液晶显示行业新品全维度品质管理探析
- 来源:消费电子 smarty:if $article.tag?>
- 关键字:开发品质,过程品质,原材料品质 smarty:/if?>
- 发布时间:2024-02-25 17:32
李方倩 孙月婷 张继勇 李兵兵 汪流培
【摘 要】由于市场显示需求多样化,包括近几年的教育行业转变带动了教育平板等特殊需求,液晶显示行业为匹配市场客户需求,产品的迭代更新速度较快,以满足客户对画质和刷新率等的多样化的需求。
基于以上市场需求点,为了满足客户使用需求,快速且高效地完成产品迭代,稳定的新产品开发过程显得尤为重要。为达成新产品健康量产,计划从开发品质、过程品质、原材料品质三个维度展开说明。
【关键词】液晶显示屏;新产品开发过程;开发品质;过程品质;原材料品质
近年来市场变化迅速,市场需求日趋多样,液晶显示行业为了可以更好地匹配市场客户的需求,产品迭代更新速度越来越快。这就对新产品的开发提出了更高的要求。要想让新产品可以在有效满足市场客户需求的基础上,实现健康投产,就需要做好全维度品质管理。接下来将从液晶显示行业的发展特点出发,就新品的全维度品质管理进行探讨。
一、管理概述及主要过程
液晶显示屏是一种借助于薄膜晶体管驱动,通过液晶的不断偏转,将光通过彩膜投射出,产生不同颜色画面显示的一种产品。在液晶显示行业中,主要生产过程是:先生产出阵列基板和彩膜基板,两块基板对合后,切割成小块裸屏(部分产品有多次切割和研磨减薄的工艺),根据整机设计的要求,针对裸屏进行再次加工,包括增加驱动电路、贴附偏光片、组装背光源,触控贴合等模组工艺,最终,最常见以带有触控功能的模组样品为最终的出货模式。
针对液晶显示行业的新品开发全维度管理,包括开发品质、过程品质、原材料品质三个部分的输出。开发品质主要涉及流程中的评审,而评审的依据,包括过程、原材料及评价的准确性输出。过程品质为基于从x(风险评审)起始,到y(绩效考核)的阶段输出,再到Y(现场检查)的最终输出,形成指标看护、工具应用、落地检查的新品过程FCA模型品质管理体系。原材料品质则是基于原材料的NUDD识别和结合IQC管理的重点监控,达成问题点的闭环管理。通过三个维度的管理强化,实现新产品的健康量产。
二、开发品质管理
开发品质是基于过程、原材料及评价的准确性输出。关于过程和原材料评审过程及要求,将在过程品质和原材料品质纬度进行详细说明。
(一)评价准确性确保
可靠性评价主要分为光学、电学、环境、机械、包装相关测试,测试基准来源于客户和内部评价规范。可靠性评价准确性的基础,是对评价规范准确性的解读。内部评价规范可溯源可参考,因此对内部评价规范的理解较为具体明确。难点在于对客户提供评价规范的解读和内化。客户提供给供应商的评价规范,可能来自不同渠道获得标准的整理集合,存在测试细节不明确或者测试本身不适用于此应用场景的情况。因此,如何正确地同客户确认,或者在部分项目上,以成熟经验来指引客户尤为重要。每项评价测试的测试条件、数量、判定准则,都是需要规范在客户定供要求上,以此来理解客户并接收完成客户的评价需求。
针对重点客户群体和特殊客户群体,更适合建立客户档案进行管理。比如针对消费品类平板市场占有率排前列的客户,持续的物量需求,是建立客户档案的基础。建立客户档案,可了解客户持续变化和不变的评价关注点,结合产品的认证履历,也可实现检讨初期对产品可达成能力的评估。此外,针对核心客户的隐性需求,也需要形成档案记录并进行传承,其中包括未体现在RFQ要求中的指标,信赖性评价中特殊的检查节点和关注节点等。此外,客户品味也作为客户档案的内容之一,也需要被详细记录和评估。比如某客户基于自身其他项目曾经发生过的不良,尤其关注角落位置的发亮不良,对发亮程度非常关注,因此在针对此客户的规格检讨和信赖性评价中,需要重点根据客户品味关注相应的不良,并进行经验传承。
