数字化监控提升齿轮质量
- 来源:国际金属加工商情 smarty:if $article.tag?>
- 关键字:数字化,监控,齿轮 smarty:/if?>
- 发布时间:2024-12-07 11:50
本文译自德国Werkstatt und Betrieb杂志
作者:Walter Graf
采埃孚勃兰登堡工厂是将数字化技术与工艺流程相结合的一个代表。设备操作者、工艺师和管理人员能够始终与所有数字化系统相互联系,实时了解生产设备的工作状况——这也使采埃孚勃兰登堡工厂成为数字化实践的先驱者。
除此之外,勃兰登堡工厂还利用莱斯豪尔公司研发的机床和Argus过程监控系统实现了齿轮加工过程的数字化。在这两家公司长期的合作过程中,它们之间结成了深厚的友谊,也取得了丰富的成果。
磨削加工的数字化解决方案
勃兰登堡工厂拥有1500多人组成的专家团队,主要生产高端跑车专用手动和双离合变速器。变速离合器质量标准的关键因素是齿轮,而磨削这些齿轮的加工设备就是莱斯豪尔公司的产品。
Argus过程监控系统用于磨削工艺过程的监控和优化,包括了机床和砂轮磨损的监控。两家企业合作的目标是在数字化创新力的帮助下实现齿轮加工工艺过程的优化。
几乎所有勃兰登堡工厂的零部件都是在Argus过程监控系统的监控下生产的。除了确保齿轮加工工艺过程可靠性之外,Argus过程监控系统还可以明显降低后续工序的生产成本。
在这套过程监控系统的帮助下,工艺师们也有能力根据监控系统发现的问题立即拿出正确的解决方案。Argus过程监控系统能够实时检测齿轮加工设备的工作状况,并将有问题的残次品送出,或者在齿轮装配之前修复有残缺的齿轮。这就减少了拆除误装残次品齿轮的情况,也大幅度节约了生产成本。
及早发现振动源
Argus过程监控系统能够有效检测出齿轮粗加工时因工艺过程不稳定而导致磨削力过载、齿轮磨削砂轮碎裂等故障。当然,因碰撞而导致砂轮出现裂纹的可能性也非常小。然而,勃兰登堡工厂购买Argus过程监控系统的主要目的是预防复杂的振动问题。因此,勃兰登堡工厂很快就在莱斯豪尔公司专家的陪同下开发出了识别齿轮磨削过程中砂轮振动和潜在振动源的Argus监控系统。这一过程监控还可以通过校准加以优化,以消除齿轮磨削加工过程中潜在的NVH振动源(NVH是英文噪声、振动与声振粗糙度的缩写,是衡量汽车制造质量的一个综合性问题,它给汽车用户的感受是最直接的)。当然这种优化改进也是在Argus Web应用程序中大量数据分析的结果。
这一应用程序可以在任何一个Web浏览器中使用,即使是没有经验的用户也可以通过轻轻地点几下鼠标了解变速齿轮生产过程。当然,要解决生产过程中的这些问题还是需要工程师的专业技术知识和经验的。因此勃兰登堡工厂也聘请了一些能够处理这些质量问题的工程师、并在莱斯豪尔公司专家们的支持下简化和加速了Argus过程监控系统的实施过程。
在使用Argus过程监控系统之前,通常只是在生产线末端的EOL质量检验台上才发现加工出来的变速齿轮存在质量问题。利用常规的静态测量技术测量出齿轮加工过程中出现问题或者在类似磨损这样变化缓慢而引起超差的概率极低。这意味着按照过去的检测技术发现齿轮加工质量问题之前,有些有质量问题的变速齿轮已经安装到变速器中了。因此,为了确定齿轮加工中出现误差的原因就变得十分有必要了。
如果一个齿轮因磨具的原因而出现了质量问题,则在这一天加工的所有变速齿轮都可能有问题。由此而产生的高昂后续成本和费用是显而易见的。尽管这样的事情很少发生,但线下检测会导致巨额的拆卸检验费用,远远高于在磨削加工设备中分拣出有潜在质量缺陷的成本费用。若是在精加工之后才发现问题,带来的损失则更高。
