基于云计算的钢包精炼仿真实验平台
- 来源:中文信息 smarty:if $article.tag?>
- 关键字:云计算,钢包精炼炉 smarty:/if?>
- 发布时间:2015-01-06 13:42
摘 要: 钢包精炼炉是重要的钢水精炼设备之一,本文设计并实现了一种基于云计算的钢包精炼炉仿真实验平台,凭借云计算扩展灵活、高效可靠的优势,可通过网络为精炼炉的操作培训提供模拟实际生产的仿真实验平台。
关键词:钢包精炼炉 云计算 仿真实验
中图分类号:TP273A 文献标识码:A 文章编号:1003-9082(2015)01-0005-01
近年来,电炉—转炉—二次精炼—连铸的短流程炼钢方式在炼钢厂占据越来越重要的地位。钢包精炼炉(Ladle Furnace,LF)是一种二次精炼设备,由于其具有投资少、功能强的特点,在国内钢厂中有广泛的应用。LF炉可以调整钢液温度、调整钢液合金成分、去除钢水夹杂物、脱硫等。
由于精炼生产具有一定的危险性,如果操作不当会造成重大经济损失,甚至人员伤亡,所以不可能直接到现场进行精炼炉的实践。为此,本文提出了一种可进行在线模拟操作的半实物仿真平台,以弥补不能在现场进行实际生产操作教学的问题。该平台采用公有云服务器作为服务的入口,可提供随时随地的仿真实验环境,并且还可根据需求的变化及时配置云服务器资源,克服了传统实验平台受时间及地域限制以及扩展性差的不足。
一、钢包精炼流程
钢包精炼的生产流程如图1所示。可简单概括为:三相电极提升, 炉盖上升,装有钢水的钢包从吊包位进入加热位。然后三相电极下降,炉盖下降,开始精炼。精炼过程中需对钢液进行测温、取样。根据钢水的温度与成分,通过送电加热以及加合金料的方式调整钢水温度与成分。再经测温和化验后,若钢水的温度与成份合格,送电断路器断开,电极提升,炉盖上升,由喂线机喂入丝线以进行钢液成分的调整与钢液的净化。喂丝后将钢包车由加热工位运送到吊包位,完成出钢操作[1]。
二、仿真实验平台的构成
采用云计算的钢包精炼炉仿真实验平台系统结构如图2所示。本系统包括以下几个模块:云端服务器、中转服务器、可编程序控制器(PLC)以及仿真模型服务器。这些模块间采用以太网方式连接。如果同时在线的人数过多,造成访问速度变慢,这时就可以借助云计算扩展灵活的特点,及时增加带宽、内存以及CPU数量等资源,以保证系统的稳定性与实时性。
云端服务器采用公有云服务器,在该服务器上部署有IIS Web服务,使用Asp.Net技术为操作者以网页的形式提供钢包精炼炉的操作界面。操作界面可以模拟出钢包炉监控系统的整体画面,便于了解本系统的组成,直观形象的模拟现场过程,还便于监视各个主要设备的运行位置以及工作状态。操作者只需在联网的计算机上打开网页浏览器即可以进行生产操作,而不需要另外安装其他软件。
控制器采用西门子的S7-300系列PLC,该控制器与实际生产中使用的控制器相同。PLC控制着精炼生产的全过程,每座精炼炉的控制系统都有一台PLC作为控制核心。在实验平台中每个连入网络的操作者可动态地分配到一台PLC以进行仿真实验。仿真平台可为多人同时在线操作部署多台PLC设备,并且PLC的数量也可按需要进行动态调整。
中转服务器是云端服务器与PLC设备的信息中转站。操作者在云端操作界面下达的操作指令通过中转服务器传送给PLC。中转服务器还可将PLC的状态传回给云端服务器,从而在界面上显示当前的运行状态。中转服务器使用西门子的Simatic Net通讯软件与PLC进行双向通讯。
实验平台采用半实物仿真的方式,使用仿真模型模拟实际被控对象的特性。所建立的模型运行于仿真模型服务器上。模型的输入输出信息与钢包精炼炉生产过程的输入输出信息类型完全相同,因此可以使用PLC直接对模型进行监控以替代对实际生产过程的监控。由于钢包精炼的生产目标主要是钢液温度与成分的调整,所以在仿真模型服务器中运行有两个模型:一个模型为钢水温升模型,用于计算钢液在一定条件下的实时温度;另一个模型为钢水合金成分模型,用于计算在多种因素影响下的钢液成分,如Si、Mn、C等元素的当前成分含量[2]。
三、仿真平台实现的功能
通过所建立的仿真平台可以实现以下模拟控制功能:
1、炉体控制:钢包车快速前进、后退以及慢速前进、后退运行控制,炉盖升降控制,限位控制,炉盖升降控制。
2、供电控制:电极的升降控制,送电回路断路器分合闸控制,电压档位选择、供电电流设定。
3、加料控制:可直接设定各种钢渣及合金料的加料量,模拟实际加料过程。
在仿真精炼平台运行时,可监测的变量有:
1、钢包车的运行状态:例如当前钢包车处于静止状态还是运动状态,若处于运动状态,还可以检测其运行方向以及处所位置。
2、供电状态:可监测电极的升降情况,断路器是否合闸送电,若处于送电状态,则当前的供电电压档位与送电电流的数值,以及当前炉次的送电时长,当前炉次的电耗等信息。
3、钢液温度:根据钢液的初始温度、钢水质量、送电电压、送电电流以及送电时间等因素可计算出当前的钢液温度。
4、钢液成分:根据钢液的初始成分,加入合金物料的种类、质量等数据计算出当前钢液中的元素成分[3]。
根据系统所提供的监测信息,操作人员即可进行相应的控制操作,系统将操作指令传送给PLC控制仿真模型运行,从而完成精炼炉的模拟生产过程。
四、结语
本文将云计算这种高效、灵活的计算方式引入到仿真实验平台的建设当中,并与钢包精炼生产结合,从而构建出钢包精炼的模拟仿真实验平台。通过该平台,可为学生提供生产实训的实验教学平台,还可为新入职的员工提供直观、可操作的培训平台。该平台不受普通实验资源的诸多限制因素,只需使用简单的设备,即可开始实验,为教学与培训提供了便利。
参考文献
[1]李晶. LF精炼技术[M]. 北京:冶金工业出版社,2009.
[2]于鹏,战东平,姜周华. LF精炼终点成分预报模型开发[J]. 材料与冶金学报,2006,5(1):20-22.
[3]高宪文,张傲岸,魏庆来. 基于神经网络的钢包精炼终点预报[J]. 东北大学学报(自然科学版), 2005(08)
文/宋涛、徐喆、王伟
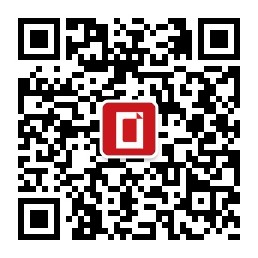