精益有道 事半功倍———浅析“精益生产”推广的第三种思路
- 来源:学问 smarty:if $article.tag?>
- 关键字:精益生产,推广 smarty:/if?>
- 发布时间:2014-12-24 14:30
【摘要】精益生产在国内制造业推广的两种思路———长期改善型和制造系统移植型。前者耗时长,见效慢,在市场竞争中,存在羽翼未丰既已夭折的风险。后者,见效快,但积累不够导致后劲不足,摆脱不了依赖。现提供第三种思路,制造系统本土化,是一个兼顾推广时间和知识积累的好办法。核心是是制造系统知识的本土化,只有真正掌握了核心知识并拥有实践经验,才真正具备参与竞争的能力。
【关键词】精益生产;制造系统;复制;本土化;知识管理
“精益生产”这个概念,来源于上个世纪八十年代末的一部著作———《改变世界的机器》。该书通过对比的方法,将五六十年代起源,六七十年代盛行于日本汽车行业,七八十年代导致日本汽车风靡全球的丰田生产方式揭示给读者,引起了一时的轰动。西方实业界也籍此对“精益生产”展开深度剖析和研究,以寻求其产品超强竞争能力背后的隐性知识、方法和工具,从而找到模仿和破解的路径,尽快实现与自身优势的集成重组,在市场竞争中形成新的优势。“制造系统”的概念,就是在这种背景下,首先在美国、德国、法国等西方工业化国家产生的。他们通过制造系统建模的方法,将“精益生产”的特征描述出来,然后通过标准的方法和路径来实现这个制造系统。“制造系统”复制,以简明、快速地形成量产能力著称,在随之而来的全球化浪潮中发挥了重大影响。
国内汽车行业是实践“精益生产”的先行者,对“精益生产”的研究和实践始于上个世纪九十年代初,将近二十年的进程里,尝试过自力更生,也尝试过合资双赢的办法,摸索中逐渐总结出两套推广“精益生产”的思路。
第一条思路,企业必须拥有一个能够生产产品的制造平台,“精益生产”开始推广后,企业将首先立足现场,将改善的理念融入到企业文化中,在改善中实现生产平顺,在改善中完成知识和经验的积累,在改善中提升设计和开发能力,最后在改善中打造出自己的核心竞争能力。
第二条思路,企业通过与跨国公司合资的办法,直接引用合资方“制造系统”,一方面通过“制造系统”知识的大量培训使员工快速掌握必要的制造技术,另一方面通过派驻少量精锐工程师的方法完成实物制造系统的复制,使工厂层面上快速形成量产能力;最后在合作伙伴方定期的评审和对标进程中,逐步消化和巩固“精益生产”和其他制造技术。
第一条推广思路走的是模仿日本的精益生产推广之路,这条思路较为传统,早在上个世纪七八十年代,日本企业在美国的合资公司走的就是这条道路。众所周知“精益生产”是在研究“大批量生产”弊端的基础上建立起来的。“准时化生产”和“自动化”是“精益生产”两大支柱,其高度概括了“精益生产”发展演化的初衷。第一,在生产组织的各个环节中杜绝浪费,实现拉动式准时化供货,以最大限度降低运行成本;第二,大量应用目视管理使现场的问题和改进机会变得显而易见;第三,推崇技术,提倡合理应用技术来进行作业条件的改善;第四,建立了一个鼓励改进,强调使命和责任感的企业文化。最终,在改善文化的强力推动下,企业各个领域都被去芜存精,真正在企业内形成了集约型制造风格。
表现出来就是高的产品品质、低的产品成本、满足顾客多样性需求的小批量生产模式,从而在最终的市场竞争中形成自身独特竞争优势,这也是丰田汽车至今仍然活跃在汽车制造顶尖层面的根本原因。按照这条思路推广“精益生产”,需要一段较长的时期来打造企业文化,引导变革,以期在整个公司层面形成推崇技术,注重知识积累,不断改进的氛围。这种思路下的“精益生产”推广方式的特点是时间跨度长,见效慢,但对初始制造系统要求不高,且稳扎稳打,效果巩固,公司发展的后劲充足。
