货车故障轨边图像检测系统实践与探索
- 来源:职业 smarty:if $article.tag?>
- 关键字:背景,安全,铁路,车组 smarty:/if?>
- 发布时间:2011-08-08 09:33
安全是铁路运输永恒的主题。我国铁路近年来经历多次大规模提速,客车速度不断提高,货物重载列车开行数量增多,列检作业保证区段延长,过去传统、粗放、人控的安全防范体系,已不能适应铁路跨越式发展的需要。
为加强货车安全防范系统的运用,确保提速安全的持续稳定,优化重组列检的作业方式,实现列检作业由静态向动态的逐步转变。根据铁道部要求,制定TFDS人机分工方案并组织了实施。
一、研制的背景
长期以来,铁路货车的运用维修手段陈旧,技术落后,列检作业基本靠检车员“手摸、锤敲、眼看、耳听、鼻闻”,列检作业人员钻入、钻出列车车辆,不仅效率低,而且无法保证作业质量。随着货物列车高速、重载、大密度的开行,势必造成各列检所日常检修任务的增加、工人劳动强度的加剧。而列检技检质量易受气候、职工素质、心理状态和人体疲劳程度等因素的影响,易给行车带来安全隐患。综上所述,传统的列检作业方式越来越难适应形势发展的需要。
二、方案的制定
根据新《铁路货车运用维修规程》(以下简称《运规》)第424条之规定,每个TFDS探测站的列车动态检查至少设1个动态检车组。每个动态检车组可采取全列分区域或分段包车的方式设置检查工位,并由动态检车组长或工长发出指令,系统自动分车、分段或分列。分区域设置检查工位时,须按转向架侧架、转向架底部、车钩缓冲部位、车底部等检查区域分别设置。包车设置检查工位时,每个检查工位须按转向架的仰视—转向架的侧视—车钩缓冲部位的仰视—车钩缓冲部位的侧视—车底部的仰视的顺序进行图像检测。1个TFDS动态检查室的每一列车的动态检查作业须由1个动态检车组完成;在确保列车到达列检作业场前或通过车站前完成列车的动态检查作业的前提下,应根据列车的区间运行时间、列车编组数量、TFDS探测站的安装位置等具体情况,确定检查工位数量;根据列车运行图规定的车流密度、列车追踪间隔时间以及检查径路数量或探测站数量等确定动态检车组数量。
明确动态检车组长、动态检车员、列检值班员、现场检车员在TFDS故障发现、预报、传递及故障确认等方面的岗位职责。列检作业组与动态检车员的配备满足技检时间和检修车的需要。考虑到各部位图像检查部件数目不同。为均衡各工位机的工作量,对每个TFDS动态检车组配备四至六名动态检车员,现场配备一定车辆故障确认人员。并制定一班、一列、一辆作业标准及TFDS动态检车员发现故障预报、确认及反馈作业流程。根据新《运规》TFDS-1动态检查程序标准(1)侧架“凹”字检查法,(2)车钩缓冲部位“e”字检查法,(3)车底“三”字检查法,(4)转向架“Z”“8”字检查法按照顺序进行检查。
三、实施情况
以济南铁路局济南西车辆段济南下行运用车间下到列检作业场2010年1月TFDS系统检测汇总为例。
1.综合使用情况
2010年1月1日8:30至2010年2月1日8:30,系统共通过货物列车1881列计99510辆,检测1842列计97404辆,日均检测59列3142辆,检测率97.93%,共预报各类故障18688件,日均发现故障603件,百辆故障发现率19.19件。
2.故障分类对比
故障分类对比情况见表1。
3.故障情况分析
