各国抢占智能制造高地
- 来源:互联网经济 smarty:if $article.tag?>
- 关键字: smarty:/if?>
- 发布时间:2017-06-20 10:08
随着新一代信息技术的兴起,以及互联网向工业领域的融合渗透,世界各国均将智能制造作为未来制造业的发展方向。美、德、日等国家纷纷提出以智能制造为核心的再工业化战略,力图通过建立先进工业生产范式掌握未来主导权。目前,智能制造已经在装备、行业应用等方面取得重要进展,各发达国家和企业的大量经验,也为我国推动落实“中国制造2025”提供了经验借鉴。
智能制造引领新一轮产业变革
技术创新集中在智能制造领域。《麻省理工科技评论》从2001年开始每年公布“十大突破技术”,这些代表世界科技前沿和未来发展方向的技术,重点是信息技术和生物技术,但自2012年起制造技术开始受到重视,当前3D打印、智能制造等制造技术影响深远,“智能化”成为近年制造技术发展的重要特征。2013年麦肯锡发布了决定未来的12大颠覆技术,其中工业物联网、云制造、3D打印/4D打印、工业机器人、大数据等是关键技术。近年来的技术创新突破,如传感技术、智能技术、机器人技术、数字制造技术的发展,特别是新一代信息和网络技术的快速发展,同时加上新能源、新材料、生物技术等方面的突破,是智能制造的技术基础,是新一轮产业革命的核心,正不断产生制造业的新方法、新模式、新业态。
不断变革制造业生产方式。随着信息技术的发展及信息化普及水平的提高,数字技术、网络技术和智能技术日益渗透并融入产品研发、设计、制造的全过程,原有的封闭的生产过程与生产模式逐步消解。如美国的“工业互联网”、德国的“工业4.0”,都是依托新一代互联网、物联网与大数据等新一代信息技术,实现价值链上企业间的横向集成,网络化制造系统的纵向集成,以及端对端的工程数字化集成,来改变当前的工业生产与服务模式。
各国加快构建智能制造创新体系,重塑制造业竞争优势。智能制造引发先进制造业创新体系的变革,在新一代信息通信技术推动下,制造业智能化演进逐步深入,高度智能化产品的商业化步伐不断加快,跨领域、协同化、网络化的创新平台正在重组传统的制造业创新体系。美国、德国、日本等主要发达国家都在政府主导下建立起制造业创新研究体系,加快推动前沿制造技术的基础研究和成果转化。如美国从2012年起投资10亿美元成立国家制造业创新网络;GE、埃森哲、AT&T、思科、IBM和英特尔等多个企业共同发起成立工业互联网联盟,全面整合联邦政府、学术界以及企业界的各方资源。
逐渐改变市场竞争格局。以3D打印、工业机器人、数控机床等为代表的智能制造先进装备技术被美、日、德等发达国家主导,中国成为智能制造装备应用需求最大的国家。如3D打印排名前4位的美国3D Systems公司、Stratasys公司,以色列Object公司和德国EOS公司,占据全球近70%的市场份额,形成了寡头垄断的市场竞争格局。工业机器人领域,全球四大工业机器人供应商发那科、安川电机、ABB、库卡几乎垄断工业机器人行业高端领域,新兴企业、互联网企业不断实现虚拟世界与实体制造业的跨界融合,中国自2013年起已成为全球工业机器人最大市场。未来智能制造装备将被更多行业更多企业广泛应用,企业发展要顺应智能化趋势,加大智能化改造力度,提升自身优势和破解发展瓶颈。
世界制造强国优先布局
美国:智能制造思想的发源地,“工业互联网”整合全球工业网络资源,保持全球领先地位。从上世纪80年代开始,美国率先提出智能制造的概念,国际金融危机后为促进美国制造业复兴,美国从国家层面就智能制造作出了系列战略部署,发布了《先进制造伙伴计划(AMP)》、《先进制造业国家战略计划》、《国家制造业创新网络》、《制造USA》等战略计划,一些机构也积极承担智能制造技术协同研发和应用推广,如美国国家标准与技术研究院承担“智能制造系统模型方法论”、“智能制造系统设计与分析”、“智能制造系统互操作”等重大科研项目工程。由美国通用电气公司发起,并由AT&T、思科、通用电气、IBM和英特尔成立的“工业互联网联盟”,提出要将互联网等技术融合在工业的设计、研发、制造、营销、服务等各个阶段中。一系列战略都强调加强政产学的智能制造创新网络,从国家层面提出加快制造业创新步伐,政府投资重点在先进材料、生产技术平台、先进制造工具与数据基础设施等与先进制造、智能制造相关的领域。目前在智能制造创新体系、智能制造产业体系、智能制造产业化应用领域、制造企业调整业务发展战略等方面都取得了一定成效。人工智能、控制论、物联网等智能技术长期处于全球主导地位,智能产品研发方面美国也一直走在全球前列。从早期的数控机床、集成电路、PLC,到如今的智能手机、无人驾驶汽车以及各种先进传感器,大量与智能技术相关的创新产品诞生自美国高校的实验室和企业的研发中心。
