双桃的百年新韵
- 来源:商周刊 smarty:if $article.tag?>
- 关键字:双桃精化,海湾集团 smarty:/if?>
- 发布时间:2015-09-14 12:35
在青岛工业百年变迁过程中,双桃精细化工(集团)有限公司总是扮演着最忠实的“见证者”,它既承载着许多青岛人的城市记忆,也带动过周边商圈的繁华演绎。
白驹过隙96年,青岛已沧桑巨变。脱胎于1919年民族染料企业的双桃精化,如今已变成了很多人口中的“老企业”。自2008年以来,这个烙印着百年荣光的“老企业”,带着对城市进化的至深理解,正在经历着一次自我进化,从灰色变成绿色,选择告别“旧化工时代”,将百年辉煌烙印在重新矗立的工业新区上,定格于新厂区搬迁的记忆之中,迎来一次具有时代意义的变迁。
追忆百年
对于很多青岛的老市民来说,双桃精化不仅仅是一家化工企业,更像是一个辉煌时代的符号。1919年,“民族染料第一家”——维新化学工艺社成立,从此由一个小作坊做大做强,成长为染料行业当之无愧的龙头企业。
翻开青岛工业文明史,不难发现双桃精化曾经的光荣节点。在那个风雨飘摇的时代,国外企业独霸着中国染料市场,肆意盘剥,牟取暴利,中国染料企业艰难地在夹缝中生存,与外国企业博弈,一个个打破它们的技术垄断;建国初期,我国所用的染料大部分为进口货,青岛染料厂(双桃精化前身)积极研究改进硫化蓝中间体亚硝基酚合成的部分操作方法,使硫化蓝新产品迅速在国内推广,成为当时国内生产蓝色服装的主要染料;近年来,双桃精化开发了新一代尤丽特系列、尤丽素系列产品填补了国内高档染料的空白,获得了国际环保纺织协会颁发的染料、助剂生态安全证书,产品的市场占有率全国第一、全球第二。长久以来,无论是产量、利润,还是技术水平,双桃精化都稳稳坐着第一把交椅。
经历过计划经济时代的辉煌,双桃精化也遭遇了向市场经济转型的过程中的阵痛。在产能过剩的恶性竞争中,资金不足、设备陈旧、操作落后让双桃精化的境况雪上加霜,产销量一路下滑,市场空间不断萎缩。发展空间、环境保护两方面的严重限制,更让企业的决策者一度迷茫于双桃精化的未来。
海湾集团董事长、总经理李明曾这样说过,如果一味沉浸在百年企业的荣光中,抱着“第一”的名号不放手,双桃精化就没有前进的空间。经过2013年7月的调研,企业的决策者认识到,单纯的复制是没有出路的,唯有全方位的创新,才能质变一条新的出路。
现代工业新图景
自2010年启动搬迁以来,5年艰辛不寻常。双桃精化人认为,搬迁不是所有建筑的大拆大建,不是对历史的遗忘与断裂,而是空间的重构、产业的升华。在新河生态化工产业园内,崭新的设备与已建成及在建的厂房见证一个化工旧时代的结束和一个现代工业新图景的开始。
在双桃精化人眼中,“技术国际化、装备大型化、环境生态化、管理现代化”的“四化”要求,不仅是流于书面的口号,更是一直奋进的方向。
瑞士的离心机、丹麦的干燥机、韩国的搅拌机、意大利的裂解炉和包装系统……在新厂区,双桃精化的主要设备皆是来自国际上最先进的设备。“在工艺的自主研发后,我们与四十几家国外一流的装备生产厂家交流,量身定做了产能高、能耗低的最适合新厂区的生产设备”,双桃精化总经理赵秀平说,“新生产线已经实现了从投料到产品包装的DCS全自动、连续化控制。7月31日投料生产的二乙芳胺生产线是国内第一条全自动生产线,在国际同行中也是领先的。”
事实上,早在上世纪60年代双桃精化已经开始生产二乙芳胺和吡唑酮。五十几年过去了,限于空间不足、设备老化、生产线小,这两个产品依旧全部采用手工操作。这次搬迁,给予了双桃精化千载难逢的机遇——生产技术脱胎换骨,重塑市场价值。
“阻碍二乙芳胺生产线全自动化的最大难题,是产品的色光难以统一的问题”,赵秀平告诉记者,“二乙芳胺在生产时,一批乙醇要套用10批产品。各批产品外观都有差异。为实现产品色光的统一性,需要将这10批产品进行拼混。这对整个工艺的自动化控制提出了很大的挑战。”经过一次又一次的实验摸索,双桃精化的技术人员通过惰性气体保护实验、对产品外观、质量、母液残余量等数据的跟踪对比,最终解决并砍掉了拼混工艺,解决了影响二乙芳胺项目全自动、连续化控制的最大的难题。“在新厂区的生产线上,不用拼混,色光基本实现每批一致。不但可大大降低半成品库存资金占用压力,降低生产成本,提高市场竞争力,而且使全自动、连续化生产成为现实。”赵秀平自豪地说。
