支持每年40万辆汽车的生产线——来自JLR增材制造专家的见解
- 来源:国际金属加工商情 smarty:if $article.tag?>
- 关键字:汽车,生产线,专家 smarty:/if?>
- 发布时间:2024-12-07 11:55
在最近举行的AMUK会员论坛上,Luke Fox概述了英国如何利用增材制造技术提高豪华汽车的生产水平。
作为英国汽车公司捷豹路虎(JLR)的增材制造技术专家,Fox概述了增材制造在公司工作流程中发挥的关键作用。
值得注意的是,增材制造技术并不用于大批量生产最终用途部件。相反,它的价值在于满足日益增长的大规模定制需求,同时还能加快测试车功能原型的生产。
后者代表了JLR在其快速成型制造中心(AMC)内部制造的“绝大多数部件”。Fox强调了这种增材制造能力的重要性,他说,如果没有增材技术,“我们就无法以如此快的速度完成测试”。
这位技术专家还讨论了增材制造如何解决汽车行业目前面临的最紧迫问题之一。
许多汽车可持续发展的最后期限正在快速临近,汽车制造商正努力最大限度地减少碳足迹,并使其车辆符合环保法规。Fox认为,增材制造技术将帮助JLR到2039年实现整个供应链净零排放的承诺方面发挥重要作用。
捷豹路虎的增材制造
英国增材制造协会(AMUK)是英国增材制造生态系统企业的行业协会。其最近一次会员论坛在航空航天制造商吉凯恩航空航天公司(GKN Aerospace)位于不列颠索尔(Britsol)的全球技术中心举行。
该活动主要介绍了英国增材制造的现状及其未来发展方向。与会者还有机会进行交流,并独家参观了吉凯恩的研发(R&D)设施。
Fox在演讲中概述了JLR的全球业务范围,JLR在英国拥有三个汽车制造基地,并在斯洛伐克、巴西、中国和印度设有工厂。该公司是塔塔汽车公司的全资子公司,生产和销售路虎揽胜、卫士、发现和捷豹等高端汽车品牌。
2018年,JLR承诺每年生产100万辆汽车。不过,Fox解释说,该公司后来转变了战略,将质量置于数量之上,在2023年生产了约40万辆汽车。
增材制造在实现这一质量方面发挥了关键作用。JLR AMC位于盖登(Gaydon)的高级产品创造中心,拥有20台工业3D打印机,采用6种快速成型制造技术。其中包括HP Multi Jet Fusion (MJF)、EOS系统、SLA、FDM和PolyJet 3D打印机。
聚合物粉末床熔融占公司增材制造能力的87%。釜式聚合占其系统的8%,而材料喷射和材料挤压分别只占3%和2%。Fox补充说:“目前,我们内部只有聚合物业务,没有任何金属增材制造业务。”
AMC是公司内部的卓越中心,发挥着从早期设计模型到功能部件的各种作用。Fox解释说:“AMC是作为一种内部资源而设立的,JLR各部门的工程师都可以申请增材制造部件。”
增材制造技术还被整合到整个企业的不同中心和部门。哈利伍德工厂是JLR的生产基地之一,那里的工程师拥有十几台工业FDM 3D打印机。
较小的台式FDM系统也分布在其他制造和工程基地。据Fox称,这些系统用于快速原型设计和测试,然后再到AMC生产更复杂的部件,这种分散的方法有助于保持灵活性。
增材制造促进汽车研发
过去,JLR曾利用增材制造技术生产终端汽车零部件。其中一个显著的例子是2019捷豹XE SV Project 8,该车采用了十多个AMC制造的部件。这些部件包括前号牌支架、汽车座椅头枕支撑和外部空气动力学特征。不过,这些都是小批量生产,Project 8仅生产了300辆。