第二条思路就是走经济全球化背景下,“制造系统”移植的方式。“制造系统”概念起源于20世纪末,很多美国大企业将精益生产方式与本公司实际相结合,创造出了适合本企业需要的管理系统。这些管理系统实质是应用精益生产的思想,并将其方法具体化,以指导公司内部各个工厂、子公司顺利地推行精益生产方式。并将每一工具实施过程分解为一系列的图表,员工只需要按照图表的要求一步步实施下去就可,并且每一工具对应有一套标准以评价实施情况,也可用于母公司对子公司的评估。使用这种方式推广“精益生产”,等于跨越了消化理解“精益生产”的步骤,直接复制合资方母公司提供的制造系统样本,短期内对制造人员进行高密度培训,并在合资方母公司项目人员帮助下,完成全新制造系统的构建和设定,达到迅速量产的目标。
“制造系统”复制的出现使精益生产方式内容和形式更加具体化,推广工作变得简单易行,并且还可以随时进行检查和评估。在经济全球化的时代,“制造系统”复制不失为一种快速复制并形成竞争力的好办法。但是“制造系统”复制的方法,也存在不足。首先,“制造系统”复制的目标短期性,限制了企业的发展后劲。现实制造系统客观上是由工人、设备、工装、产品和知识等要素组成的。“制造系统”复制,固然能够对实物制造系统进行全方位拷贝,然而,说到掌握的知识,却只能是“制造系统”文本所覆盖的那部分知识,它揭示了一部分“精益生产”方式的规律,但并不能全面描述实物制造系统,特别在设备、工装和产品等核心领域,而这些领域恰恰就是跨国公司核心竞争能力的体现。
实践中,我们很多合资企业的中方经理人,往往花了大量的时间和精力学习和贯彻合资方的“制造系统”文本要求,改善案例完成了一个又一个,但总是由点及点,很难形成面的突破,原因就在于忽略了现实制造系统的长期规划和知识更新,最终影响到企业竞争能力的提升。一些使用“制造系统”复制的企业实践证明,随着时间的推移,员工持续改进的能力不是在与时俱进,而是在逐渐枯竭,主要原因就在于我们的企业片面强调标准化操作,疏于设备、工装知识的探索和积累,在公司发展到一定规模后,持续改进的文化推动力就会受制于企业对知识的掌握程度。
“制造系统”复制的另一个弊端,在于描述和复制过程中的失真现象。这种失真通常表现在三个方面。第一种失真,首先表现在分辨率的问题上,这好比是数码相机拍照,由于象素的限制,照片质量再好却永远赶不上实物本身,分辨率影响到制造系统细节的复制。第二种失真表现在局部扭曲方面。制造系统毕竟是一个庞大系统,任何一个人或者公司,只精通其中的一个部分,这好比盲人摸象,摸到大腿的就认为大象是圆柱型,而摸到身体的会反驳,大象更象一堵墙,这使制造系统从一开始的样本描述上就失之偏颇。
最后,更加致命的失真会出现在制造系统的运营阶段,由于不断的发现问题,制造系统会经过不断“改良”,当多个改良累积起来后,就会导致制造系统的局部臃肿,当臃肿累积到一定程度,制造系统效率就会大打折扣,这样集约型制造的初衷就会与我们渐行渐远。而这样的失真现象,根源就在于“制造系统”是复制来的,未经实战锤炼,在企业文化和知识积累不够火候的情形下,制造系统的失真就随之而来了。由此可见,在第二条推广思路指导下的“精益生产”推广方式的特点是周期短,见效快,实物制造系统水平高,但人员知识基础相对不扎实,对母公司的依存度较高,公司自主发展的后劲略显不足。
