自动化焊接技术在薄板成型中的应用
- 来源:大众文摘 smarty:if $article.tag?>
- 关键字:自动化焊接技术,薄板成型,应用 smarty:/if?>
- 发布时间:2022-08-21 16:37
摘要:薄板焊接时,传统的薄板成型焊接技术焊接时的局部不均匀热输入会产生焊接应力与变形,影响焊接效率和质量。而自动化焊接技术可以满足同时进行多块薄板的焊接操作,提升焊接生产效率,焊接质量比较稳定,焊接水平趋于一致,同时还能够减少企业劳动力,降低劳动力成本,提升企业的生产经济效益。
1焊接自动化技术概述
由于焊接工人的焊接经验、身体素质、焊接设备各有差异,传统的人工手动焊接技术精度低,质量较差。自动化焊接技术要充分明确焊接工艺和工艺流程,但由于焊接环境是难以控制的,因此还需要时刻关注焊接生产的稳定性。所以在实施自动化焊接的过程中,要正确地运用各项自动化机械设备,对设备的配置、参数有一个较为清晰的了解,充分满足产品加工制造实际要求。焊接技术的自动化发展也使得各种规格的电焊机层出不穷,如气体保护弧焊机、电焊机、缝焊机、电子束焊机等,在自动化的基础上更近一步地提升了焊接工艺。并且,人工智能焊接机械臂、机器人的出现又使得焊接技术成为一个全新的研究领域,从自动化向智能化、集成化、高精度化转变,为我国机械设备制造业的整体水平提升起到了非常大的推动作用。
2自动化焊接技术在薄板成型中的应用
由于自动化焊接技术在薄板成型中的应用大多存在于汽车骨架的装配与船舶制造,因此本文主要以船舶制造为例,对其的应用进行具体分析。
2.1钢料加工阶段
2.1.1平板的拼接
2.1.1.1薄板拼接方法的选择
对于6mm以下薄板的拼接,按以往的经验,正反面焊接均采用CO2气体保护自动焊进行,该种焊接方法虽然使得焊缝成型美观,但也存在工序繁杂、效率底、焊接质量不易控制等缺点。考虑到CO2气体保护自动焊的诸多缺点,可以使用细丝埋弧焊技术,利用2.0mm焊丝对4-6mm薄板进行自动化焊接,大大地提高焊接效率和焊接质量。细丝埋弧焊的焊缝成型不如 CO2气体保护自动焊美观,相对而言,其焊接变形也较大。为此,经过对船体薄板结构特点和在实际船上所处位置的仔细分析,考虑焊接效率并兼顾焊缝表面成型效果的情况下,可以采用组合焊。在焊缝设计时,将细丝埋弧焊焊缝放在有结构一侧,在甲板面和通道两侧尽量设置CO2气体保护自动焊焊缝。
2.1.1.2薄板拼接工艺要求
严格控制钢板对接间隙,3mm板材拼接对接间隙不大于 1mm,6mm及以下板材拼接对接间隙控制在1.5-2mm之间;定位焊焊点直径为5mm,焊点间距为50mm,均匀分布。焊前对定位焊部位进行打磨,焊肉磨平高度约为0-0.5mm,焊点高度不能超过钢板表面0.5mm,以免影响焊缝表面质量;采用单面定位焊,先焊接定位焊面,除3mm板材需清根后焊接外,4-6mm 板材打磨后直接采用细丝埋弧焊进行焊接;平板拼接前将磁性压码或专用压板器均匀放置在焊缝两侧,磁性压码间距为 500mm左右,板材周边用马板固定,防止板材翘起。在不影响焊接的情况下,磁性压码或专用压板器应尽量靠近焊缝,待焊缝冷却后方可移开。磁性压码应采用防磁措施,避免造成焊接作业时产生磁偏吹现象,影响焊接质量;平板拼接焊接时,CO2气体保护自动焊选用0.8mm实芯焊丝,埋弧自动焊选用 2.0mm焊丝,需要注意的是此种焊接方法仅适用于4-6mm板材的拼接。
2.1.2平面板架的焊接
2.1.2.1平面板架焊接方法的选择
