彭葵:留下自己痕迹
- 来源:中国汽车界·汽车人 smarty:if $article.tag?>
- 关键字:彭葵,质量,管理 smarty:/if?>
- 发布时间:2014-08-26 12:47
彭葵以更忙碌的节奏迈入素有“火炉”之称的武汉之夏。5月29日,他所在的东风乘用车公司发动机工厂开始进行设备改造。目标是企业高温假结束后,将现有6万辆的产能提升为12万辆。
对于这样一个庞大的工程,身为发动机副厂长的彭葵了然于胸。内敛而又平和的技术管理者谈话方式,有着工科背景的明显特征,讲究逻辑,思维缜密。发动机领域摸爬滚打近20年,堪称动力老资格的他对于这一切已经驾轻就熟。
1996年大学毕业进入神龙汽车公司襄阳工厂,从自动化技术员做起,负责过质量,管过设备,还当过5年车间工段长,2012年,当他看到东风乘用车发动机厂招聘副厂长岗位启事时,他已经做到分厂厂长的位置。
从技术到质量再到管理,经受过专业培训和十余年实战打磨,彭葵无疑是合适的人选。喜欢挑战,并希望能为自主事业做些事情的彭葵,就这样成为东风乘用车团队的一员。
发动机对于汽车的重要程度,不亚于心脏对于人体,有着极高质量标准和技术要求,需要各个部件紧密配合,各个环节一丝不苟,保证每道工序的质量符合要求,最终才能保证发动机整机符合要求。这对于管理者和制造者素质要求甚高。
进入这个企业时,东风乘用车发动机厂还处在调试和试制的阶段。从零起步的东风乘用车自主首款发动机,保证质量尤为重要。彼时,彭葵自赋使命:“发动机产品的质量,关系着驾乘人员的生命财产,质量首先是良心,以自己的良心,做好质量工作,符合客户质量要求。”
事实证明,他做到了。
质量为本
2012年初,东风乘用车发布了中期事业计划——A1计划。根据计划,东风乘用车到2016年之前,累计销量将达到100万辆。并确立了“质量卓越、服务领先、魅力产品”三大战略路径。
这一目标的实现与发动机息息相关。作为整车技术核心中的核心,发动机工艺复杂,精度要求高,工序质量的相关性比较强,因此,发动机工厂的质量管理关键在于预防体系的建立就显得格外重要。
在发动机工厂,从领导干部到工艺员,从班长到线上工人,从现场管理到保全人员,都深刻地感受到了这份沉甸甸的责任。为了保证质量,发动机工厂每天召开QRQC(快速响应质量控制)晨会,对前一天的质量不良情况进行通报,同时探讨接连几天的质量责任人和立项情况。
针对质量改善,东风乘用车发动机工厂还制作了品质不良问题一元管理表,包含一百多项问题点,彭葵每天都进行更新和跟进。
彭葵认为,发动机质量管理有其特有的规律,也有一些科学的手段预控质量风险,抽样检查,工序质量扣分,缓慢偏差监控,设备能力值监控,产品质量扣分监控、发动机动、静态扣分监控等科学方法的实施,可以有效地预防质量风险的发生。
而全员质量改善,是实现质量卓越的基础,对质量问题的反思和水平展开,全员参与的PDCA质量改善,可以不断提高产品质量水平,从而满足不断提高的客户质量要求,使产品更加具有竞争力。
以主要搭载于东风风神S30、H30、CROSS等车型的首批自主发动机量为例,工作人员带着它进行“四高”(高温、高海拔、高寒、高湿热)测试。经历了20000小时台架试验和80万公里的整车道路试验。经过市场验证,这些发动机具有高动力性、高燃油经济性、高可靠性,低噪音设计、低排放的优势和特点。
发动机零公里退返率、一次装配合格率、市场故障率是衡量发动机质量3个重要指标。“从油耗、动力以及排放来说,东风风神的发动机技术在自主品牌阵营中是领先的,从市场营销部反馈的市场调查看,消费者还是很认可的。”彭葵告诉《汽车人》,从发动机市场故障率反馈看,直接客户反映发动机问题故障率在0.49%。正常情况下,故障率达到1%就是一个不错的数据。
由于发动机质量的可靠性,目前发动机工厂生产的乘用车发动机在供应东风风神品牌外,开始尝试向集团内部企业供货。彭葵透露,目前他们正在为东风裕隆做适配,大概会在明年正式批量供应。
标准化管理
一般而言,发动机的制造需要3道工序:铸造、机加、装配。要保证每道工序的正常运转,就需要有一个管理体系。
在彭葵看来,质量是制造出来的,而不是检查出来的,标准化是质量保证的最好手段,首先是制定正确的工作规范,培训让每一个人熟知,然后强化完美执行,监督检查纠偏,最后执行形成习惯,形成标准执行的习惯,规避质量风险,这也是质量体系建立和健全的必由之路。
“工作质量保证过程质量,过程质量保证产品质量,人的品格决定了产品质量。”彭葵说。
从人员培训与标准化流程开始,围绕着质量所做的提升和改善,彭葵和他的团队挑起了为东风风神打造可持续的动力心脏的重担。
“最重要的是结合自身特点,建立标准化的管理模式,培养后备人才。”彭葵表示,乘用车市场在快速发展,国家乘用车燃油限值标准也在不断提高,发动机工厂在产能以及产品更新方面都会发生急剧的变化。为使个人能力适应环境变化,持续学习,团队协作,形成一个高效简洁的管理模式尤为重要。
合资企业发动机工厂15的工作经验,彭葵深刻体会到,与合资企业相比,自主发动机在制造管理和制造技术已经没有太大的差异,但在核心技术和研发能力上存在很大的差距。人才、规模、管理模式恰恰是自主发动机企业需要弥补的地方。因此,从去年开始,彭葵就把“作业标准化”作为工厂改进的重心,今年,这个重心升级为“管理标准化”。
在这个过程中,各方困难可想而知。与提及困难相比,他更大的感受是“感动”。发动机这个团队有着积极向上的做事氛围和强烈的责任感。大家为解决一个问题,会连续通宵作战。也会因为一个辅具上的螺钉不见了,而全线停工,直至找到才开始复工。
“一个全新的发动机工厂,首款产品就像棵小树苗一样,每天辛苦劳作,施肥浇水,看到它每天都在不断地在进步,我们也会有成就感。”他们生产的A系列发动机,无论从动力性、经济性,还是质量水平,都不逊色于合资品牌。
2013年,彭葵牵头组织实现A16发动机高质量切换,市场响应良好,获得公司4I改善课题一等奖;今年3月,在他的带领下,实现A16发动机垂直转产、产量爬坡的生产任务。
为人简单,不喜欢应酬,偶尔会做一些简单运动,彭葵符合技术型管理人才的特质。作为东风企业培养成长起来的管理高管,彭葵更希望能让自己的所学最大程度地回馈给这个企业,“我希望在自主发动机事业中,留下属于自己的痕迹。”这是发自他心底的声音。
文/本刊记者 张敏
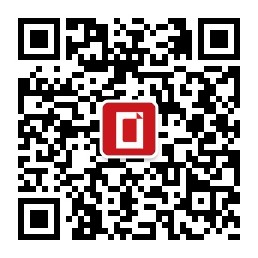