客观上讲,“制造系统”复制推广模式的国内引进,在很短的时间里,最大限度地缩短了国内各车企与国外车企之间的现实差距,虽然在一些领域内如:装备、材料、过程还比较陌生,但相信通过合适的人才和知识战略,假以时日,必定能够熟练掌握。已经有很多成功的兼并和收购案例可以证明这一点。从另一方面来讲,市场竞争进入白热化程度的今天,制造模式的创新层出不穷,以缩短开发周期为目标的敏捷制造、以低成本为目的的批量定制等制造模式,无一不是建立在“制造系统”复制基础上的模式创新。也正是有鉴于这两个方面,“制造系统本土化”不失为一个兼顾推广时间和知识积累的好办法。
“制造系统本土化”是建立在“制造系统”复制基础上的概念延伸,就好比我们过去试读了十年的进口教材,掌握了较多的知识和教学经验,现在我们要根据我们的实践体会和生员特点,制定一份适合企业自身发展需要的培训教材。制造系统本土化首先指的是制造系统理论体系的本土化,其次是操控制造系统的人员本土化,最后是制造系统重要装备技术的本土化。制造系统本土化决不等同于制造系统文本的本土化,前者囊括了制造系统人、机、料、法、环五大要素在内的实物制造系统,而后者仅仅是前者诸多内容的一个部分。同时,制造系统本土化也不等于制造系统的本地应用,前者是一个包括制造系统开发、标准化、验证、运行、改进等全方位同水平的本地化,而后者仅仅包括制造系统的运行和改进。可见制造系统本土化的核心,是制造系统知识的本土化,只有真正掌握了核心知识并拥有实践经验,才真正具备参与竞争的能力。要做到“制造系统”本土化,企业应该做好以下几方面的工作。
第一,充分利用新兴企业的后发优势,将本土制造系统理论体系建立在充分消化日式“精益生产”制造模式和西方制造经验(产品\过程专业知识和装备技术)的基础上。
第二,大力推广知识管理,将制造系统实践中获取的知识、通过一定渠道收集来的知识,进行整理、排序和保存。
第三,建立制造系统本地化论坛,形成一个制造系统应用知识的平台。
第四,在企业构建崇尚技术和改善的企业文化,组建学习型组织。
第五,在企业设立专职改善的组织机构,以指导完成根据各企业自身条件制定的“制造系统”中长期推进计划。
第六、形成不断削减制造系统各环节库存的机制,不断发现问题,以改善流程和过程。
最后,在制造系统内进行必要的信息化工作,以简化并巩固流程。“制造系统本土化”战略一旦得到实施,至少能够给企业带来如下好处。
第一、短期内实现企业运行阶段的低成本效应。
第二、能够指导并帮助企业选择更佳的制造系统发展路线,避免了制造系统失真和后劲不足。
第三、大大缩短企业所急需高层次专业人才的培养周期。
第四、有利于创造一个精益求精的企业文化。
从而,最终这些优势将形成为产品市场上的竞争胜势。
总之,制造系统本土化策略,是在总结“精益生产”推广两条思路基础上的第三条思路,既复制了第二条思路中的快捷,又继承了第一条思路的稳固,是一种“扬弃”和创新的结合体,能够转化为不可模仿的竞争优势。当前全球金融危机条件下,中国车市的一枝独秀的现象使我们相信,实现制造系统本土化是各车企当下一个不错的时机,只要方法得当,不抛弃、不放弃,那么道亦有道。精益有道,就能达成事半功倍的效果。
【参考文献】
[1](美)詹姆斯·p·沃麦克、(英)丹尼尔·T·琼斯、(美)丹尼尔·鲁斯;The Machine That Changed The World
[2](日)门田安弘;.新丰田生产方式
[3](日)若松义人,近藤哲夫;.丰田生产力
吴郁峰
上海通用汽车有限公司(201206)
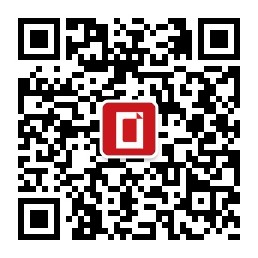