对TFDS动态检查与人工静态检查发现的情况进行对比分析,可以发现以下现象:
(1)摇枕裂损、侧架裂损、制动梁裂损、承载鞍前端裂损、轴箱前盖裂损、轮缘缺损等故障,TFDS发现的故障比现场发现的少。其主要原因为上述各种部件裂损(特别是裂纹)、从TFDS拍摄的图片大部分无法分辨出来(TFDS拍摄的图片与实际的比例相差很大);另由于阳光干扰及设备不稳定,致使相应部位图片不清晰或丢失(图1),室内检车员无法判断。
(2)钩缓装置破损等故障室内检车员发现的基本占现场发现的50%左右。对于钩缓装置破损故障比裂损故障的实际损伤程度大,在图片上可以看出来,但由于阳光干扰,尤其是晴天对光或背光时,钩缓部无任何遮挡,图像或者太白或者太黑,动态检车员无法正常看图,这是导致钩缓装置破损虽然可以直观看出,但占的比例较小的主要原因。
(3)关门车故障,枕簧窜出、丢失以及其他各类配件丢失、折断、弯曲等故障,由于本身较容易发现,在设备性能稳定的前提下,动态检车员发现情况基本与现场检车员发现的故障持平或比例偏大。
(4)手制动机拉杆链丢失、闸瓦插销丢失、圆销开口销丢失(如图1所示)这类故障,TFDS机检较人工检查发现件数多,TFDS机检方式优于人工检查方式。
(5)对于拉环丢失、转8G型转向架交叉杆下盖板裂损弯曲、上作用式车钩钩舌销折断、制动阀及管路故障、各风缸堵丢失、折角塞门手把丢失、敞车钢地板破损、低磨合成闸瓦折断、附加杠杆丢失、截断塞门手把关闭、折角塞门手把丢失、ST1—600型闸调器控制杠杆丢失等12类故障,2种作业方式发现件数一致。
(6)固定链条式手制动机链条滑轮丢失(阳光干扰时TFDS无法发现)、滚动轴承渗油(渗油量小时TFDS无法发现)、缓冲器弹簧盒盖破损(由于缓冲器处于牵引梁内部且受钩尾框与从板影响,裂损故障小时TFDS无法发现)等3类故障,TFDS机检方式不如人工检查。
(7)车轮辐板孔周向裂纹、车轮踏面剥离、车轮踏面擦伤、踏面圆周磨耗超限、枕梁腹板裂纹、枕梁翼板裂纹、心盘纵裂纹、闸瓦厚度超限、制动软管局部凸起、闸瓦托磨损、制动缸堵丢失、复位弹簧丢失等12类故障,不属于TFDS动态检查范围,需要进行人工检查方式。
四、实施的效果
释放了列检劳动生产力。现场检车员在到达列车技检作业时不再钻入车下检查,不仅减轻了劳动强度,而且将工作人员充实到始发列车和动态检测作业中,使劳动组织更加科学合理。
TFDS作为防范车辆故障的重要设备,发现了大量车辆故障,通过统计分析,系统能够满足现行《运规》检查范围的40%;且由于新型车的大量使用及非提速车的大量改造,根据现场统计,系统发现的故障能够达到现场检车员发现故障的94%,扣除漏检因素,系统可以发现95%以上的当前车辆故障,对确保列车安全起到了重要作用。
优化了列车技检作业程序。到达列车技术检查作业时间可压缩至25min,与车站货检作业同步进行,不再单独占用到达列车作业时间。余出时间可全部补充至始发列车技术检查作业,为检车员严格执行“全面检、全面修”作业范围和质量标准保证了足够的作业时间。
充分发挥了TFDS设备保安作用。改善了列检作业环境,弥补了传统人工作业方式的缺陷,并能实现列检作业质量的追溯等。
五、待完善的问题
