3D打印万能?
- 来源:中国计算机报 smarty:if $article.tag?>
- 关键字:3D打印,零部件 smarty:/if?>
- 发布时间:2013-12-05 16:35
2012年4月,《经济学人》的一篇文章让3D打印(学名增材制造)迅速蹿红,甚至被冠以“第三次工业革命”的称号。其实3D打印机并不是新产品,3D打印机诞生于20世纪80年代中期,是由美国科学家最早发明的。3D打印机的基本原理是利用特殊的耗材(胶水、树脂或金属粉末等)按照由电脑预先设计好的三维立体模型,通过黏结剂的沉积将每层粉末黏结成型,最终打印出3D物体。由于3D打印分层加工的过程与喷墨打印机十分相似,所以被称为“打印机”。
3D打印技术诞生二十多年来,已应用于航空航天、汽车、模具、生物医疗、电子、建筑等专业化领域,也应用到了个人消费、办公、教育等大众化领域,3D打印产品和服务收入的年均增长率接近27%。据市场研究公司Wohlers Associate发布的2012年度报告显示,2011年3D打印业销售收入达16.8亿美元,比2010年增长29.4%。据预测,到2016年3D打印市场规模将达到31亿美元,到2020年将增长到52亿美元。
从应用的领域来看,目前3D打印主要应用于原型制造、模具制造和直接制造三大领域。其中,原型制造主要是指应用3D打印技术制造用于产品设计、测试和评估的模型。模具制造主要是指应用3D打印技术制作蜡模或砂型。直接制造包括两类:一是应用3D打印技术制造玩具、饰品、鞋类、陶瓷制品、简单服装与教育器材等消费品;二是制造金属、塑料、生物构料块等复杂难加工、小批量的功能部件。
充分定制化
随着近年来3D打印设备价格的降低,3D打印正从实验室和工厂走向办公室甚至是家庭,在包括玩具、饰品、鞋类、陶瓷制品和简单服装在内的特定消费品领域将产生深远影响,3D打印技术制作这些产品相对容易,而且可以实现充分的定制化。从2007年到2011年,个人消费用3D打印设备的销售量实现了200%以上的年均增长速度。
对于用户来说,3D打印最吸引人的就是可以以最快的速度实现其创意,这在过去是不可能的。过去,设计师设计一款产品要考虑到生产制造过程中的各种问题,有些设计由于无法生产被设计师舍弃,非常的可惜。有了3D打印,设计师可以发挥他的想象力,专注于产品形态创意和功能创新,而无需担心产品的生产制造。这不仅降低了产品的研发成本、缩短了产品的开发周期,而且可以实现更多的创新。
由于3D打印简化或省略了工艺准备、试验等环节,产品数字化设计、制造、分析高度一体化,因而可以显著缩短新产品开发定型的周期。过去,汽车厂商试制一台六缸发动机,采用传统砂型铸造方式,模具设计制造周期长达5个月,如果采用3D打印,则只需一周便可制成。
无需组装
对于产品来说,从理论上讲,零部件越多越不安全,结合部越多出现问题的隐患越大。尤其是像空客A380飞机这样的大型机械,它大约有450多万个零部件,如果可以将其中的部分零件进行整合,对于整个机械稳定性的提高是有帮助的。
3D打印技术的一个明显优势就是可以将多个零部件集合成一个整体制造出来,减少零部件的数量,不但大幅简化了之后的装配工作,其安全性和可靠性也随之提高。
值得一提的是,3D打印突破了几何结构限制,能够制造出传统方法无法加工的非常规结构特征,这种工艺能力对于实现零部件轻量化、优化性能有极其重要的意义。
如果采用3D打印,用户可以将零件内部设计为网状结构,替代传统的实心结构,这不仅可以减少制造时的材料使用量,而且还减少了制造的时间,降低能源消耗量,更是可以让产品实现轻量化。
材料难题待解
在材料方面,3D打印最先采用的主要是塑料,多数应用在原型开发及产品设计领域。最早的3D设备所采用的材料多是热塑性塑料,所采取的工艺为熔融沉积成形,打印出来的物品精度很低,难以作为部件使用。
随着技术的进步,现在3D打印的材料开始从塑料向砂、光敏树脂、黏合金属扩展,应用也随之扩展到蜡模、砂型等领域,成形精度也进一步提高,可以达到0.2mm,SLM(选择性激光熔凝)成形精度可达0.1mm,甚至更高。3D打印的应用也日趋广泛,SLS(选择性激光烧结)除了成形铸造用蜡模和砂型外,还可直接成形多种类高性能塑料零件,SLM可直接成形性能与锻件相当的金属零件甚至是高性能的陶瓷零件。
3D打印的革命性突破在于近年来钛合金、不锈钢等金属粉末的使用。最新的3D打印设备可以打印出金属零部件,并做到精度高、尺寸大,无需大型锻造工业装备、大型锻造模具制造及大规格锻坯制备加工,而零件机械加工余量小、数控加工时间短、材料利用率高、生产周期短、制造成本低,目前已经应用在飞机高强度结构件、无人机、航天器及高档跑车等领域。