薄板平面板架的焊接效果是薄板成型的关键,该工序焊接方法使用不当会直接影响后续工序乃至全船薄板整体成型质量。要想板架成型效果好必须做好以下三点,即焊脚尺寸一致且趋近设计尺寸下限;板架整体受热均匀;做到焊接有序,自动角焊小车是同时满足前两点要求的不二选择,结构安装时应考虑自动角焊小车的利用率情况。在平面板架结构安装时,应将方向一致且数量多的结构先安装。一般情况下,先安装全部纵向结构,使用自动角焊小车焊接后,再安装横向结构。由于形成了十字相交结构形式,须将小车的轨道用特定的工装垫平,分段焊接横向结构。此种方法焊接的平面板架,自动化焊接量最高可达到焊缝总长的80%以上。
2.1.2.2平面板架装配、焊接工艺要求
使用专用平台装配、焊接, 平台表面平面度保证在 ±1mm/5m;平面板架结构装配间隙应控制在0.5mm以下,尽量做到“不透光”;定位焊分布均匀,间距为50mm为宜,并只在结构的一侧定位焊,不得使用拉杆固定;焊前使用厚度为25- 35mm、宽度为300mm的条形压铁,放置在预先钉焊好的结构两侧,待焊缝冷却后方可移开。为使焊接应力能够自由释放,板架边缘无需刚性固定。
2.2分段建造阶段
所谓分段建造,实际上就是分段装配,对之前一个阶段得到的部件或零件进行组装。从高速船的角度讲,这一阶段的焊接自动化表现为以下两个方面:其一,分段反造;其二,板架安装和焊接。
2.2.1分段反造时甲板结构的焊接
分段反造时,一般以甲板或平台为基本操作面,将板材直接铺于胎架上,然后进行板材拼接、划线、结构件安装、焊接等作业,其施工要点与平板的拼接、平面板架的焊接类似。不同之处是在坡口的选择上,当板厚大于或等于5mm时,对于对接板缝就可以尝试使用陶质衬垫,实现单面焊双面成型的效果;当板厚小于5mm时,就只能选择CO2气体保护自动焊进行焊接,以确保焊接质量和焊缝成型美观。
2.2.2舷侧板架安装、焊接
对于深V船型或舷侧结构线型不大的船体,其舷侧外板由于横向线型多为斜直线型或直线型,所以舷侧结构十分适合形成板架后整体安装。为了提高焊接自动化率和薄板成型质量,在设计时将舷侧结构组成平面板架在钢加阶段进行焊接,最后在分段建造阶段整体安装到分段上,这样既节省了工时又有利于薄板成型控制,所以其焊接方法与钢加阶段平面板架的焊接相同。为提高外板横焊缝的美观程度,可以采用自动焊摆头小车,使用CO2气体保护半自动焊在结构内侧焊接,外侧气刨清根,CO2气体保护自动焊盖面。此种工艺有效地杜绝了外板横焊缝的“双眼皮”问题,大大地提高了外板横焊缝的美观程度。此外,相较于手工焊缝,立对接焊缝有更好的成型效果。
2.2.3焊接规范
横向对接焊缝焊接时应满足以下规范要求:焊接电流为 90-120A,焊接电压为20-22V,气体流量为20L/min,焊接速度为280-320mm/min。对于立面对接焊缝,其焊接时应满足以下规范要求:焊接电流为100-130A,焊接电压为20-22V,气体流量为20L/min,焊接速度为260-300mm/min。
3结束语
长期以来,如何克服焊接与成型薄板时产生的各项问题都是汽车、船舶等制造企业难以攻克的一项技术难题。手动焊接时,不稳定的热力输出将会导致焊缝处的熔断金属受到内应力的拉伸,从而产生较大程度的形变。对此,行业内将自动化机械技术与焊接技术相结合,形成自动化焊接技术,以高精机械臂对焊头、焊接点进行精确控制,使薄板焊缝处受热均匀,成型更为自然,瑕疵也较少。
参考文献:
[1]王艳.焊接自动化技术发展情况分析[ J ].科技经济导刊, 2019,0(21):48-48.
[2]韩荣生,张磊,康亮.焊接技术国内外发展现状与前景 [J].中国金属通报,2019,0(2):245-246.
[3]薛泽超.钢质船舶薄板成型质量控制的现代研究[J ].科学与信息化,2017,0(22):119-119.
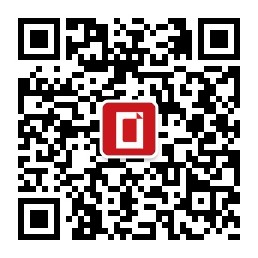