桥梁钻孔灌注桩断桩形成原因及预防处理方法
- 来源:环球市场信息导报 smarty:if $article.tag?>
- 关键字:钻孔灌注桩,断桩,施工,桥梁钻孔 smarty:/if?>
- 发布时间:2014-02-09 09:45
钻孔灌注桩作为一种基础形式以其适应性强、成本适中、施工简便等特点被广泛地应用于公路桥梁及其它工程领域。但是在实践中断桩现象时有发生,该文就钻孔灌注桩断桩的原因及预防处治作了简要分析,旨在为类似工程提供借鉴。
随着我国交通基础设施建设的快速发展,钻孔灌注桩作为一种基础形式以其适应性强、成本适中、施工简便等特点仍将被广泛地应用于公路桥梁及其它工程领域。钻孔灌注桩属于隐蔽工程,但由于影响灌注桩施工质量的因素很多,对其施工过程每一环节都必须要严格要求,对各种影响因素都必须有详细的考虑,如地质因素、钻孔工艺、护壁、钢筋笼的上浮、混凝土的配制、灌注等。若稍有不慎或措施不严,就会在灌注中产生质量事故,小到塌孔松散、缩颈,大到断桩报废,给国家财产造成重大损失,直至影响工期并对整个工程质量产生不利影响。所以,必须高度重视并严格控制钻孔灌注桩的施工质量,尽量避免发生事故及减少事故造成的损失,以利于工程的顺利进展。
常见的断桩形式及影响因素
常见的断桩形式。从目前情况看,常见的断桩形式一般有以四种:
混凝上桩体与基岩之间被不凝固。由于导管下孔距孔底过远或混凝上被冲洗液稀释,使水灰比增大,造成混凝土不凝固而出现断桩现象。
桩身中段出现混凝土不凝体。受地下水活动的影响或泞管密封不良,冲洗液浸入使局部混凝土水灰比增大,也能产生断桩现象。
桩身中岩渣沉积成层,将混凝土桩上下分开。在浇注混凝上时,泞管提升过多,露出了混凝土面,或因停电、待料等原因造成夹渣,这些问题也是产生断桩现象的重要原因。
桩身出现空洞体。原因是未采用“回顶”法灌注,而是从孔口直接倾倒的办法灌注混凝土,产生离析,造成凝固后不密实,个别区段产生疏松、空洞现象。
影响断桩的因素。断桩是由于桩基混凝土的某一部分和全部端面段泥浆浸入,破坏了桩的整体性受力形态,形成废桩。影响断桩的因素是各种各样的,但主要是由于材料、工艺不当造成的,归纳起来,这些产生因素主要有以下几点:⑴水泥初凝时间过短;⑵骨料粒径偏太,砂粒中有大卵石;⑶水泥混凝土的和易性差,流动性差;⑷清孔工作不彻底;⑸导管埋得过深或过浅;⑹导管进水了;⑺由于机械故障、施工机具配置、劳动力组织不合理,致使灌注时间过长。
产生断桩的原因分析
断桩作为产生严重质量事故的重要原因。对于诱发断桩的因素,我们必须在施工初期就彻底清除其隐患,同时又必须准备相应的对策,预防事故的发生。一旦发生事故,就要及时采取补救措施。分析起来,断桩产生的原因有以下几个方面:
在灌注混凝土过程中,由于测定已灌混凝土表面标高错误,导致导管埋深过小,出现拔脱提漏现象,形成夹层断桩。特别是钻孔灌注桩后期,超压力不大或探测仪器不精确时,易将泥浆中混合的坍土层误认为是混凝土表面。因此,必须严格按照规程规定的测深锤测量孔内混凝土表面高度,并认真核对,保证提升导管不出现失误。
在灌注过程中导管的埋置深度是一个重要的施工指标。由于导管埋深过大,以及灌注时间过长,导致已灌混凝土流动性降低,从而增大混凝土与导管壁的摩擦力,加上导管采用已很落后且提升阻力很大的法兰盘连接的导管,在提升时,因为连接螺栓拉断或导管破裂而产生断桩。
产生卡管现象。由于人工配料的随意性较大,如果责任心差,造成混凝土配合比在执行过程中的误差大,使坍落度波动大,拌出的混合料时稀时干。坍落度过大时会产生离析现象,使粗骨料相互挤压阻塞导管;由于坍落度过小或灌注时间过长,使混凝土的初凝时间缩短,加大混凝土下落阻力而阻塞导管,都会导致卡管事故,造成断桩。所以,要严格控制混凝土配合比,缩短灌注时间,这是减少和避免此类断桩的重要措施。
