徐工:擎起“国家臂膀”
- 来源:中国品牌 smarty:if $article.tag?>
- 关键字:荣誉,中国质量,升级 smarty:/if?>
- 发布时间:2014-11-18 09:42
如今中国在工程机械的核心零部件等方面仍然存在瓶颈,但徐工集团以及中联重科、三一重工等,已经组成了中国工程机械向世界挑战的“集团军”
编者的话:为深入贯彻党的十八大和十八届三中全会精神,切实把推动发展的立足点转到提高质量和效益上来,不断总结提炼我国企业的质量管理经验,推动我国向质量强国、品牌强国目标迈进,以质量升级助推转型升级,打造中国质量升级版,本刊特别推出“品牌培育·中国质量奖”栏目,希望他们的经验能够带给更多企业以启示。
2013年12月,我国质量领域最高荣誉的“首届中国质量奖”在北京颁奖,徐工集团工程机械股份有限公司(简称徐工)荣获首届中国质量奖提名奖。在这引人瞩目的重大奖项的背后,是徐工集团工程师团队的默默付出。
2014年9月中旬,在江苏徐工集团徐州重型机械有限公司的调试场地,一台起重能力4000吨的起重机正在组装,准备调试。
尚未安装吊臂等部件,这台机器仅履带就有3米多高,大小两台履带式底座,面积超过一个篮球场。
作为主设计师,徐工履带起重机研究所所长孙丽表示,4000吨起重能力是指在吊臂20米范围内,可以将约2260辆奥迪A6轿车同时吊起。如果让这些车首尾相连,从北京的建国门可以一直排到公主坟。
这是徐工集团生产建造的第二台同型号起重机,未来很可能用于中国大型核电工程建设。此前,2013年交付的首台4000吨起重机,已服务于石油化工领域的大吨位吊装工程。
这是一种前所未有的国家力量,它凝聚着几十年来工程机械领域的苦心积累。以这个“巨无霸”为代表,用徐工集团董事长王民的话说:“已经登上了8000米的高度,还剩下几百米的努力,就可以登顶珠峰。”
在王民和孙丽心中,将来用户在徐工集团和卡特彼勒、利勃海尔这样的国际巨头间选择时,最终觉得徐工集团的产品更好一点儿,“就成功了”。
这可能也是中国工程机械行业漫长征途中最艰难的篇章,“用5到10年,咬咬牙就过去了。”王民对我们说。
本不喜欢“硬邦邦”的工程师
这台4000吨级起重机,全称是徐工XGC88000—4000吨级履带式起重机,88000指力矩88000吨米。
力矩,在物理学上是指使物体的重量乘以到转轴的距离。同等重量,力矩越大,则显示起重机的起重能力越强。在此之前,国际上的起重力矩设计极限为60000吨米。不过,孙丽甚至不愿意回忆这台“世界之最”的设计过程,“觉得每次回忆都是一种伤害。”
1990年考入江苏扬州大学工程机械专业前,希望靠高考“跳出农门”的孙丽本想进入师范院校,做教师。几分之差,错失梦想。
“除了第一志愿,其他随便填,那时候根本不知道机械设计到底是干什么的。”她承认,开始并不喜欢这个“硬邦邦”的专业,觉得服装设计之类更好,“可以把自己打扮得很漂亮。”
不过,按照她要强的性格,在工程机械专业的成绩仍然很好。
孙丽毕业回到家乡徐州,进入与自己专业最对口的单位——徐工集团,很快被安排参与50吨履带起重机的设计。
大型履带起重机在国外历史超过百年,但中国自上世纪80年代才从国外引进。孙丽进厂第二年,经过消化、吸收的艰苦努力,徐工集团生产出第一台具有自主知识产权的50吨履带起重机。
起重能力是起重机最重要的衡量指标。1998年徐工集团将这个数字提升到150吨,2004年前后达到300吨,“当时称为神州第一吊,是国内最大的吊车项目。”
此后,随着基础设施建设高潮直接拉动工程机械发展,徐工集团的大型履带起重机也从450吨、850吨,一直发展到2000吨和4000吨。
如今,孙丽认为:“工程机械项目的确不像做服装,服装展示外在美,而工程机械是内心丰富。”
当年与孙丽同期进入徐工集团的同事,都已转去销售和生产管理岗位,只有她一人仍然留在研发一线。
2009年,风电、核电等超大型能源工程立项。而之前此类工程的吊装市场一直为国外企业垄断。为了解决这个问题,国家能源局召集国内最好的机械工程厂家开会讨论。
当年年底,徐工集团开始着手调研大型吊装项目。某日在徐工集团建设机械分公司副总办公室,孙丽被问道:“公司有个大项目,你可以干吗?”