尽管打印材料有了革命性突破,但当前3D打印的广泛应用还有待于材料成本的降低。首先,可用的材料十分有限,如航空航天材料,需要进一步轻量化和高强度化,而目前的钛合金、不锈钢等材料的成本还很高,所制造的部件表面的光洁度还不够。其次,材料的认证也是需要考虑的重要因素,因为材料属性和结构设计尚未统一或标准化,限制了3D打印技术的进步。再次,还需要标准化的是材料属性数据库,该数据库必须足够健全,囊括大量的材料及其相应属性。未来,3D打印的发展将取决于所用材料的扩展、材料数据库的完善、材料自身成本的下降,如果这些方面取得突破,应用领域将会进一步拓展。
生物打印最具革命性
目前,等待器官移植的患者在得到合适的器官之前,通常要等待几个月甚至数年,有的患者甚至在等待的过程中死去。如果能像科幻电影《星河舰队》里面那样,可以由机器“打印”出人类的肌肉、血管、器官,那将拯救无数人的生命。
虽然人们现在还不能像电影中那样,但是由美国Organovo公司研制的3D生物打印机如今已经可以制造动脉血管,开发者称由这种设备“打印”出的动脉有望在未来用于心脏搭桥手术。
生物3D打印机与一般的3D打印机的不同之处在于,它不是利用塑料或金属,而是利用生物构造块,去制造真正的活体组织。虽然生物3D打印技术尚处于初级阶段,不过第一台3D生物打印机的原型机已在2009年底制造出来。
3D生物打印机有两个打印头,一个放置最多达8万个人体细胞,被称为“生物墨”;另一个可打印“生物纸”。所谓生物纸其实就是主要成分是水的凝胶,是细胞生长的支架。医生首先通过三维生物成像和超声技术,取得病人体内目标器官的大小、形状、内部三维结构的技术信息,根据这些信息设计一个器官蓝图,上面标明了每一个细胞的具体位置,也就是它在这个器官中的立体坐标。
因为3D生物打印机使用来自患者自身的细胞,所以不会产生排异反应。这种机器首先“打印”器官或动脉的3D模型,接着将一层细胞置于另一层细胞之上。打印完一圈“生物墨”细胞以后,接着打印一张“生物纸”凝胶。不断重复这一过程,直至打印完成新器官。
随后,自然生成的细胞开始重新组织、融合,形成新的血管。每个血管大约需要一小时形成,而融合在一起需要数天时间。这时候的器官只是一个各种细胞堆积在一起的活体组织而已,细胞间的互相作用还没有建立,之间的相互黏合力也很微弱,而且还不具备器官应有的许多生理功能。这个新生的器官需要放入一个培养箱内,加入各种细胞生长因子和促分化因子,以加速其组织结构和各种生理功能发育成熟。
审慎对待3D打印
当前3D打印发展尚不成熟,人们要对其有清晰的认识。中国电子信息产业发展研究院副院长杨拴昌在新工业革命与增材制造国际研讨会上表示,3D打印目前主要面临四个方面的问题。
一是设计工具需进一步优化。3D打印要求开发和广泛运用计算机辅助设计(CAD)工具。对于功能部件制造,需要新的工具来优化形状和材料性能,以最大化地减少材料使用和重量。对于非专业人员,需要开发出易于操作的设计工具,来进行产品设计。
二是可用材料需持续拓宽。目前的可用原料还不多,正逐步从树脂、塑料扩展到陶瓷、金属,乃至最新的金、银以及强度极高的钛和不锈钢等材料。未来,仍然需要开发更多的材料,并深入研究材料的加工-结构-属性之间关系,明确材料的优点和局限性,为材料提供规范性标准。
三是生产过程需要加强工艺控制。为提高连贯性、重复性和统一性,需要建立装备认证标准,并对生产过程进行内部监控和闭环反馈,如通过传感器提供无损性评估与早期缺陷检测,通过流程控制减少设备故障。为更好了解、预测材料性能和零部件功能特性,需要建立预测性模型,使设计师、工程师和用户能够估计零部件的功能特性,并通过调整设计达到预期效果。
四是产业发展需要加强必要的监管。如利用3D打印,犯罪分子能够下载枪支设计软件,私下制作枪支,而且枪支很容易隐藏,可以躲过金属探测器。又如,3D打印的汽车方向盘如果在交通事故中失效,将很难确定事故中的责任方,失效可能是由于设计不足、制造不当、材料甚至是安装所引起的。此外,如果将3D打印技术用于生产人体的肾脏等器官、婴儿模型等,还将涉及到社会道德和伦理问题。
赛迪智库装备工业研究所所长左世全之前在接受媒体采访时表示,3D打印暂时还不可能替代传统的制造技术,只是一个补充,目前市场空间依然有限。3D打印发展初期要靠国家相关部门来统筹布局、合理安排,不能一哄而上,在有技术、人才资源、市场基础的地方先行先试,根据效果进行推广。如在航空航天、汽车制造、生物医疗等领域开展一些示范,在示范的过程中制定相关行业标准,积累发展经验。
本报记者 张楠
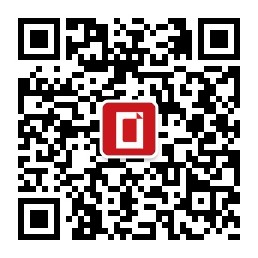