坍塌。由于工程地质情况较差,施工单位组织施工时重视不够,有甚者分包或转包,施工者没有经验,在灌注过程中,井壁坍塌严重或出现流砂、软塑状质等,造成类泥砂性断桩。这类现象在本工程的断桩中占有相当大的比例,较为严重,而且位置深、难处理。这些都是导致工期无限延期及经济浪费的重要因素。
特殊原因。由于导管漏水、机械故障和停电造成施工不能连续进行,井中水位突然下降等因素,都可能造成断桩。因此,认真对待灌注前的准备工作,这对保证桩基的质量是也十分重要的。
断桩的预防与处治措施
针对上述分析,我们应从预防与处治两方面采取措施:
采取预防措施
要选用初凝时间不早于2.5h的水泥,对于桩较长,桩径大,灌注时间较长者,可在首批混凝土中掺入缓凝剂。
严格把好材料关,严格控制粗骨料最大粒径不大于导管内径的1/6-1/8和钢筋最小净距的1/4,细骨料的级配选择良好的中砂,同时注意剔除细骨料中的大卵石。
最大限度地降低实际生产与试验之间的偏差,施工过程中要及时做好材料含水量的检测,应该做到每车集料都要过秤,采取重量比控制,保证用水量和含砂率不至产生较大偏差,保证混凝土的和易性和流动性,其坍落度控制在18cm-22cm之间。
要严格按规范要求进行清孔。由于孔内沉淀层厚度对于摩擦桩不大于0.5倍的桩径,对于柱桩不大于设计规定;泥浆的比重在1.05-1.20之间,含砂率小于4%,粘度17s-20s。灌注前,必须对孔底沉淀层厚度再进行一次测定,如厚度超过规定,需再次清孔,可用灌注导管做吸泥管用空气吸泥机清孔,或对孔底高压射水或射风3min-5min,使沉渣悬浮,然后立即灌注混凝土。
灌注即将结束时,如出现混凝土顶升困难时,除按规范保证漏斗底口高出井孔水面4m=6m外,应在孔内加水稀释泥浆,并掏出部分沉淀土。在拔出最后一段导管时,拔管速度应较慢些,以防泥浆挤入桩内。
处治措施
灌注初期的断桩。在开盘后,仅仅灌注了数米就因故中止,而且确实不能在短时间内恢复灌注,则应立即拔出导管,用气举法吸渣将孔内尚未凝结的混凝土清除干净,不宜采用二次剪球的方法,因为这样处理易造成夹泥的缺陷。如断桩时,孔内混凝土已有相当数量,气举法难以吸除而混凝土面离护筒底还有一定距离。这种情况下可考虑割除部分钢筋笼,趁混凝土强度低时用冲击钻将混凝土连同钢筋全部冲碎清除。钢筋碎断后可用电磁铁吸除。
内套钢护筒,清水接桩。在灌注中止时,混凝土面离孔口不足20米,可采用一个比钢筋笼直径稍小的牙轮钻,从混凝土面钻入1米以清除表层混凝土,然后制作一条比现有护筒稍小而比钢筋笼直径稍大,尽量接近设计桩径的钢护筒,从外护筒与钢筋笼之间放入孔内,可直至混凝土面。
旋喷帷幕法。要在桩身周围连续钻孔后旋喷灌浆,浆与砂土固结后形成一帷幕,然后用小钻头扫除桩经内1米后混凝土表层,将泥浆置换为清水,由潜水员下去将余渣清除干净,最后在清水中第二次灌注水下混凝土。如果钻孔间距20~60米不等,依具体地质情况而定。为稳妥期间,要防止液窜入孔内,还应向孔内回填土才能保证质量。
冻结法。要用人工制冷技术,在桩外周钻孔,放置冷混凝土,将混凝土以上护筒以下的孔壁土体中的水冻结,形成强度约为5~10MPa的冻土帷幕,达到人工处理断面并在干处浇注混凝土的目的。在冷冻孔内宜采取降低水化热措并搀加防冻早强剂,从而以免混凝土遭冻害及产生温度裂纹。
总之,从上面的分析看,虽然断桩的产生有着很多原因,只要我们认真分析清楚断桩产生的原因,找出相应的预防措施,断桩是可以避免的。如果产生了断桩,我们还应采取相应的处治理措施。
李庆明 朱萍
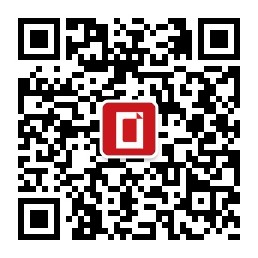