提高数控加工效率
- 来源:环球市场信息导报 smarty:if $article.tag?>
- 关键字:加工,效率,数控 smarty:/if?>
- 发布时间:2014-11-03 16:05
一、数控机床(加工中心)的特点:
数控机床与普通机床相比:优点是:对加工对象适应性强,适合多品种小批量零件的加工,被加工零件经过一次装夹后,连续地对工件各加工面自动地进行钻孔、锪孔、铰孔、镗孔、攻螺纹、铣削等多工序加工,能精确加工各种轮廓和形状复杂的零件,而有些轮廓是普通机床无法实现的;加工中心能集中地、自动地完成多种工序,避免了人为的操作误差、减少了工件装夹、测量和机床的调整时间及工件周转、搬运和存放时间,大大提高了加工效率和加工精度,所以具有良好的经济效;数控设备的自动化程度高,可大大减轻操作者的劳动强度;实现计算机辅助设计(CAD)、计算机辅助工艺设计(CAPP)、计算机辅助(CAM),有利于实现信息化生产和管理的现代化。
缺点是:数控机床价值高;数控机床的运行和维护成本大;对维修人员的技术水平要求高,一旦出现故障要尽快准确判断及时修复;对编程操作人员要求高,编程人员既要非常熟悉编软件的应用,同时还要有非常丰富的专业知识及经验,否则不能很好地发挥设备的优势,不仅不能创造良好的效益,还可能对设备造成损害。
二、数控加工的过程
数控加工,就是在数控机床上进行零件加工的工艺过程。数控机床是通过由专用计算机或通用计算机(数控系统)来控制的机床。数控机床的运动和辅助动作均受控于数控系统发出的指令。而数控系统的指令是由程序员根据工件的材质、加工要求、机床的特性和系统所规定的指令格式(数控语言或符号)编制的。数控系统根据程序指令向伺服装置和其它功能部件发出运行或终断信息来控制机床的各种运动。一个零件在数控机床上完成加工,一般需要经过下面的步骤:工艺性分析和工步的合理确定:选择可靠快捷的装夹:刀具的选择:程序的编制验证及修改:切削参数的选择:工装夹具及刀具的准备:零件加工及检测。
三、提高生产效率的途径
产品结构设计的工艺性:产品设计过程中,要最大限度地考虑零件加工的工艺性和适应性,便于零件的实现。应遵循下述原则:a、基准统一的原则;数控设备的加工基准与零件的基准相一致可避免因基准转换造成误差。b、内腔设计圆角尽可能大的原则;较大的圆角可采用较大的刀具,有利于优化加工参数,提高加工效率。c、避免深盲腔的采用;盲腔的加工易造成切屑的堆集无法排泄,形成夹刀,挤屑等现象,需要中间停顿清屑影响效率。同时易造成加工表面挤伤、断刀,降低加工精度等情况。d、在允许的情况下,尽量使各棱边的倒角和圆角一致。e、零件的结构应有利于装夹、测量,并容易实现装夹与测量基准的统一。
合理的工序工步安排:对铣加工中心而言应遵循工序相对集中的原则,在保证质量的前提下,尽量在一道工序完成较多的加工,减少装夹的次数,避免工序之间的周转、检验所产生的无效工作。在工序安排时,要考虑的因:a、粗精加工的关系,根据不同的加工材料及零件的结构特点来确定。b、各加工面的加工顺序,既要遵循高效的原则,又要为下道工序提供可靠的基准和快捷的装夹面,必要时可考虑增加工艺台、工艺孔等措施。c、装夹的夹持边(面)应尽可能的大,即可减少变形,又可采用较好的切削参数,达到高效的目的。通过对零件结构、材料、精度等的分析,确定相对可靠的定位基准、辅助基准和合理的工步。d、对薄壁件加工时,可考虑采用工艺块撑内腔的方式,即确保装夹的可靠,减少变形,又可尽可能地优化加工参数,以达到提高效率的目的。
快捷、可靠的装夹:快速、可靠的装夹是数控加工中的非常重要的环节,装夹的可靠与否,不仅决定着零件加工精度,同时也决定着加工参数的优化。要避免应装夹而产生的变形应力不均,尽可能多的加大夹持面……。快捷的装夹,可最大限度地减少无效的工作时间,提高机床的利用率,如何实现快捷、可靠的装夹?