第一,系统本身存在缺点,由于系统是安装在轨边的设备,雨雪天气和强光照射对图片的清晰度影响很大。例如,光干扰问题,白班在一定时间内阳光斜射、直射均可造成所有车型转向架、互钩差这两个部位图片严重曝光,罐车、集装箱平车则4个工位均有影响,这为鉴别车辆故障带来一定难度,天气晴朗时甚至造成转向架、互钩差两个部位根本无法正常检测。还有雨天雨水进入摄像井遮蔽镜头,造成图片模糊鉴别故障有难度。
第二,系统不稳定,存在图像漏传、误传、信息数据丢失、设备停机等问题,不能保证正常的工作质量。特别是网络传输不稳定,有丢图现象,有时全列车无图像,有时个别工位无图像,有时个别工位的一侧无图像,经对下到列检作业场2009年1~4月份的统计,全月全列无图像平均在7~8列,图像不全平均在30列左右。
第三,拼图质量不理想,有错位、变形等问题,其中尤以制动梁部和中间部拼图错位严重,制动梁的梁体、弓形杆、中间部的各部管系都不同程度存在错位重叠现象,为正常检测、鉴别车辆故障带来一定影响,错乱的画面也无形中增加了动态检车员的视觉疲劳。
第四,系统的高速摄像机对车底部图片的拍摄只有一个角度就是仰拍,这就不可避免的造成拍摄死角,比如转8G、转8AG的上盖板故障不可视;制动梁支柱、梁体、撑杆、弓形杆下平面故障可视;上平面则不可视。转8G、转K2等转向架有交叉支撑装置的遮挡,制动梁闸瓦套根部和端轴检测因拍摄画面的幅度限制检测有难度;制动缸、风缸吊架螺栓丢失或吊架开焊,没有一定幅度的下垂角度,系统无法检测;再比如折断类故障,如果折断而断面没有错开的角度系统检测也有难度。
第五,由于TFDS一旦出现故障不能使用时,无法预备充足的列检人员投入到现场作业,应当不断完善TFDS设备的稳定性和系统本身的功能,特别是系统自动识别报警功能、报表自动统计生成功能、长大货物列车自动识别功能,并对系统兼容功能等方面进行改进,实现综合预报,以符合现场生产实际的需要。
(作者单位:宋可总,山东职业学院;王锦奎,上海铁路局南京东车辆段)
文/宋可总王锦奎
……
为加强货车安全防范系统的运用,确保提速安全的持续稳定,优化重组列检的作业方式,实现列检作业由静态向动态的逐步转变。根据铁道部要求,制定TFDS人机分工方案并组织了实施。
一、研制的背景
长期以来,铁路货车的运用维修手段陈旧,技术落后,列检作业基本靠检车员“手摸、锤敲、眼看、耳听、鼻闻”,列检作业人员钻入、钻出列车车辆,不仅效率低,而且无法保证作业质量。随着货物列车高速、重载、大密度的开行,势必造成各列检所日常检修任务的增加、工人劳动强度的加剧。而列检技检质量易受气候、职工素质、心理状态和人体疲劳程度等因素的影响,易给行车带来安全隐患。综上所述,传统的列检作业方式越来越难适应形势发展的需要。
二、方案的制定
根据新《铁路货车运用维修规程》(以下简称《运规》)第424条之规定,每个TFDS探测站的列车动态检查至少设1个动态检车组。每个动态检车组可采取全列分区域或分段包车的方式设置检查工位,并由动态检车组长或工长发出指令,系统自动分车、分段或分列。分区域设置检查工位时,须按转向架侧架、转向架底部、车钩缓冲部位、车底部等检查区域分别设置。包车设置检查工位时,每个检查工位须按转向架的仰视—转向架的侧视—车钩缓冲部位的仰视—车钩缓冲部位的侧视—车底部的仰视的顺序进行图像检测。1个TFDS动态检查室的每一列车的动态检查作业须由1个动态检车组完成;在确保列车到达列检作业场前或通过车站前完成列车的动态检查作业的前提下,应根据列车的区间运行时间、列车编组数量、TFDS探测站的安装位置等具体情况,确定检查工位数量;根据列车运行图规定的车流密度、列车追踪间隔时间以及检查径路数量或探测站数量等确定动态检车组数量。