据赵秀平介绍,目前在新厂区1.5万吨/年二乙芳胺项目生产线车间里,包含包装人员在内的实际操作人员只需12人。即使到8月底,1万吨/年吡唑酮项目正式投料试生产,二乙芳胺、吡唑酮人员定员也只有24人,比原来减少120多人。可以说,产能提高了5倍,人员却缩减到原来的六分之一,45亩地、24个人,创造了和老区282亩、700人几乎一样的价值。也难怪双桃精化的一位老员工会感叹:以前是忙得像陀螺,各处都要盯,如今所有操作都是自动化控制,人闲下来了,效率却大大提高了!这是以前想也不敢想的事情。
环保先行
2015年1月1日起施行的《环保法修订案》(新《环保法》),被认为是一部“不环保,罚破产”和“不达标,别生产”的最严《环保法》。它的出台,让高耗能、高排放、高污染的化工行业感到了深深的寒意。尤其对染料行业来说,它的影响是全产业链的,并不仅仅是体现在某一两个产品上。从上游到终端的各个产品之间,苯二胺、还原物、H酸、分散染料和活性染料等均有不同程度的环保问题。在愈加严苛的环保标准下,企业面临着又一轮的洗牌。
其实,早在上世纪90年代中后期,青岛化工企业就因环保问题主动停产1家企业,搬迁两家企业,搬迁产品7个。一方面节能减排,一方面调整产品结构,走低耗能、低污染、高附加值之路,青岛化工一路摸索前行。对于双桃精化来说,环保同样是一个不容逃避的社会责任。李明多次强调,“如果不能从根本上解决环保问题,不管项目能产生多少效益都不能上马。弄虚作假,早晚会出问题。”
从新厂区的规划布局到基础设施建设,从建筑设计到设备引进,双桃精化都按照严格的环保标准,塑造一个全新的园区生态,打造国内一流的绿色新形象。在搬迁过程中,双桃精化人千方百计的研究废水、废气、废渣的治理方案,多项循环经济新技术申报了国家专利。
“新厂区建设的污水处理厂,采用了先进的菌种处理技术”,赵秀平告诉记者,“经过初步处理后,废水耐盐量为2.5%-4%。再通过膜处理,产生的一部分中水会回到生产系统应用,而另一部分的耐盐量提高到8%-12%的高盐废水将进入MVR系统蒸发处理。经过蒸发冷凝后的冷凝水回归生产应用,剩余的高浓度氯化钠则可自用或外卖,基本实现了零排放。”同时,为了从根上处理污染问题,双桃精化还投入大量的资金建设了液体焚烧炉和固体焚烧炉。其中,固体焚烧炉在处理本厂固体废料的同时,也满足整个园区固废处理的需要。
令人惊讶的是,在双桃精化3期将投入的分散染料项目3亿元的投资中,环保投入占据了一半的资金,这在许多企业是完全无法想象的。赵秀平告诉记者,双桃精化可以说是我国分散染料的鼻祖。过去迫于生产过程中产生的废硫酸、废硝酸难以处理,污染太重,不得不在90年代末下马。一次偶然的机会,李明在朋友的微信中发现了一篇关于国外通过萃取等化工工艺将低浓度的废酸转化成合格的酸产品的文章,意识到分散染料的污染问题解决有望,迅速安排相关的技术人员学习。“通过工艺提升与新技术的应用,污染问题在很大程度上得到了解决,再启动分散染料项目也就没有了后顾之忧”,赵秀平说。
值得一提的是,作为新河生态化工产业园最早开工建设的企业,双桃精化还承接了热电联产项目建设,在工艺上也遵循了循环经济的模式。众所周知,煤炭中含有硫,在燃烧后会产生大量的二氧化硫,污染严重。双桃精化创造性地采用了氨法脱硫工艺,利用氨水与二氧化硫反应,产生含有亚硫酸铵和亚硫酸氢铵的还原液,而这正是8月底将要投入试车的吡唑酮的原料;同时,在吡唑酮生产中会产生含胺的副产物,通过蒸胺工艺生成氨水,则可以重新进入热电厂用于脱硫脱硝,真正实现了废弃物的无害化利用。
当下,中国的化工企业正在经历一场紧迫的转型试炼,资本、技术和安全正在遭受前所未有的挑战。在双桃精化的精心选择下,一大批创新项目正接踵而至。承载着几代染料人的梦想,双桃精化人正迎来跨越发展新的百年。
本刊记者/李菲
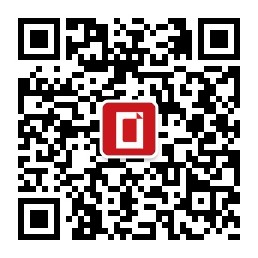