业务部的AvioAero 公司宣布了一些举措,这些举措可能会使他们各自的技术在新的航空应用中得到部署。随着Antero840CN03 聚合物在猎户座航天器上的使用资格数据的公布,Stratasys 公司打算鼓励建立一个模型,将该材料应用于类似的情况。另一方面,空中客车公司选择了Avio Aero 公司的Catalyst 发动机为其“Eurodrone ”提供动力,这是一种无人驾驶航空器,旨在执行欧洲的监测任务。
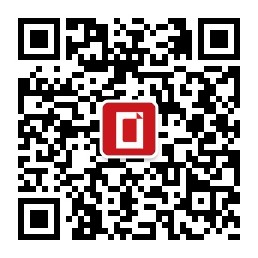