精益IT:制造业转型的路径选择
- 来源:中国计算机报 smarty:if $article.tag?>
- 关键字:制造业,IT smarty:/if?>
- 发布时间:2014-02-25 15:41
面对国际金融危机波及、先进国家高端制造业回归、国内改变原有粗放式经济增长方式等多重挑战,我国制造业应对挑战的路径选择十分重要。
“多数新兴市场现在和今后一两年面临一个经济调整的相对困难时期。中国依旧是高增长,只不过是回归到了正常的高增长过程。”经济学家樊纲在今年年初富士通中国论坛上发表演讲时表示,今后两三年中国经济将保持7.5%~8%的增长速度。
然而,7.5%~8%的宏观经济增长速度,对于微观之中的中国制造业企业而言,挑战不仅是艰巨的而且是多方面的,而应对这些挑战的路径选择十分重要。
为什么要选择精益
当前,我国制造业企业处在一个复杂剧变的内外部环境之中。
世界各国都是以各自的比较优势参与经济全球化带来的产业链全球再分工。中国制造业在产业链的低端,日益感受到来自东南亚各国基于廉价劳动力的用工成本优势带来的严峻挑战,而在产业链高端,2012年美国发布了《国家先进制造战略规划》,2013年德国发布了工业4.0战略,经济发达国家日益重视高端制造。下挤上压的国际产业环境让中国制造业企业颇有进退维谷的感受。
中国多年来经济高速发展,世人有目共睹。但总体而言,这种经济的高增长是以不经济的方式实现的,是以能源、自然资源和环境为代价的粗放型发展。当雾霾在中国经济最发达地区投下经久不散的阴影时,公众都已切身体会到原有的经济发展方式难以为继了。
尽管此次国际金融危机对全球经济的影响是前所未有的,但这毕竟还是量上的差别;而转变经济增长方式对于为数众多的制造业企业而言,意味着既要保持增长,又要放弃增长所依赖的生产模式,这是质的挑战。
如今转变经济增长方式已经成为迫在眉睫的国家战略,这一战略落实到产业层面就是转型升级,进一步体现到企业层面就是创新。
无疑,技术创新是创新的最高层次,也是我国制造业企业从低端走向高端必须突破的。但是技术创新是一项艰巨而长期的投入,不可能一蹴而就,而且国外同行多年来在研发领域投入巨资,已经在市场上构筑了专利壁垒。
对于大多数亟待放弃原有粗放发展模式的制造业企业而言,解决“远水解不了近渴”的最现实的路径就是生产管理制度的改善。
“制度是人与人之间的关系,它存在很多阻碍生产发展、效率提高的因素,通过制度的改进,可以释放出更多的效率。”樊纲在演讲中表示,“这一方面最好的例子,是30年前搞的农村改革。地还是那些地,人还是那些人,当时农业技术上也没有很多突破,就因为改进了制度,二年之间中国解决了吃饭和温饱问题。”
如果说土地承包制是在原有资源的条件下释放出农业的活力,那么,基于精益思想的生产管理制度则是在企业现有资源的条件下,消除浪费、提高效率的最佳途径。
从精益到超越
汽车工业无疑是现代工业社会发育最为成熟的产业,也在生产方式、管理实践上深刻而广泛地影响到整个工业社会。
1913年,亨利·福特开创性地将流水线引入T型汽车的生产,辅之以泰罗的科学管理思想,开创了大规模生产的工业化生产模式。美国汽车工业从此开始告别手工作坊的生产方式。
而敢于与福特挑战并最终成为全球最大汽车公司的通用汽车,其时任CEO斯隆凭借的就是多品牌的差异化竞争和企业组织管理上的创新。
2006年,丰田汽车首次超过通用汽车,成为全球最大的汽车公司,这对有着“轮子上的国家”之称的美国影响之大,不难想象。