明确动态检车组长、动态检车员、列检值班员、现场检车员在TFDS故障发现、预报、传递及故障确认等方面的岗位职责。列检作业组与动态检车员的配备满足技检时间和检修车的需要。考虑到各部位图像检查部件数目不同。为均衡各工位机的工作量,对每个TFDS动态检车组配备四至六名动态检车员,现场配备一定车辆故障确认人员。并制定一班、一列、一辆作业标准及TFDS动态检车员发现故障预报、确认及反馈作业流程。根据新《运规》TFDS-1动态检查程序标准(1)侧架“凹”字检查法,(2)车钩缓冲部位“e”字检查法,(3)车底“三”字检查法,(4)转向架“Z”“8”字检查法按照顺序进行检查。
三、实施情况
以济南铁路局济南西车辆段济南下行运用车间下到列检作业场2010年1月TFDS系统检测汇总为例。
1.综合使用情况
2010年1月1日8:30至2010年2月1日8:30,系统共通过货物列车1881列计99510辆,检测1842列计97404辆,日均检测59列3142辆,检测率97.93%,共预报各类故障18688件,日均发现故障603件,百辆故障发现率19.19件。
2.故障分类对比
故障分类对比情况见表1。
3.故障情况分析
对TFDS动态检查与人工静态检查发现的情况进行对比分析,可以发现以下现象:
(1)摇枕裂损、侧架裂损、制动梁裂损、承载鞍前端裂损、轴箱前盖裂损、轮缘缺损等故障,TFDS发现的故障比现场发现的少。其主要原因为上述各种部件裂损(特别是裂纹)、从TFDS拍摄的图片大部分无法分辨出来(TFDS拍摄的图片与实际的比例相差很大);另由于阳光干扰及设备不稳定,致使相应部位图片不清晰或丢失(图1),室内检车员无法判断。
(2)钩缓装置破损等故障室内检车员发现的基本占现场发现的50%左右。对于钩缓装置破损故障比裂损故障的实际损伤程度大,在图片上可以看出来,但由于阳光干扰,尤其是晴天对光或背光时,钩缓部无任何遮挡,图像或者太白或者太黑,动态检车员无法正常看图,这是导致钩缓装置破损虽然可以直观看出,但占的比例较小的主要原因。
(3)关门车故障,枕簧窜出、丢失以及其他各类配件丢失、折断、弯曲等故障,由于本身较容易发现,在设备性能稳定的前提下,动态检车员发现情况基本与现场检车员发现的故障持平或比例偏大。
(4)手制动机拉杆链丢失、闸瓦插销丢失、圆销开口销丢失(如图1所示)这类故障,TFDS机检较人工检查发现件数多,TFDS机检方式优于人工检查方式。
(5)对于拉环丢失、转8G型转向架交叉杆下盖板裂损弯曲、上作用式车钩钩舌销折断、制动阀及管路故障、各风缸堵丢失、折角塞门手把丢失、敞车钢地板破损、低磨合成闸瓦折断、附加杠杆丢失、截断塞门手把关闭、折角塞门手把丢失、ST1—600型闸调器控制杠杆丢失等12类故障,2种作业方式发现件数一致。
(6)固定链条式手制动机链条滑轮丢失(阳光干扰时TFDS无法发现)、滚动轴承渗油(渗油量小时TFDS无法发现)、缓冲器弹簧盒盖破损(由于缓冲器处于牵引梁内部且受钩尾框与从板影响,裂损故障小时TFDS无法发现)等3类故障,TFDS机检方式不如人工检查。