除了对可靠性评价规范的准确解读,还需要评价方案标准化,从5M1E出发,重点关注 “人”“机”“法”三个方面。基于“机”和“法”的准确可靠,可基本忽略“人”的影响。因此,我们针对“机”和“法”进行说明。 “机”指的是评价设备的准确可靠,常指环境试验所需要的炉体的准确可靠。为了实现实验室环境下的加速验证,常用温度或者湿度因子,让被测样品处于一个较为严苛的环境中,实现加速验证。因此需要在能够满足环境要求的实验条件下根据评价规范进行评价。以要求的环境进行实验的炉体能够按照评价规范要求进行。主要评估项包括:稳定可控的温度,湿度,以及可按照序列安排的温湿度变化,炉体整体氛围的单纯性。除设备自身能力可满足外,还需要做到与设备连接的外部资源的稳定性,如水、电等。定期对设备循环水进行Ph及金属离子的确认,可以保证实验过程中无其他化学腐蚀的影响,仅需要考虑温湿度的加速。
“法”可参照评价规范进行内化。接收到的标准包括实验的条件,而“法”中,不仅是强调规范中明确的条件,还需要落实到细节执行中,包括测试治具的使用,测试点位的选取等。标准且可被准确执行的方法,才是落地的方法。
(二)评审流程说明
在液晶显示屏的生产模式中,部分产品是在屏厂直接一站式完成从“大基板”到“最终模组样品”的生产,也有部分生产模式中,是屏厂与后段模组厂合作分工,进行产品生产。这种模式下,屏厂作为物权工厂,将模组工艺段外包给合作工厂,由外部合作工厂完成切割后的组装生产。基于此种生产模式,又区分为OEM和ODM模式,用以区分原材料由物权工厂自购(OEM包工不包料)和由模组工厂自购(ODM包工包料)。
不同的生产模式下,评审流程有共性也有差异性。针对共性和差异性,需要明确不同角色的评审要求。
共性要求包括试产每个阶段的进阶评审,包括量产的进阶评审。
单个试产过程包括:试产事前会→试产过程→试产总结会→下一次试产事前会,试产总结会作为每个试产过程的评审点,需要针对试产过程中原材料入检数据,过程数据,良率数据,可靠性评价结果等进行综合判断,确认是否可以进阶到下一次试产中。只有试产中的问题点都有明确的原因分析及改善对策,才可以采取有效对策,在下一次试产过程中进行避免,确保每一次试产资源得到充分应用,不会因为相同问题重复发生而导致评审的反复不通过。
量产的进阶评审,相当于更加具体化且详细的试产评审。在量产进阶评审中,需要输出的结论为,此产品是否已经具备量产能力,是否可以从小批量生产转为大批量投产。试产问题点是否已经全部找到根因并验证结束,针对问题点的改善对策,是否已经落实在文件中,文件中的变更点是否已经传递到现场,现场是否可以直接看到或者查询到最新的文件,关于文件的执行,现场实际作业人员是否有其他意见。只有以上都得到合理解决,才可以进阶量产阶段。
在共性的评审流程外,需要针对不同的生产模式,进行评审要求的差异性说明。
基于屏厂为物权工厂的前提下,针对屏厂从前至后一站式生产的模式,由屏厂的各组织依据业务职责,进行评审意见输出。针对原材料由物权工厂自购,代工厂只负责生产的模式下,整体评审仍由屏厂对应涉及组织总体输出,代工厂的制程评审结论可作为参考。而针对原材料由模组工厂自购的模式,由于代工厂进行整体模组段机构以及电路相关的设计及原材料的选型,对整体模组生产管理负责,因此在这种商务模式下,由代工厂针对模组段部分进行整体评审,物权工厂作为监督方,对代工厂的评审结论进行复核。如果该新品项目不仅只涉及模组段工艺部分,那仍由屏厂输出整体评审结论(通过或者不通过)。
在模组段代工中,仍有一些特殊的代工模式,比如只进行部分制程的代工,整体评审职责的划定,需要参考以上合作模式,以工艺段进行划分,每段对其各自部分负责,由屏厂输出最终汇总结论。
三、原材料品质管理
原材料管理,是输出也是输入。它作为生产过程的输入,决定着整个试产的成功与失败。在原材料品质管理中,界定了5个节点,包括“做在立项前”、“做在首次试产前”、“做在出货前”、“做在下次试产前”和“做在转量产前”。通过节点策划,把事情做在前面。
在立项前,关注点在于规格识别,有利于在供应商定供时争取更匹配合适的资源池内供应商[1]。在首次试产前,进行风险规避和工艺梳理。在出货前,完成能力监控和机差对标。在下次试产前,对问题点进行充分识别和试产总结。在转量产前,完成良率和问题点闭环。通过流程梳理,细化各节点必要交付物,输出“需要做好的18项交付物”。
在企划阶段输出原材料的内化规格,在定供阶段输出良率综合成本对比结果。在设计确认阶段,输出《新品设计风险Check》表单和《原材料选型NUDD》文件。首次试产前,需要输出《工艺Lesson Learnt》《制程工艺门槛》《测试SOP》《单部品 QCP》。在首次试产过程中,需要监控首件检查(即FAI)和过程能力分析,试产后需要输出光学机差对比,在下次EN前,针对上次试产问题点,需要输出良率、图纸、不良改善对策清单和更新后的《单部品QCP》。在产品转量产前,输出正式的终版文件,包括良率、试产对策清单及QCP文件。