德国:全球制造业的“众厂之厂”,以“工业4.0”打造德国制造业的新名片。德国的制造战略重点侧重利用信息通信技术与网络空间虚拟系统(CPS,信息物理系统)相结合的手段,将制造业向智能化转型。2010年德国联邦教研部主持制订《2020高科技战略》,2013年,德国电子电气制造商协会等向德国政府提交了《保障德国制造业的未来—关于实施工业4.0战略的建议》。在德国工程院、弗劳恩霍费尔协会、西门子公司等德国学术界和产业界的推动下,“工业4.0”战略在同年举行的汉诺威工业博览会上正式推出,并作为2020高科技战略的重要组成部分。在具体实践“工业4.0”时,重点利用物联网等技术,依托强大的制造业优势,尤其是装备制造业和生产线自动化方面的优势,从产品的制造端提出智能化转型方案,为抢占未来智能制造装备市场做好充分准备。目前德国一大批企业的智能化生产和制造水平已经成为全球的典范,“工业4.0”成为德国制造的新品牌。同时,“工业4.0”也进一步凝聚了联邦、州政府、企业、民间组织等各方的力量,构建了各方协同推进的工作机制。
日本:智能制造最早发起国之一,重视技术自主创新,以科学技术立国。2007年,日本审议并开始实施“创新25战略”。这是一项社会体制与科技创新一体化的战略,为日本创新立国制定了具体的政策路线图。其中包括146个短期项目和28个中长期项目,后者以“智能制造系统”作为核心理念,大力实施技术创新项目。2013年日本推出《日本复兴战略》,鼓励汽车、信息通信设备、电子电器等制造业回归本土市场,重点发展制造业的尖端领域,加快大数据应用、机器人、3D打印技术等的发展,并通过减税、租赁补贴、技术攻关等促进科技创新。2015年公布《机器人新战略》,起初主要有两大目的,即“扩大机器人应用领域”与“加快新一代机器人技术研发”。未来将大力推动大数据、物联网等企业向传统机器人产业的涉足,使机器人开始应用大数据实现自律化,机器人之间实现网络化。现在日本通过智能制造装备有效地缓解了用工短缺,制造业成本大幅下降,在汽车制造、电子信息、工业机器人等领域保持全球竞争优势,通过减税、补贴等手段使得智能制造技术应用环境和制造业创新人才得到改善。
典型企业加速发展智能制造
西门子:全球智能制造的先行者。西门子一直是自动化领域的佼佼者,为顺应产业发展新趋势,进一步将数字化作为未来的战略重点,最早提出“工业4.0”概念的机构和组织之一,得到了世界各国的广泛认可。西门子的智能化战略主要包括三个方面:一是搭建了统一的数字化企业平台Teamcenter,将所有产品相关的信息和技术充分整合。二是建立开放式的统一标准,实现各种设备和部件自发地与工作环境相连接,实现“即插即生产”。三是打造“数字化双胞胎”,从产品、生产工艺和设备数字化三个层面,形成基于模型的虚拟企业和基于自动化技术的现实企业镜像。目前,西门子已经成为实践工业4.0的标杆企业,受到广泛关注。西门子安贝格电子制造工厂,目前可实现年产零部件100万件,即平均1秒生产一个产品。西门子成都工厂,通过智能化改造,已经节约了90%的编程时间。
通用电气:以“工业互联网”为核心加快战略转型。作为美国老牌工业企业,通用电气基于自身优势,充分利用互联网与信息化技术挖掘生产潜力,于2012年提出了“工业互联网”的发展战略。希望在全面互联的基础上,通过数据流动和分析,提升技术创新和服务能力,创造新的增值空间。通用电气在工业互联网方面的产品和服务布局主要包括三个方面。一是推出了工业分析专门平台Predix及解决方案Predictivity。二是以航空、电力、医疗等熟悉的领域为切入点,推进工业互联网的项目落地。三是对自身短板和业务拓展需求,收购优质企业填补空缺。通用电气已经先后完成了对MTL公司、Pivotal、CHCA、API Healthcare、阿尔斯通等相关部门的收购、并购或入股,极大地拓展了业务覆盖范围。目前,工业互联网的概念已经被广泛接受,盈利能力逐步显现。据统计,截止到2015年2月,通用电气已经销售大约43种“工业互联网”产品,营业收入超过10亿美元。