实际上,美国产业界早已感受到丰田汽车的锋芒。早在1984年,麻省理工学院就在多家汽车企业资助下启动了“国际汽车计划”,在全球范围内研究汽车产业的生产管理模式。这一研究成果最先以《改变世界的机器》一书呈现世人。
这本书首次揭示了丰田汽车精益生产的秘密。与大规模生产方式相比,基于“消除一切浪费”这一核心理念的精益生产方式, 可以将企业研发、生产和管理人员数量减少50%,新产品开发周期缩短25%~50%,生产过程中的库存降低90%,成品库存下降75%,而且其将瑕疵消除在流程中的做法又有效地提升了成品率。
这些人工、时间、库存、成品等效率的提高,并非因为技术上的创新,而完全依赖的是JIT(准时生产)、看板、零库存、持续不断地改进等生产管理方式上的创新和改善。
精益生产以“多品种、小批量”的生产方式,使得企业投入的资源价值最大化,进而颠覆了现代工业社会大规模的生产范式。
之后,《改变世界的机器》作者,又将关注点从生产现场上升到整合企业,进而发现,精益的思维方式不仅适合制造业的企业活动,而且适用于第三产业,于是又推出《精益思想》一书。
到了1998年,源自国际汽车项目计划的另一项研究成果又以《超越精益思想》一书问世。该研究聚焦于丰田等行业领先企业的产品开发管理,即以多项目协同开发的管理模式,颠覆传统的项目管理模式。
用IT超越精益
伴随着信息技术的发展,汽车企业早已借助信息技术告别了人工传递看板的年代。但是每当人们提起精益,必然联想到丰田汽车,很少有人知道承载丰田精益体系的IT服务商富士通。
在富士通中国论坛精益IT与制造业分论坛上,本报记者也才得知,早在1961年富士通与日本汽车业进行合作,接着便与丰田汽车结成战略联盟,陪伴客户一路经历了日本汽车业的发展和壮大、精益制造理念的实践和完善。
在与丰田汽车等日本企业的长期合作中,富士通也形成了自身对于精益的独特理解。“精益的‘精’就是精准,采用ICT实现包括生产在内的企业行为的可视化、标准化,从而实现企业管理的数字化、精准化;‘益’则代表着持续不断地改善。企业的活力和成功往往来自于现场的不断的革新和创新。” 富士通(中国)信息系统有限公司CEO石丰瑜表达了信息技术时代富士通对精益生产的超越。
富士通(中国)信息系统有限公司北京分公司总经理汪波介绍说,工厂生产现场信息化与办公室信息化存在着很大的差异,在实施精益IT之前,富士通会帮助企业分析当前面临的实际困难与挑战;从细节入手,消除生产中的物流、存货、动力、等待时间、多余加工、剩余生产、不良品、知识等8类浪费;及时整理、整顿清洁现场,促进生产的持续改善,从而实现生产管理的全面改善。
长安汽车副总裁兼CIO马军则在演讲中展示了另一种超越。去年下半年长安汽车高管“整建制”来到北京,拜访百度、腾讯等互联网企业。这一举动在制造业企业中是很难见到的。
长安汽车关心的是十年后,消费者选择“买”车还是“用”车?汽车与IT及互联网如何融合、如何行动?据介绍,长安汽车已经制定了“现阶段车载信息系统以互联网接入和TSP初级服务为主,并以实现自动驾驶作为汽车产品信息化发展未来目标”的战略。
而精益生产体系、精益制造标准工厂在长安汽车集团的建成,增强了企业的市场竞争力,也使得长安汽车高管能够有时间和精力,从容地与互联网企业探讨产业的未来发展。
本报记者 马文方
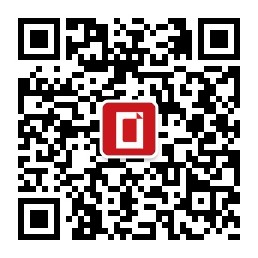