一个更实际的应用案例与传统零部件有关。Fox举例说,1999年生产的路虎发现2的座椅把手经常出现问题,这个部件很容易断裂。
拥有该车型的客户现在希望能够从路虎经销商那里订购替换零件。然而,最初生产这些部件的公司已不复存在,注塑模具也已丢失。
JLR的解决方案是在内部制造这些零件,稍微改变几何形状以提高耐用性。Fox说:“我们每年打印大约50个这样的零件,客户往往不知道替换零件是用3D打印出来的。
大规模定制是 增材制造在汽车领域的另一个显著应用。Fox说:“大规模定制肯定不会消失,所以我们正在做很多这方面的工作。”他指出,JLR正在积极研究3D打印如何实现更多的定制部件,如个性化油箱盖和仪表盘。
不过,JLR “绝大多数 ”的增材制造工作都是针对测试车的功能原型。这些试生产的车辆在公开展出和试驾时,通常会用乙烯基迷彩图案包裹,以隐藏其设计。Fox表示,3D打印原型部件大大加快了测试过程,与传统制造方法相比,可以更快地对设计进行修改和评估。
一个令人惊讶的后期制作实例与影响路虎卫士越野车车主的一个问题有关。Fox解释说:“当他们把狗牵进车后座时,狗刮伤了保险杠。”
JLR的快速成型制造团队采取的应对措施是,对狗爪子进行3D扫描,分析爪子的硬度,然后3D打印出一个仿制爪子,放在机械臂上。这只狗“在很长一段时间内”反复抓挠卫士保险杠,因此开发出了一种可以购买的保护条,以最大限度地减少损坏。
JLR的金属增材制造路线图
据Fox称,JLR未来将致力于进一步扩大增材制造的使用规模。不过,他指出,该公司更注重扩大能力而不是产能。
这一发展的一个重要部分与金属增材制造能力的增长有关。该公司已经利用外部金属3D打印技术为路虎揽胜SV 460生产豪华后座部件。
这些最终使用部件由一级供应商制造,每年生产约40个。Fox补充说:“这是一个产量很低的项目,但在我们的生产车辆中,它是金属3D打印的。”
随着规模的扩大,JLR 正在努力将增材制造技术整合到更多的大批量制造应用中。Fox提到了一个正在进行的项目,该项目使用3D打印技术来支持 “大约一百万个零件”的生产。
最初,该公司采用激光粉末床熔融技术进行最初的概念验证测试。接下来,该团队希望生产“几百个”金属零件,以获得更严格、更精确的结果。为此,他们采用了粘合剂喷射技术,并酝酿将金属注射成型(MIM)作为最终的生产技术。
据报道,粘合剂喷射3D打印工艺生产出的零件更接近所需的机械性能。Fox补充说,这种方法可以进行更广泛的测试和改进,而不需要传统金属制造的高成本,因为传统金属制造需要昂贵的模具。
据报道,将金属3D打印技术纳入这一预生产阶段将使JLR能够在投入批量生产之前更有效地对设计进行微调。
在谈到公司更广泛的增材制造战略时,Fox强调了平衡内部能力与外部合作伙伴关系的重要性。虽然JLR可以在内部对零件进行原型设计和测试,但要实现全面生产,往往需要外包给专业供应商。Fox承认:“我们并不适合大批量生产。”他的 “金发姑娘方案”是在内部设计和测试方面与供应商密切合作,然后随着产量的增加逐步移交责任。
兰博基尼等其他汽车制造商也采用了这种模式。据Fox介绍,该公司最初在内部生产3D打印油箱盖,然后扩大生产规模,最终在验证后将整个流程外包。这种方法既利用了增材制造定制能力的优势,又将大规模生产流程移交给了第三方。
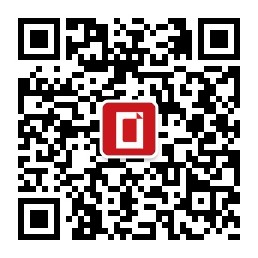