丰田公司:推进“人机合一,以人为本”的智能化。丰田是“精益生产”管理理念的重要来源,其智能化战略也体现着浓厚的管理学特征。丰田一方面继续强调精益化生产,即所谓的“just in time”模式,利用信息化网络化手段进一步提升系统控制能力,提高各个环节的协同制造能力,逐步实现生产智能化;另一方面强调人的决定性作用,将人的作用与权限置于机器之上,推进“带人字旁的自动化”。为此,丰田建立了一套覆盖全流程的数据采集、存储、分析系统,在赋予机器进行决策权限同时,赋予操作工人更高权限,可以在机器出现问题时停止生产。这种模式既提高了员工主观能动性,也符合日本与丰田的实际情况,充分发挥了丰田既有管理优势和人力资本,有效提高了公司运营效率。
多管齐下完善智能制造产业体系
政府引领,为智能制造提供良好政策环境。我国应加强政府引领作用,学习美国、德国、日本等国家政府高度参与,同时配套税收优惠、研发资金、先进产业专项基金、人才培养、创新激励等方面政策的经验做法,强化骨干企业、科研机构、高校的合作,充分调动智能制造产业联盟各类资源积极性,发挥各类智能制造产业基金作用。注重智能制造产业先进技术的前沿布局,特别是满足未来智能制造模式对大数据和网络基础设施的需求。要加快建设完善信息安全防护体系和相关法律体系,保障开放条件下工业互联网的数据安全和保护,修订相关贸易保护规则。建立智能制造人才培育体系,政府与企业联合对在校大学生进行智能制造专业化人才培养,同时引进全球智能制造业高层次人才。
标准先行,抢占智能制造产业发展先机。德国推进“工业4.0”是标准先行,重视标准对产业的贡献率仅次于资本。我国要注重把握智能制造发展的特点和规律,学习借鉴德国“工业4.0”标准化路线图,加快建设包括智能制造标准化路线图、智能工厂及智能产品技术标准、智能化数字化网络化“三化”融合管理体系等在内的智能制造标准化体系。在一些规范和协议尚处于空白的领域,要及早抢占先机,以标准促发展。
企业主导,发挥主观能动性。美国的“工业互联网”、德国的“工业4.0”战略中GE、ABB、宝马、巴斯夫等重点企业是发起者、引领者和实践者,成为智能制造的市场主体。我国推动智能制造过程中不可忽视企业的主导作用,要突出企业开展集成创新、制定标准、产业化、试点示范的主体地位,大力推进以企业为主导的产学研合作,组建龙头骨干企业为引领的产业联盟。让企业在不断实践中寻求市场,实现提质增效的目标。
推广应用,加强典型企业的试点示范。加强新产品新技术推广应用的资金支持,积极鼓励企业应用智能装备和数字化技术,实现生产的智能化、管理的数字化、服务的信息化。对尚不具备条件的企业,可以有选择地对部分厂房和车间进行智能化和数字技术的配置和应用,打造数字车间、智能工厂的样本车间,再逐步有序全面推进。把握工信部“智能制造试点示范专项”契机,开展离散型智能制造、流程型智能制造、网络协同制造、大规模个性化定制、远程运维服务5种智能制造新模式试点示范,根据企业发展需求,定期组织召开经验交流会、现场会。
重视合作,加强企业间、国际间的交流。依托我国的制造业基础优势,充分挖掘我国智能制造的潜在市场,建立企业间、国际间交流合作的公共服务平台和工作机制,重点建立工业机器人、数控机床、3D打印等智能制造领域的公共服务平台。鼓励、支持国内有条件的企业在国外建立工业园区,与国外智能化程度较高的企业展开合作,吸收国际先进研究技术经验。建立国家智能制造创新中心,形成集政府、企业、科研机构、高校、平台、联盟等各方资源的智能制造产业生态体系。
总之,我国应广泛借鉴、多管齐下,建立健全智能制造产业生态体系,为推动落实“中国制造2025”提供坚定支撑。
文/张洪国 黎文娟 邵立国
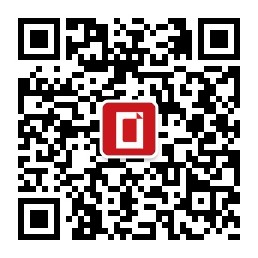