为燃料电池的大规模生产铺平道路
- 来源:国际金属加工商情 smarty:if $article.tag?>
- 关键字:燃料,电池,生产 smarty:/if?>
- 发布时间:2024-04-15 16:11
弗劳恩霍夫工程与自动化研究所(Fraunhofer IPA)和黑森林校区的一个研究小组制造出了一种机器人单元,可在几秒钟内完全自动组装燃料电池。这为燃料电池系统的价格下降以及在重型货物运输中取代内燃机提供了必要条件。
传送带将双极板送入机器人的视野。它的图像处理软件可以识别这种安装在燃料电池中的部件。机器人用吸力抓手抓起双极板,并在另一个摄像头中短暂停留。它从下方扫描双极板,记录准确的尺寸,并识别底部精细结构的性质——这是一个重要的质量特征。然后,机器人将双极板放在一个堆栈上。整个过程只需两秒钟。
1秒钟后,第二个机器人识别、拾取并放置膜电极单元。双极板和膜电极单元——这两层构成了燃料电池。氢气和氧气通过双极板进入。这两种化学元素在膜电极单元中相互反应。由于这只能产生1V的最大电压,因此必须将大约400个燃料电池堆叠在一起,才能形成一个燃料电池堆,例如为卡车提供动力的燃料电池发动机。
双机器人在几秒钟内堆叠燃料电池
迄今为止,燃料电池堆一直是以类似工厂的方式制造的,这意味着需要大量的手工劳动和相应的耗时过程。弗劳恩霍夫制造工程与自动化研究所企业战略与发展部的Erwin Groß说:“如果燃料电池要取代重型货物运输中的内燃机,就必须实现工业化大规模生产,并在很大程度上实现自动化和相应的成本效益。”
这正是弗劳恩霍夫工程与自动化研究所和黑森林数字化、领导力与可持续发展中心(黑森林校区)的研究团队目前在H2FastCell项目中取得的成果。机器人单元每秒钟就能在燃料电池堆上放置一个双极板或膜电极单元。因此,一个由400个独立燃料电池组成的堆栈只需约13分钟即可完成。而人工生产则需要数倍的时间。
燃料电池堆工业化批量生产的另一个标准是精度。因为任何偏差,即使是μm级的偏差,都会降低燃料电池系统的性能。这就是2个机器人平行堆叠两个燃料电池堆的原因。如果它们的摄像头在质量控制过程中记录到形状和尺寸上的微小偏差,它们就会将双极板或膜电极单元分配到相应的堆栈中。弗劳恩霍夫工程与自动化研究所数字化电池生产中心的Friedrich-Wilhelm Speckmann说:“通过这种最佳匹配方法,我们减少了制造商一直抱怨的废品率。”他与 Groß共同领导了H2FastCell项目。
为企业提供试验台的机器人单元
完工的机器人单元位于弗罗伊登施塔特黑森林园区的试验场上,将作为中小型企业测试其产品的试验台。施瓦茨瓦尔德校区总经理Stefan Bogenrieder说:“我们已经为黑森林未来的生物智能氢循环经济研究中心奠定了基石。我们希望与巴登符腾堡州的企业合作,将氢技术作为一种能源用于移动和固定用途。”
除了弗劳恩霍夫工程与自动化研究所和黑森林园区之外,巴登符腾堡州的五家公司也参与H2FastCell项目,该项目现已结束:软件开发商ISG Industrielle Steuerungstechnik GmbH(斯图加特)、真空技术制造商J. Schmalz GmbH(格拉滕)、传感器生产商i-mation GmbH(罗特维尔)、机械设备制造商teamtechnik Maschinen und Anlagen GmbH(内卡河畔弗赖贝格)和自动化技术供应商 Weiss GmbH(奥登瓦尔德布亨)以及巴登符腾堡州经济、劳动和旅游部为H2FastCell提供了约230万欧元的资助。
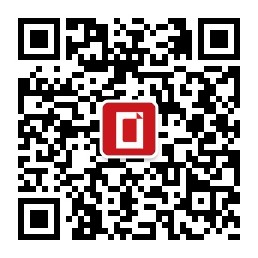