今天,Argus Web应用程序允许技术人员随时查看齿轮加工过程中的实时情况——无论是在生产线的计算机上还是在他们办公桌的平板电脑上,无论他们身处何地。“该系统使我们能够更加深入地了解生产制造过程并采取比以前更具有针对性的技术措施。借助于Argus过程监控系统能够让我们及时发现出错的根源,提前做好预防残次品出现的措施。”工艺师Denny Machholdt说。
在Argus过程监控系统中,可以很容易地将技术参数与测量数据联系起来,这也就很容易发现潜在的问题,而这些过程参数的很小变化都会带来很大的成效。
Argus过程监控系统的另一大优势是状态监控,它能够利用自动化诊断功能不断地监测和评估加工设备的各种信号,并通过对这些信号的评判分析识别出潜在的故障。Argus过程监控系统中的传感器配置和测试周期使其能够快速地检测出机床设备中潜在的故障源。借助于云算法可以把加工设备一个测量周期内的所有数据都转换为表示设备工况的“信号灯”。如果信号灯是红色,则表示必须采取相应的纠错行动。
不需要多次测量和试磨
在使用Argus过程监控系统之前,如果发现磨削后的齿轮出现齿面轮廓误差时必须进行大量的测试和试验才能找出导致出现齿面轮廓误差的原因,而这些测试和试验工作常常需要2-3名员工才能完成。利用Argus过程监控系统的自动诊断功能之后就可以立即查明导致齿面磨削误差的根源,减少人力资源成本和设备停机时间。而且Argus过程监控系统使用起来非常简单、方便,得到了使用者的广泛好评。只要对设备操作者进行2-3小时的技术培训就足以让他们独立、安全可靠地操作和使用Argus过程监控系统,得出正确的监控数据了。
当需要更加准确的数据分析时,当然要求设备操作者也具有更多的经验,例如在振动频率的分析时。在莱斯豪尔公司的帮助下,勃兰登堡工厂获得了这方面的专业知识,另一方面,工程技术人员也将掌握的这些知识融入,培养出了一批自己的机床设备振动分析专家。
自从引进Argus过程监控系统,设备操作者和工艺人员之间就有了更加明确的责任和分工。工艺技术人员更加关心的是大批量产品生产时的数据分析,根据监控系统得到的数据评估分析可能出现的极限值、发展趋势和应该采取的技术措施。设备操作者的任务则是确保生产线、生产设备上的Argus系统平稳运行。在Argus过程监控系统中,这两部分工作始终与实时监控密不可分。Argus过程监控系统还可以通过对磨削砂轮的实时监控来最大程度地了解刀具的工作状况,降低刀具成本费用。因为它会控制着磨削砂轮不会提前退出磨削,最大程度地挖掘砂轮的使用潜力。
采埃孚指出,Argus过程监控系统大大改善了变速齿轮的磨削加工情况。需要强调的是,出厂后(线下检验后)产品退货的数量减少了,产品退货带来的成本费用也降低了。凭借准确的极限值设置,磨削齿轮零件的质量也得到了提高,因为在生产过程中将检测到的半成品剔除去了。今天,采埃孚已经在齿轮制造过程中掌握了Argus过程监控系统的应用。现在是进一步优化变速齿轮生产工艺流程和延长砂轮使用寿命的时候了。Machhold说:“现在真是开始的时候了。”勃兰登堡工厂的生产主管Niklas Kriegler说:“如果没有Argus过程监控系统将是一个巨大的历史倒退。
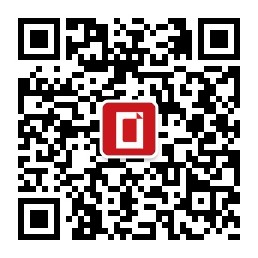