怎么描画“巨无霸”
这个“大项目”,就是后来打破了多项世界纪录的XGC88000履带起重机。
根据过去数年的积累,孙丽本没觉得有多大压力。到2010年开始做方案的时候,她才发现困难非比寻常。
“比如说我们画一张脸,一个鼻子、两个眼睛,怎么画都有类似的原型。但这个项目没有原型可以参考。”孙丽说。
作为全球第一强大的起重机,“没人告诉我要画什么样的脸型,画几个鼻子几个眼睛,但结果已经定好,就是要吊起4000吨重量。”
吊起4000吨重量,必须有至少4000吨的配重对称“压着”。这就有接近1万吨的重量,这样的“巨无霸”还要移动——这已经不仅仅是数量升级的问题。
“没有思路的时候,我就去研究桥梁、建筑。”孙丽说。这些内容已经超越了工程机械的范畴。
在研究了所有横跨在长江上的大桥之后,孙丽发现,那些拉索式大桥,桥塔的形状要么是H形,要么是A形,“桥塔的受力模式,和履带起重机的受力模式相似,那么它们的结构也应该有相通之处。”
XGC88000履带起重机被设计为前车、后车两个部分,中间用横梁连接,在工作时,通过约20米长的4组履带,实现整车强大的吊装功能。
为解决一车多用及接近5000吨自重的运输问题,XGC88000履带起重机在设计时就采用了模块化的方式。
大吨位起重机通过自身部件组装,变形为一台小型起重机,以适应不同的工作需求,提高设备的利用率及运营经济效益——这个课题是世界工程机械行业的梦想,但一直无法真正实现。
“模块如何划分,功能如何实现,很多问题都难以解决。”孙丽说,这个拆分和重组,远远不像小孩玩积木那么简单。
她也曾直接拒绝业主单位的类似想法,“干不了”,因为这只是一个概念。
但是,为解决起重机的经济效益问题,这一设计必须实现。“所有部件的设计理念都得发生变化,都得是组装式的。如何实现模块通用,同时具备大车与小车的功能,具体实现大车与小车的转换,做了几十个方案,结果还真做出来了。”
看到最终成果,孙丽本人也觉得神奇。这个装备在2012年首次亮相时,好评如潮。孙丽自己则寄予了特殊的感情,“担心用户不会用,担心自己宝贵的东西让别人用坏了。”交付之后,每次吊装她仍然要赶到现场,看见路面不平,她都会向施工方提出意见。
被拒签的“小学生”
时间回到1989年,孙丽开始学习工程机械前一年,作为徐工集团重型机械厂党委副书记、纪委书记,王民第一次被派到国外。那是去德国的利勃海尔参加为期3周的起重机技术培训。
摆在王民眼前的是漆成黄色的整洁的起重机,一排排如艺术品。
那时的利勃海尔是全球最先进的起重机产出地,在它的产品达到800吨水平时,中国才生产50吨级的产品。
关键是,那时国内企业都以“卖掉产品”为目标,“没有质量意识,也没有用户意识。”
王民回忆说,上世纪90年代初徐工集团曾经出口过一批产品,下船后,客户问为什么送来二手货。
“漆掉了,生锈了,包括电镀的油缸、螺栓都锈了。”王民说,客户最终拒收。“那时西方已经进入奥迪时代,我们仍然开着手扶拖拉机。”在利勃海尔的这次经历,有一个令王民终身难忘的情节。
德国老工程师曾热情地告诉他们:“你们用摄像机全录制下来也行。”但是午饭时,中方翻译人员说,老工程师后边还跟了一句话:“反正你们再怎么学,也永远做不到。”
“但是他们不让日本人看,因为日本人学得太快了。”王民觉得,德国人向他们毫无保留地展示,“是觉得那是小学生看研究生的作业”。