通过交付物的明确,明确了原材料管理的指导方向。
四、过程品质管理
稳定可控的过程,是新产品稳定的基础[2]。新品开发过程,试错成本过高,因此运营生产精益管理弥足重要[3],基于此思路,需要建立完整的、落地的、可执行的体系品质链。
此体系品质链的基础是FMEA。目前FMEA文件版本升级,由第四版FMEA升级为新版FMEA,取消RPN风险等级,更替为AP措施采取等级,而在大部分使用场景下,FMEA 文件的运用流于形式,开发阶段项目组未充分使用FMEA工具。
基于FMEA工具的指导,建立FCA模型。
具体模型如下:
“F”代表“FMEA”,“C”代表“ControlPlan”, “A”代表“Action”。基于FCA模型,整体流程包括:流程建立、执行监控、CP-现场-执行一致性检查、持续改进。在流程建立方面,需要定义每个时间节点需要监控的事项。如在设计定版前需要完成新品FMEA评审,并在试产投入前 3天完成FMEA文件上传,前1天内完成Control Plan文件。每次试产阶段根据问题点持续检讨优化改善,在量产投入前1 天,完成终版FMEA和ControlPlan文件上传。首次量产时,将针对试产阶段问题点及对应文件变更,进行Control Plan/ 现场执行一致性检查。
基于以上流程,进行新品制程问题点管控和过程能力分析和确认,输出新品制程问题点清单和未达标原因分析改善清单,并在后续的一致性确认中逐条确认,输出一致性检查不符合项,不符合项关闭率等指标,并完成文件的更新。在这种良性循环中,定期确认总体的执行达成情况,并与绩效挂钩,强化组织间的互动[4-5]。
在整个新品过程管控中,强调每个过点评审的输入的完整性和输出的结论性,输入经由过程到输出,强调设计完成的过点评审,试产完成的过点评审和量产移交的过点评审三个过点。在过点一主要强化风险识别,通过四新识别,输出《FMEA评审会议录》、《产品初版FMEA》、《产品初版CP》。过点二开始对产品全生命周期进行制程管理,依据FMEA文件确定Control Plan文件CTQ,收集跟踪试产问题点及改善验证,在试产结束后,更新相应FMEA和CP文件,再此过点评审时输出修改版FMEA及Control Plan,以及制程问题点清单。进阶到量产阶段时,需要完成大批量生产前的所有准备工作,确认改善对策已落实,输出《量产性 FMEA&CP》和《一致性检查不符合项》。
通过FCA模型的运行,结合既往优秀经验模式,建立过点卡控流程,成立新版FMEA 多功能小组,在新品过程介入,实现风险→试产→移交的闭环管理。
总结
综上所述,液晶显示屏应用非常广泛,而客户的不同对于液晶显示屏的要求也不同,这就对液晶显示屏的新品开发提出了较高的要求。通过对开发品质、过程品质、原材料品质三个维度的全面管理,能够有效降低试产中问题点数量,并且针对试产问题点能做到预防再发的效果。重复问题点在试产和量产中不再发生,是产品快速健康量产的前提。而减少问题点的发生,是能够缩短试产时间的最有效途径。在未来的研究中,还需要在考虑市场变化的基础上,针对行业、企业的实际情况予以更加深入的研究,只有这样才能够确保所开发出的产品可以更好地满足客户的需要、满足市场发展的需要。
参考文献:
[1] 张玮. 供应商远程品质管理[J]. 电子技术与软件工程,2019(19):254-255.
[2] 孙远. J 电子公司新产品导入管理问题研究[D]. 西南大学,2022.
[3] 王丽娟. 探究液晶显示产品开发过程中的质量管理分析[J]. 新型工业化,2020,10(11):147-148.
[4] 沙双庆, 庄恩泽. 液晶显示产品开发过程中的质量管理措施[J]. 计算机与网络,2020,46(18):26-27.
[5] 吴照丹, 刘辕, 汪洪亮等. BPI 项目管理法在液晶显示面板产品开发项目的应用研究[J]. 现代商业,2020(16):150-152.
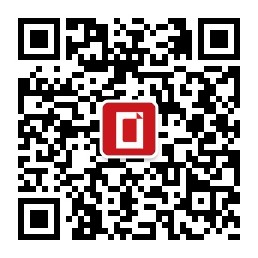