孟磊:把关风神品质
- 来源:中国汽车界·汽车人 smarty:if $article.tag?>
- 关键字:孟磊,质量 smarty:/if?>
- 发布时间:2014-08-26 13:03
刚过不惑之年的孟磊,是东风风神品质把关者中的关键一员。
身为质量保证部主任,“找茬和挑错”是他日常工作的一部分,“较真”则是这个岗位最重要的素质之一。某种意义上,这是一个不受欢迎的角色。但他并不打算改变自己的执拗。
从东风乘用车品牌开始筹备,这样的事情他已经坚持了7年。在此之前,他曾在东风本田前身东风万通工作相当长时间。
2007年,他加盟到这个刚刚蹒跚学步的自主品牌时,算上他,质量保证部不过区区4人。7年后的今天,这个团队已经拥有150多名精兵强将,置身于产品研发、生产、售后过程中的质量问题监督与解决。
在集产品质量、过程质量、经营质量等于一体的“大质量观”指导下,孟磊和他所在的团队建立并严格执行从研发到售后的全价值链高标准的质量管理体系,每台新车都要历经590多项工序和200多个流程的严格把关。
这些繁杂的工序与流程构成了一整套行业先进的评价标准,当然,还要由孟磊等能够熟练掌握运用这些标准的人才,才确保产品形成的整个过程中,精确满足顾客需求。
只有严苛的管理体系,才能铸就卓越质量,从J.D.Power公布的IQS指数来看,东风风神产品质量连续3年大幅提升,孟磊更是欣慰地看到一大批超60万、50万公里无大修车主的诞生,他们都是东风风神品质最有力的见证。这又何尝不是对他最大鼓舞与嘉奖?
3个层级
负责整车质量的孟磊很大精力放在了新项目导入上。从新车开发项目立项开始,来自于质量管理部的同事就会加入到项目团队,确保项目在投产期能够达到设定的质量目标。这个过程会延续整个项目始末,通常会持续二至三年。这期间他们开展一系列的评价和检查的活动,来找问题,“挑毛病”。这些被挑出来的“毛病”,要在项目投产前全部被解决。
被挑毛病的一般会是研发中心或设计团队。从东风风神投产第一款车型S30到H30再到A60,每一款车研发过程都凝聚着两组力量的碰撞、交织,乃至形成共同的目标——最大程度上让消费者满意。
以开发质量管理为例,东风风神对整车的评价就有商品性评价、保安防灾评价、VES评价、电装机能评价等,达26种之多。“我们可以不很懂设计的理念,但根据这些评价标准,我们可以告诉你,哪些些地方没有做到位。”
为了一个并不影响车辆性能的5毫米配合公差,技术人员花费一年时间,通过提升车体精度,精修引擎盖、保险杠和前大灯的模具,最终,将公差控制在正负0.5毫米,配合精度整整提高5倍,完全达到主流合资品牌的水平。
改善无处不在。从车本身而言,设计水平的提升致使出现的问题在减少,从孟磊的角度,挑毛病的水平也在提升。尤其是与研发人员的沟通中,技巧性的沟通会更容易被对方接受。“一般很少对设计师说你做的不好,会给他一些别人更好的、更被大众接受的做法,不是单纯的挑毛病,而是会给一些建议。”
亲临现场的沟通会带来更彻底的贯彻。孟磊把这个沟通方式叫做“三现”,即现场、现实、现物。要沟通设计过程中的质量问题?Ok,我们不要在邮件中说,也不要开会中对着报告念,我们去现场,让车辆说话。
评价体系也随之不断完善。在孟磊看来,质量控制要分3个层面。第一级别是基本质量,做好了客户不一定就满意,但做不好客户就会很不满意;第二层次是一元质量(如参数、油耗、性能等),做得越好客户越满意;第三个层次就是魅力质量,做不好客户不一定会不满意,但做好了就能给客户带来惊喜。
东风风神正向着第三个层次进发。在J.D.Power亚太公司发布的2013新车质量研究报告(IQS)中,竞争最激烈的中型车市场,东风风神A60以分值95的优异成绩,荣登自主品牌榜首,位列行业前七,堪称“中国品牌质量冠军”。
而S30系列可靠性(VDS)位居中级车国家队第一,创造了60万公里无大修的记录,上市5年来销量仍保持细分市场前10名,堪称自主品牌“常青树”。
质量底线
从2007起步伊始,东风乘用车就开始了质量体系的构建,这期间,风神的质量体系经历了3个发展阶段,从“立足自我”的开发、制造、零部件质量保证的3条主线管理,到“聚集客户立足市场改善”,通过提升开发、制造、供应商质量水平、加快市场改善速度的4个维度管理,再到如今践行“大质量观”的全价值链质量管理体系。
在东风乘用车“质量卓越”战略下,“大质量观”被提上日程。东风风神的“大质量观”贯穿产品从研发到流通的每个领域,始终站在顾客的角度去聚焦客户的需求,全维度提升产品的硬件质量和感知质量。作为质保工作者,孟磊他们需要从设计研发、采购、制造、物流等各个业务层面进行质量管控。
繁杂的事物中,流程与标准成为提升效率,减少误差的法宝。如果“三现”是一个质检人员的必杀技的话,那么对于问题追本溯源的精神则是质检人必备素质。“这个问题产生了,可能有很多原因,你要找到真正的那个因素,只有把那个问题解决了,才能真正保障这个问题得到最终的解决。”
孟磊对《汽车人》分享的是一个看似很小的案例。不久前,配送零部件的第三方物流送错了一个零件。这是个通用件,外观与其他一个零件差异性很小,但是不同车型的配件。这导致了装配人员的错装,影响很大,孟磊他们为此开了好几次会,寻找故障原因。
配送方给出的解释是,老员工辞职了,作业员新来的,培训不到位等等。为什么老员工离职率很高?原因可能有待遇差、薪水没有竞争力等等。真的是这样吗?后来,经过深入调查,发现这家物流企业没有一个好的食堂。大家中午吃不好饭,干活自然心情不好。所以出现了差错。
问题就是这么简单。“你预先想到的因素与解决的问题相差很大。作为质检人员,只能刨根问底,才能最终解决问题。”孟磊说。
更多的问题出现在与各方平衡中。比如,当完美设计遭遇制造工艺,当高质量引爆成本压力,当开发周期遇到上市压力,如何平衡?
对于孟磊而言,一个雷打不动的原则摆在那里。“可以加班加点推进上市步伐,但所有一切不能以牺牲产品质量为前提。”
今年,孟磊80%的精力会用在新项目上。没有特殊情况,每天早晨8点半至10点他会准时出现在现场,解决一些产品在量产中出现问题。下午3点半会参加新车型的试作/评价会议,与相关部门针对新项目进行测评。
挑剔是一如既往的态度。“只要在这个位置上,我代表的就是客户。”孟磊说。
文/本刊记者 张敏
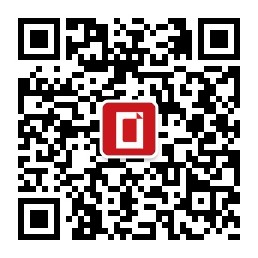