制造业升级的陷阱在哪里
- 来源:新经济 smarty:if $article.tag?>
- 关键字:德国工业4.0,制造业 smarty:/if?>
- 发布时间:2015-12-16 14:01
制造业转型和中国制造2025,我相信大家都不陌生。被诸多网友拿出来类比的德国工业4.0看上去很美,反而摆在我国制造业升级路上的问题仍然是困难重重。是否制造业大国和制造业强国之间就只是一线之隔?是否全面推进自动化升级或者互联网+之后就能够标志着我国的制造业已经“追英赶美”?中国和德国这两个制造业国家之间的差距是否只是所谓的德国品质?是否我们在全面提升品质之后,就能够标志着中国制造业已经进入世界强国俱乐部?
事实上,凡此种种的诸多问题,我认为最大的核心在于,网友错误地将科研和工业规划当成了一回事,然而事实上是工业只要有制度和资本就可以产出,而科研则需要付出更多。
事实上,中国的制造业模式,严格来说,与80年代的日本非常相似,我们引入西方成熟的技术工艺,让最优质的老师来教--就像我们引以为豪的高铁,当初谈判的筹码是,外国老师教出来的中国学生如果不达标,那么不给你们结账--但是这种技术引进的模式,并不意味着我们就真的具有了相应的技术水平。
制造业的科研究竟有多难?大家不妨看一下我们的大飞机项目,在西方的波音、空客已经满天飞的大环境下,一个跨越了数十年的项目,多次叫停,多次重启,即便C919真的能够成功,其关键零部件--航空发动机的技术仍然是受制于西方。这就是研发的差距,而这一差距的核心又是什么呢?是资本?是市场?都不是,我认为中国制造业转型的症结,最关键的在人才。
事实上,与很多产业所谓投入资本就能引发质变有着根本不同,制造业的技术积累是一个非常漫长且循序渐进的过程。我们还是用德国来做对比,德国制造业的基础是德国人引以为傲的学徒制,一个人从十几岁开始学手艺,学成后得到国家认可的学历,然后几十年如一日从事同一件工艺,精益求精,再将自己的技术一代代薪火相传。德国工厂的车间里,处处可见五十多岁还在流水线上兢兢业业的工人,工地上随时可见六十多岁还在开挖掘机的师傅。这些人将自己的一生贡献给一门手艺中的一个环节,他们的经验对于行业的发展和进步是巨大的财富。
与很多大众更容易接触的服务业完全不同,制造业的进化,从工程师脑子里的想法,到车间上每一个焊接点的工艺,到产品使用时的现场条件和环境变量,再到售后维修时每一个时间节点可能造成的种种差异,其中的各个环节千差万别,这些都需要一线人员的经验来完成技术上一点一滴的积累。
从这个角度来说,中国的制造业进化所面临的最重要问题,是人才机制导致的断层--工程师和基础工人之间的沟通断层。对于欧美国家而言,他们的产业升级是遵循着我们说的循序的过程而启动的。工人到熟练工人,后者的量变累积启动了一次次的质变--带动着工业化、自动化的升级。换句话说,西方国家通过不断累积量变来寻求质变的工业升级,拥有非常坚实的传统制造业基础和人才基础。然而有如中国的技术引进型国家,通过技术引进而引发质变,最终会形成的就是技术应用和技术研发之间巨大的断裂带。这种断裂带的成因,最大的根源在于基础工业的累积不足,而更核心的问题就是人才的消耗量根本不在同一个水平。
如果从这个逻辑上看,当前的中国制造业也处在这样一个时代,一方面我们缺乏有经验的高级技术工人,另一方面由于自动化发展,我们对于基层工人的需求又越来越小,同时我们又没有一个培训体系来弥补这中间的断层,也没有一个完善的保障体系来保护工人职业生涯的可延续性。
而之所以出现这种模式,恰恰也是源于资本端对于制造业领域的误解。如果未来仍然仅仅是抱着“多快好”的心态来主导制造业升级,那么最终的途径,恐怕仍然是无法脱离80年代日本的尴尬梦魇。
宋阳
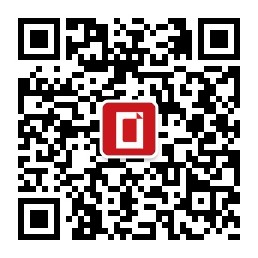