这件事,在徐工集团的工程师中传讲了十几年。如孙丽一般的年轻工程师,无一不曾被此激励过。
2006年的上海工程机械展览会上,利勃海尔的高管在看到徐工集团的200吨、300吨全路面起重机后说,在中国找到了真正的对手。
2011年,王民随徐州市领导去美国卡特彼勒参观。后者是世界上最大的工程机械和矿山设备生产厂家。对方却把他从进厂参观的名单中划掉。
“但是,我很骄傲。”王民说。
此前在2009年,向来标榜最开放的“工程机械奥林匹克”慕尼黑宝马展览会,徐工集团派出上百人的技术团队赴会参观学习,结果签证一再被延期,最后许多人被拒签。“尤其是主任设计师以上的工程师,全部被拒签。”王民回忆。
国家工业基础能力的瓶颈
从“小学生”到赢得尊重,历程艰难而漫长。
在“买图纸的时代”,中国人显得窘迫。“吊臂安装后,伸缩时不平顺。”徐州重型机械有限公司副总经理单增海说,有一次组装,吊臂伸开后误差甚至达到四五米。
为了解决吊臂问题,用4根钢板焊接成四角形,以实现吊臂伸缩。但西方国家已经实现了六边形吊臂,“吊臂的边越多,受力越合理。”单增海说。
到上世纪90年代末期,西方制造业实现了圆形吊臂,中国在2004年也有了这一技术。
80年代之前,中国起重机行业进展缓慢。90年代,徐工集团开始与日本、德国企业合作,“当时叫技贸结合,引进技术,同时作为销售商销售他们的产品。”
但以世界先进水平为目标的自主研发也在此时起步。徐工集团的第一批自主化产品,其主要零部件已可以实现在国内配套体系中组装、生产。
最终拉动中国工程机械行业历史性发展的,是新世纪以来的工程建设高潮。徐工集团起重机的销售额也从1亿多元起步,5年内销售额增长高达80%以上。
可是,单增海也承认,西方先进企业的产品技术仍领先不少。
国家工业基础能力不足,带来的烦恼很多。
“不太相信命运,喜欢抗争,只相信自己的努力、奋斗”的王民坦言,如今中国在核心零部件等方面仍然存在瓶颈,“现在普通产品,市场容量大的产品,包括零部件,一般国内都能制造。但是涉及大型、超大型设备,特别是在可靠性上有严格要求的,国内企业仍然难以提供配套。”
单增海举例:发动机、液压设备、变速箱、高强度钢材等方面与西方差距不小,部分零部件仍然只能依靠进口。
以高强度钢材为例,几年前国内刚刚研发出拉断力为96公斤级的钢板,但柔韧性很差,折到90度左右就会开裂。西方企业早已实现130公斤级水平,在几乎对折的情况下也不会开裂。
此类高强度钢材价格昂贵,96公斤级进口价格原为每吨3.5万元。国内实现这一技术后,进口产品降价到3万元以内,而自主产品价格不足2万元。
“越涉及基础问题,研究周期越长,市场见效越慢。”单增海说,“我们不可能去投建一个钢厂,这需要国家基础工业的整体进步。发动机、变速箱,情况类似。”
但徐工集团以及中联重科、三一重工等,已经组成了中国工程机械向世界挑战的“集团军”。
“20年前,看国际工程机械类同行,完全是仰视。”王民说,现在,“基本可以平视了”。只是,“我们很多大型国有企业、政府,仍然迷信国外,这和多数国家对待自己国内企业的态度完全不同。在重大装备上,国家和政府更要关注国内的企业和产品。”他认为。
而孙丽则回忆起读书时校园里张贴的宣传画:一个工程师戴着安全帽,胳膊下夹着一摞图纸,匆匆走向车间。这个画面曾令她久久憧憬。“现在我也是这个样子,真的很好。”
葛江涛 文
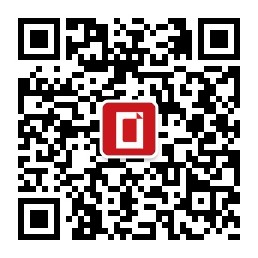