探索家电制造行业数字化转型
- 来源:智能制造纵横 smarty:if $article.tag?>
- 关键字:探索,家电,制造 smarty:/if?>
- 发布时间:2024-02-21 15:37
文/ 张瑾
谈起中国彩电发展史,创维一定是耳熟能详的名字。这家成立于1988年的企业是“中国制造2025”首批示范单位,连续多年位列中国电子百强企业前列,名列“2023中国企业500强”第425位。
在本期内容中,我们邀请到深圳创维-RGB电子有限公司制造总部智能设备部副主任工程师袁杰,分享创维彩电数字化转型的实践经验。
数字化转型历程
深圳创维-RGB电子有限公司是创维集团旗下最大的电子产业公司,生产经营彩色电视机、监视器、显示器、通讯器件等多种电子硬件设备,多年来始终坚持以大屏为中心,为消费者提供一整套智慧生活整体解决方案,并通过5G+8K的技术赋能,为家庭场景带来极致的娱乐体验。
作为一家传统制造企业,创维并不缺乏与时俱进的能力。据袁杰介绍,创维早在2012年就提出了机器人战略,一直以来坚持务实创新,并高度契合“中国制造2025”国家发展战略,承担起国家首批智能制造试点示范单位的重要任务,系统布局彩电智能制造自动化、信息化,形成了以示范推广、高效实用、持续升级为核心原则的智能制造实施策略,并获批国家首批智能制造试点示范企业,承担了工信部2015和2016年的智能制造专项;之后至2018年,创维围绕提质、降本、增效三大目标,高质量精细化发展,并获批组建了深圳市彩电智能制造工程技术研究中心;2021年创维入选工信部5G+工业互联网重点行业典型案例,公司“5G+8K赋能柔性智能工厂引领家电行业数字化转型”项目获得2021年“绽放杯”5G应用征集大赛工业互联网专题赛道一等奖和总决赛全国二等奖。
在传统家电制造行业,产品迭代快、品种多,对柔性化生产要求高;各生产基地、线体设备和人员水平存在差异,人工质检效率低;小订单高频转机生产模式下,物料分拣人员疲于应对,生产现场配送环境复杂;SMT贴片料用量大、体积小、种类多、难区分,包装相似,人工找料慢,易出错;人才培养周期长,高精尖设备运维难度大等是普遍存在的问题,因此,该类型企业进行智能化转型升级也面临一定的困难。
在袁杰的分享中,创维彩电制造的转型过程经历了自动化、信息化、智能化三个阶段。
在自动化阶段,公司首先从工艺角度进行改进,然后延伸开来覆盖整个生产阶段。利用机器人来进行自动化生产,包括自动点胶、自动保压、自动喷胶、自动翻屏、自动模组屏贴合、自动立机、自动贴码、自动高压、自动装箱、自动码垛等,根据彩电制造的工艺流程进行自动化的整体实施。
在信息化阶段,聚焦生产管理系统(MES)、企业资源计划(ERP)和仓库管理系统(WMS),同时集成设备管理系统(EMS)、质量管理系统(QMS)、计划排产系统(APS)、工艺管理系统(PMS)、能源管理系统(FMCS)、工厂可视平台(BI)以及移动办公系统(OA)等智能应用服务,达成更多关键数据采集和系统连通全流程覆盖,实现从接单到出货全工序信息化的建设。
据了解,创维彩电制造环节40+条SMT(表面安装技术)产线,20+条DIP(双列直插式封装技术)产线,以及40+条模组整机已全面覆盖MES系统。在仓储物流环节,其仓储面积达30W+m²,有94+种业务流程,包括进出口料、海关、保税、代工、内/外销等,场景非常复杂。通过信息系统的贯通,实现原材料、半成品、成品收料、发料、盘点、质检及库内的系统化管控,并结合料件管控要求实现对料件的批次、先进先出、库龄、超期复检等精细化管理。
在智能化阶段,落地5G应用场景,结合智慧园区打造5G+融合网络支持柔性生产、5G+AI车间眼智能视觉检测、5G+8K+VR/AR智能远程运维、5G+智能物流、5G+灯光拣选电子仓储、5G+能源管理等创新应用。
应用场景落地
创维彩电在数字化转型过程中,依托5G+8K技术,结合AI、VR、AR等新兴技术,以5G融合网络+工业切片+MEC定制化方案,率先规模化实践5G融合网络。公司以有线网络为基座,融合5G形成全流程无死角全覆盖,能匹配不同场景使用更合适的连接方式,最大程度支持工业生产环节的全要素收集和云边协同。