a、完备的基础建设,可增加装夹方式的多选方案,这就要求针对自身产品的特点、配备各种压板、螺钉及定位件,如:平压板、弯压板、宽压板、窄压板、叉形压板、单向压板、双向压板、钩型压板、V型块挡板等。
b、可配备一些快速装夹装置,以实现快速装夹,如:偏心轮夹紧机构,斜楔夹紧机构,气动夹紧机构,液动夹紧机构、真空吸盘等,可将这些机构组成独立的、通用的快速装夹装置,以备不同结构零件加工时选用,实现提高效率的目的。
c、利用数控设备多座标系的功能,用组合式快速裝夹,实现多零件的加工,使得设备的运行时间连续和延长,从而实现一人操作多台设备,达到降低成本,增加效益的目的。
加工程序的优化:数控加工程序,是实现对机床各轴(x、y、z等)进行控制的指令,程序的编制分为手工编程和软件编程,对于零件结构简单,加工量不大,使用刀具不多的情况下,手工编程更快,而对形状复杂,工作量大的零件、需借助于计算机编程。程序编制过程中,要根据零件具体结构的不同而采取不同的编制。
a、粗精加工分开:粗加工时,是以尽可能快地去除材料为目的,所采用的加工参数(如转速、走刀速度、切削深度等)和所选用的刀具均应以效率为优先考虑。精加工时,是以保证零件最终尺寸精度要求和获得相应的表面粗糙度为目的,它的加工参数的选取和刀具的选取不同于粗加工。
b、下刀点和刀具路径的选取;下刀点的选取应遵循尽可能好的切削条件,必要时先钻铣出下刀点,使整个切削过程平稳。刀具路径的选择,同样要遵循确保良好的切削条件,良好的排屑性能以及尽可能短的切削路径,对于复杂曲面的加工,还要考虑切削路径的不同,程序量大小的影响。
c、根据零件的具体结构采取相对集中和分步加工相结合的原则,由于结构的不同采用的刀具会不同,使用一种程序时,相应的切削参数难以实现最优化,而分步实施即将程序分解为几个单独程序,有利于切削参数的优化达到提高效率的目的。
d、最大限度地发挥机床的性能如转速,快速移动等功能,压缩程序中的无效时间…
刀具及切削参数的选择:对数控铣加工来说,目前常用的刀具材料有高速钢,硬质合金,超细微粒硬质合金,涂层硬质合金,这几种材料因其较高的硬度、强度和耐磨性,较好的红硬性,而广泛用于铣刀的制作,而不同材质的刀具相适应的切削参数也不同,各生产刀具的厂家都会给出一个推荐的切削参数以供参考,除了刀具的材质不同外,刀具的齿数,螺旋角、前、后角等的不同,也会对应于不同的加工材料和不同的加工。
a、粗加工刀具的选择,是以切除大量金属为目的,应选用齿数相对少的铣刀,增加容屑的空间,提高切削速度,如二齿或三齿或镶齿铣刀等。也常选用波刃铣刀,改善切削条件,提高效率。
b、精加工时相应的切削金属量会小一些,而更多的要求保证尺寸的精度和表面的粗糙度,精加工的刀具可选用密齿及刚性好的铣刀,如四齿铣刀和硬质合金铣刀。
c、内R的大小决定了刀具直径的大小,当R较大时,可选用大的切削参数,提高效率,若R较小,由于刀具的刚性较差及排屑等因素,切削参数需选择较小尤其考虑每齿的进给量和切深。
d、对于相对较厚的加工如零件厚度大,深腔等的加工,因其切削时的面积较大,刀具的长度就需要较大,尤其是刀具直径较小时,很容易产生刀具的刚性变形,造成加工面的缺陷,侧齿加工的面会出现潲度,底齿加工的面表面的微观不平度较大,此时,选取刀具要尽可选择刚性好的刀具,如直径较大的和材料刚性好的硬质合金刀具,同时要对切深和每齿切削量(转速和进给量)的科学选择,必要时,最终加工以零进給多次切削,以消除因刀具刚性变形而产生的缺陷,以保证零件的加工精度和表面光洁度。
冷却液的使用:冷却液的作用一是对刀具和工件冷却将切削时所产生的热量带走,降低切削温度,避免积屑瘤的产生,减少热应力和热变形;二是起切削润滑的作用,以降低切削力;三是带走切屑,改善切削条件。目前常用的切削液有浮化液、机油、油气三大类,选用时要根据设备的情况,被加工零件的材料、零件的精度等因素选择。一般的设备常用油、浮化液、被加工零件的材料为钢时,材料的抗拉强度较大,相对切削力较大,切削过程产生较大的热量的同时对刀具的磨损也较大,一般易采用油冷,其目的是以降低刀具磨损,提高刀具寿命为主。当被加工材料为铜、铝时,材料的抗拉强度较小,切削力较小,对刀具的磨损也较小,一般多采用浮化液一类的切削液,主要是以降低切削温度为主。数控设备的冷却液喷嘴,一般至少也在两个以上,使用时,根据被加工零件的结构、刀具等具体情况调整喷嘴的喷射位置和方向。最大可能直接喷射到加工部位,其次要考虑尽可能多带走切屑。当设备喷射压力大,刀具直径较小(≦2mm)时,要注意喷射压力对刀具刚性的影响,以免产生刀具变形影响加工精度和表面光洁度。
设备的维护保养及正确使用:保持设备的良好运行是数控加工的基础,要严格按设备的操作要求,正确操作机床,其次要保证设备的正常润滑,保证设备机械运动、机构的清洁和运动的正常,保证电控系统的清洁和检查。另外,要对各种辅助设备、设施、工装夹具等进行随时的维护保养,以保证设备处于良好的运行状态。
减少无效工作时间、提高机床的利用率:在数控加工的过程中,存在着许多的无效工作时间,如:编程序时机床等待,零件的装夹、刀具的准备、加工中的空行程,机床故障、维修等,过多的无效工作时间,必然影响数控机床加工的效率,如何消除减少无效工作时间,对数控加工来说,是非常重要的。根据各自的生产条件梳理工作流程,引入精细化生产和并行工程的管理思路,优化工作流程并固化。通过对人员和设备的合理配置,使编程与设备运行并行;将设备、刀具等准备时间的工作优化,尽可能使这些工作事先准备好,减少在机床上准备的时间;配备一些快速装夹的夹具,如气动、液动、杠杆等原理的夹具,实现快速装卸零件,提高机床效率;编制程序时,优化刀具路径,多采用快速移动功能减少空行程,合理切削参数的使用。
陈书斌 文
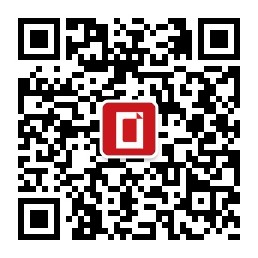