(7)车轮辐板孔周向裂纹、车轮踏面剥离、车轮踏面擦伤、踏面圆周磨耗超限、枕梁腹板裂纹、枕梁翼板裂纹、心盘纵裂纹、闸瓦厚度超限、制动软管局部凸起、闸瓦托磨损、制动缸堵丢失、复位弹簧丢失等12类故障,不属于TFDS动态检查范围,需要进行人工检查方式。
四、实施的效果
释放了列检劳动生产力。现场检车员在到达列车技检作业时不再钻入车下检查,不仅减轻了劳动强度,而且将工作人员充实到始发列车和动态检测作业中,使劳动组织更加科学合理。
TFDS作为防范车辆故障的重要设备,发现了大量车辆故障,通过统计分析,系统能够满足现行《运规》检查范围的40%;且由于新型车的大量使用及非提速车的大量改造,根据现场统计,系统发现的故障能够达到现场检车员发现故障的94%,扣除漏检因素,系统可以发现95%以上的当前车辆故障,对确保列车安全起到了重要作用。
优化了列车技检作业程序。到达列车技术检查作业时间可压缩至25min,与车站货检作业同步进行,不再单独占用到达列车作业时间。余出时间可全部补充至始发列车技术检查作业,为检车员严格执行“全面检、全面修”作业范围和质量标准保证了足够的作业时间。
充分发挥了TFDS设备保安作用。改善了列检作业环境,弥补了传统人工作业方式的缺陷,并能实现列检作业质量的追溯等。
五、待完善的问题
第一,系统本身存在缺点,由于系统是安装在轨边的设备,雨雪天气和强光照射对图片的清晰度影响很大。例如,光干扰问题,白班在一定时间内阳光斜射、直射均可造成所有车型转向架、互钩差这两个部位图片严重曝光,罐车、集装箱平车则4个工位均有影响,这为鉴别车辆故障带来一定难度,天气晴朗时甚至造成转向架、互钩差两个部位根本无法正常检测。还有雨天雨水进入摄像井遮蔽镜头,造成图片模糊鉴别故障有难度。
第二,系统不稳定,存在图像漏传、误传、信息数据丢失、设备停机等问题,不能保证正常的工作质量。特别是网络传输不稳定,有丢图现象,有时全列车无图像,有时个别工位无图像,有时个别工位的一侧无图像,经对下到列检作业场2009年1~4月份的统计,全月全列无图像平均在7~8列,图像不全平均在30列左右。
第三,拼图质量不理想,有错位、变形等问题,其中尤以制动梁部和中间部拼图错位严重,制动梁的梁体、弓形杆、中间部的各部管系都不同程度存在错位重叠现象,为正常检测、鉴别车辆故障带来一定影响,错乱的画面也无形中增加了动态检车员的视觉疲劳。
第四,系统的高速摄像机对车底部图片的拍摄只有一个角度就是仰拍,这就不可避免的造成拍摄死角,比如转8G、转8AG的上盖板故障不可视;制动梁支柱、梁体、撑杆、弓形杆下平面故障可视;上平面则不可视。转8G、转K2等转向架有交叉支撑装置的遮挡,制动梁闸瓦套根部和端轴检测因拍摄画面的幅度限制检测有难度;制动缸、风缸吊架螺栓丢失或吊架开焊,没有一定幅度的下垂角度,系统无法检测;再比如折断类故障,如果折断而断面没有错开的角度系统检测也有难度。
第五,由于TFDS一旦出现故障不能使用时,无法预备充足的列检人员投入到现场作业,应当不断完善TFDS设备的稳定性和系统本身的功能,特别是系统自动识别报警功能、报表自动统计生成功能、长大货物列车自动识别功能,并对系统兼容功能等方面进行改进,实现综合预报,以符合现场生产实际的需要。
(作者单位:宋可总,山东职业学院;王锦奎,上海铁路局南京东车辆段)
文/宋可总王锦奎
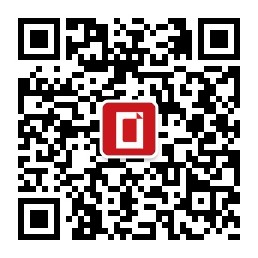