项目还建设了一个工业互联网平台,深度融合8K、AI等先进技术,落地六大核心应用场景:5G+融合网络支持柔性生产、5G+AI车间眼智能视觉检测、5G+8K+VR/AR智能远程运维、5G+智能物流、5G+灯光拣选电子仓储、5G+能源管理,形成了一批经过实践验证的5G工业互联网解决方案,逐步推进5G技术向核心生产环节渗透,打造“制造设备全连接+制造系统全连接+数据可视+场景落地可复制”模式。全面提升企业生产效率和效能,将传统产能升级为优势产能。
1)5G融合网络支持柔性生产
柔性生产实际上相当于把所有车间的设备进行联网。例如原来一条产线有20台设备,需要一个工作人员或者5~6个设备维护人员,在一台机器上面进行转机操作时可能要好几个小时。如果将转机全部集成起来在后台进行柔性生产,就相当于柔性制造,让所有的数据联网,在后台统一发配统一进行转机操作。如此下来,可能一条产线只需要一个员工或者两条产线一个员工,能节省人力。
袁杰表示,当前制造企业内很多都是多品种小批量的订单,因此经常需要转机。以电视机生产为例,十多年前单个订单大多超过15,000台,比较少的订单是5000台,以1~2万台的订单为主,转机频率比较少,但是现在可能50台的订单生产完就要立即转机,每天转机多次。市场对企业生产效率、微型制造以及定制化的需求越来越高。
创维通过5G+融合网络,对车间的设备如SPI、印刷机、贴片机、回流焊、AOI光学检测设备、模组贴合设备、内观视觉检测、整机自动包装等进行实时数据采集,并接入数字化制造工业互联网平台,最终实现对所有设备的监控、分析和可视化。
2)5G+AI车间眼智能视觉检测
在创维彩电之前的检测中,产品的工艺、部品、配件、外观、包装等质检作业主要依赖于人工和单机设备检测,缺乏一定的学习能力和检测弹性,且各质检设备之间信息孤岛不能共享,导致检测精度和效率低下,质量标准不统一,增加了企业生产和运营成本。
创维采用5G+AI的技术模式,自主研发机器视觉检测装置,从电视机制造前端到末端共推出了22个品类300多台视觉检测设备。
“视觉检测有AI检测或其它一些智能检测以及云检测,云检测非常高大上但是投入成本非常高,我们针对彩电制造的各个环节进行重点突破。”袁杰表示,以电视机铭牌检测为例,创维的生产车间除了生产创维自己的品牌外也生产其它品牌的产品,因此铭牌检测尤为重要。属于功能看似很简单,但是作用非常大的检测类别。当前创维彩电车间的每台电视机包装之前都要对铭牌进行检测,自动识别是否正确。“这一类是我们主张小而美的一些应用,而且可以复制,应用到纸箱贴纸检测或是条码检测等场景中去。”袁杰说道。
生产的视觉质检各个工序环节通过5G网络联动,产品故障诊断及预测,返修、维修等跟踪,从而实现智能生产与调度管理的高效协同,降低管理风险;利用高可靠的技术能力和5G的低延迟,可以及时获取产线边缘端视觉检测设备暂停或停止信号,将问题出现到发现再到停机的时间降到最低,通过机器视觉自动智能检测替代人工,可靠保障产品出厂品质。
尾记
在袁杰看来,创维彩电数字化转型的目标主要围绕降成本、提质量、增效率、保交付4大核心,包含4个模块:一是信息化协同,即企业各系统之间实现无缝连接,协同闭环反馈;二是透明化,车间的信息要进行透明的管控分享,共融物料信息以及实时追溯;三是品控,品质管控送本求源;四是效率,订单需求及时传达,管控生产准时交货。
“彩电行业相对而言利润比较薄弱,因此我们当前走的还是精细化路线,以数字化转型为大方向,自上而下进行全面的推进,并最终以企业产生价值为目标的理念进行裁定,在自动化、信息化、仓储物流、机器视觉质检、设备管理等模块持续进行智能制造的建设和应用。公司一直以来坚持务实创新,推进彩电智能制造和数字化转型取得了阶段性的应用成果,为公司制造提升夯实了基础,致力于打造成行业内最具竞争力的彩电工厂。”袁杰最后如此总结。
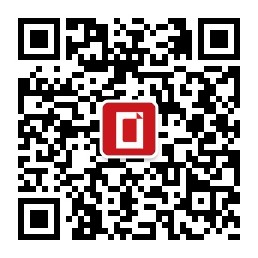